Are you in the welding industry and looking to expand your knowledge of different welding techniques? If so, you have come to the right place. In this article, we will explore the differences between two widely used welding techniques: arc welding and TIG welding. Arc welding vs TIG welding are both effective methods for joining metals, but they differ in terms of process and applications. Each technique has its advantages and disadvantages, and understanding these differences can help you choose the right method for your welding needs.
Whether you are a novice welder or someone with years of experience, knowing the distinctions between TIG welding vs arc welding can greatly enhance your welding capabilities. So, let’s dive into the details and discover the key differences between these two popular welding techniques.
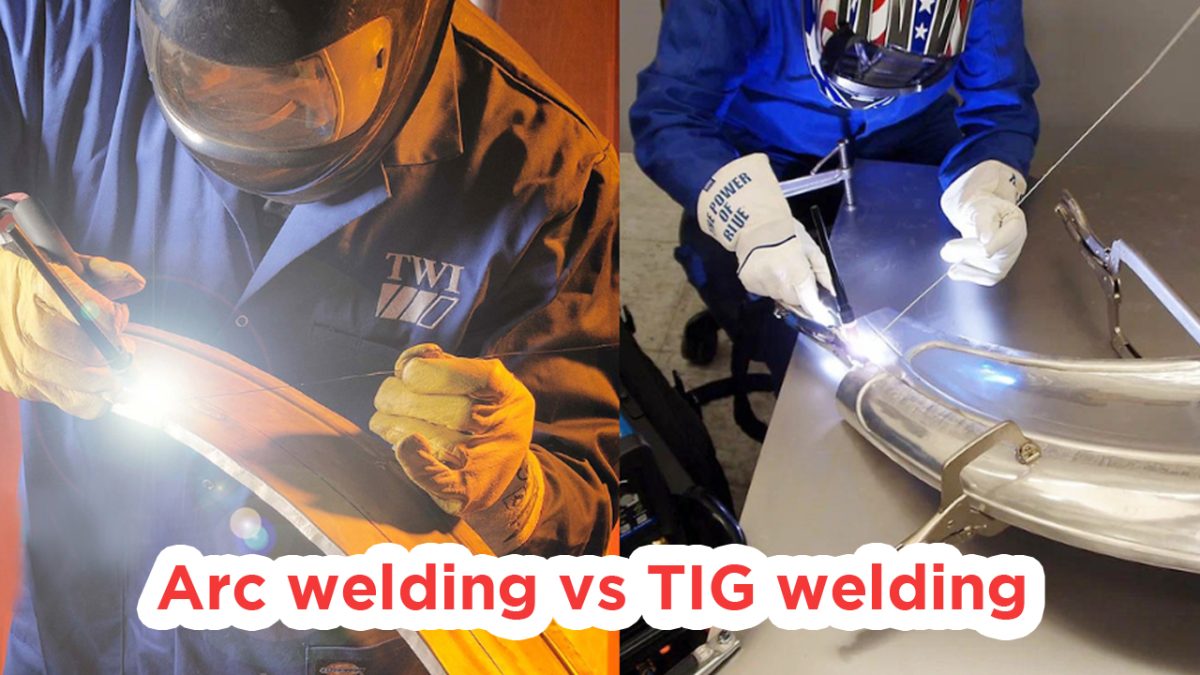
Photo by thepipingmart
Arc welding explained
Arc welding, also known as shielded metal arc welding (SMAW) or stick welding, is a common welding technique used across various industries. It involves using an electric arc to melt metals together, creating a strong bond between the materials. The process begins by establishing an electrical current between the metal being welded and an electrode, which is typically coated with flux. The heat generated by the electrical arc melts the electrode and the base metal, fusing them together as the molten metal cools.
Arc welding offers several advantages. First, it is a versatile technique that can be used to join a wide range of metals, including steel, stainless steel, cast iron, and aluminum. Second, it is a relatively simple and affordable welding method, making it accessible to both professionals and hobbyists. Additionally, arc welding can be performed in various positions, such as flat, horizontal, vertical, and overhead, allowing for flexibility in welding applications.
However, arc welding also has its drawbacks. It produces more spatter and sparks compared to other welding techniques, which can lead to a messier work environment. The process can also be slower than some other methods, as the electrode needs to be replaced periodically. Arc welding requires a steady hand and skillful technique to produce high-quality welds consistently.
TIG welding explained
TIG welding, short for tungsten inert gas welding, is a precise and delicate welding technique commonly used for high-quality welding applications. Unlike arc welding, TIG welding uses a non-consumable tungsten electrode to create the weld. The electrode generates the heat required to melt the base metal, while an inert gas, such as argon, is used to shield the weld area from atmospheric contamination.
TIG welding is known for its ability to produce clean and aesthetically pleasing welds. It offers excellent control over the welding process, allowing welders to create intricate and precise welds. This makes TIG welding particularly suitable for applications that require high accuracy and aesthetic appeal, such as automotive, aerospace, and art fabrication.
One of the main advantages of TIG welding is its versatility. It can be used to weld a wide range of metals, including stainless steel, aluminum, copper, brass, and titanium. TIG welding also allows for welding thin materials without distortion or burn-through, making it ideal for delicate work.
