Mild steel is a difficult material to work with. It corrodes easily and it’s typically used in applications where rust is unlikely to be an issue. However, this doesn’t mean that you should shy away from it just because it’s not as popular as carbon or stainless steels. In fact, there are plenty of advantages to working with mild steel. Before you know it, you will be amazed by the things you can accomplish if you put your mind to it and learn how to weld this challenging material. In this article we explain the basics of welding mild steel so that you can begin tackling projects confidently. Read on if you want to find out more.
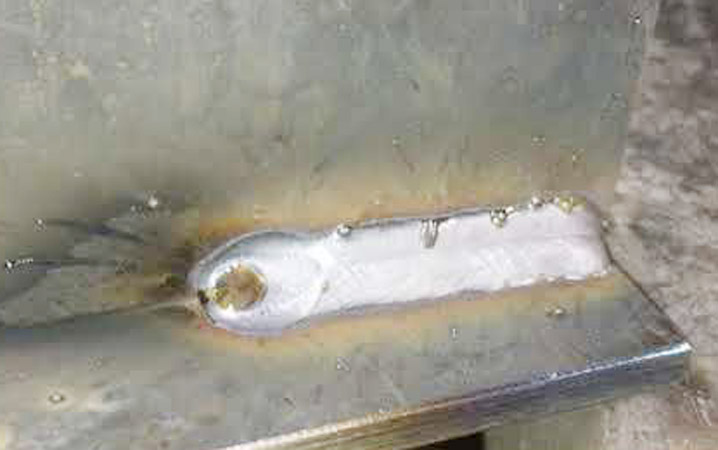
What is Mild Steel?
Mild steel is a type of carbon steel that has a low carbon content. This makes it highly malleable, allowing you to shape it into whatever shape you need. It’s also very corrosion resistant, making it a great choice for projects that require a long lifespan. It has been used in a variety of applications, from automotive and aerospace components to industrial equipment and structural components. The key to welding mild steel is to understand its properties.
Mild steel is relatively soft, which makes it easier to shape, but it has a low melting point. This means that welding on it requires a lot of heat, which can cause warping if not managed properly. It’s also prone to cracking, which means that you must pay close attention to your welds and be prepared to make adjustments if necessary.
Why Need to Weld Mild Steel?
Welding mild steel is an important skill to learn if you are looking to take on projects involving the material. It’s relatively easy to learn and provides you with the opportunity to create a variety of projects with a professional finish. Not only that, but it also offers a number of advantages over other materials. First, mild steel is strong and durable, making it great for projects that need to stand up to wear and tear.
It’s also corrosion resistant, so it won’t rust or corrode over time. It’s also relatively inexpensive, making it a great choice for those on a budget. It’s easy to shape and manipulate, allowing you to create intricate designs with ease.
Safety Tips for Welding Mild Steel
Welding mild steel may be easy to learn, but it also presents some risks. Before you begin welding, make sure that you take the necessary safety precautions. Always wear protective clothing, including a welding helmet, a welding jacket, and welding gloves. In addition, make sure that you’re welding in a well ventilated area and that you are using the right equipment. It’s also important to make sure that you are using the correct setting on your welder.
Mild steel requires a higher temperature than other materials, so make sure that you are using the right setting. If you are using a stick welder, you should use a higher amperage. If you are using a TIG welder, you should use a lower amperage.
Essential equipment for Mild Steel Welding
In order to get started welding mild steel, you will need the right equipment. This includes a welding machine, welding rods, a wire brush, and a welding helmet. You will also need to make sure that you have the right tools for the job. This includes a grinder, a set of pliers, a hammer, and a chisel. Finally, you will need a welding table, clamps, and a welding shield.
Set your arc and MIG welder to the right settings
Setting the right parameters for your arc or MIG welder is crucial when welding mild steel. This will ensure that you achieve the desired weld penetration, bead appearance, and overall quality. Here are some general guidelines for setting your welding equipment when working with mild steel:
Amperage
The amperage setting will depend on the thickness of the metal being welded. In general, a good starting point for mild steel is about 20-30 amps per 1/16 inch of thickness.
Voltage
The voltage setting will also depend on the thickness of the metal. A good starting point is about 18-20 volts for 1/8 inch thick mild steel.
Wire Feed Speed
The wire feed speed is the speed at which the welding wire is fed through the welding gun. It should be adjusted based on the amperage and voltage settings, as well as the thickness of the metal being welded. A good starting point for mild steel is about 150-200 inches per minute (IPM).
