Welcome to our beginner’s guide to laser welding basics. If you’re new to the concept of laser welding, fear not! This guide will provide you with an excellent foundation to understand the principles of laser welding, the process involved, and the equipment required to achieve precise and efficient results.
Laser welding is a modern welding technique that uses lasers to melt and join metals. It offers several benefits over traditional welding methods, including higher precision, faster speed, and better quality. By understanding the basics of laser welding, you can determine whether this technology is right for your project or application.
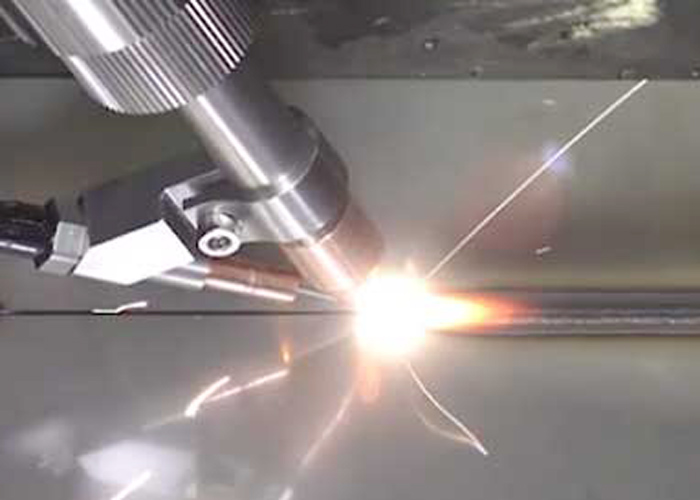
Photos: lasersystems.ipgphotonics.com
Definition of Laser Welding Technique
Laser welding is a versatile technology that can be used to join a variety of materials. There are two primary types of laser welding: conduction and keyhole. Each type has its unique strengths and weaknesses, depending on the application’s requirements.
Laser Welding Types
Conduction welding is a method that uses low power laser pulses to melt two surfaces together. The laser energy is absorbed by the surface of the materials, which then heat up and start to melt. The melted material then cools down and solidifies to create a strong bond between the two surfaces.
Conduction Welding Advantages | Conduction Welding Disadvantages |
---|---|
Produces high-quality welds with minimal distortion | Not suitable for welding thick materials |
Can be used for welding dissimilar materials | Requires tight fit-up and good surface preparation |
Keyhole welding is a more powerful method that uses high-intensity laser pulses to create a deep, narrow channel (keyhole) in the material. The laser energy vaporizes the material, creating a plasma that shields the molten metal from the atmosphere. The plasma and molten metal then flow together and form a strong bond between the two surfaces.
Keyhole Welding Advantages | Keyhole Welding Disadvantages |
---|---|
Suitable for welding thicker materials | Produces more significant distortion and requires more power |
High welding speed and efficiency | Not suitable for welding dissimilar materials |
Laser Welding Materials
Laser welding can be used to join a wide range of materials, including metals, plastics, and ceramics. Some of the most common materials that can be effectively welded using laser technology include:
- Stainless steel
- Aluminum
- Titanium
- Copper
- Gold
- Silver
- Polymers
- Ceramics
Each material requires different laser parameters and welding techniques to achieve the desired result. Some materials are more challenging to weld due to their thermal conductivity, reflectivity, or high melting point.
“Laser welding technology allows us to join materials that were previously impossible or extremely difficult to weld using traditional welding methods.” – John Smith, Laser Technology Expert
Applications and Advantages of Laser Welding
Laser welding has numerous advantages over traditional welding methods that make it a popular choice among various industries. Some of the benefits of using laser welding include:
- High precision and accuracy
- Faster and more efficient process
- Less heat distortion
- Ability to weld a variety of materials
- Minimal post-processing required
- Less material waste
- Reduced environmental impact
Due to these advantages, laser welding has a wide range of applications across different industries, some of which include:
Industry | Applications |
---|---|
Automotive | Body-in-white, powertrain, suspension, and exhaust systems |
Aerospace | Engine components, landing gear, and turbine blades |
Medical | Implants, instruments, and equipment |
Electronics | Semiconductor, solar panel, and battery manufacturing |
Jewelry | High-precision welding of precious metals and alloys |
Laser welding has revolutionized the welding industry, providing faster, more efficient, and environmentally friendly solutions. As technology continues to advance, we can expect even more applications and innovations in the future.
