Looking to delve into the cutting-edge world of hot air plastic welding? This innovative technique is revolutionizing the way plastic fabrication and repairs are conducted, offering a seamless and durable join that’s perfect for a wide range of applications. Whether you’re a professional in the manufacturing industry or a DIY enthusiast, understanding the ins and outs of hot air plastic welding can be invaluable. From its eco-friendly nature to its versatility in bonding various types of thermoplastics, the possibilities with hot air welding are endless.
In this comprehensive guide, we will explore the fundamentals of hot air plastic welding, the equipment needed, and the step-by-step process to achieve impeccable results. Get ready to unlock the potential of hot air plastic welding and take your projects to the next level.
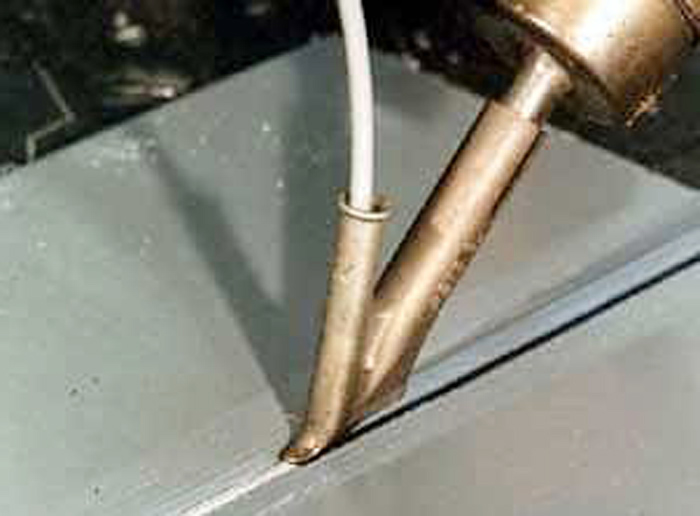
Photo by twi-global.com
Understanding Process of Hot Air Plastic Welding
Hot air plastic welding is a technique that uses heated air to soften the surfaces of thermoplastics, allowing them to be joined together seamlessly. This process involves the use of specialized tools and equipment, which we’ll delve into in more detail later. The key to successful hot air welding lies in achieving the optimal temperature and airflow to ensure a strong and durable bond between the plastic pieces. The principles of heat transfer and material properties is crucial for mastering hot air plastic welding techniques. Whether you’re working on small-scale repairs or large-scale fabrication projects, having a solid grasp of the fundamentals is essential for achieving professional results.
Hot air plastic welding is a versatile method that can be used for a wide range of applications, including but not limited to, repairing plastic components, fabricating custom plastic structures, and even creating airtight seals. Its ability to create strong and durable bonds makes it a preferred choice in industries such as automotive, construction, and manufacturing. By understanding the intricacies of hot air plastic welding, you’ll be equipped with the knowledge to tackle diverse projects with confidence and precision.
Mastering the art of hot air plastic welding opens up a world of possibilities for professionals and DIY enthusiasts alike. Whether you are looking to enhance your skill set for professional advancement or seeking to complete intricate plastic fabrication projects with ease, hot air welding offers a wealth of opportunities. With the right knowledge and techniques at your disposal, you’ll be able to achieve seamless and durable plastic joins that meet the highest standards of quality and performance.
Advantages of Hot Air Plastic Welding
One of the primary advantages of hot air plastic welding is its eco-friendly nature. Unlike traditional adhesives or solvent-based joining methods, hot air welding does not rely on additional consumables that may contain harmful chemicals or produce waste. By utilizing heat and pressure to fuse thermoplastics together, hot air welding promotes sustainability and environmental responsibility in plastic fabrication and repair processes. This makes it an appealing choice for industries and individuals committed to reducing their ecological footprint and promoting green practices.
Another notable advantage of hot air plastic welding is its versatility in bonding various types of thermoplastics. Whether you are working with polyethylene, polypropylene, PVC, or other thermoplastic materials, hot air welding offers a reliable and effective joining method. This flexibility makes it a valuable technique for professionals who encounter a diverse range of plastic materials in their work. With the ability to create strong and durable bonds across different thermoplastics, hot air welding provides a universal solution for various fabrication and repair needs.
In addition to its eco-friendly and versatile nature, hot air welding offers exceptional strength and durability in the resulting joins. When executed with precision and expertise, hot air welding produces seamless bonds that exhibit high tensile strength and resistance to environmental factors. This makes it an ideal choice for applications that require robust and long-lasting plastic joins, such as structural components, fluid containment systems, and custom plastic assemblies. By harnessing the advantages of hot air welding, professionals and hobbyists can achieve superior results in their plastic fabrication and repair endeavors.
