Welcome to our exploration of ultrasonic welding, the process used to join materials using ultrasonic vibrations. Ultrasonic welding is a rapidly growing field, thanks to its speed, efficiency, and precision. In this section, we will delve into the basics of ultrasonic welding and provide you with a detailed understanding of how it works. Ultrasonic welding is a process in which high-frequency vibrations are applied to materials, causing the molecules to vibrate. As a result, the materials become soft and are pressed together, creating a bond. The process is used to join materials such as thermoplastics, metals, and composites.
The ultrasonic welding process involves several steps, including the preparation of the materials, the application of ultrasonic waves, and the cooling of the bonded materials. Ultrasonic welding is a versatile technique used in various industries, including automotive, electronics, medical, and packaging.
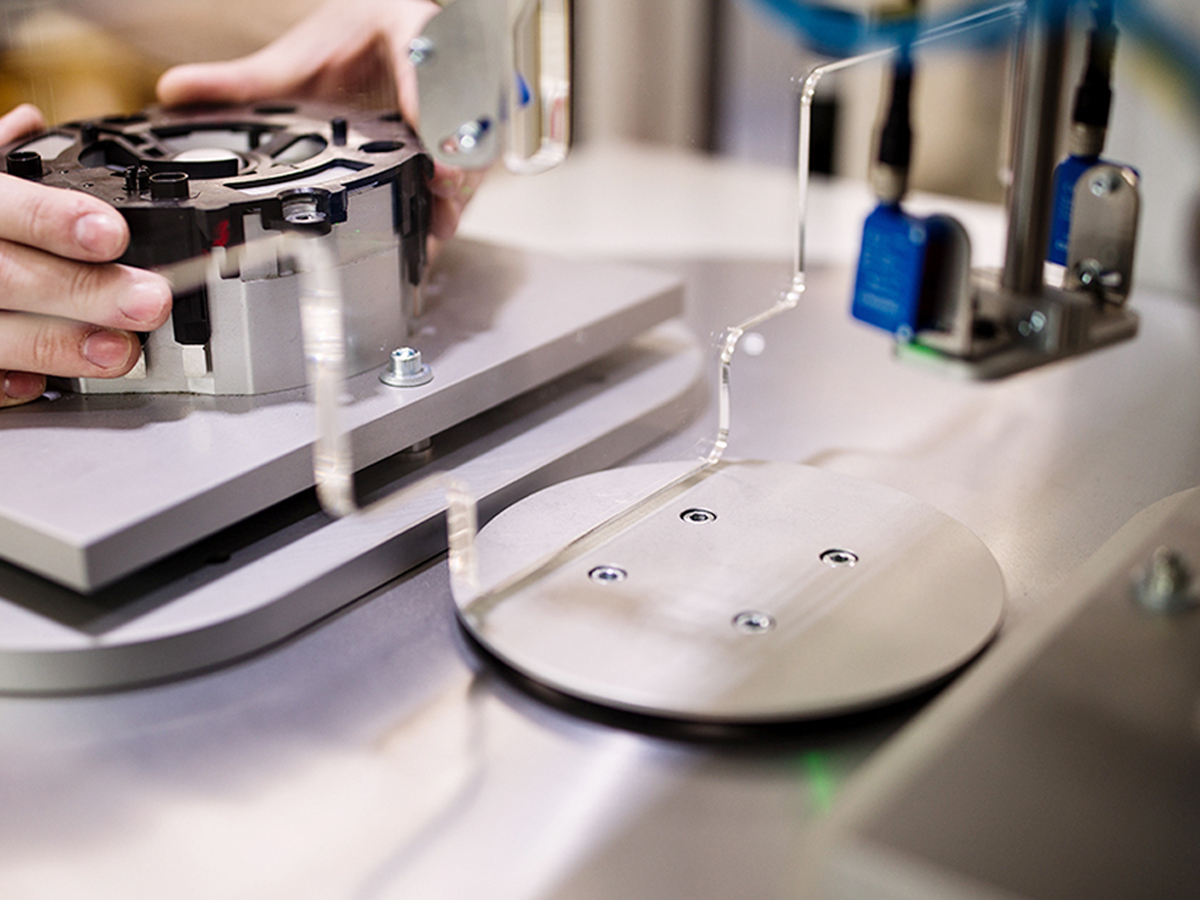
Photos by vial-automation.si
Understanding the Ultrasonic Welding System
Ultrasonic welding is a cutting-edge manufacturing technique that utilizes ultrasonic vibrations to join two materials together. The process is achieved by transmitting high-frequency ultrasonic vibrations to the materials to be welded, creating heat and pressure that causes the materials to bond.
