Are you considering spot welding galvanized steel for your upcoming project? This method offers a slew of benefits, but it’s crucial to understand the specifics to ensure successful and durable outcomes. Galvanized steel is designed to withstand corrosion, but the welding process can alter its protective zinc coating, impacting its corrosion resistance. In this article, we will delve into the ins and outs of spot welding galvanized steel, covering the best practices to maintain the integrity of the coating and achieve strong welds.
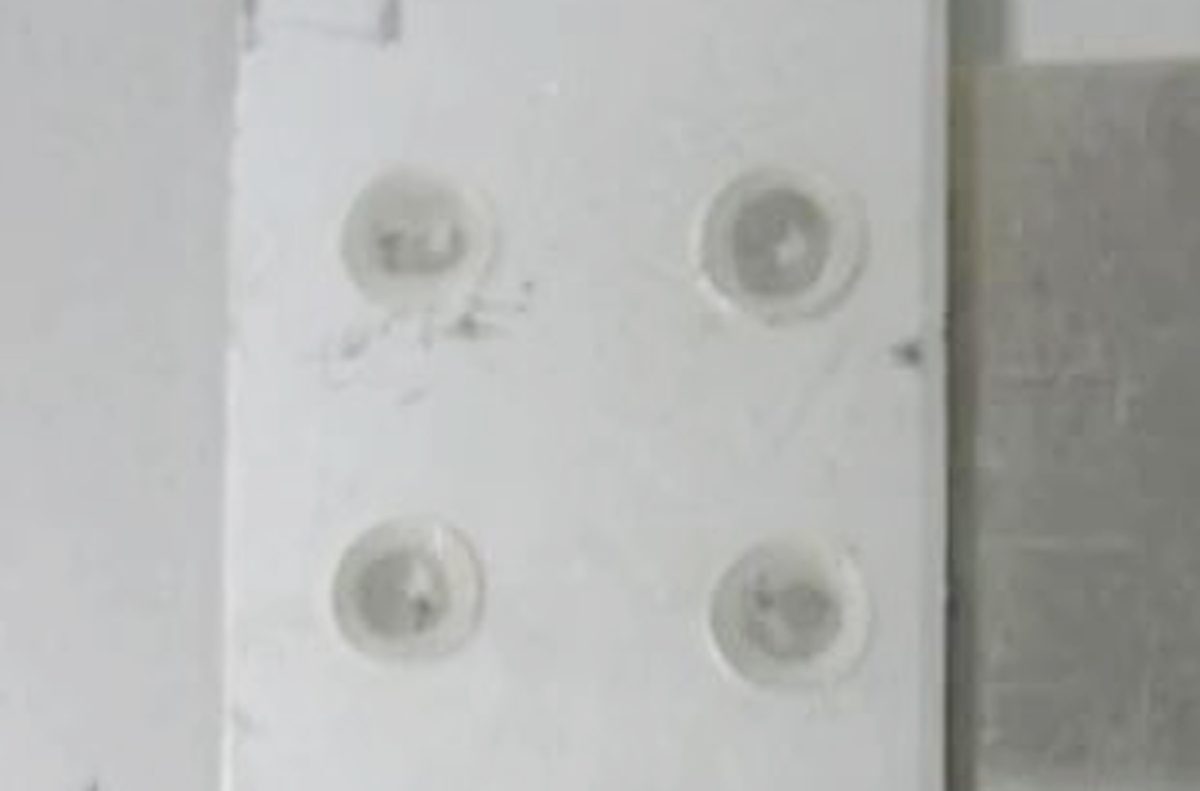
Photos by kiaind.en.made-in-china
With decades of experience in the industry, we understand the intricacies involved in welding galvanized steel. We will provide you with expert insights and practical tips to optimize your welding process, taking into account factors such as electrode selection, proper ventilation to mitigate fumes, and post-weld coating restoration techniques. Whether you’re a seasoned professional or new to welding galvanized steel, our comprehensive guide will equip you with the knowledge to execute spot welding with precision and confidence.
About Spot Welding Galvanized Steel
Spot welding, also known as resistance spot welding, is a popular method for joining metal sheets in various industries, including automotive, construction, and manufacturing. This process involves applying pressure and heat to the metal sheets using copper alloy electrodes, creating a strong and durable bond. Galvanized steel, on the other hand, is steel coated with a layer of zinc to protect it from corrosion. The zinc coating provides an additional layer of defense against environmental elements, making galvanized steel a preferred choice for outdoor and high-moisture applications.
When spot welding galvanized steel, it’s essential to consider the interaction between the zinc coating and the welding process. The heat generated during welding can vaporize the zinc, leading to the formation of zinc oxide fumes. These fumes pose health risks to the welder and can also affect the quality of the weld. The welding process can compromise the integrity of the zinc coating, potentially reducing the steel’s corrosion resistance in the welded areas. Understanding these interactions is crucial for achieving successful spot welds on galvanized steel while preserving its protective properties.