Types of Plastics Suitable for Hot Air Welding
Hot air plastic welding is compatible with a wide range of thermoplastic materials, each with its own unique properties and applications. The characteristics of different plastics is essential for determining their suitability for hot air welding and optimizing the welding process accordingly. Common thermoplastics suitable for air welding include polyethylene, polypropylene, PVC, ABS, polycarbonate, and acrylics, among others. Each type of plastic exhibits distinct melting points, flow properties, and chemical compositions, which influence the hot air welding parameters and techniques required for successful joins.
Polyethylene, for example, is a widely used thermoplastic known for its high chemical resistance and low moisture absorption. When hot air welding polyethylene, it’s crucial to maintain precise temperature control to achieve a strong bond without compromising the material’s integrity. Polypropylene, on the other hand, offers excellent resistance to fatigue and stress cracking, making it a popular choice for applications requiring durability and flexibility. The specific characteristics of polypropylene is essential for optimizing the air welding process and ensuring reliable joins.
PVC, a versatile thermoplastic known for its durability and chemical resistance, is commonly hot air welded in applications ranging from plumbing to signage fabrication. The unique properties of PVC, including its flame-retardant nature and excellent electrical insulation, make it a preferred material for various industrial and commercial uses. By understanding the distinct properties of PVC and other thermoplastics, welders can tailor their hot air welding techniques to achieve precise and reliable joins that meet the specific requirements of each material.
In addition to the aforementioned thermoplastics, ABS, polycarbonate, and acrylics are also commonly hot air welded for a wide range of applications. Each type of plastic presents its own set of considerations and challenges when it comes to hot air welding, requiring welders to adapt their techniques and equipment settings accordingly. By familiarizing yourself with the characteristics of different thermoplastics, you’ll be better equipped to tackle diverse hot air welding projects with confidence and proficiency.
Hot Air Plastic Welding Equipment
To achieve professional results in hot air plastic welding, it’s essential to have the right equipment at your disposal. The following are the key components of hot air welding equipment:
- Hot Air Welding Gun: A hot air welding gun, also known as a heat gun or hot air gun, is the primary tool used to deliver heated air to the plastic surfaces being joined. These guns are equipped with adjustable temperature and airflow settings, allowing welders to customize the heat output based on the specific requirements of the materials being welded. Hot air welding guns come in various sizes and configurations, catering to a wide range of welding applications.
- Welding Nozzles and Attachments: Different welding nozzles and attachments are available to accommodate various welding scenarios and project requirements. These accessories help direct and control the flow of heated air, enabling precise manipulation of the welding process. From narrow tip nozzles for detailed work to wide slot nozzles for broader welds, the selection of welding nozzles and attachments plays a crucial role in achieving optimal welding results.
- Welding Rods: In some hot air welding applications, welding rods, also known as filler rods, are used to reinforce the welded joint and fill any gaps or voids in the plastic surfaces. These rods are typically made from the same material as the base plastic, ensuring compatibility and uniformity in the welded structure. By selecting the appropriate welding rods and mastering the technique of rod incorporation, welders can enhance the strength and integrity of their hot air welded joints.
- Temperature and Airflow Controls: Many modern hot air welding guns are equipped with precise temperature and airflow controls, allowing welders to fine-tune the heat output and air velocity for optimal welding conditions. The ability to adjust these parameters in real time empowers welders to adapt to changing material properties and welding scenarios, ultimately leading to superior welding results.
- Welding Workstation and Fixtures: A well-equipped welding workstation provides a stable and organized environment for conducting hot air plastic welding. Fixtures and clamping devices may be employed to hold the plastic pieces in position during the welding process, ensuring accurate alignment and consistent joint quality. The layout and setup of the welding workstation play a crucial role in facilitating efficient and precise hot air welding operations.
- Safety Gear and Ventilation Equipment: As with any welding process, hot air plastic welding requires the use of appropriate safety gear and ventilation equipment to protect the welder from potential hazards. This may include protective gloves, safety glasses, respiratory masks, and adequate ventilation systems to minimize exposure to airborne contaminants and fumes. Prioritizing safety measures is essential for creating a secure working environment and preventing occupational hazards associated with hot air plastic welding.
By equipping yourself with the right hot air welding tools and accessories, you’ll be well-prepared to tackle a diverse range of plastic welding projects with confidence and precision. Whether you’re working on small-scale repairs or large-scale fabrication, having the appropriate equipment at your disposal is fundamental to achieving professional results in hot air plastic welding.
Steps for Hot Air Plastic Welding
Achieving impeccable results in hot air plastic welding requires a systematic approach and attention to detail. The following steps outline the fundamental process for conducting hot air plastic welding:
- Surface Preparation: Begin by preparing the surfaces of the plastic pieces to be welded. This may involve cleaning the surfaces to remove contaminants, roughening the bonding area to enhance adhesion, and ensuring proper alignment of the components. Surface preparation is crucial for promoting strong and reliable welds.
