Welding steel to aluminum is a good idea if you want your project to be cost effective and long lasting. Aluminum is commonly used in construction, automotive manufacturing, aircraft manufacturing, home appliances, wind turbine production, electronics and much more. Steel is also commonly used for construction because it’s corrosion resistant and lasts for many years without rusting or deteriorating. If you have an idea of making a project of welding steel to aluminum pipe, then this article will help you get started with the right steps. Keep reading to learn more about it.
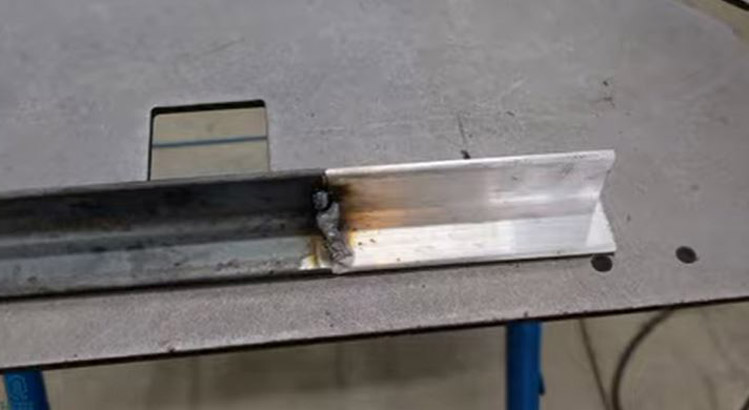
Definition of Welding
Welding is the process of joining metals with arc or plasma with friction or convection in a special environment, under pressure, to create permanent joints. It can be done with gases (as in MIG welding), liquid metal (as in Stick welding), or with solid metal as in GAS welding. Welding is an excellent way to join metals, but should be used to join strong, corrosion-resistant materials only. Welding is not the same as brazing, although either process is often called “welding”.
Welding Aluminum to Steel
Welding Aluminum to Steel works best with seamless or semi-seamless joint. If the joint is not seamless, the weld will crack and split apart in a few years. A continuous seam weld is not recommended, as it is not as strong as a seamless weld. If the seam weld is on a long pipe, the weld will eventually break. When welding aluminum to steel, you have to keep in mind the differences between the metals’ properties and the welding process parameters.
The engineers at the aluminium mill will provide you with welding parameters to weld aluminium to steel. Generally, the lower the welding power, the better. If the weld is too strong, it will cause the pipe to stretch and develop cracks. When welding steel to aluminum, take note that you have to weld with copper shielding gas.
Choosing the Right Welding Rods
Aluminum welding rods are usually made from dendritic salt based flux, flux cored wires, and weld speed boosting ingredients. Dendritic salt based flux is used in welding rods because it minimizes the risk of weld pitting. Welding rods with low levels of weld pitting can be used in aluminum joints.
Type of Welding to Weld Steel to Aluminum
Standard and Stick Welding: Stick welding is a fusion welding process. It is a basic welding process that uses a single electrode to produce a weld. It is suitable for joining metals together where the bonding characteristics of one metal are in direct contact with those of the other. Stick welding is suitable for joining two metals together that have close together but not exact matching properties.
Shielded Metal Arc Welding (SMAW): SMAW welding is the most common welding method for welding steel to aluminum. It is used for mild metals and has a mild arc and good penetration. It is also known as gas metal arc welding or self-shielded arc welding. This welding method usually uses a shielded metal arc (SMAW) welding electrode. Gas metal arc welding is used for gas welding and has a serious arc with excellent penetration. It is also known as gas metal arc or open-arc welding. SMAW welding is suitable for welding aluminum to mild steel and mild aluminum.
It is not suitable for welding aluminum to other metals. It has a mild arc and good penetration. The aluminum joint is not very strong. It is not suitable for forming an entire pipe. SMAW welding is a cost effective welding method and suitable for welding aluminum to mild steel and mild aluminum.
Gas Tungsten Arc Welding (GTAW): GTAW welding is also known as tungsten inert gas (TIG) welding. It has a serious arc with good penetration and is suitable for welding aluminum to steel, mild steel, and stainless steel. GTAW welding is mostly used for forming joints. It is a cost effective welding method, and aluminum GTAW welding is a good choice for welding aluminum to steel and mild steel.
GTAW welding is suitable for welding aluminum to mild steel, stainless steel, and titanium. It has a serious arc with good penetration. The aluminum joint is not very strong. It is not suitable for forming an entire pipe. GTAW welding is a cost effective welding method, and suitable for welding aluminum to mild steel, stainless steel, and titanium.
Plasma Arc Welding (PWA): PLA welding is an arc welding method that uses a low DC current (1-20amp) to help achieve a finer weld with less heat distortion, less erosion, and better joint integrity. The welding is produced by a low pressure arc between the tungsten electrode and the aluminum electrode. PLA welding is suitable for welding aluminum to ferrous and non-ferrous metals. It has a severe arc with good penetration. The aluminum joint is very strong. It is suitable for forming an entire pipe. It is also known as tungsten inert-gas (TIG) welding.
Differences between Butt welding and Joint Welding
Here are the main differences between butt welding and joint welding:
Butt welding | Joint welding |
Strong but if the joint is subjected to high pressure, it will break. | Joint welding is more durable and can withstand high pressures. |
Butt welds are easy, fast, and inexpensive to make. | Joint welding is expensive and easy, but difficult to make. |
Butt welds are made when welding two pieces of metal that are not completely aligned and equal. | Joint welding is made between two equal pieces of metal. |
Butt welding vs Joint welding – Which one should you choose?
Butt Welding Butt welds are strong and durable, but do not have a long service life. They should be used for short-term jobs such as repairs, maintenance, and construction related jobs. Joint Welding Joint welding has better durability and strength, but does not withstand high pressure as well. Joint welding is the standard for long-term projects, and is recommended for welders who want long-lasting projects. Here are the pros and cons of using each welding method.
Butt welding: Pros
- It is cheap, fast, and easy to make.
- It has good penetration.
- It is suitable for joining two dissimilar metals.
- It can withstand high pressure.
- It is not brittle.
- It produces brittle welds.
- It is less durable.
- It will break when subjected to high pressure.
- It is susceptible to pitting.
- It produces more weld spatter.
Joint welding: Pros
- It is strong and durable.
- It withstands high pressure.
- It is not brittle.
- It is suitable for joining two equal metals.
- It produces strong joints.
- It is suitable for joining two dissimilar metals.
- It is less expensive than joint welding.
- It produces less weld spatter.
Final Thoughts: Welder Settings and Tips for Welding Steel to Aluminum Pipe
Welders setting for Welding Steel to Aluminum project vary depending on the type of welding being done. However, there are some general welding tips that are applicable to both types of welding. When welding steel to aluminum pipe, the most important settings to consider are the pipe diameter and the filler material. The pipe diameter affects the weld bead size and the weld penetration depth. The filler material affects the heat input and the weld quality.