Looking to master the art of MIG welding stainless steel without gas? You are in the right place. While traditional MIG welding uses gas to shield the weld pool from impurities, it’s entirely possible to achieve pristine stainless steel welds without using gas. From understanding the role of flux-core wire to adjusting your welding settings, this guide covers everything you need to know to weld stainless steel without gas like a pro.
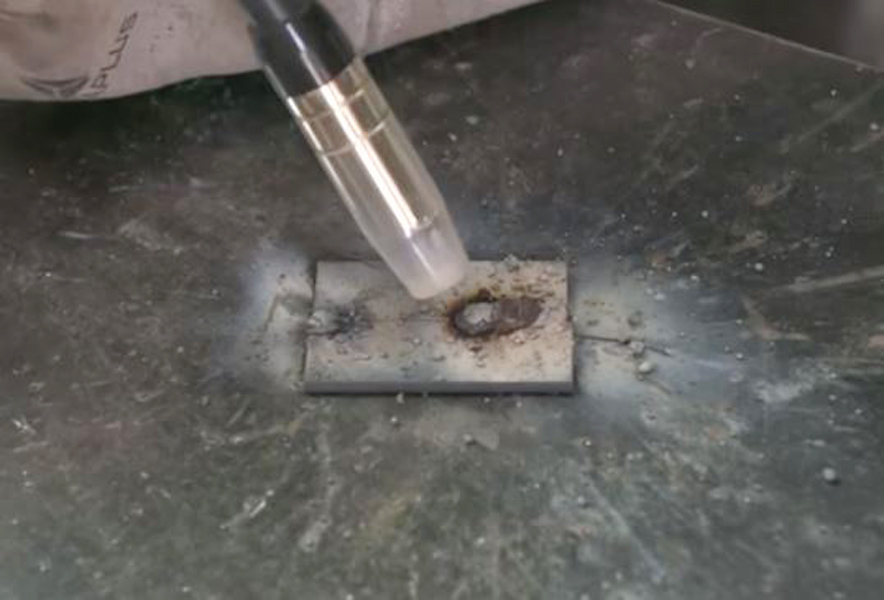
Perfecting this technique not only expands your welding capabilities but also saves you the hassle and cost of using gas. We will walk you through the essentials and offer practical tips to ensure your welding projects are a resounding success. So, whether you’re a seasoned welder looking to broaden your skills or a hobbyist eager to delve into stainless steel welding, mastering the art of gasless MIG welding is a valuable asset. Get ready to elevate your welding game and produce high-quality stainless steel welds, gas-free.
MIG welding and its applications
MIG (Metal Inert Gas) welding, also known as Gas Metal Arc Welding (GMAW), is a widely used welding process that utilizes a continuous solid wire electrode, shielding gas, and a welding gun. It is known for its versatility, allowing welders to work with various metals, including stainless steel. MIG welding with gas creates a protective atmosphere around the welding arc, preventing atmospheric contamination of the weld pool.
When it comes to welding stainless steel without gas, the process involves using a flux-cored wire that releases a shielding gas when heated. This gas shields the weld from atmospheric contamination, enabling the weld to remain clean and strong. Understanding the principles of traditional MIG welding and its gasless alternative is crucial for achieving quality stainless steel welds.
Gasless MIG welding is particularly useful in outdoor or windy conditions where using gas shielding may be impractical. It offers the flexibility to weld stainless steel without being limited by the availability of a shielding gas source, making it a valuable technique for various welding applications.
Advantages and challenges of MIG welding stainless steel without gas
Welding stainless steel without gas presents both advantages and challenges. One of the main advantages is the cost savings associated with not having to purchase and transport shielding gas. This makes gasless MIG welding a cost-effective option, especially for small-scale welding projects.
The flux-cored wire used in gasless MIG welding provides better penetration and higher welding speeds compared to solid wires, making it suitable for thicker stainless steel materials. The ability to work outdoors without the need for a constant supply of shielding gas is another notable advantage of this technique.
Gasless MIG welding also comes with its challenges. The flux-cored wire may produce more spatter compared to solid wire with shielding gas, requiring extra cleaning and post-welding care. Furthermore, achieving the same level of precision and cleanliness as traditional MIG welding with gas can be more demanding when using the gasless method. Understanding these advantages and challenges is essential for successful gasless MIG welding of stainless steel.
Techniques for MIG welding stainless steel without gas
Mastering the techniques for MIG welding stainless steel without gas is a key aspect of achieving high-quality welds. Proper preparation of the workpiece, including cleaning and ensuring proper fit-up, is crucial for successful gasless MIG welding. Additionally, selecting the appropriate flux-cored wire for stainless steel and adjusting the welding machine settings to suit the specific material thickness and joint configuration are essential steps for achieving optimal weld results.
Maintaining a consistent travel speed and angle during welding, as well as employing proper gun positioning and manipulation techniques, significantly influences the quality of the weld bead. It’s important to ensure smooth and steady wire feeding to prevent irregularities in the weld pool. These techniques, combined with a thorough understanding of the welding process, contribute to achieving clean and durable stainless steel welds without gas.
