Plug welding is a crucial technique in the realm of metalworking, offering a reliable method for joining two overlapping workpieces. This process involves creating a weld in the overlapped area, resulting in a strong and durable bond. By understanding the mechanics of plug welding, individuals can enhance their expertise in welding and expand their knowledge of fabrication and construction. Let’s delve into the intricacies of plug welding and explore its significance in various industrial applications.
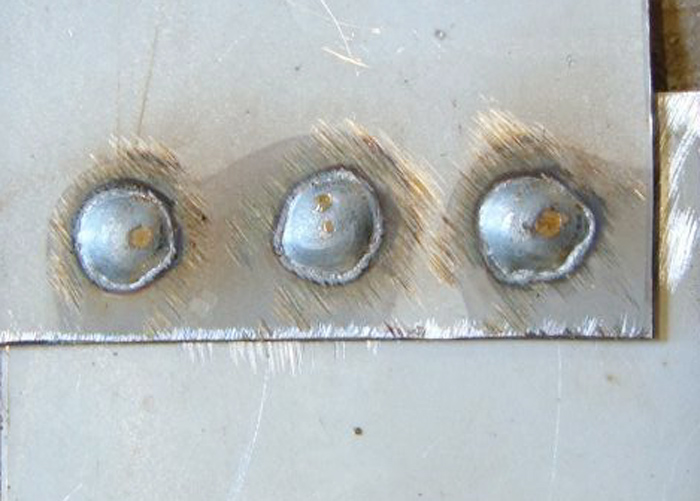
Image by mig-welding.co.uk
Plug welding is particularly advantageous due to its ability to create robust connections between workpieces. It is known for its high strength and durability, making it a preferred choice in manufacturing processes where structural integrity is paramount. Plug welding allows for the seamless joining of metal components, contributing to the overall efficiency and reliability of the finished products. By comprehending the advantages of plug welding, professionals can make informed decisions regarding its utilization in diverse projects.
Advantages of Plug Welding
One of the key advantages of plug welding lies in its ability to produce strong and durable connections between workpieces. This welding technique is particularly well-suited for applications where the structural integrity of the joint is crucial. Plug welding offers a cost-effective solution for joining metal components, as it eliminates the need for additional fasteners or connectors. The seamless nature of plug welding results in aesthetically pleasing finished products, making it an appealing choice in various industries.
In industrial settings, plug welding finds extensive use in the assembly of automotive components, structural steel fabrication, shipbuilding, and other manufacturing processes. Its versatility and reliability make it a go-to method for joining metal parts, contributing to the overall quality and performance of the assembled structures. By understanding the broad spectrum of applications for plug welding, professionals can leverage its benefits across a wide range of industries and projects.
Applications of Plug Welding
The process of plug welding involves overlapping two workpieces and creating a weld in the overlapped area. This technique requires careful preparation of the workpieces, ensuring that they are properly aligned and secured before the welding process begins. The equipment and materials used for plug welding include welding machines, electrodes, protective gear, and the workpieces themselves. It is essential to select suitable materials and welding parameters to achieve optimal results in plug welding.
In comparison to other welding techniques, plug welding offers distinct advantages in certain applications. For instance, it provides a visually appealing and structurally sound joint without the need for additional fasteners or connectors. Plug welding can be performed on materials with varying thicknesses, making it a versatile choice for joining metal components of different dimensions. By exploring the nuances of plug welding in relation to other welding methods, professionals can make informed decisions regarding its suitability for specific projects.
The Process of Plug Welding
The process of plug welding involves several key steps, starting with the careful preparation of the workpieces to be joined. This includes ensuring that the overlapping areas are clean, free of contaminants, and properly aligned. Once the workpieces are in position, a weld is created in the overlapped area by using a welding machine and suitable electrodes. The weld is formed by melting the base metal and adding filler material as needed, resulting in a strong and durable bond between the workpieces.
To perform plug welding successfully, it is essential to utilize the appropriate equipment and materials, including welding machines, electrodes, and protective gear. Understanding the specific parameters for plug welding, such as current settings and welding speed, is crucial for achieving optimal results. By mastering the process of plug welding, professionals can ensure the integrity and reliability of the welded joints, contributing to the overall quality of the finished products.
Equipment and Materials for Plug Welding
The equipment and materials required for plug welding include welding machines, electrodes, protective gear, and the workpieces themselves. It is essential to select high-quality electrodes that are suitable for the materials being welded, ensuring a strong and durable bond. Additionally, protective gear such as welding helmets, gloves, and aprons are necessary to ensure the safety of the welding operator during the plug welding process. Proper maintenance of welding equipment is also crucial to ensure consistent performance and reliable results.