The fundamental principle behind ultrasonic welding is that when ultrasonic frequencies are applied to a material, it causes the material to vibrate at high speeds, generating heat and friction. This, in turn, causes the material to melt and bond with the other material being welded.
Objectives of Ultrasonic Welding |
---|
Joining dissimilar materials |
Creating strong and durable bonds |
Minimizing the heat input to the materials being joined |
Unlike traditional welding methods, ultrasonic welding generates very little heat, making it ideal for joining heat-sensitive materials such as thermoplastics. Because of its ability to create strong and durable bonds between materials, ultrasonic welding is used in a wide range of industries, including automotive, electronics, medical, and packaging.
Definition of Ultrasonic Welding
Ultrasonic welding is defined as a welding process that utilizes high-frequency ultrasonic vibrations to join two materials together. The process involves the application of heat and pressure to the materials being joined, causing them to melt and bond together.
The Ultrasonic Welding Process
Ultrasonic welding is a highly efficient and precise method of joining two materials using high-frequency acoustic vibrations. The process requires specialized equipment and techniques that have evolved over time to improve its efficiency and performance. Let’s take a closer look at the various elements involved in ultrasonic welding.
Ultrasonic Welding Equipment
Ultrasonic welding machines use three key components: a power supply, a transducer, and a horn. The power supply converts electrical energy into high-frequency mechanical vibrations, which are then transmitted to the transducer. The transducer, in turn, converts these mechanical vibrations into high-frequency acoustic waves that are amplified by the horn and directed towards the workpiece. Other components of the ultrasonic welding equipment include the fixture, which holds the workpiece in place, and the controller, which regulates the welding process.
Ultrasonic Welding Techniques
There are various techniques employed in ultrasonic welding, depending on the type of materials being joined. The most common technique is spot welding, which involves the application of high-frequency vibrations to a small area of the workpiece. Seam welding, on the other hand, involves the application of vibrations along the entire length of the joint. Other techniques include staking, inserting, and even cutting.
Ultrasonic Welding Technology
The technology behind ultrasonic welding has advanced significantly in recent years, resulting in improvements in efficiency, precision, and safety. Newer ultrasonic welding machines incorporate features such as real-time monitoring of the welding process, automatic horn frequency tuning, and the ability to weld dissimilar materials. Additionally, innovations such as servo-driven ultrasonic welding systems have increased the reliability and consistency of the process.
Applications of Ultrasonic Welding
Ultrasonic welding, due to its versatile nature, finds uses in several industries across the globe. Below are some of the applications of ultrasonic welding:
Industry | Application |
---|---|
Automotive | Ultrasonic welding is used to join plastic parts in the automotive industry. The process is used in making automotive lighting, interior parts, dashboards, and air ducts. |
Electronics | In the electronics industry, ultrasonic welding is used to assemble small components such as capacitors, sensors, and connectors. It is also used to join plastic housings or parts of electronic products such as laptops, phones, and TVs. |
Medical | The medical industry utilizes ultrasonic welding to join plastics used in medical equipment and devices such as blood filters, IV tubing, and fluid bags. Ultrasonic welding is also used in cosmetic surgery equipment and dental products. |
Packaging | Ultrasonic welding is used to create strong seals in packaging materials such as blister packs, tubes, and sachets. |
Textile | Ultrasonic welding is used in textile manufacturing to bond fabric layers or to cut and seal edges. |
These are just a few examples of how ultrasonic welding is utilized in various industries. As technology continues to advance, we can expect to see even more widespread applications for this versatile joining method.
