Friction Seam Welding is an innovative and highly efficient welding process that’s rapidly gaining popularity in the manufacturing industry. This technique utilizes friction to create superbly sealed and robust joints between metal panels, tubes, and bars. In this article, we’ll explore friction seam welding and its intricate details. We’ll discuss its effectiveness as a joining technique, its equipment, its advantages, and its disadvantages.
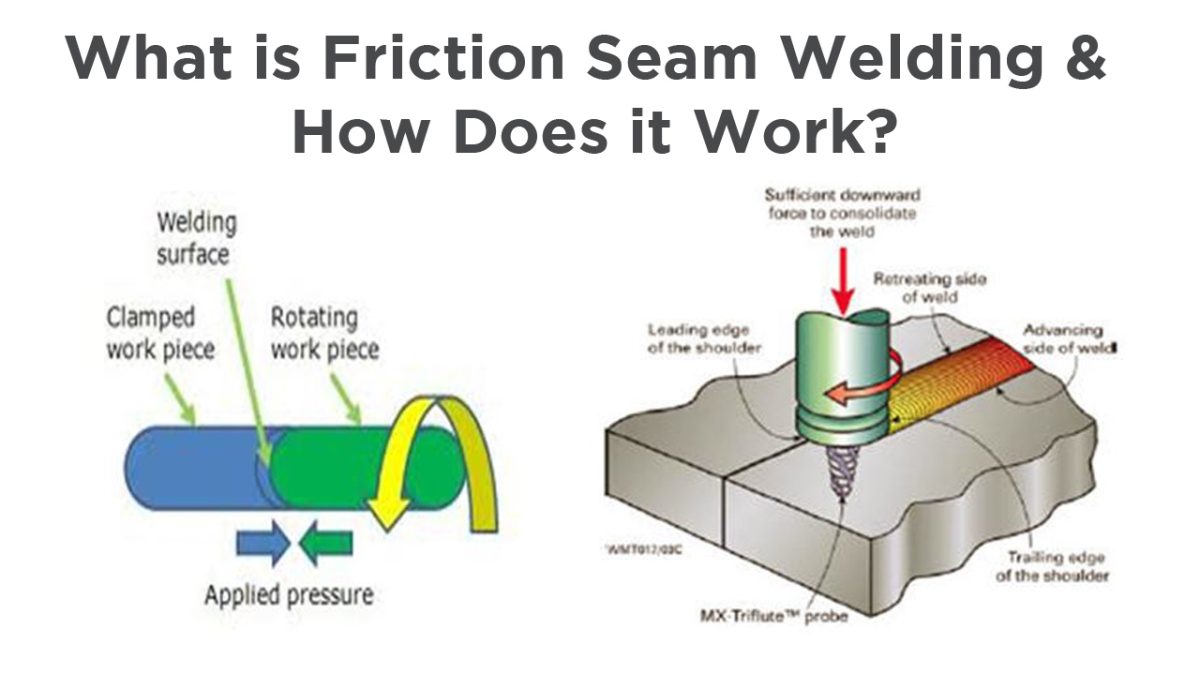
Photo by slideplayer
What is Friction Seam Welding?
Friction seam welding is a joining technique that achieves seamless and continuous welds. This process involves using frictional heat generated by mechanical friction between two workpieces to fuse them together. It is a solid-state welding technique that does not require any filler materials or shielding gases.
The process of friction seam welding involves the use of specialized equipment that applies pressure and heat to the workpieces. The equipment includes a rotating tool that applies pressure to the metal plates, creating frictional heat that softens the material. The rotation of the tool forces the softened material to mix together, forming a bond that fuses the two plates.
One of the main advantages of friction seam welding is that it produces high-quality, strong, and durable joints. The process can handle a wide range of metals, including aluminum, copper, and titanium, making it a versatile joining technique. The equipment required is expensive, and the process can be time-consuming, making it suitable for high-volume production runs only.
Advantages and Disadvantages of Friction Seam Welding
Friction seam welding has its advantages and disadvantages when used in industrial applications. Some of the advantages include:
- Produces strong and durable joints.
- Does not require additional filler materials or shielding gases.
- Can handle a wide range of metals, including dissimilar metals.
- Highly precise and repeatable.
Friction seam welding has some limitations and drawbacks. These include:
- Expensive equipment required for the welding process.
- Requires skilled operators to achieve optimal results.
- Longer welding times compared to other joining techniques.
- Not suitable for thin plates or small works.
To achieve the best results with friction seam welding, it’s essential to use the right equipment and understand the process thoroughly. For high-volume production runs that require high-quality welds, friction seam welding is a reliable joining technique that offers many advantages.
Advantages of Friction Seam Welding
Friction seam welding is a joining technique that provides numerous advantages over traditional welding methods. One significant advantage is its ability to create strong and durable joints without requiring extensive post-welding processing. The resulting joints are resistant to fatigue, corrosion, and wear, making this technique highly desirable for numerous applications.
One of the key advantages of using friction seam welding is that it can join dissimilar metals with differing properties. This is because the process does not rely on melting any of the materials, allowing them to maintain their original properties and characteristics. This technique is particularly suitable for high-temperature situations, as it generates less heat compared to traditional welding methods.
Friction seam welding offers immense versatility, with applications across many different industries such as automotive, aerospace, and power generation. It is commonly used in the production of drive shafts, exhaust systems, and engine components. Its high weld quality and efficient process have made it a popular choice for manufacturers seeking cost-effective production methods that guarantee excellent results.
The low heat input also makes friction seam welding an environmentally friendly solution, reducing the amount of energy required for post-welding processing. The minimization of heat-affected zones in the welded area results in a tighter, more precise weld in comparison to other welding methods.
The advantages of friction seam welding are impressive, making it an increasingly popular choice for diverse manufacturing processes. These numerous advantages include easier weld creation, versatile applications, energy efficiency, and high-quality welds that last longer, making it an highly competitive joining technique with a bright future.
Disadvantages of Friction Seam Welding
While friction seam welding offers many benefits, there are potential drawbacks to consider when selecting a joining technique. One disadvantage is that friction welding equipment can be expensive and requires skilled operators to perform correctly.
Additionally, friction welding may not be suitable for all materials and part configurations. For example, parts with large variations in thickness may not form a quality bond using friction welding. Certain materials such as aluminum, may experience metallurgical changes during the friction welding process, which can impact the integrity and strength of the joint.
Another potential disadvantage of friction seam welding is that it is not always practical for small-scale or prototype manufacturing. Due to equipment and set-up requirements, friction welding is more suitable for larger production runs where efficiency and cost-effectiveness can be maximized.
When considering friction welding as a joining technique, it’s important to evaluate the potential disadvantages and determine whether they outweigh the advantages for your specific application.
Conclusion
Friction seam welding is a revolutionary joining technique that offers various benefits over traditional welding methods. It’s a highly efficient process that creates strong and durable joints with seamless continuity. Friction seam welding has demonstrated its usefulness in numerous industries such as automotive, aerospace, and manufacturing, facilitating innovation and progress.
The potential for further developments in friction welding is enormous, and the future looks promising. As technology continues to advance, the potential for enhanced weld quality and more affordable equipment grows. It’s exciting to observe how friction welding will revolutionize the industry and facilitate unprecedented advancements.
Friction welding is a valuable technique that can solve numerous welding challenges and provide cost-effective solutions in various industries. We hope this article has provided you with a comprehensive understanding of friction seam welding and its significance.