Advantages and Challenges of Spot Welding Galvanized Steel
Spot welding galvanized steel offers several advantages, making it a preferred method for joining galvanized metal sheets. The process is fast, efficient, and cost-effective, allowing for high production rates in industrial settings. Additionally, spot welding creates a strong and consistent bond, ensuring structural integrity and durability in the welded components. The ability to automate spot welding further enhances its appeal, especially in mass production environments where precision and speed are critical.
However, spot welding galvanized steel comes with its set of challenges. The presence of the zinc coating introduces complexities to the welding process, requiring careful consideration of parameters such as welding current, pressure, and time to achieve optimal results. The formation of zinc oxide fumes necessitates proper ventilation and safety measures to protect the welder and maintain a healthy work environment. Balancing the benefits and challenges of spot welding galvanized steel is essential for maximizing its advantages while mitigating potential drawbacks.
Spot Welding Galvanized Steel Process
The spot welding process for galvanized steel involves several key steps to ensure a successful and durable weld. Before initiating the welding operation, it’s crucial to prepare the metal surfaces by removing any contaminants, such as oil, grease, or dirt, that can interfere with the welding process. Proper cleaning and pre-treatment of the galvanized steel surfaces help promote adhesion and minimize the risk of weld defects.
Once the surfaces are prepared, the next step is to set up the spot welding equipment and select the appropriate welding parameters. This includes adjusting the welding current, electrode force, and welding time to achieve proper fusion and bonding of the metal sheets. It’s important to note that the welding parameters for galvanized steel may differ from those used for uncoated steel due to the presence of the zinc coating.
During the welding operation, the electrodes apply pressure to the metal sheets, creating a localized heating effect at the contact points. The heat generated softens the metal surfaces, allowing for the formation of a strong metallurgical bond. However, it’s essential to monitor the welding process closely to prevent excessive vaporization of the zinc coating, which can lead to weld spattering and compromised corrosion resistance.
Factors to Consider for Successful Spot Welding Galvanized Steel
Achieving successful spot welds on galvanized steel requires careful consideration of several factors that can influence the welding process and the quality of the resulting welds. One of the critical factors is electrode selection. Copper alloy electrodes are commonly used for spot welding galvanized steel due to their excellent conductivity and resistance to sticking. The choice of electrode shape and surface condition also plays a significant role in achieving consistent and high-quality welds.
In addition to electrode selection, the welding current and time settings must be optimized to account for the presence of the zinc coating. Excessive heat can vaporize the zinc, leading to weld spatter and reduced corrosion resistance, while insufficient heat may result in inadequate fusion of the metal sheets. Finding the right balance of welding parameters is essential for achieving strong and durable spot welds on galvanized steel.
Another crucial factor to consider is the post-weld coating restoration. The welding process can alter the zinc coating in the vicinity of the weld, potentially compromising its corrosion resistance. Implementing post-weld coating restoration techniques, such as zinc-rich paint application or thermal spraying, can help reestablish the protective properties of the zinc coating, ensuring long-term durability and corrosion protection in the welded areas.
Precautions and Safety Measures for Spot Welding Galvanized Steel
When spot welding galvanized steel, it’s paramount to prioritize safety and implement necessary precautions to protect the welder and maintain a safe working environment. As mentioned earlier, the formation of zinc oxide fumes during welding poses health risks, including metal fume fever, respiratory irritation, and other adverse effects. Therefore, adequate ventilation, such as local exhaust systems or respiratory protection, is essential to control and mitigate the exposure to zinc oxide fumes.
Additionally, proper personal protective equipment (PPE), including respiratory masks, gloves, and protective clothing, should be worn to minimize direct contact with zinc oxide fumes and prevent skin irritation. Employers and welders should be aware of the potential hazards associated with welding galvanized steel and undergo training on safe practices, emergency procedures, and the proper use of protective equipment.
Furthermore, maintaining a clean work environment and implementing good housekeeping practices can help minimize the accumulation of zinc oxide residues and reduce the risk of exposure. Regular equipment maintenance and inspection, particularly for ventilation systems and welding apparatus, are essential to ensure their effectiveness in controlling fume emissions and safeguarding the well-being of the welding personnel.
Common Issues and Troubleshooting in Spot Welding Galvanized Steel
Spot welding galvanized steel can encounter various issues that may compromise the quality of the welds and the integrity of the zinc coating. One common issue is the formation of weld spatter, which occurs when excessive heat vaporizes the zinc coating, leading to the ejection of molten zinc particles onto the surrounding surfaces. Weld spatter not only mars the appearance of the welded components but also diminishes the corrosion resistance of the affected areas.
To address weld spatter and other related issues, it’s crucial to implement effective troubleshooting strategies. Adjusting the welding parameters, such as reducing the welding current or optimizing the electrode force and time, can help minimize the vaporization of the zinc coating and mitigate weld spatter formation. Proper cleaning and pre-treatment of the metal surfaces, as well as the use of anti-spatter coatings, can aid in preventing and managing weld spatter during spot welding.