Advantages of Ultrasonic Welding
Ultrasonic welding offers numerous advantages over traditional welding techniques. These advantages include:
Advantages | Description |
---|---|
Speed | Ultrasonic welding is a fast process that can produce a weld in as little as a few seconds, increasing productivity and reducing cycle times. |
Cost-effectiveness | Ultrasonic welding is a cost-effective method of joining materials, as it requires no consumables such as welding rods or filler materials. |
Strong bond strength | Ultrasonic welding produces a strong, reliable weld with a bond strength that is often stronger than the base materials being joined. |
Ability to join dissimilar materials | Ultrasonic welding can join materials that are difficult or impossible to weld using traditional methods, such as plastics and metals. |
Clean and safe process | Ultrasonic welding does not require the use of adhesives, solvents, or other hazardous materials, making it a clean and safe process for workers and the environment. |
These advantages have made ultrasonic welding a popular choice in numerous industries, from automotive and electronics to medical and packaging. The ability to produce a strong, reliable bond quickly and cost-effectively makes it an attractive option for manufacturers looking to improve production efficiency and reduce costs.
Types of Ultrasonic Welding
Ultrasonic welding comes in various forms, each with its distinct advantages, applications, and limitations. Below, we will explore the most common types of ultrasonic welding techniques.
1. Spot Welding
Spot welding is the most widely used type of ultrasonic welding. It involves welding small areas or points, typically using a single sonotrode and an anvil. Spot welding is particularly useful in industries like electronics, where it is used to join wires, connectors, and other small components.
2. Seam Welding
Seam welding is used to join two or more overlapping parts along a continuous joint. Unlike spot welding, it requires a rotating sonotrode to weld the parts continuously. Seam welding is useful in industries such as automotive, where it is used to join sheet metal and plastic components.
3. Staking
Staking is used to join two or more parts by melting and forming one part to create a mechanical interlock with another. It is particularly useful in the medical industry, where it is used to join plastic parts in surgical instruments and devices.
4. Insertion
Insertion is used to bond a small part into a hole or cavity of another part. This technique is useful in the automotive and medical industries, where it is used to join plastic or metal parts by inserting one part into another.
5. Wave Welding
Wave welding is used to join large plastic parts that are too big for the traditional ultrasonic welding process. This technique involves using several sonotrodes arranged in a wave pattern to create a continuous weld along the entire joint.
Each type of ultrasonic welding has its unique advantages, and understanding them is crucial in selecting the right technique for a specific application.
Conclusion
Ultrasonic welding is a widely utilized manufacturing process that provides numerous advantages over traditional welding methods. By utilizing ultrasonic welding, industries such as automotive, electronics, and medical can create strong and efficient bonds between various materials. Throughout this article, we have explored the concept of ultrasonic welding, its definition, and the principles behind its operation. We have discussed the equipment used in the ultrasonic welding process, along with the various techniques employed.
We have also highlighted the diverse range of applications for ultrasonic welding, emphasizing the benefits of this process such as its speed, cost-effectiveness, and strong bond strength. Additionally, we have explored the different types of ultrasonic welding, such as spot welding and seam welding.
In conclusion, ultrasonic welding is an important technology that has been advancing rapidly in recent years. As the manufacturing industry continues to evolve, we can expect to see even more innovations in ultrasonic welding technology. Its potential for future advancements is exciting, and we look forward to what the future holds.
FAQ
What is ultrasonic welding and how does it work?
Ultrasonic welding is a process used to join two or more pieces of material by using high-frequency ultrasonic vibrations. The vibrations create heat, which melts and fuses the materials together, forming a strong bond.
What is the definition of ultrasonic welding?
Ultrasonic welding is a welding technique that uses high-frequency ultrasonic vibrations to create heat and join materials together. It is commonly used in industries such as automotive, electronics, medical, and packaging.
How does the ultrasonic welding process work?
The ultrasonic welding process involves placing the materials to be joined between an ultrasonic welding horn and an anvil. When the ultrasonic energy is applied, the vibrations create friction and heat at the interface of the materials, causing them to melt and fuse together.
What are the applications of ultrasonic welding?
Ultrasonic welding finds applications in various industries, including automotive, electronics, medical, and packaging. It is used to assemble components, seal packages, bond wires, and create hermetic seals, among other applications.
What are the advantages of ultrasonic welding?
Ultrasonic welding offers several advantages, including fast cycle times, cost-effectiveness, strong bond strength, and the ability to join dissimilar materials. It is a non-contact process that does not require additional consumables such as adhesives or solvents.
What are the types of ultrasonic welding?
There are different types of ultrasonic welding techniques, including spot welding, seam welding, and rotary welding. Each type is suited for specific applications and offers unique advantages in terms of speed, precision, and joint strength.