In plug welding, the choice of welding machine and electrodes plays a critical role in achieving successful welds. Different types of welding machines, such as MIG welders or TIG welders, may be utilized depending on the specific requirements of the project. Similarly, selecting the appropriate electrodes based on the material composition and thickness is essential for producing high-quality plug welds. By understanding the significance of equipment and materials in plug welding, professionals can ensure the efficiency and reliability of the welding process.
Plug Welding vs Other Welding Techniques
When comparing plug welding to other welding techniques, it is important to consider the specific advantages and limitations of each method. Plug welding offers the advantage of creating visually appealing and structurally sound joints without the need for additional fasteners or connectors. This makes it a cost-effective and efficient choice for joining metal components in various applications. Plug welding can be performed on materials with varying thicknesses, providing versatility in fabrication and construction projects.
It is essential to recognize that plug welding may have limitations in certain scenarios, particularly when joining materials with significant thickness disparities. In such cases, other welding techniques, such as fillet welding or groove welding, may be more suitable for achieving strong and durable connections. By understanding the comparative aspects of plug welding and other welding methods, professionals can make informed decisions regarding the most appropriate technique for specific welding applications.
Common Mistakes in Plug Welding
In the realm of plug welding, several common mistakes can compromise the quality and integrity of welded joints. One prevalent error is inadequate preparation of the workpieces, including improper alignment and cleanliness of the overlapping areas. This can result in weak and inconsistent welds, leading to compromised structural integrity. Another common mistake is the improper selection of welding parameters, such as current settings and welding speed, which can affect the quality of the weld and the overall performance of the joint.
Furthermore, overlooking the proper maintenance of welding equipment and neglecting the use of suitable electrodes can lead to subpar plug welds. Inadequate training and lack of adherence to safety measures also contribute to potential mistakes in plug welding, posing risks to the welding operator and the integrity of the welded joints. By addressing and avoiding these common mistakes, professionals can elevate the quality and reliability of plug welding in various industrial applications.
Plug Welding Safety Measures
Safety is paramount in the practice of plug welding, and adherence to specific safety measures is essential to ensure the well-being of the welding operator and the integrity of the welded joints. Prior to initiating the plug welding process, it is crucial to conduct a thorough assessment of the work environment and implement appropriate safety protocols. This includes wearing protective gear such as welding helmets, gloves, and aprons to shield against potential hazards associated with welding operations.
Additionally, proper ventilation and fume extraction systems should be in place to minimize exposure to welding fumes and airborne contaminants. Training in safe welding practices and emergency procedures is imperative for all individuals involved in plug welding activities, fostering a culture of awareness and preparedness in the event of unforeseen circumstances. By prioritizing safety measures in plug welding, professionals can create a secure and conducive environment for the execution of welding operations.
Training and Certification for Plug Welding
As with any specialized skill, comprehensive training and certification in plug welding are essential for professionals seeking to excel in this field. Formal training programs provide individuals with the necessary knowledge and practical experience to perform plug welding with proficiency and confidence. Obtaining certification in plug welding demonstrates a commitment to upholding industry standards and best practices, enhancing one’s credibility and employability in the welding sector.
Training in plug welding encompasses various aspects, including understanding welding principles, equipment operation, material selection, and safety protocols. Hands-on practice and mentorship under experienced welding professionals further solidify the skills and expertise required for proficient plug welding. By investing in training and certification for plug welding, individuals can position themselves as competent and reliable practitioners in the dynamic landscape of metalworking and fabrication.
Final Thoughts
Plug welding is a fundamental welding technique that plays a pivotal role in various industrial applications, offering robust and durable connections between metal components. By grasping the intricacies of plug welding, professionals can leverage its advantages in manufacturing processes, construction projects, and other metalworking endeavors. Understanding the process, equipment, safety measures, and training requirements for plug welding is essential for achieving consistent and reliable results.
As the demand for high-quality welded joints continues to grow across diverse industries, the significance of plug welding as a versatile and cost-effective method cannot be overlooked. By staying abreast of advancements in welding technology and best practices, professionals can harness the full potential of plug welding to contribute to the efficiency, reliability, and safety of welded structures and assemblies. With a firm grasp of plug welding principles and applications, individuals can elevate their expertise and make meaningful contributions to the ever-evolving landscape of metal fabrication and construction.