Thermoplastic Rubber, commonly known as thermoplastic rubber, is a versatile material used in various industries for its unique combination of flexibility and durability. But many people wonder, is thermoplastic rubber safe for use? In this article, we will explore the properties of thermoplastic rubber and its safety considerations.
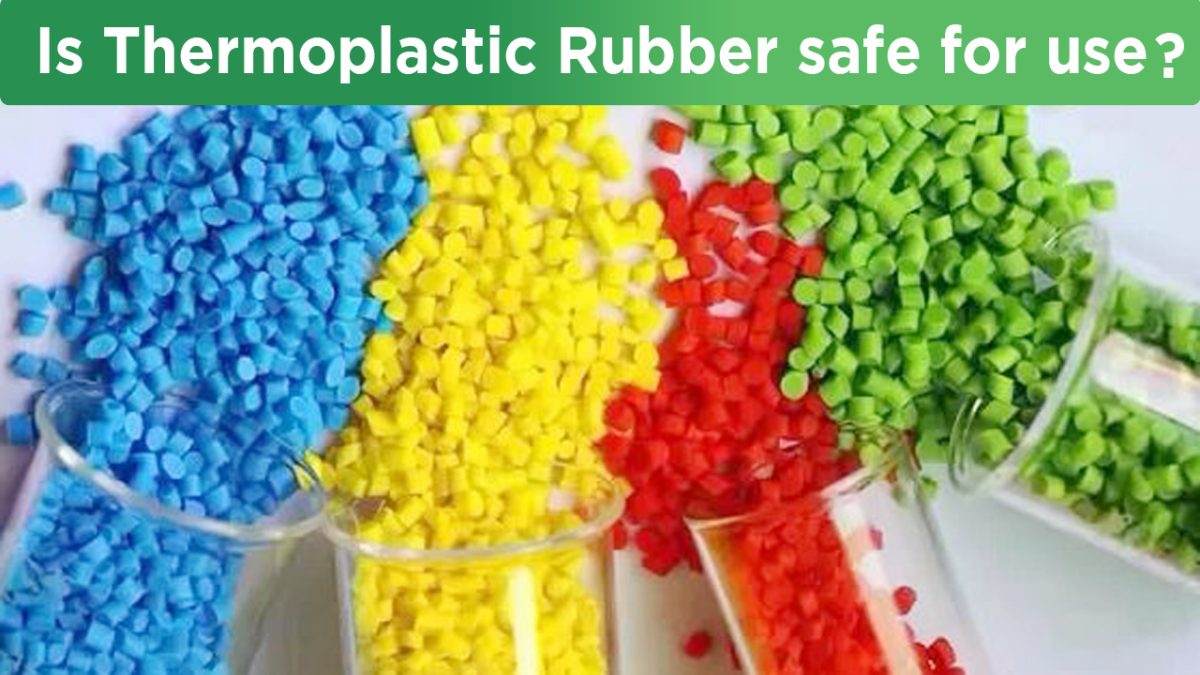
Image by whkjh
Properties and characteristics of TPR
Thermoplastic rubber (TPR) is a synthetic material that exhibits characteristics of both thermoplastics and rubber. It is composed of a blend of polymers, typically a mix of rubber and plastic. This combination gives thermoplastic rubber its unique properties, making it an ideal material for a wide range of applications.
TPR can be easily molded and shaped when heated, and once cooled, it retains its form. This makes it highly versatile and suitable for manufacturing products such as footwear, consumer electronics, automotive components, and more. TPR offers excellent flexibility, allowing it to withstand repeated bending, stretching, and compression without losing its shape or functionality.
Additionally, TPR exhibits remarkable resistance to abrasion and chemicals, making it highly durable and long-lasting. It can withstand exposure to oils, solvents, acids, and bases, making it suitable for use in demanding environments where other materials may fail.
Common uses and applications of TPR
Due to its exceptional properties, TPR finds extensive use in various industries and applications. One of the most common uses of TPR is in the production of footwear. TPR outsoles provide excellent grip, shock absorption, and flexibility, making them ideal for athletic shoes, boots, and sandals.
In the consumer electronics industry, TPR is utilized for manufacturing protective cases and covers for smartphones, tablets, and other electronic devices. Its flexibility and impact resistance help protect devices from accidental drops and impacts. TPR is also commonly used in the automotive industry for producing weather-stripping, gaskets, and seals due to its ability to withstand extreme temperatures and resist chemicals.
Moreover, TPR is often found in household products such as kitchen utensils, toys, and medical devices. Its non-toxic and hypoallergenic nature makes it suitable for applications where contact with skin or food is involved.
Is thermoplastic rubber safe for use?
Yes, it is safe to use thermoplastic rubber. When it comes to safety, thermoplastic rubber is generally considered to be safe for regular use. Thermoplastic rubber is non-toxic, hypoallergenic, and does not contain harmful chemicals like phthalates or PVC, which are commonly found in other materials. This makes thermoplastic rubber a preferred choice for products that come into contact with the human body.
