MIG welding, also known as Gas Metal Arc Welding (GMAW), is a versatile and efficient method that has gained widespread popularity for its ability to create strong and enduring bonds. When it comes to working with copper, MIG welding emerges as a reliable solution, offering the means to produce durable and conductive joints. In this comprehensive guide, we will delve into the intricacies of MIG welding copper, exploring the techniques, considerations, and equipment necessary to master this specialized process.
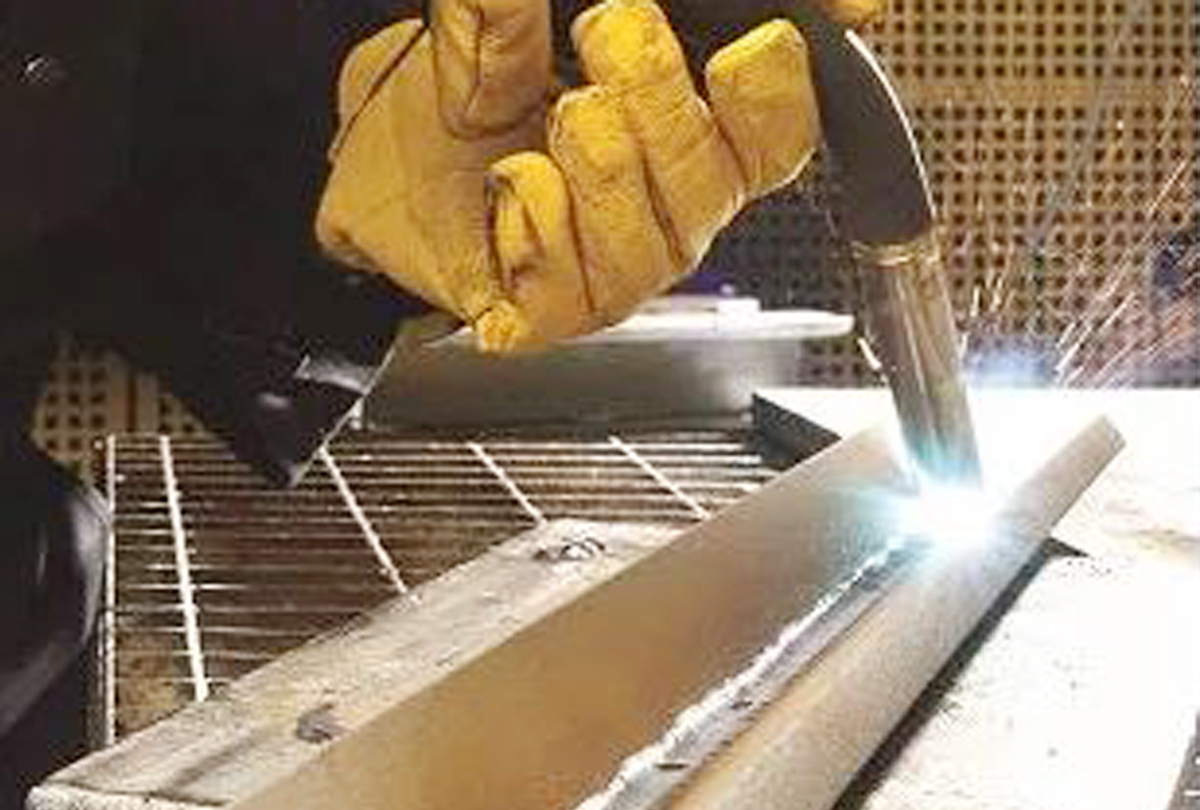
Understanding the Basics of MIG Welding
MIG welding involves the use of a continuously fed wire electrode and a shielding gas to create the weld. The process is known for its high deposition rates and versatility across various materials. When applied to copper, MIG welding offers the advantage of producing clean and efficient welds, making it a preferred choice for a wide range of applications. Understanding the fundamental principles of MIG welding is crucial for achieving precise and durable copper welds.
Copper, with its exceptional electrical and thermal conductivity, presents unique properties that require specific considerations when applying MIG welding techniques. Its high melting point and thermal conductivity necessitate careful control of heat input to achieve optimal results. The ductility and malleability of copper demand a nuanced approach to welding, ensuring that the material retains its integrity and conductivity during the welding process.
The Unique Properties of Copper for MIG Welding
Copper, as a material for welding, offers a host of advantages that make it highly desirable for various applications. Its exceptional electrical and thermal conductivity, corrosion resistance, and malleability contribute to its widespread use in electrical and plumbing systems, as well as in artistic and decorative metalwork. When MIG welding copper, these unique properties open up opportunities to create durable and efficient joints that meet the demands of diverse projects.
The high thermal and electrical conductivity of copper requires specific considerations when applying MIG welding techniques. Managing heat input and achieving proper penetration are critical to producing strong and reliable welds. Additionally, the ductility and malleability of copper necessitate precise control over welding parameters to prevent deformation and ensure the structural integrity of the welded joints.
Advantages of MIG Welding Copper
MIG welding offers several distinct advantages when applied to copper. The process allows for high deposition rates, enabling efficient and rapid welding of copper components. Additionally, MIG welding produces minimal spatter, resulting in clean and precise welds that require minimal post-weld cleanup. The use of a shielding gas further enhances the quality of the weld by protecting the molten metal from atmospheric contamination.