Gas Flow Rate
If you are using a MIG welder, you will need to set the flow rate for the welding gas. The gas flow rate should be adjusted based on the size of the nozzle and the thickness of the metal being welded. A good starting point for mild steel is about 20-25 cubic feet per hour (CFH).
These settings are just a starting point. You may need to adjust them slightly based on the specific conditions of your welding project. Always refer to the manufacturer’s instructions for your welding equipment and consult with an experienced welder if you are unsure about the proper settings.
How to weld Mild Steel easily?
Now that you have all the necessary equipment, it’s time to get started welding mild steel. The first step is to make sure that the surface is clean. Use a wire brush to remove any dirt and debris, and then use a grinder to smooth out any rough edges. Once the surface is clean, you can begin welding. The most common type of welding for mild steel is arc welding. This is done by using an electric current to melt the metal and create a bond between the two pieces.
You will need to set the amperage on your welding machine to the appropriate level, and then use the welding rod to fill in the gap between the two pieces of metal. Make sure to move the welding rod in a circular motion to ensure that the weld is even and secure.
Once you’ve finished welding, you will need to clean up the area. Use a wire brush to remove any slag or other debris, and then use a grinder to smooth out any rough edges. When you’re done, you can inspect your weld and make sure that it’s secure.
Benefits of Welding Mild Steel
Welding mild steel has a number of advantages over other materials. It’s strong and durable, making it a great choice for projects that need to stand up to wear and tear. It’s also corrosion resistant, so it won’t rust or corrode over time. It’s also relatively inexpensive, making it a great choice for those on a budget. It’s easy to shape and manipulate, allowing you to create intricate designs with ease.
Maintain your cool and be patient
Always try to maintain your cool while working with mild steel. This is because when you get too excited, your body produces a lot of adrenaline, which can make you feel more excited and increase the heat generated during welding. It can also make your welds weak. If you are welding an object that is too exciting, then it can increase the temperature of the metal and make a weak weld.
You can maintain your cool by breathing deeply and slowly. This can help you to calm down and focus on your work. You can also try to meditate or focus on your work. You can try some exercises that can help you to maintain your cool.
Use good hand techniques while welding
When welding mild steel, you should keep the welding hand flat against the work with the palm facing down. This can help you to control the welding rod and maintain the correct angle for welding. You should also try to keep your wrist straight while welding. This can help to control the welding rod and reduce fatigue. Keeping your wrist straight can also help to prevent injury.
It is also important to keep your elbow relaxed while welding. If your elbow is tense while welding, it can lead to back injuries. The welding rod should also be kept against the work with your elbow.
Always stay alert and watch out for sparks
Sparks flying off the welding rod can be dangerous. It can cause injury if it hits you. You should always be on the lookout for sparks flying off the welding rod. If you are welding on a smooth piece of metal, you may not be able to notice the sparks. However, if you are welding a piece that has a lot of grooves or joints, you will notice sparks flying off the rod. You should also be careful while welding when you are welding on a steel, iron or aluminum base. These metals can cause sparks as they can be ignited by the welding rod.
When using a torch for welding mild steel?
You can either use a gas or an arc welder for welding mild steel. A torch is a portable welding gun that uses an electric arc for welding. You can easily carry it around and use it at any place. Using a torch is more convenient than using a gas or gas shielded arc welder. With a torch, you do not have to worry about gas leaks or gas shielding because it does not use gas.
A torch can weld all types of metal, but it is popular among welders because of its low cost and easy portability. A torch is also a good option for welding mild steel. You can easily weld mild steel with a torch and you will be surprised with the result. A torch can weld mild steel with ease, but it has its limitations too.
Tips for welding mild steel reinforced with carbon fiber or glass fiber
When welding the mild steel with the reinforcement, you must always use a shielding gas or carbon fiber welding rods. This is because these welding rods have a special shield and can reduce the flux of the metal. You can weld mild steel reinforced with carbon fiber or glass fiber using a shielding gas with or without an electrode. Shielding gas is used when the metal is too hot or hot to be welded with an electrode. When welding mild steel reinforced with carbon fiber or glass fiber, you must always weld slowly and maintain the correct welding angle. It is also important to weld at the correct welding angle on the component.
Wrapping up
Welding mild steel can be a challenging but rewarding process. With the right equipment and a little practice, you will be able to tackle projects involving the material with confidence. Make sure to take the necessary safety precautions, and always be prepared to make adjustments if necessary. With a little patience and practice, you’ll be creating beautiful welds in no time.