However, it is essential to ensure that thermoplastic rubber products meet relevant safety standards and regulations to ensure their overall safety. Manufacturers should comply with guidelines and testing requirements to guarantee that thermoplastic rubber products do not pose any health risks to consumers. It is advisable to look for certifications or labels indicating compliance with safety standards when purchasing thermoplastic rubber products.
Understanding thermoplastic rubber safety standards and regulations
To ensure the safety of thermoplastic rubber products, various safety standards and regulations are in place. These standards aim to establish guidelines for the composition, manufacturing processes, and potential hazards associated with thermoplastic rubber.
One widely recognized standard is the Restriction of Hazardous Substances (RoHS) directive. It restricts the use of certain hazardous substances in electrical and electronic equipment, including TPR components. Compliance with the RoHS directive ensures that TPR products do not contain harmful substances such as lead, mercury, cadmium, and more.
Additionally, the Consumer Product Safety Improvement Act (CPSIA) in the United States sets safety standards for children’s products, including those made with TPR. This act regulates the use of phthalates, lead, and other harmful substances in products intended for children under the age of 12.
It is crucial for manufacturers and consumers alike to be aware of these safety standards and regulations to ensure that TPR products are safe for use.
Benefits of using TPR compared to other materials
TPR offers several advantages over alternative materials, which contribute to its widespread use in various industries. Some of the key benefits of thermoplastic rubber include:
Cost-effectiveness: TPR is generally more affordable compared to natural rubber and other synthetic materials, making it an economical choice for manufacturers.
Versatility: TPR’s unique combination of flexibility, durability, and chemical resistance makes it suitable for a wide range of applications.
Ease of processing: TPR can be easily molded and shaped using common manufacturing techniques such as injection molding and extrusion, reducing production time and costs.
Environmental friendliness: TPR is recyclable and can be reused or repurposed, contributing to a more sustainable manufacturing process.
Comfort and safety: TPR’s flexibility and hypoallergenic nature make it comfortable to use and safe for various applications, including those involving direct contact with the skin.
TPR manufacturing process
The manufacturing process of TPR involves several steps to create the desired properties and characteristics. The process typically includes:
Raw material selection: The selection of the appropriate blend of polymers, including rubber and plastic, is crucial to achieving the desired properties of TPR.
Compounding: The selected materials are mixed together, often with the addition of fillers, plasticizers, and other additives, to achieve the desired balance of flexibility, durability, and chemical resistance.
Molding: The compounded TPR material is heated and injected into molds, where it takes the desired shape and form. The molded TPR is then cooled and solidified.
Finishing processes: After molding, the TPR products may undergo additional processes such as trimming, surface finishing, and quality control to ensure they meet the required specifications.
The precise manufacturing process may vary depending on the specific application and requirements of the TPR product.
TPR recycling and sustainability
TPR is a recyclable material, which contributes to its sustainability and reduces waste. Recycling TPR involves collecting and processing used TPR products, transforming them into reusable material for new products.
The recycling process typically includes shredding or grinding the TPR products into small particles, melting these particles down, and then reforming them into new TPR products. This recycling process helps conserve resources, reduce landfill waste, and decrease the environmental impact of TPR production.
Furthermore, TPR’s durability and resistance to chemicals contribute to its longevity, reducing the need for frequent replacements and lowering overall waste generation.
Alternatives to TPR
While TPR offers numerous advantages, there are also alternative materials available for various applications. Some common alternatives to TPR include:
Thermoplastic Elastomers (TPE): TPEs are similar to TPR in terms of flexibility and durability. They are often used as an alternative to TPR when specific performance requirements need to be met, such as enhanced weather resistance or higher temperature tolerance.
Silicone: Silicone is a synthetic rubber that offers excellent heat resistance, making it suitable for applications where high temperatures are involved. It is commonly used in the production of kitchen utensils, medical devices, and automotive components.
Natural Rubber: Natural rubber, derived from the sap of rubber trees, offers exceptional flexibility and elasticity. It is commonly used in applications where biodegradability or high levels of elasticity are required.
It is essential to consider the specific requirements and characteristics of each material when selecting the most suitable option for a particular application.
Conclusion
Thermoplastic rubber (TPR) is a versatile material that combines the best qualities of traditional rubber and thermoplastics. Its unique blend of flexibility, durability, and chemical resistance makes it an ideal choice for various industries and applications.
While generally safe for everyday use, it is crucial to verify that TPR products adhere to safety guidelines and regulations to ensure their overall safety. Certification and compliance with relevant standards such as RoHS and CPSIA provide assurance that TPR products are free from harmful substances.
Thermoplastic rubber offers several advantages over alternative materials, including cost-effectiveness, versatility, ease of processing, and environmental friendliness. Its recyclability contributes to sustainability and waste reduction.
By understanding the properties, safety considerations, manufacturing process, and alternatives to TPR, individuals and businesses can make informed decisions when selecting materials for their specific needs.