If you’re new to welding and cutting, you may be wondering what the difference is between plasma welding vs plasma cutting. While both methods use plasma, they serve different purposes and require different techniques. In this article, we’ll explore the key differences between plasma welding and plasma cutting, including their unique functions, uses, and techniques.
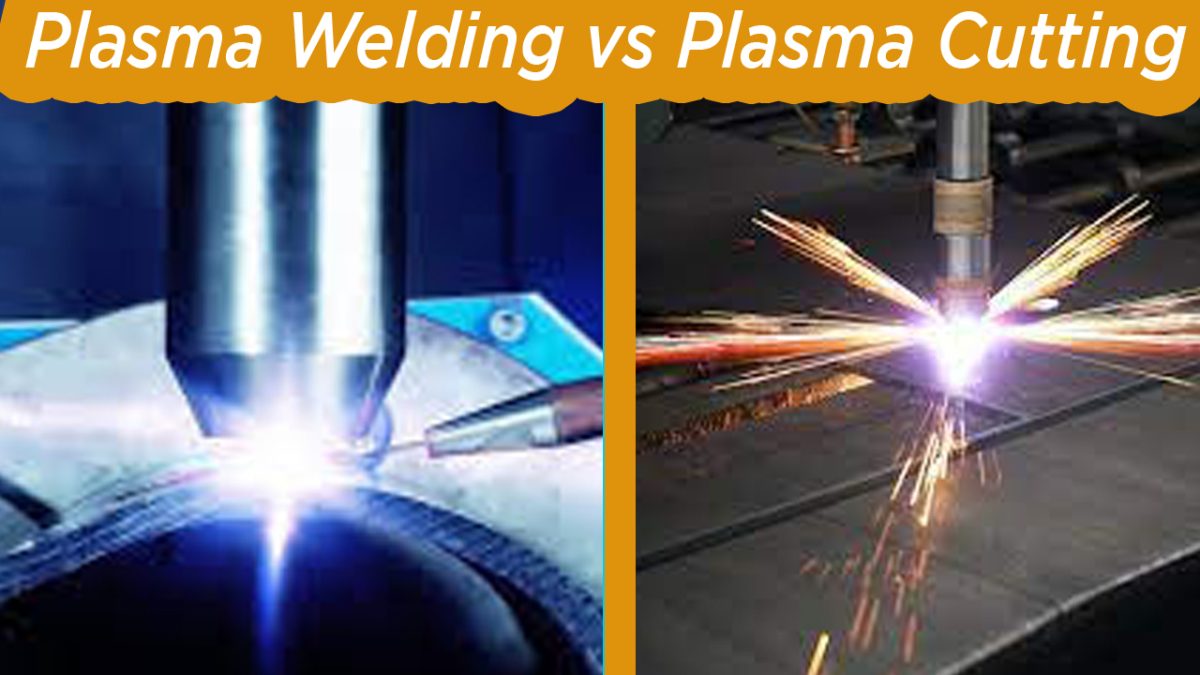
Understanding these differences is crucial for anyone looking to use plasma technology in their work. By the end of this article, you’ll have a comprehensive understanding of what distinguishes plasma welding from plasma cutting, and which technique is best suited for your needs. So, let’s dive into the world of plasma welding and plasma cutting, and explore what sets them apart from each other.
Understanding Plasma Cutting
Plasma cutting is a process that involves cutting conductive materials using a plasma torch. The torch creates a high-temperature plasma arc that melts and blows away the metal, leaving behind a clean cut.
The Plasma Cutting Process
The plasma cutting process involves the following steps:
- A gas, such as oxygen or air, is blown through a nozzle at high speed.
- An electrical arc is created between the nozzle and the metal being cut.
- The electrical arc ionizes the gas, creating plasma.
- The high-temperature plasma arc melts the metal, while the gas blows away the molten metal, leaving a clean cut.
Advantages of Plasma Cutting
There are several advantages to using plasma cutting:
- Plasma cutting can cut a wide range of materials, including steel, stainless steel, aluminum, and copper.
