Shielding gas plays a crucial role in the world of welding. It’s a type of gas that protects the weld from atmospheric contamination during the welding process. But what exactly is shielding gas, and how does it work? In this article, we will explore the fascinating world of shielding gas and its important role in welding.
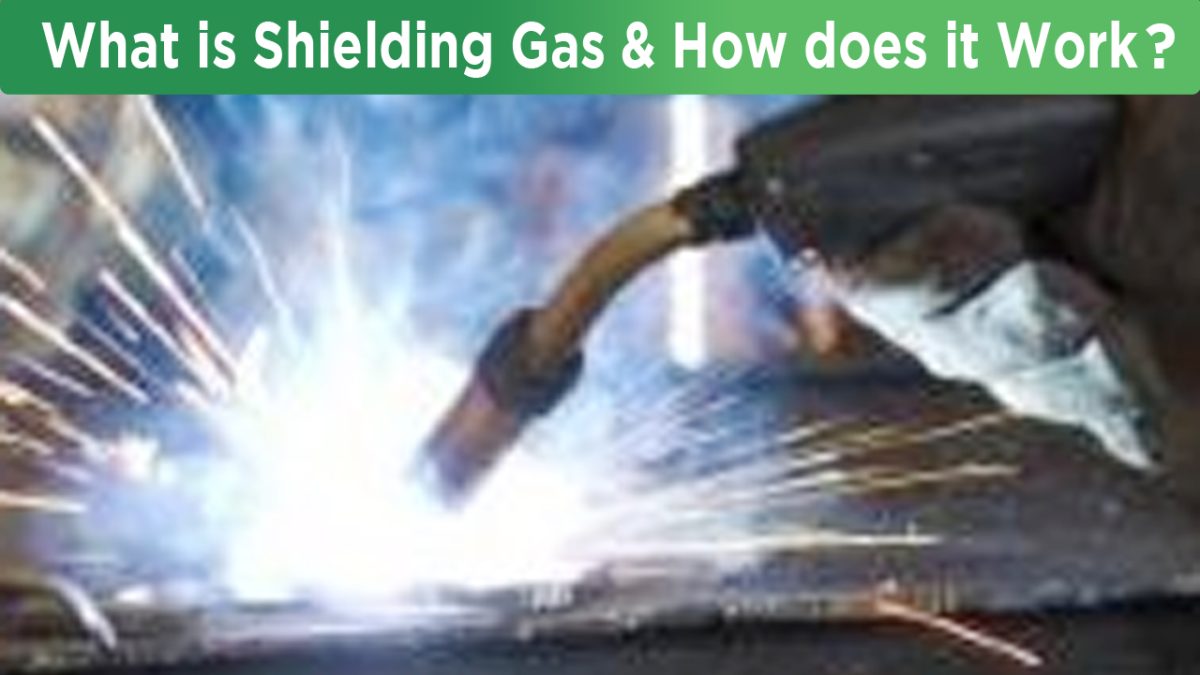
Importance of shielding gas in welding
Shielding gas is an essential component of the welding process, serving to protect the weld from atmospheric gases that can cause defects and compromise its integrity. When metal is heated during welding, it becomes vulnerable to oxidation and other chemical reactions with the surrounding air. This can lead to the formation of weak and brittle welds, reducing the overall strength and quality of the joint.
By introducing shielding gas into the welding environment, a protective barrier is created around the weld pool, preventing atmospheric gases from coming into contact with the molten metal. This barrier ensures that the weld is shielded from oxygen, nitrogen, and other contaminants that can cause porosity, cracking, and other defects.
How does shielding gas work?
Shielding gas works by displacing the surrounding air and creating a protective atmosphere around the weld. The most commonly used shielding gas in welding is argon, known for its low reactivity and ability to shield the weld pool effectively. Argon is an inert gas, meaning it does not react with other elements, making it an ideal choice for most welding applications.
When the welding arc is initiated, the heat generated melts the base metal and the filler metal (if used), creating a molten pool. At the same time, the shielding gas is released through the welding torch or nozzle, enveloping the weld pool. This flow of shielding gas displaces the surrounding air, preventing atmospheric gases from reaching the weld.
In addition to argon, other gases such as helium and carbon dioxide are also used as shielding gases, depending on the specific welding process and materials being welded. Helium offers higher heat conductivity and can be used in combination with argon to enhance the welding process. Carbon dioxide, on the other hand, is often used in certain types of welding, such as MIG welding, due to its ability to stabilize the arc and provide deep penetration.
Types of shielding gases
There are several types of shielding gases used in welding, each with its own unique properties and applications. The choice of shielding gas depends on factors such as the welding process, material type, and desired weld characteristics. Here are some of the most commonly used shielding gases:
Argon: Argon is the most commonly used shielding gas in welding. It is an inert gas that provides excellent protection against atmospheric contamination. Argon is ideal for welding non-ferrous metals, such as aluminum and stainless steel.
Helium: Helium is often used in combination with argon to enhance the welding process. It offers higher heat conductivity and can improve the weld penetration and speed. Helium is commonly used in applications where deep penetration is required, such as welding thick materials.
Carbon dioxide: Carbon dioxide is commonly used in MIG welding (Metal Inert Gas) due to its ability to stabilize the arc and provide deep penetration. It is also an economical choice for welding carbon steel.