MIG welding provides excellent control over the welding parameters, allowing for precise adjustment of heat input and weld penetration. This level of control is essential when working with copper, as it ensures that the material’s unique properties are preserved, ultimately leading to durable and conductive welds. The versatility and efficiency of MIG welding make it an ideal choice for a wide range of copper welding applications.
Challenges and Considerations When Welding Copper with MIG
While MIG welding offers numerous benefits for copper welding, it also presents specific challenges that require careful consideration. Copper’s high thermal conductivity can result in rapid heat dissipation, making it essential to adjust welding parameters to compensate for this characteristic. Controlling heat input and managing the welding environment are crucial elements in overcoming this challenge.
The potential for copper to form an oxide layer during welding necessitates the use of appropriate shielding gases to prevent oxidation and ensure the integrity of the weld. Proper surface preparation and cleaning are essential to remove any contaminants or oxide layers from the copper, facilitating optimal weld quality. By addressing these challenges and considerations, welders can achieve successful and reliable copper welds using MIG welding techniques.
Equipment and Materials Needed for MIG Welding Copper
To effectively MIG welding copper, specific equipment and materials are required to ensure the successful execution of the welding process. The primary components include a MIG welding machine capable of handling copper, a suitable wire feeder, and a compatible shielding gas. In addition to the welding equipment, the selection of filler metal is a critical consideration when welding copper with MIG.
Copper welding wire, typically composed of a high copper content alloy, is used as the filler metal in MIG welding applications. The choice of filler metal is crucial, as it directly impacts the mechanical and electrical properties of the weld. Selecting the appropriate wire diameter and composition is essential for achieving the desired weld characteristics, such as conductivity, strength, and corrosion resistance. By ensuring that the equipment and materials are well-suited for MIG welding copper, welders can optimize the quality and durability of their copper welds.
Techniques for Successful MIG Welding of Copper
Mastering the techniques for MIG welding copper is essential to achieve precise, durable, and conductive welds. Controlling heat input, managing welding parameters, and ensuring proper joint preparation are fundamental aspects of successful copper welding. Adjusting the wire feed speed, voltage, and shielding gas flow rate allows for fine-tuning the welding process to suit the specific requirements of copper welding.
Proper joint fit-up and cleanliness are critical for achieving high-quality copper welds. Careful attention to welding technique, such as maintaining a consistent travel speed and angle, is essential for producing uniform and reliable welds. Additionally, understanding the interactions between the welding parameters and the unique properties of copper is key to mastering the art of MIG welding for copper applications.
Safety Precautions for MIG Welding Copper
As with any welding process, safety is paramount when MIG welding copper. The use of appropriate personal protective equipment (PPE), including welding helmets, gloves, and clothing, is essential to protect against potential hazards such as arc flash, heat, and fumes. Furthermore, ensuring adequate ventilation in the welding environment and adhering to proper welding procedures are crucial for minimizing health and safety risks.
The handling of shielding gases and the proper setup of the welding equipment also require attention to safety protocols. Understanding the potential hazards associated with MIG welding and implementing comprehensive safety measures are essential for creating a secure and healthy work environment. By prioritizing safety in MIG welding operations, welders can mitigate risks and focus on achieving exceptional results in copper welding.
Common Mistakes to Avoid When MIG Welding Copper
In the process of MIG welding copper, several common mistakes can detract from the quality and integrity of the welds. Inadequate surface preparation, such as failing to remove oxide layers or contaminants from the copper, can compromise the weld’s strength and conductivity. Improper shielding gas selection or flow rate may lead to oxidation or atmospheric contamination, affecting the weld’s quality.
Overheating the copper during welding can result in excessive heat input, leading to deformation and reduced electrical conductivity. Insufficient penetration or incomplete fusion at the weld joint can compromise the mechanical strength of the weld. Awareness of these common mistakes and proactive measures to address them are essential for achieving successful MIG welding outcomes in copper applications.
Applications and Uses of MIG Welding Copper Products
The versatility and durability of MIG-welded copper products make them well-suited for a wide range of applications across various industries. In electrical and electronic systems, MIG-welded copper components provide reliable and efficient conductive connections, ensuring optimal performance and longevity. Plumbing and HVAC systems benefit from the durability and corrosion resistance of MIG-welded copper pipes and fittings.
Artistic and decorative metalwork also leverage MIG-welded copper for creating intricate and visually captivating designs. The ability to produce clean and precise welds with MIG welding enhances the aesthetic appeal and structural integrity of copper artwork. Furthermore, industrial and manufacturing sectors utilize MIG welding copper for fabricating components that demand high electrical and thermal conductivity, as well as exceptional durability.
Conclusion
MIG welding copper offers a unique set of challenges and rewards, requiring a thorough understanding of the material’s properties and the intricacies of the welding process. By mastering the techniques, considerations, and equipment specific to MIG welding copper, welders can unlock the full potential of this versatile material. The ability to create durable, conductive, and aesthetically pleasing copper welds opens up opportunities for innovation and excellence across diverse fields, from electrical and plumbing systems to artistic and industrial applications. With the knowledge and insights gained from this comprehensive guide, aspiring and experienced welders alike can elevate their craftsmanship and achieve exceptional results in MIG welding copper.