- It is faster than traditional cutting methods, such as oxy-fuel cutting.
- The cuts are clean and precise, with minimal material waste.
- Plasma cutting can be used on materials of varying thicknesses, from thin sheets to thicker plates.
Plasma Cutting Applications
Plasma cutting is commonly used in various industries, such as:
Industry | Plasma Cutting Application |
---|---|
Automotive | Cutting of frames, chassis, and exhaust systems |
Construction | Cutting of metal sheets and pipes for building and infrastructure projects |
Metal Fabrication | Cutting of metal parts and components for machinery and equipment |
Shipbuilding | Cutting of metal plates for ship hulls and decks |
Plasma cutting is a versatile and efficient cutting method that offers several advantages over traditional cutting methods. It is widely used in various industries, making it an essential technique in modern manufacturing processes.
Exploring Plasma Welding
Plasma welding is a process that utilizes high-velocity ionized gas to melt and join metal. The plasma welding process is similar to traditional TIG welding, but with some key differences.
The plasma welding process involves creating a high-temperature plasma arc that melts the base metal and allows for the addition of filler material to create a strong bond. This arc is created by passing a gas through a small orifice in the torch to create a high-velocity stream.
Plasma Welding Process
The plasma welding process involves several steps:
Preparation of the workpieces – The surfaces to be welded must be clean and free of any contaminants to ensure a proper bond.
Setting up the equipment – The plasma welding equipment consists of a welding torch, power supply, and gas delivery system.
Creating the plasma arc – The plasma arc is created by passing a gas through the torch orifice, which ionizes the gas and creates a high-velocity stream that melts the base metal.
Adding filler material – The filler material is added to the base metal at the appropriate time to create a strong bond.
Finishing the weld – After the weld is complete, it must be cleaned and inspected to ensure it meets the necessary quality standards.
Plasma Welding vs Traditional Welding
One of the main advantages of plasma welding over traditional welding methods is its ability to create a high-quality, precise weld. Plasma welding can produce welds with less heat input, resulting in reduced distortion and a smaller heat-affected zone.
Additionally, plasma welding can be used on a wider variety of materials than conventional welding processes, including aluminum, stainless steel, and copper alloys. This makes it an ideal choice for industries such as aerospace, automotive, and electronics manufacturing, where precision and consistency are crucial.
Advantages of Plasma Welding
When compared to other welding methods, plasma welding offers several advantages:
Advantages of Plasma Welding | |
---|---|
Produces high-quality, precise welds | Less heat input, reduced distortion, and a smaller heat-affected zone. |
Can be used on a wider variety of materials | Aluminum, stainless steel, and copper alloys. |
Allows for greater control over the welding process | Precise heat input and arc length control. |
Produces little to no spatter | Creates a clean and precise weld. |
Can be automated for increased efficiency | Allows for faster production times and reduced labor costs. |
Overall, plasma welding offers several advantages over traditional welding methods and is an excellent choice for industries that require high-quality, precise welds.
Comparing Plasma Welding vs Plasma Cutting
Now that we have explored the basics of plasma welding vs plasma cutting in the previous sections, let us have a direct comparison of the two.
Equipment Requirements
Process | Equipment Required |
---|---|
Plasma Welding | Specialized equipment, such as a plasma torch, power supply, and gas control system. The welding material can be tungsten or molybdenum electrode. |
Plasma Cutting | A plasma cutter, which utilizes compressed air, electricity, and an inert gas to cut through materials such as steel, aluminum, and copper. The cutter uses a consumable electrode that directs the plasma flow. |
As you can see, plasma welding requires more specialized equipment than plasma cutting.
Techniques Used
Plasma welding vs plasma cutting require different techniques for the desired results.
- Plasma welding utilizes a direct current power source to create a plasma arc between the electrode and the workpiece. As the arc heats the metal, it melts and fuses with the filler material, resulting in a strong weld.
- Plasma cutting, on the other hand, uses a high-velocity jet of ionized gas to melt the material being cut and blow it away from the workpiece.
