Non-destructive testing (NDT) is a crucial process in various industries, especially in welding. It involves inspecting and evaluating the integrity of a material or component without causing any damage. NDT testing ensures the quality and safety of welded structures, preventing potential failures that could have serious consequences. In this comprehensive guide, we will explore the top three NDT testing methods for welding and provide insights into their principles, applications, advantages, and limitations.
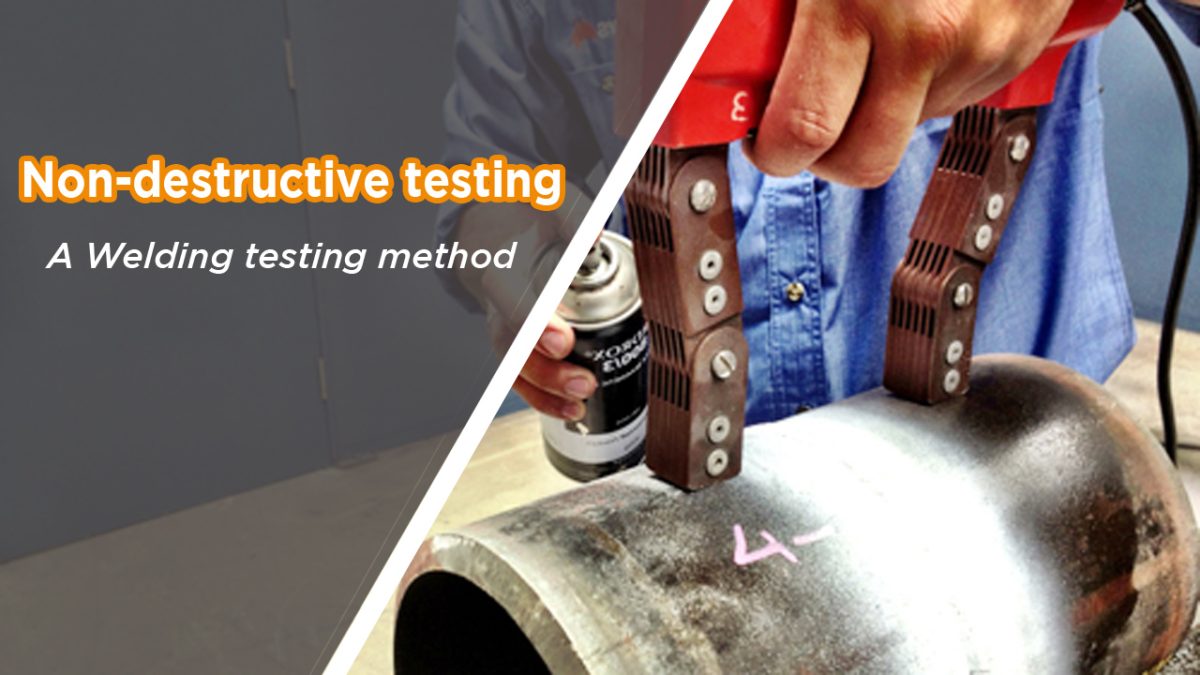
Importance of NDT Testing in Welding
Welding is a fundamental process in fabricating structures, and its integrity is of utmost importance. Defects in welds can lead to catastrophic failures, endangering lives and causing financial losses. NDT testing plays a vital role in identifying and assessing these defects, ensuring the quality and reliability of welded components. By detecting flaws such as cracks, porosity, or incomplete fusion, NDT testing allows for early intervention, preventing failures and optimizing the performance of welded structures.
Top 3 NDT Testing Methods For Welding
1. Visual Testing (VT)
Visual testing is the most basic and widely used NDT method. It involves visually inspecting the surface of a material or component for any visible defects. This method requires trained personnel to conduct a thorough examination using various tools, such as magnifying lenses, borescopes, or videoscopes. Visual testing is particularly effective in detecting surface cracks, incomplete penetration, or misalignments in welds. However, it has limitations when it comes to detecting internal defects or assessing the depth of flaws.
2. Magnetic Particle Testing (MT)
Magnetic particle testing utilizes the principles of magnetism to detect surface and near-surface defects in ferromagnetic materials. The process involves magnetizing the material and applying iron particles to the surface. If there are any defects, such as cracks or discontinuities, the magnetic field will cause the iron particles to cluster, indicating the presence of a flaw. Magnetic particle testing is highly sensitive and can detect defects that are not visible to the naked eye. It is commonly used in welding to inspect welds and adjacent areas for surface cracks and indications of stress.
3. Ultrasonic Testing (UT)
Ultrasonic testing is a versatile NDT method that uses high-frequency sound waves to inspect the internal structure of materials. It involves sending ultrasonic waves into the material and analyzing the reflected waves to identify any flaws or changes in the material’s properties. Ultrasonic testing can detect defects such as voids, inclusions, or lack of fusion within welds. It provides detailed information about the size, shape, and location of flaws, making it a valuable method for assessing the integrity of welded structures.