- Temperature and Airflow Adjustment: Set the hot air welding gun to the appropriate temperature and airflow settings based on the specific requirements of the thermoplastic materials being welded. It’s essential to refer to the material specifications and welding guidelines to determine the optimal heat output and air velocity for the given plastics.
- Heating and Softening: Direct the heated air from the welding gun onto the bonding surfaces of the plastic pieces, gradually heating and softening the material. The goal is to achieve a consistent and uniform softening of the plastic surfaces without causing overheating or degradation. Careful control of the heating process is essential for successful welding.
- Welding Rod Incorporation (If Applicable): If welding rods are being used to reinforce the joint, carefully incorporate the welding rod into the softened plastic interface. The rod should melt and fuse with the base material, creating a homogeneous and reinforced weld. Proper technique and rod material selection are critical for achieving a strong and durable joint.
- Pressure and Fusion: Once the plastic surfaces are adequately softened, apply gentle pressure to bring the softened materials into contact with each other. This promotes fusion and intermingling of the plastic molecules, creating a strong and seamless bond. The application of pressure should be uniform and controlled to ensure consistent weld quality.
- Cooling and Solidification: Allow the welded joint to cool and solidify under controlled conditions. This may involve gradually reducing the heat input and ensuring that the welded assembly maintains structural integrity during the cooling process. Proper cooling is essential for stabilizing the weld and achieving optimal mechanical properties.
- Post-Weld Inspection: After the weld has cooled, conduct a thorough inspection of the welded joint to assess its quality and integrity. Check for any signs of voids, irregularities, or inadequate fusion. If necessary, perform additional steps to address any deficiencies and ensure the weld meets the desired specifications.
By following these step-by-step guidelines and exercising precision and care throughout the hot air welding process, you will be able to achieve exceptional results in your plastic welding projects. Each stage of the welding process plays a critical role in determining the strength, durability, and visual appearance of the final weld, making it essential to adhere to best practices and established techniques.
Safety Precautions for Hot Air Plastic Welding
Prioritizing safety is paramount when engaging in hot air plastic welding activities. The following safety precautions should be observed to minimize risks and ensure a secure working environment:
- Personal Protective Equipment (PPE): Wear appropriate personal protective equipment, including safety glasses, heat-resistant gloves, and respiratory masks, to shield yourself from potential hazards associated with hot air welding. PPE helps mitigate the risk of injury and exposure to airborne contaminants.
- Ventilation and Fume Extraction: Work in a well-ventilated area or utilize fume extraction systems to remove airborne fumes and particulates generated during the hot air welding process. Proper ventilation minimizes the inhalation of potentially harmful substances and promotes a healthier work environment.
- Fire Safety Measures: Be mindful of fire safety protocols and avoid working near flammable materials or sources of ignition. Hot air welding involves the use of heat, making it essential to prevent potential fire hazards and maintain a safe workspace.
- Equipment Maintenance and Inspection: Regularly inspect and maintain hot air welding equipment to ensure it is in optimal working condition. Malfunctioning tools and accessories can pose safety risks and compromise the quality of welds, making equipment maintenance a crucial aspect of safety management.
- Training and Education: Invest in comprehensive training and education in hot air plastic welding techniques and safety practices. By equipping yourself and your team with the necessary knowledge and skills, you can minimize the likelihood of accidents and errors during welding operations.
By adhering to these safety precautions and fostering a safety-conscious work environment, you can mitigate potential risks associated with hot air plastic welding and promote the well-being of everyone involved in the welding process. Safety should always remain a top priority in any welding endeavor, ensuring that projects are completed with the utmost care and consideration for occupational health and safety.
Applications of Hot Air Plastic Welding
The versatility and reliability of hot air welding make it suitable for a diverse array of applications across various industries. Some common applications of hot air welding include:
- Automotive Repairs: Hot air plastic welding is widely used in the automotive industry for repairing plastic components, such as bumpers, interior trim panels, and ducting systems. The ability to achieve seamless and durable repairs makes hot air welding a preferred choice for restoring the structural and aesthetic integrity of automotive plastic parts.
- Construction and Fabrication: In the construction sector, air plastic welding is employed for fabricating custom plastic structures, sealing membranes, and joining plastic pipes and fittings. Its strength and versatility make it a valuable technique for creating robust and weather-resistant plastic assemblies in construction projects.
- Marine and Aquatic Applications: Hot air welding is utilized in marine and aquatic environments for fabricating and repairing plastic components used in boats, watercraft, and other marine equipment. Its resistance to moisture and environmental factors
Final Thoughts
As you have learned, hot air plastic welding is a fantastic option for joining multiple pieces of plastic material together. Not only is the process quick and efficient, but it also has an incredibly low failure rate when done correctly. And the best part is that with the right tools, it can be done even in saving yourself money from having to hire a professional welder. So if you are looking for an effective way to join materials quickly and affordably, then hot air plastic welding could be just what you have been searching for. Now all that’s left to do is find some high-quality tools and start getting creative with your projects.