Applications
Process | Applications |
---|---|
Plasma Welding | Welding materials that are difficult to work with, such as titanium, cobalt, and nickel alloys. It is also used in aircraft and automotive manufacturing, as well as in the medical and electronics industries. |
Plasma Cutting | The process is used to cut precise shapes and designs in metal sheets, pipes, and plates. It is widely used in the construction, automotive, and HVAC industries. |
Differences Between Plasma Welding vs Plasma Cutting
The main difference between plasma welding vs plasma cutting is their functions. While plasma welding is primarily used for joining metals, plasma cutting is used to cut and shape metals. Additionally, plasma welding requires more specialized equipment and uses a different types of plasma cutting.
By understanding the differences between plasma welding vs plasma cutting, you can determine which process is best suited for your needs.
Conclusion
It is important to understand the differences between plasma welding vs plasma cutting. While plasma cutting involves using plasma to cut through materials, plasma welding involves using plasma to fuse materials together. Both processes offer unique advantages and applications in various industries.
Plasma cutting is commonly used in industries such as automotive, metal fabrication, and construction, offering faster and more precise cutting capabilities than traditional methods. On the other hand, plasma welding is preferred for welding thin and delicate materials, such as aluminum and titanium, due to its precise control and high-quality results.
By understanding the distinctions between plasma cutting vs plasma welding, you can better determine which one is suitable for your specific needs. Whether it’s plasma cutting or plasma welding, both techniques offer valuable solutions in various industries.
So, whether you need to cut thick steel plates or weld thin aluminum pipes, plasma cutting and plasma welding are two techniques that offer reliable and efficient solutions.
FAQ
What is the difference between plasma welding and plasma cutting?
Plasma welding and plasma cutting are two distinct processes. Plasma welding is used to join metal pieces together, while plasma cutting is used to cut through metal. The main difference is the purpose and outcome of each process.
How does plasma cutting work?
Plasma cutting involves using a high-velocity jet of ionized gas (plasma) to melt and remove metal. The plasma is created by passing an electrical arc through a gas, causing it to reach extremely high temperatures. This intense heat melts the metal, and a high-velocity gas stream blows away the molten metal.
What are the advantages of plasma cutting?
Plasma cutting offers several advantages. It can cut through a wide range of metal thicknesses, from thin sheets to thick plates. It provides high cutting speed, precision, and a narrow kerf width. Additionally, plasma cutting doesn’t rely on flammable gases and can be used on various metals.
What is plasma welding?
Plasma welding is a process that uses a high-temperature, ionized gas (plasma) to generate heat and join metal parts together. It creates a concentrated and controlled heat source, resulting in a smooth and precise weld. Plasma welding is commonly used for applications that require high-quality welds on materials such as stainless steel, aluminum, and titanium.
How does plasma welding differ from traditional welding?
Plasma welding differs from traditional welding methods in several ways. Traditional welding typically relies on a filler metal, while plasma welding can be performed without using a filler. Additionally, plasma welding offers greater control over the heat input, resulting in less distortion and improved weld quality.
What are the advantages of plasma welding?
Plasma welding offers several advantages over traditional welding methods. It provides precise control over the heat input, resulting in high-quality welds with minimal distortion. Plasma welding can also be performed at higher speeds, increasing productivity. Additionally, it allows for welding of thin materials without the need for additional support.
How do plasma welding and plasma cutting differ?
While both processes involve the use of plasma, plasma welding and plasma cutting serve different purposes. Plasma welding is used to join metal parts together, while plasma cutting is used to cut through metal. The techniques, equipment, and objectives of plasma welding and plasma cutting are distinct.
Which process should I choose, plasma welding or plasma cutting?
The choice between plasma welding and plasma cutting depends on your specific needs. If you need to join metal parts together, plasma welding is the appropriate process. On the other hand, if you need to cut through metal, plasma cutting is the suitable method. Consider factors such as the desired outcome, material type, and project requirements to make an informed decision.