Visual Testing (VT)
a. Principles and Equipment used
Visual testing relies on the visual inspection of a material or component’s surface to identify defects. Trained inspectors utilize various tools and equipment, such as magnifying lenses, borescopes, or videoscopes, to conduct a thorough examination. The process involves inspecting the welds and adjacent areas for visible signs of cracking, incomplete penetration, undercutting, or misalignment. The inspector relies on their expertise and experience to identify potential flaws and determine their severity.
b. Applications in Welding
Visual testing is widely used in welding to assess the quality of welds and ensure compliance with industry standards and specifications. It is particularly effective in detecting surface cracks, which are common defects in welds. Visual testing is also valuable in identifying incomplete penetration, which can weaken the weld’s strength. Inspectors use this method to verify the alignment of welds, ensuring they meet the required specifications. Visual testing is essential during the fabrication process, as it allows for immediate adjustments or repairs before the completion of the welded structure.
c. Advantages and Limitations
The advantages of visual testing include its simplicity, cost-effectiveness, and immediate results. It does not require complex equipment or extensive training, making it accessible to a wide range of personnel. Visual testing can provide instant feedback, allowing for immediate actions to rectify any detected issues. However, its limitations lie in its inability to detect internal defects or assess the depth of flaws within the material. It heavily relies on the inspector’s expertise and may vary in consistency based on the individual’s skills and experience.
Magnetic Particle Testing (MT)
Magnetic particle testing is a widely used NDT method for detecting surface and near-surface defects in ferromagnetic materials. It relies on the principles of magnetism and the behavior of iron particles in the presence of a magnetic field. The process involves magnetizing the material and applying iron particles, either dry or suspended in liquid, to the surface. If there are any defects, such as cracks or discontinuities, the magnetic field will cause the iron particles to cluster, forming visible indications of the flaw.
Magnetic particle testing is highly sensitive and can detect flaws that are not visible to the naked eye. It is commonly employed in welding to inspect welds and adjacent areas for surface cracks, indications of stress, or other discontinuities. The method is particularly useful for detecting surface-breaking defects in materials with a high permeability to magnetic fields. However, it is not suitable for non-ferromagnetic materials and has limitations in detecting internal defects or identifying the severity of the detected flaws.
Ultrasonic Testing (UT)
Ultrasonic testing is a versatile NDT method that utilizes high-frequency sound waves to inspect the internal structure of materials. It involves transmitting ultrasonic waves into the material and analyzing the reflected waves to identify any flaws or changes in the material’s properties. Ultrasonic testing can detect a wide range of defects within a material, including voids, inclusions, or lack of fusion within welds.
In welding, ultrasonic testing is particularly valuable for assessing the integrity of welded structures. It provides detailed information about the size, shape, and location of flaws, enabling engineers and inspectors to make informed decisions regarding the quality and reliability of welds. Ultrasonic testing can be performed using different techniques, such as pulse-echo, through-transmission, or phased array. Each technique offers specific advantages and may vary in complexity and cost. Ultrasonic testing is highly accurate and reliable, but it requires trained personnel and specialized equipment to perform the inspections effectively.
Choosing the Right NDT Testing Method for Welding
When it comes to selecting the appropriate NDT testing method for welding, several factors need to be considered. These factors include the type of material being inspected, the nature of the defects to be detected, the required inspection speed, and the available resources. Case studies and examples can provide valuable insights into the selection process and help highlight the benefits of different NDT methods in specific scenarios.
For instance, in a project involving the fabrication of pressure vessels, where internal defects are critical, ultrasonic testing would be an ideal choice. Its ability to detect internal flaws accurately would ensure the integrity and safety of the vessels. On the other hand, if the project involves inspecting welds on the surface of a large steel structure, visual testing combined with magnetic particle testing may be more suitable. Visual testing can quickly identify surface cracks, while magnetic particle testing can provide additional confirmation and detect hidden discontinuities.
NDT Testing Certification and Training
NDT testing requires skilled and certified personnel to ensure accurate and reliable inspections. Certification is crucial for NDT technicians, as it demonstrates their competence and understanding of the principles, techniques, and equipment used in NDT testing. Certification programs follow industry standards, such as those provided by the American Society for Nondestructive Testing (ASNT) or the International Organization for Standardization (ISO). These programs typically include theoretical knowledge assessments and practical examinations to evaluate the technician’s ability to perform NDT inspections.
Training programs and courses are available to help individuals acquire the necessary knowledge and skills in NDT testing. These programs cover various NDT methods and their applications, equipment operation and maintenance, interpretation of test results, and quality control procedures. Some training programs offer certifications upon completion, providing a solid foundation for individuals seeking a career in NDT testing.
NDT Testing Services and Providers
When outsourcing NDT testing services, choosing the right provider is crucial to ensure accurate and reliable results. Several key considerations should be taken into account when selecting an NDT testing service provider. These considerations include the provider’s experience and expertise in the specific NDT methods required, their adherence to industry standards and regulations, the availability of state-of-the-art equipment, and their track record of delivering high-quality services.
To assist in the selection process, several top NDT testing service providers can be considered. These providers have established reputations in the industry and offer a range of NDT services, including visual testing, magnetic particle testing, ultrasonic testing, and more. Their expertise, experience, and commitment to quality make them reliable partners for ensuring the integrity and safety of welded structures.
Final Thoughts
Non-destructive testing (NDT) plays a pivotal role in welding, ensuring the quality and safety of welded structures. Visual testing, magnetic particle testing, and ultrasonic testing are three commonly used NDT methods in the welding industry. Each method has its principles, applications, advantages, and limitations, making them suitable for different scenarios and defect detection requirements. When choosing the right NDT method, factors such as material type, defect nature, inspection speed, and available resources should be considered. NDT technicians should undergo certification and training programs to ensure their competence in performing accurate inspections. Selecting the right NDT testing service provider is crucial to obtain reliable results.
By demystifying NDT testing and understanding its various methods, welders and engineers can ensure the quality, reliability, and safety of welded structures.