Another common issue in spot welding galvanized steel is the potential for weld nugget expulsion, where the molten metal is expelled from the weld zone, resulting in incomplete fusion and weak welds. This issue can be attributed to inadequate welding parameters or improper electrode alignment, emphasizing the importance of precise setup and control during the spot welding process.
Addressing these common issues through proactive troubleshooting and corrective measures is essential for maintaining the quality and integrity of spot welds on galvanized steel, ensuring the durability and performance of the welded components in service.
Welding Equipment and Materials for Spot Welding Galvanized Steel
Selecting the appropriate welding equipment and materials is crucial for achieving successful spot welds on galvanized steel. The choice of spot welding machine, including its power capacity, control features, and electrode configuration, can significantly impact the welding process and the quality of the resulting welds. It’s essential to select a spot welding machine that is designed to accommodate the specific requirements of spot welding galvanized steel, including the ability to control welding parameters and electrode pressure.
In addition to the welding machine, the selection of electrodes and consumables is equally important. Copper alloy electrodes, typically composed of copper with small additions of other elements such as chromium or zirconium, are preferred for spot welding galvanized steel due to their excellent electrical conductivity and resistance to sticking. The surface condition of the electrodes, such as smoothness and cleanliness, also influences the welding performance and the prevention of weld defects.
The availability of high-quality welding materials, including galvanized steel sheets and supplementary coatings or treatments for post-weld restoration, contributes to the overall success of spot welding galvanized steel. Employing materials that meet industry standards and specifications ensures the integrity and performance of the welded components in various applications and environments.
Best Practices for Spot Welding Galvanized Steel
To achieve optimal results and ensure the longevity of spot welds on galvanized steel, it’s essential to adhere to best practices that encompass the entire welding process, from preparation to post-weld treatments. Proper surface preparation, including cleaning and pre-treatment of the galvanized steel sheets, sets the foundation for successful spot welding by promoting adhesion and minimizing contamination.
Selecting the appropriate welding parameters, such as current, time, and electrode force, tailored to the characteristics of galvanized steel helps achieve consistent and durable spot welds while minimizing the impact on the zinc coating. Monitoring the welding operation and inspecting the quality of the welds are critical steps to verify the integrity and strength of the bond, ensuring that the welded components meet the desired performance requirements.
Implementing effective post-weld coating restoration techniques, such as the application of zinc-rich paint or thermal spraying, in the welded areas helps rejuvenate the protective properties of the zinc coating, restoring its corrosion resistance and durability. Adhering to safety measures and precautions, including proper ventilation, personal protective equipment, and good housekeeping practices, safeguards the well-being of the welding personnel and maintains a healthy work environment.
Spot Welding Galvanized Steel in Industry Applications
Spot welding galvanized steel finds widespread applications across various industries, leveraging its advantages in terms of speed, efficiency, and structural integrity. In the automotive sector, spot welding is extensively used for assembling vehicle bodies, joining galvanized steel panels to create robust and lightweight structures. The construction industry also benefits from spot welding galvanized steel, incorporating welded components in building frameworks, roofing systems, and structural elements that require corrosion resistance and longevity.
Moreover, the manufacturing sector relies on spot welding galvanized steel for fabricating diverse products, including appliances, furniture, and industrial equipment, where the combination of galvanized steel’s protective properties and spot welding’s efficiency contributes to the production of high-quality and durable goods. The versatility and reliability of spot welding galvanized steel make it an indispensable joining method in industries that prioritize performance, longevity, and cost-effectiveness in their products and structures.
Future of Spot Welding Galvanized Steel
Spot welding galvanized steel presents an effective and versatile method for joining galvanized metal sheets, offering a balance of advantages and challenges that require careful consideration and expertise. Understanding the intricacies of the welding process, including the interaction with the zinc coating, and implementing best practices and safety measures are essential for achieving successful and durable spot welds on galvanized steel.
As technology and materials continue to evolve, the future of spot welding galvanized steel holds promise for further advancements in process optimization, automation, and the development of specialized equipment and materials tailored to the unique requirements of welding galvanized steel. With ongoing research and innovation, the industry is poised to enhance the efficiency, quality, and sustainability of spot welding galvanized steel, reinforcing its position as a preferred joining method in diverse applications and industries.
Conclusion
Spot welding galvanized steel offers a myriad of benefits, but it’s essential to navigate the intricacies to ensure successful outcomes. This comprehensive guide equips you with the knowledge and insights to execute spot welding with precision and confidence, maximizing the potential of galvanized steel in your projects and applications.
This comprehensive guide provides valuable insights and practical tips for spot welding galvanized steel, addressing the nuances of the process and the best practices to achieve strong and durable welds. Whether you’re a seasoned professional or new to welding galvanized steel, our expert guidance empowers you to navigate the complexities and optimize your welding process with confidence and precision.
Do you have any questions or need further assistance with spot welding galvanized steel? We’re here to help you elevate your welding capabilities and achieve outstanding results. Feel free to reach out to us for personalized support and expert advice tailored to your specific welding needs and projects. Unlock the full potential of spot welding galvanized steel and elevate your welding endeavors with our industry-leading expertise and guidance.