Welding Inspection are essential aspects of ensuring the quality, reliability, and safety of welded joints. Welding inspection involves examining and evaluating welded joints to specific quality standards. The inspection process aims to detect welding defects, assess adherence to industry codes, and ensure overall safety and performance.
In this comprehensive guide, we will explore the different types of welding inspection, advanced technology used in the process and the purpose it serves. Understanding the types of inspection, technology, and purpose is crucial for professionals in various industries to uphold industry standards and ensure the quality of welds.
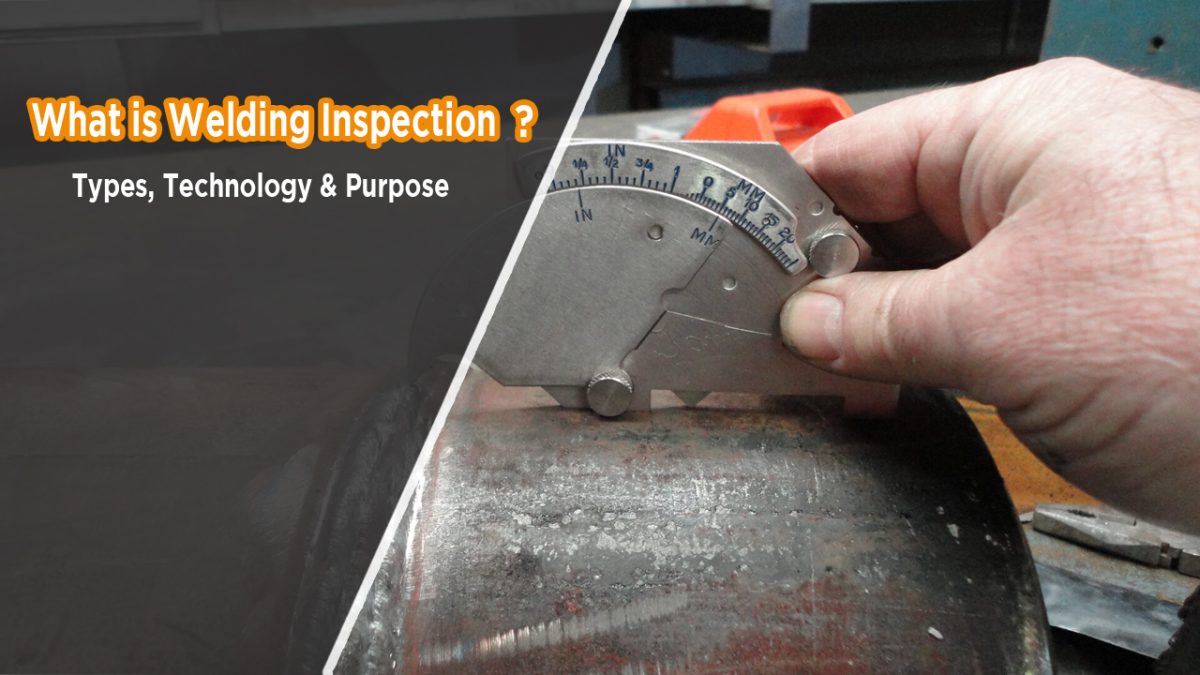
Image by swissapproval
What is Welding Inspection?
Welding inspection is a critical process that involves examining and evaluating welded joints to ensure that they meet specific quality standards. Simply put, it is a non-destructive testing method that evaluates a weld’s quality, integrity, and adherence to safety regulations.
The ultimate aim of welding inspection is to detect any welding defects that could compromise the strength, performance, and safety of the welded joint. The inspection process involves using various techniques and tools to ensure the weld’s quality while maintaining its structural integrity.
Welding inspection is a mandatory process in industries where welded joints play an integral role in the structure’s safety and performance, including construction, aerospace, automotive, and oil and gas.
Types of Welding Inspection
Welding inspection involves different methods, depending on the project’s nature and requirements. Here are some types of welding inspection:
Type | Application | Advantage |
---|---|---|
Visual Inspection | Checking the surface of the welded joint with the naked eye or magnifying tools | Quick and economical, minimal equipment required |
Radiographic Testing | Using radiation to examine the welded joint’s internal structure | Identifies internal welding defects, applicable to different thicknesses and materials |
Ultrasonic Testing | Using high-frequency sound waves to detect welding defects, such as cracks, voids, or inclusions | Accurately detects subsurface defects, both for ferrous and non-ferrous materials |
Magnetic Particle Inspection | Checking for surface-breaking defects using magnetic fields and iron oxide particles | Easy to perform on-site, identifies surface-breaking defects |
Each type of inspection has its unique advantages and applications. Choosing the right type of welding inspection ensures that the project meets quality standards and industry-specific requirements.
Welding Inspection Technology
Welding inspection employs advanced technology to ensure the quality and safety of welded joints. One widely-used technology is non-destructive testing, a set of techniques that help detect defects in welds without compromising their integrity.
Liquid Penetrant Testing
This technique involves applying a dye to the weld surface and allowing it to seep into surface-breaking cracks and flaws. After cleaning the surface, a developer is applied to highlight the penetrant and reveal any defects.
Eddy Current Testing
This method uses electromagnetic induction to assess the conductivity and integrity of the weld. The process involves passing an electric current through a coil, which induces eddy currents in the metal surface of the weld. By measuring changes in this current, inspectors can identify defects.