Suitable equipment and materials for gasless MIG welding
To effectively weld stainless steel without gas, it’s important to use the right equipment and materials. A reliable MIG welding machine capable of running flux-cored wire is essential. Selecting the appropriate flux-cored wire designed specifically for stainless steel ensures proper shielding and weld integrity. Additionally, having the right welding accessories, such as a suitable welding gun and personal protective equipment, is crucial for safe and efficient gasless MIG welding.
Understanding the characteristics of different types of flux-cored wires and their compatibility with stainless steel enables welders to make informed choices when selecting materials for gasless MIG welding. Quality equipment and materials play a significant role in achieving successful welds and enhancing the overall welding experience.
Safety measures for gasless MIG welding stainless steel
Safety should always be a top priority when engaging in gasless MIG welding of stainless steel. As with any welding process, proper ventilation and the use of personal protective equipment, including welding helmets, gloves, and clothing, are essential for safeguarding against potential hazards such as fumes, arc radiation, and molten metal splatter.
In addition to personal protective gear, ensuring a clean and clutter-free work environment, as well as implementing fire prevention measures, further enhances the safety of gasless MIG welding operations. Prioritizing safety measures not only protects the welder but also contributes to the overall success and quality of the welding project.
Tips for achieving quality welds without gas
Achieving quality welds when MIG welding stainless steel without gas requires attention to detail and adherence to best practices. Properly preparing the workpiece by removing any contaminants and ensuring proper fit-up sets the foundation for successful gasless MIG welding. Choosing the right flux-cored wire and adjusting welding parameters based on the specific requirements of the stainless steel material being welded is crucial for achieving optimal results.
Maintaining a steady welding technique, including consistent travel speed and gun positioning, helps produce clean and uniform weld beads. Conducting thorough inspections of the welds and making any necessary adjustments during the welding process contributes to achieving high-quality gasless MIG welds. Implementing these tips elevates the overall welding proficiency and ensures the production of durable and visually appealing stainless steel welds.
Common mistakes to avoid during gasless MIG welding
Understanding and avoiding common mistakes associated with gasless MIG welding of stainless steel is essential for achieving successful outcomes. One common mistake is neglecting proper surface preparation, leading to contamination and reduced weld quality. Inadequate selection of flux-cored wire or incorrect adjustment of welding parameters can also result in subpar welds.
Inconsistent wire feeding and improper gun manipulation during welding may lead to irregularities in the weld pool, impacting the overall weld appearance and integrity. Failing to address these mistakes can compromise the strength and aesthetics of the welded joints. Recognizing and mitigating these common errors is crucial for mastering the art of gasless MIG welding stainless steel.
Best practices for post-welding care and finishing
After completing gasless MIG welding of stainless steel, proper post-welding care and finishing are essential for ensuring the durability and visual appeal of the welds. This includes removing any welding spatter or slag, cleaning the welded area, and conducting visual inspections to identify any defects or imperfections. Additionally, implementing appropriate surface finishing techniques, such as grinding or polishing, enhances the overall appearance of the welded joints.
Inspecting the completed welds for proper fusion and integrity, as well as conducting any necessary repairs or touch-ups, contributes to the overall quality of the gasless MIG welding project. Employing best practices for post-welding care and finishing elevates the final outcome and ensures that the stainless steel welds meet the desired standards.
Comparison of gasless MIG welding vs traditional MIG welding
When comparing gasless MIG welding with traditional MIG welding using gas, several factors come into play. Traditional MIG welding with gas offers precise control over the welding atmosphere, resulting in clean and aesthetically pleasing welds. It is commonly used for applications that demand high-quality, visually appealing welds, such as automotive and architectural projects.
On the other hand, gasless MIG welding provides the flexibility to weld stainless steel without the need for a shielding gas source, making it suitable for outdoor and remote welding applications. The use of flux-cored wire in gasless MIG welding offers improved penetration and higher welding speeds, making it a preferred choice for thicker stainless steel materials and structural welding projects.
Understanding the strengths and limitations of both techniques enables welders to select the most appropriate method based on the specific requirements of their welding projects. Whether prioritizing precision and aesthetics or seeking flexibility and cost-effectiveness, choosing between gasless MIG welding and traditional MIG welding depends on the unique needs of each welding application.
Conclusion and recommendations
Mastering at MIG welding stainless steel without gas opens up new possibilities for welders seeking to expand their capabilities and tackle diverse welding projects. By understanding the principles, techniques, and best practices associated with gasless MIG welding, welders can confidently produce high-quality stainless steel welds without the reliance on shielding gas.
While gasless MIG welding presents its own set of advantages and challenges, the ability to weld stainless steel without gas offers cost savings, flexibility, and enhanced penetration capabilities. By prioritizing safety, adhering to best practices, and continually refining their welding skills, welders can elevate their proficiency in gasless MIG welding and achieve exceptional results.
Whether you are a professional welder looking to diversify your skills or a hobbyist eager to explore the world of stainless steel welding, mastering the art of MIG welding stainless steel without gas is a valuable asset. Embrace the opportunities that gasless MIG welding presents, and elevate your welding game to produce pristine stainless steel welds, gas-free.
By incorporating the insights and recommendations shared in this guide, you can embark on your gasless MIG welding journey with confidence, knowing that you have the knowledge and expertise to excel in welding stainless steel without gas.