Despite its advantages, TIG welding also has some limitations. It is a slower welding process compared to arc welding, as the welder needs to manually feed the filler rod into the weld pool. TIG welding also requires a higher level of skill and experience to master, as it demands precise control of the welding torch and the filler rod simultaneously. Additionally, the equipment required for TIG welding can be more expensive compared to other welding methods.
Differences Between Arc welding vs TIG welding
Now that we have a better understanding of arc welding vs TIG welding individually, let’s compare the key differences between these two popular welding techniques.
- Process: Arc welding uses an electric arc to melt metals, while TIG welding uses a non-consumable tungsten electrode to create the weld.
- Heat source: In arc welding, the heat is generated by the electrical arc between the electrode and the base metal. In TIG welding, the heat is generated by the tungsten electrode.
- Electrode usage: Arc welding uses a consumable electrode, which gets consumed during the welding process. TIG welding, on the other hand, uses a non-consumable tungsten electrode that remains intact.
- Weld appearance: TIG welding produces clean and aesthetically pleasing welds with minimal spatter, while arc welding may result in a messier appearance due to more spatter and sparks.
- Welding speed: Arc welding is generally faster than TIG welding, as it does not require manual feeding of the filler rod. TIG welding, with its manual deposition of the filler rod, is a slower process.
- Skill level: Arc welding is relatively easier to learn and requires less skill compared to TIG welding. TIG welding demands a higher level of skill and precision due to the need for simultaneous control of the welding torch and the filler rod.
- Applications: Arc welding is commonly used in heavy-duty applications, such as construction, pipelines, and structural fabrication. TIG welding is preferred for applications that require precision, cleanliness, and aesthetics, such as automotive, aerospace, and art fabrication.
Pros and cons of arc welding
Arc welding has several advantages:
- It is a versatile welding technique that can be used on a wide range of metals.
- Arc welding is relatively affordable and accessible, making it suitable for both professionals and hobbyists.
- It allows for welding in various positions, offering flexibility in welding applications.
- Arc welding is faster than TIG welding, making it more efficient for certain projects.
However, arc welding also has its disadvantages:
- The process produces more spatter and sparks, leading to a messier work environment.
- It requires periodic replacement of the consumable electrode.
- Arc welding demands a steady hand and skilled technique to consistently produce high-quality welds.
Pros and cons of TIG welding
TIG welding offers several advantages:
- It produces clean and aesthetically pleasing welds with minimal spatter.
- TIG welding allows for precise control of the welding process, making it suitable for applications that require high accuracy.
- It can weld a wide range of metals, including stainless steel, aluminum, copper, brass, and titanium.
- TIG welding is ideal for welding thin materials without distortion or burn-through.
However, TIG welding also has its drawbacks:
- It is a slower welding process compared to arc welding, as the filler rod needs to be manually fed into the weld pool.
- TIG welding requires a higher level of skill and experience to master.
- The equipment required for TIG welding can be more expensive compared to other welding methods.
Applications of arc welding
Arc welding finds applications in various industries:
- Construction: Arc welding is commonly used in the construction industry for welding structural steel, pipelines, and heavy equipment.
- Automotive: It is used for welding automotive frames, body panels, and other components.
- Fabrication: Arc welding is widely used in metal fabrication, including the production of gates, fences, and metal furniture.
- Maintenance and repair: Arc welding is essential for repairing equipment and machinery in various industries.
Applications of TIG welding
TIG welding is preferred for applications that require precision, cleanliness, and aesthetics:
- Aerospace: TIG welding is commonly used in the aerospace industry for welding critical components that require high quality and precision.
- Automotive: TIG welding is used for welding exhaust systems, engine components, and other automotive parts that demand high-quality welds.
- Art fabrication: TIG welding is popular among artists for creating intricate metal sculptures and artwork.
- Jewelry making: TIG welding is used in the jewelry industry for precise and clean welds on precious metals.
Choosing the right welding method for your project
When selecting between arc welding and TIG welding, consider the following factors:
- Material: Determine the type of metal you’ll be working with, as certain metals may be better suited for one welding method over the other.
- Application: Consider the specific requirements of your project. Are aesthetics important? Is precision crucial? These factors will influence your choice.
- Skill level: Evaluate your own skill level and expertise. TIG welding requires more experience and control, while arc welding is more accessible for beginners.
- Budget: Take into account the cost of equipment and consumables associated with each welding method.
By considering these factors, you can make an informed decision and choose the welding method that best suits your project’s requirements.
Conclusion
Tig welding vs Arc welding are two popular welding techniques that offer different advantages and applications. Arc welding is versatile, affordable, and suitable for heavy-duty applications, while TIG welding offers precise control, clean welds, and is preferred for applications that demand high-quality aesthetics. By understanding the differences between these two techniques and considering the specific requirements of your project, you can select the appropriate method to achieve the desired results. Whether you choose arc welding or TIG welding, both techniques have their place in the welding industry, and mastering either one can greatly enhance your welding capabilities.