Radiographic Testing
This is a widely-used non-destructive testing method that involves using ionizing radiation to create an image of the internal structure of the weld. By analyzing the image, inspectors can identify any defects that may be present.
These technologies are highly accurate and effective in detecting welding defects, ensuring the weld meets specific quality standards, and protecting the structural integrity of welded joints.
What is the Purpose of Welding Inspection?
Welding inspection plays a crucial role in ensuring the quality and safety of welded joints. The purpose of welding inspection is multifold and includes:
- Preventing potential failures: Welding inspection helps to detect any defects in the weld before they lead to catastrophic failures.
- Improving weld quality: By ensuring that the weld meets industry standards, welding inspection helps to improve the overall quality of the weld.
- Complying with industry standards: Welding inspection is essential to ensure that the weld meets the required industry standards and regulations.
- Meeting project requirements: Welding inspection helps to ensure that the weld meets the specific project requirements and performs as expected.
The process of welding inspection involves various techniques, standards, and equipment. It typically includes visual inspection, ultrasonic testing, radiographic testing, and magnetic particle inspection. The use of non-destructive testing methods such as liquid penetrant testing, eddy current testing, and radiographic testing is also common. The equipment involved in welding inspection ranges from simple rulers and gauges to advanced technologies such as automated ultrasonic systems.
Benefits of Welding Inspection
Welding inspection offers numerous benefits to various stakeholders involved in the welding process. For fabricators and contractors, it ensures that their work meets the required quality standards and minimizes the risk of rework or costly repairs. For engineers and designers, it provides confidence in the structural integrity of their designs and helps them make informed decisions. Inspections also contribute to the overall safety of the workforce and the public by identifying potential hazards and preventing accidents. Moreover, welding inspection helps build trust and credibility among clients and regulatory authorities, enhancing the reputation of the welding industry as a whole.
Welding Inspection Process and Procedures
The welding inspection process involves several steps and procedures to ensure a comprehensive evaluation of welds. It typically starts with visual inspection, where welds are examined for surface defects and overall appearance. If necessary, non-destructive testing techniques are employed to assess the internal integrity of welds. This may include the use of ultrasonic testing, radiography, or magnetic particle inspection.
The inspection results are then carefully analyzed, and any defects or inconsistencies are documented. Finally, based on the findings, appropriate corrective actions are recommended to address the identified issues and ensure the quality and safety of the welds.
Common Welding Defects and How Inspection Helps Prevent Them
Welding defects can occur due to various reasons, including improper technique, inadequate preparation, or subpar materials. Some common welding defects include cracks, porosity, lack of fusion, and excessive spatter. These defects can compromise the strength and integrity of the weld, leading to structural failures. Welding inspection plays a crucial role in preventing these defects by identifying them early on. Through visual inspection and non-destructive testing, inspectors can detect and assess the severity of defects. This allows for timely corrective actions, such as re-welding or repairs, to be implemented before the structure is put into service.
Welding Inspection Best Practices
To ensure effective and reliable welding inspection, it is essential to follow best practices. First and foremost, inspectors must stay updated with the latest industry codes, standards, and regulations. Regular training and continuing education help maintain proficiency and enhance knowledge. Inspectors should also have access to the necessary tools and technologies required for accurate evaluations. Proper documentation of inspections, including photographs, videos, and reports, is crucial for future reference and traceability. Collaboration and communication among all stakeholders involved in the welding process are vital to address any issues and ensure the quality of welds.
Conclusion
Welding inspection is a critical process that ensures the safety, performance, and structural integrity of welded joints. It involves examining and evaluating these joints to meet specific quality standards and detect welding defects. Using advanced technology, welding inspectors can identify these defects without compromising the weld’s integrity.
The purpose of welding inspection is to prevent potential failures, improve weld quality, comply with industry standards, and meet specific project requirements. Professionals must understand the types of inspection, the advanced technologies employed, and the purpose it serves to ensure the quality of welds and uphold industry standards.
By prioritizing welding inspection, industries can avoid costly failures and ensure the safety of workers and the public. Overall, welding inspection is a critical component of the welding process, and professionals must prioritize it for successful project outcomes.
FAQ’s
What is welding inspection?
Welding inspection is a crucial process that involves examining and evaluating welded joints to ensure they meet specific quality standards. It aims to detect welding defects, assess the weld’s adherence to code requirements, and ensure overall safety and performance.
What are the types of welding inspection?
There are different methods of conducting welding inspection, depending on the nature and requirements of the project. Some common types include visual inspection, radiographic testing, ultrasonic testing, and magnetic particle inspection. Each type has its unique advantages and applications.
How has welding inspection technology evolved?
Advancements in technology have revolutionized the field of welding inspection. Cutting-edge tools and techniques such as non-destructive testing methods (liquid penetrant testing, eddy current testing, and radiographic testing) enable inspectors to identify defects without compromising the weld’s integrity.
What is the purpose of welding inspection?
Welding inspection serves a crucial purpose in ensuring the quality and reliability of welded joints. It helps prevent potential failures, improve weld quality, comply with industry standards, and meet specific project requirements. The process involves utilizing various techniques, following standards, and employing specialized inspection equipment.