When it comes to welding, two popular methods often come to mind: flux core welding and stick welding. Both techniques have their own unique set of advantages and disadvantages, making it important to understand the differences between the two.
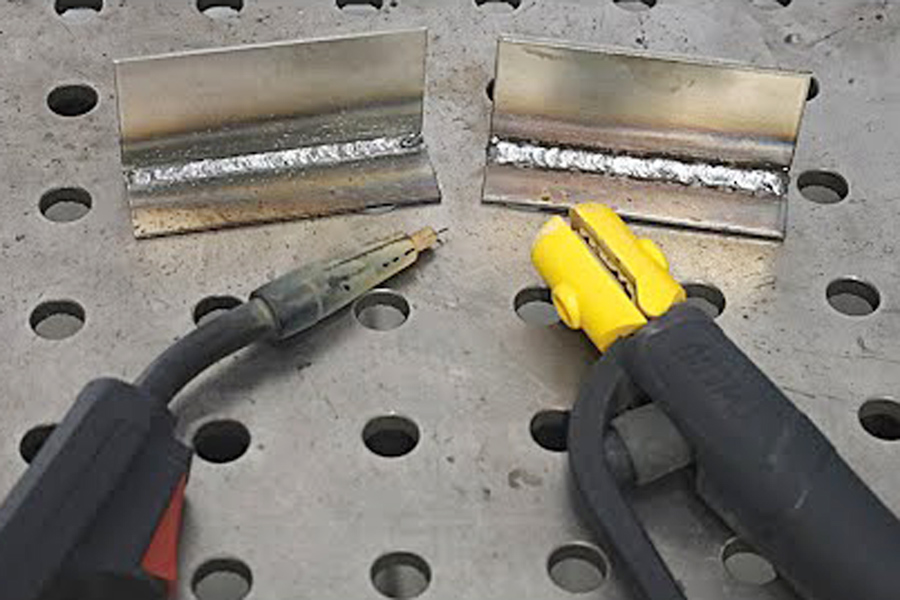
Flux core welding, also known as FCAW (Flux-Cored Arc Welding), utilizes a continuously fed wire electrode filled with flux. This method offers excellent penetration and can be used on thick materials, making it ideal for heavy-duty applications. The flux in the wire electrode creates a shielding gas that protects the weld pool from atmospheric contamination, resulting in high-quality welds. Compared to stick welding, flux core welding is generally faster and requires less cleanup.
On the other hand, stick welding, or SMAW (Shielded Metal Arc Welding), uses a consumable electrode coated in flux. It is a versatile method that can be used on various materials and is easier to start up. Stick welding is a popular choice for outdoor applications or situations where a power source is limited. The flux coating on the electrode creates a shielding gas when it melts, protecting the weld pool from impurities. However, stick welding may produce more spatter and require more cleanup compared to flux core welding.
Pros and cons of flux core welding
Flux core welding offers several advantages that make it a preferred choice for certain applications. One of the main advantages is its ability to provide deep penetration, making it suitable for welding thick materials. The continuous feeding of the wire electrode also allows for high welding speeds, increasing productivity. Flux core welding can be performed in windy conditions without the need for additional shielding gas, making it ideal for outdoor projects.
There are some drawbacks to consider. Flux core welding may produce more smoke and fumes compared to other welding methods, requiring proper ventilation. The flux in the wire electrode can also create slag that needs to be removed after welding, adding to the cleanup process. It is also worth noting that flux core welding tends to have a higher cost per pound of consumables compared to stick welding.
Pros and cons of stick welding
Stick welding has its own set of advantages that make it a popular choice for many welders. One of the main benefits is its versatility. Stick welding can be used on a wide range of materials, including carbon steel, stainless steel, and cast iron. It is also relatively easy to start up, making it suitable for beginners or those who are new to welding.
Another advantage of stick welding is its portability. The equipment required for stick welding is typically more compact and lightweight compared to other welding methods, making it easier to transport to different job sites. Stick welding also produces less noise compared to other welding processes, making it more suitable for residential areas or noise-sensitive environments.
However, stick welding does have some limitations. It can be more challenging to achieve deep penetration on thick materials compared to flux core welding. Stick welding also requires frequent electrode changes, which can interrupt the welding process and slow down productivity. The slag produced during stick welding needs to be chipped off after welding, adding to the cleanup process.
Flux core welding techniques and tips
To ensure successful flux core welding, there are several techniques and tips to keep in mind. First and foremost, it is important to select the correct polarity for the welding machine. Flux core welding typically requires a DC electrode positive (DCEP) polarity. This polarity helps to ensure proper penetration and welding performance.
It is also crucial to choose the appropriate wire size and type for the specific application. The wire size should be selected based on the thickness of the material being welded. Thicker materials typically require larger wire diameters. The type of flux core wire should be chosen based on the specific welding process and desired weld characteristics.
Proper joint preparation is essential for flux core welding. The joint edges should be clean and free from any contaminants or oxides. It is recommended to use a wire brush or grinding wheel to remove any rust, paint, or mill scale from the joint surfaces. This helps to ensure good fusion and strong welds.