Oxygen: Oxygen is sometimes used as a component of shielding gas in certain welding processes. It can improve arc stability and penetration in some applications. However, high levels of oxygen can increase the risk of oxidation and porosity, so its use needs to be carefully controlled.
Mixtures: In addition to individual gases, mixtures of shielding gases can also be used to achieve specific welding outcomes. For example, a mixture of argon and carbon dioxide, known as C25, is commonly used in MIG welding of carbon steel.
Common applications of shielding gas in various welding processes
Shielding gas is used in various welding processes to ensure high-quality and defect-free welds. Here are some common applications of shielding gas in different welding techniques:
Gas Metal Arc Welding (GMAW): Also known as MIG welding, GMAW uses a continuous wire electrode and a shielding gas to protect the weld. The shielding gas is typically a mixture of argon and carbon dioxide or argon and oxygen, depending on the material being welded.
Gas Tungsten Arc Welding (GTAW): GTAW, also known as TIG welding, uses a non-consumable tungsten electrode and a shielding gas to protect the weld. Argon is commonly used as the shielding gas in TIG welding due to its ability to provide excellent protection and stability.
Flux-Cored Arc Welding (FCAW): FCAW uses a tubular electrode with flux inside, eliminating the need for a separate shielding gas. However, some Flux Cored Arc Welding processes still use shielding gas to enhance the weld quality and protect against atmospheric contamination.
Submerged Arc Welding (SAW): SAW involves the use of a granular flux and a continuous solid wire electrode. The flux provides the shielding, eliminating the need for a separate shielding gas. SAW is commonly used in heavy-duty welding applications, such as welding thick plates and pipes.
Factors to consider when selecting the right shielding gas
When selecting the appropriate shielding gas for a welding application, several factors need to be considered. These factors include:
Material type: Different materials require different shielding gases to achieve optimal results. For example, stainless steel welding typically requires the use of argon-based shielding gases, while carbon steel welding may utilize a mixture of argon and carbon dioxide.
Welding process: Each welding process has its own specific requirements in terms of shielding gas. Understanding the characteristics and limitations of the chosen welding process is crucial in selecting the right shielding gas.
Welding position: The position in which the weld needs to be made can also impact the choice of shielding gas. Some shielding gases may perform better in certain positions, such as overhead or vertical welding.
Weld quality requirements: The desired quality of the weld also plays a role in selecting the appropriate shielding gas. For critical applications that require high-quality and defect-free welds, a more inert shielding gas may be necessary.
Safety precautions when using shielding gas
While shielding gas is essential in welding, it is important to take proper safety precautions when working with these gases. Here are some safety guidelines to follow:
Ventilation: Ensure that the welding area is well-ventilated to prevent the buildup of gases. Proper ventilation helps to disperse any fumes or gases released during the welding process.
Gas cylinder handling: Handle shielding gas cylinders with care and follow proper storage and handling procedures. Cylinders should be stored in a well-ventilated area, away from sources of heat and ignition.
Protective equipment: Wear appropriate personal protective equipment (PPE) when working with shielding gas. This includes welding helmets, gloves, and protective clothing to protect against potential hazards.
Gas leaks: Regularly inspect and maintain the welding equipment to prevent gas leaks. Gas leaks can be hazardous and increase the risk of fire or explosion.
Common troubleshooting issues with shielding gas
While shielding gas is crucial for achieving high-quality welds, certain issues can arise during the welding process. Here are some common troubleshooting issues related to shielding gas:
Insufficient gas flow: Inadequate gas flow can result in poor shielding, leading to defects in the weld. Ensure that the gas flow rate is set correctly and that there are no obstructions in the gas delivery system.
Gas leaks: Gas leaks can compromise the integrity of the shielding gas and lead to poor weld quality. Regularly inspect the gas connections and fittings for any signs of leaks and address them promptly.
Contaminated gas: Contaminated shielding gas can cause defects in the weld. Regularly check the purity of the gas and ensure that the gas supply is free from contaminants.
Gas composition: Using the wrong shielding gas composition for the specific welding application can result in poor weld quality. Always verify the recommended shielding gas composition for the materials being welded.
Advancements in shielding gas technology
As technology continues to advance, so does the field of shielding gas. New developments in gas mixtures, delivery systems, and process control have led to improved welding performance and efficiency. Some advancements in shielding gas technology include:
Gas mixtures: The development of new gas mixtures has enabled welders to achieve better control over the welding process. These mixtures can provide enhanced arc stability, penetration, and weld quality.
Gas flow control: Advanced gas flow control systems allow for precise regulation of the shielding gas flow rate. This helps to ensure consistent and optimal shielding throughout the welding process.
Gas monitoring systems: Gas monitoring systems have been developed to continuously monitor and analyze the composition of the shielding gas during welding. This ensures that the gas quality remains within the specified range, minimizing the risk of defects.
Gas delivery systems: Improvements in gas delivery systems have made it easier to deliver the shielding gas to the welding torch or nozzle. These advancements help to ensure efficient and effective gas coverage during welding.
Conclusion
Shielding gas is a critical component of the welding process, providing protection against atmospheric contamination and ensuring high-quality welds. By understanding the importance of shielding gas and its functionality in various welding processes, welders can achieve optimal results and produce defect-free welds. With advancements in shielding gas technology, the future of welding looks promising, offering even greater control and efficiency.
So, whether you’re a professional welder or simply curious about the world of welding, understanding the role of shielding gas is essential for appreciating the art and science behind this versatile metal fabrication technique.