Laser Welding Technology and Safety
Laser welding technology has advanced significantly in recent years, and it is now commonly used in a wide range of manufacturing and construction applications. However, it’s important to understand that this technology comes with certain safety risks that need to be minimized to avoid injury or material damage.
Laser Welding Equipment
There are several types of laser welding equipment, each with its specific functionalities and safety considerations. For example, fiber lasers are often used for cutting and welding thin materials, while CO2 lasers are preferred for thicker materials.
When using laser welding equipment, it’s important to follow all manufacturer guidelines and wear appropriate personal protective equipment (PPE), such as goggles, gloves, and a welding helmet. You should also ensure that the equipment is well-maintained and inspected regularly to identify and address any potential safety hazards.
Laser Welding Safety
“The use of lasers requires caution to prevent injury. Exposure to laser radiation may cause severe burns and eye injuries. Proper precautions such as labelling, safety interlocks, and protective barriers must be followed to prevent against accidental exposure.”
– Occupational Safety and Health Administration (OSHA)
The most significant safety risk associated with laser welding is exposure to laser radiation, which can cause severe burns and eye injuries. Therefore, it’s essential to follow all recommended precautions, including wearing PPE, ensuring proper ventilation, and having trained personnel operate the equipment.
Additionally, laser welding generates fumes and gases that can be hazardous if inhaled. It is important to ensure that the welding area is well-ventilated, and the operator wears appropriate respiratory protection when necessary.
As with any technology, laser welding has its advantages and disadvantages. While it offers many benefits, including precision, speed, and minimal material distortion, it also comes with certain safety risks that need to be considered and mitigated. By understanding the technology and taking appropriate safety precautions, laser welding can be a reliable and safe method for welding a variety of materials.
Conclusion
You have completed this beginner’s guide to laser welding basics. We hope you found it informative and useful in understanding the principles and potential of this technology. As you have learned, laser welding offers many advantages over traditional welding methods, including precision, efficiency, and versatility. It is commonly used in a wide range of industries, including automotive, aerospace, and medical fields.
However, it is important to remember that laser welding technology also requires careful attention to safety. Proper training, equipment, and precautions are necessary to ensure a safe working environment and prevent accidents. With this knowledge, you are now ready to explore the world of laser welding with confidence. We encourage you to continue learning and expanding your knowledge of this exciting technology.
FAQ
What is laser welding?
Laser welding is a method of joining materials using a focused laser beam. It involves heating the materials to their melting point and then cooling them to form a solid bond.
How does laser welding work?
Laser welding works by directing a laser beam onto the materials to be welded. The laser beam creates a heat source that melts the materials, allowing them to fuse together. The process is precise and efficient, resulting in high-quality welds.
What types of materials can be laser welded?
Laser welding can be used on a wide range of materials, including metals, plastics, and even some ceramics. It is particularly effective for materials that have high melting points or are difficult to weld using traditional methods.
What are the advantages of laser welding?
Laser welding offers several advantages over traditional welding methods. It provides high weld quality, precision, and speed. It also minimizes distortion and reduces the need for post-welding processes.
What are the applications of laser welding?
Laser welding is commonly used in industries such as automotive, aerospace, electronics, and medical devices. It is often used for joining components, creating intricate designs, and repairing delicate parts.
Is laser welding safe?
Laser welding can be safe when proper precautions are taken. Safety measures include wearing appropriate protective equipment, ensuring proper ventilation, and following established safety protocols. It is important to receive training and practice safe handling of laser welding equipment.