During the welding process, it is important to maintain a consistent travel speed and arc length. Moving too slowly can result in excessive heat input and potential burn-through, while moving too quickly may lead to insufficient penetration. The correct travel speed should be determined through practice and adjustments based on the specific welding parameters and joint configurations.
Stick welding techniques and tips
To achieve optimal results with stick welding, there are several techniques and tips that can be followed. First, it is important to choose the right electrode for the specific application. Different types of electrodes are available, each with their own characteristics and suitable applications. The electrode diameter should also be selected based on the thickness of the material being welded.
Proper joint preparation is crucial for stick welding. The joint edges should be clean and free from any contaminants or oxides. It is recommended to use a wire brush or grinding wheel to remove any rust, paint, or mill scale from the joint surfaces. This helps to ensure good fusion and strong welds.
When striking an arc, it is important to strike it quickly and at the correct angle. The electrode should be struck against the workpiece with a short, snappy motion. The angle of the electrode should be around 10-15 degrees from vertical, depending on the specific welding position and joint configuration.
Maintaining a consistent arc length is essential for successful stick welding. The arc length should be kept as short as possible without touching the workpiece. This helps to ensure good arc stability and control. It is also important to maintain a steady travel speed and avoid excessive weaving or oscillation, which can result in uneven weld beads.
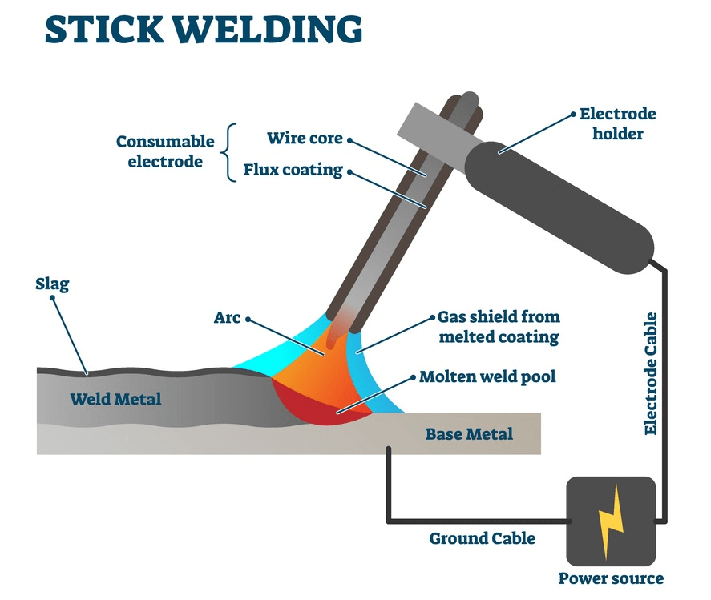
Applications and industries where flux core welding is commonly used
Flux core welding is commonly used in various applications and industries due to its unique advantages. One of the primary industries where flux core welding is utilized is the construction industry. It is often used for structural steel fabrication, heavy equipment manufacturing, and bridge construction. The deep penetration and high welding speeds make flux core welding an efficient choice for these applications.
Another industry where flux core welding is commonly employed is shipbuilding and offshore fabrication. The ability to perform flux core welding in windy conditions without the need for additional shielding gas makes it ideal for outdoor welding on ships and offshore structures. Flux core welding is also used in the automotive industry for welding frames, exhaust systems, and other components.
Applications and industries where stick welding is commonly used
Stick welding is a versatile welding method that finds applications in various industries. One of the main industries where stick welding is commonly used is the construction industry. It is often employed for welding structural steel, pipelines, and other infrastructure projects. The portability and versatility of stick welding make it well-suited for construction sites where power sources may be limited.
Another industry where stick welding is widely utilized is the maintenance and repair sector. Stick welding is often used for repairing heavy machinery, farm equipment, and pipelines. The ability to weld a wide range of materials, including cast iron, makes stick welding a preferred choice for repairing and joining diverse components.
Choosing the right welding process for your project
Choosing between flux core welding and stick welding depends on the specific requirements of your project. Factors such as the material being welded, the available equipment, and skill level all play a role in determining which method is best suited for the job at hand.
If you require deep penetration on thick materials and need high welding speeds, flux core welding may be the preferred choice. It is well-suited for heavy-duty applications in industries such as construction, shipbuilding, and automotive.
On the other hand, if you need versatility and portability, stick welding may be the better option. It is suitable for a wide range of materials and can be used in various industries, including construction, maintenance, and repair.
It is important to consider the specific advantages and disadvantages of each welding process, as well as the requirements of your project, before making a decision. Consulting with a welding professional or conducting tests on sample materials can also help in determining the most appropriate welding method.
Conclusion and final thoughts on flux core vs stick welding
In conclusion, both flux core welding and stick welding have their own unique advantages and disadvantages. Flux core welding offers deep penetration, high welding speeds, and the ability to weld thick materials, making it suitable for heavy-duty applications. Stick welding, on the other hand, provides versatility, portability, and ease of use, making it a popular choice for various industries.
When choosing between flux core welding and stick welding, it is important to consider the specific requirements of your project, including the material being welded, available equipment, and skill level. By understanding the differences between these two welding methods and weighing their pros and cons, you can make an informed decision that best suits your individual needs.