Destructive testing is a crucial process in various industries that involves subjecting materials or products to extreme conditions to assess their durability and performance. In this article, we will explore the concept of destructive testing and its different types. Whether it’s testing the structural integrity of a building or evaluating the strength of a new material, destructive testing provides valuable insights into product quality and safety.
By intentionally causing failure, engineers can identify weak points, analyze failure modes, and make necessary improvements to enhance the overall product design. From tension tests to impact tests, we will dive into the various methods used in destructive testing and their applications in different industries. So, let’s delve deeper into the world of destructive testing and discover its importance in ensuring quality and reliability.
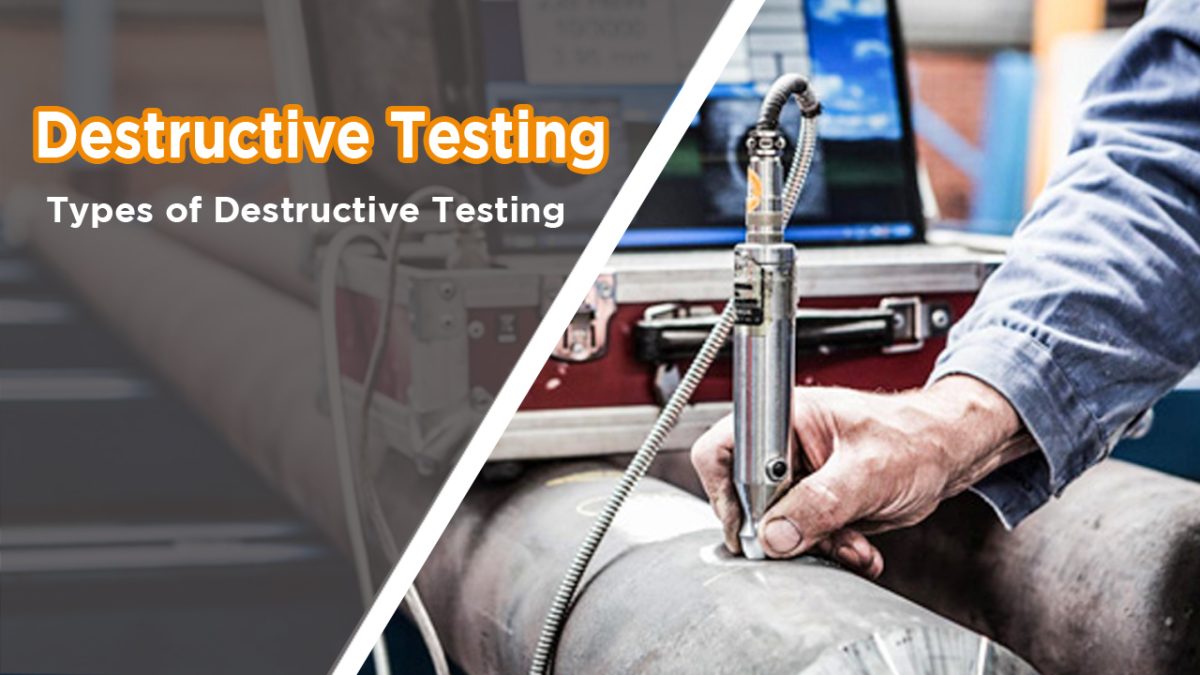
Image by eastern-steels
What is Destructive Testing?
Destructive testing is a crucial part of the product development and quality control process. It involves subjecting materials or components to extreme conditions that are intended to cause failure. The purpose of destructive testing is to push the limits of a product or structure and uncover any weaknesses or flaws that could compromise its safety and reliability. By intentionally breaking or damaging a sample, engineers can evaluate its performance in real-world scenarios and make informed decisions about design improvements or material selection.
Destructive testing is commonly used in industries such as aerospace, automotive, construction, and manufacturing. It is an essential tool for ensuring the safety and quality of various products, ranging from aircraft components to bridges and consumer goods. By understanding the different types of destructive testing and their applications, engineers and manufacturers can create safer and more reliable products.
Importance of Destructive Testing
Destructive testing is crucial for several reasons. First and foremost, it helps identify potential failure points in a product or structure. By intentionally subjecting materials to extreme conditions, engineers can simulate worst-case scenarios and evaluate how they perform. This allows them to identify any weak spots or design flaws that could lead to failure in real-world applications. By identifying these issues early on, engineers can make necessary design improvements and prevent costly failures and accidents.
Additionally, destructive testing helps ensure compliance with safety standards and regulations. Many industries have specific requirements and standards that products must meet to ensure safety. By conducting destructive tests, manufacturers can verify if their products meet these standards and make any necessary adjustments to ensure compliance.
Destructive testing provides valuable data about a material’s behavior under extreme conditions. This data can be used to validate computer simulations and models, improving the accuracy of future designs. It also helps engineers understand the limitations of different materials, enabling them to make informed decisions about material selection.
Common Types of Destructive Testing
Tensile Testing
Tensile testing, also known as tension testing, is one of the most common types of destructive testing. It involves subjecting a material to a controlled pulling force until it breaks. The purpose of tensile testing is to evaluate a material’s strength, ductility, and other mechanical properties.
During a tensile test, a sample is placed in a testing machine and gradually pulled until it fractures. The machine measures the applied force and the resulting elongation or deformation of the material. This data is used to calculate properties such as the ultimate tensile strength, yield strength, and elongation at break.
Tensile testing is widely used in industries such as automotive, aerospace, and construction. It helps engineers understand how a material will behave under tension and determine its suitability for specific applications. For example, in the automotive industry, tensile testing is used to evaluate the strength of steel used in car frames and determine if it meets safety standards.
Impact Testing
Impact testing is used to evaluate a material’s ability to absorb energy under high-velocity impact conditions. It is particularly important for materials that are subjected to sudden or dynamic loads, such as those used in the automotive and aerospace industries.
During an impact test, a sample is placed in a pendulum or drop-weight machine, and a heavy weight is released to strike the sample. The machine measures the energy absorbed by the sample during impact and calculates properties such as the impact strength and toughness.
Impact testing helps engineers assess a material’s ability to withstand sudden loads and determine its suitability for applications where impact resistance is critical. For example, in the aerospace industry, impact testing is used to evaluate the strength of materials used in aircraft components, such as fuselage structures.
Hardness Testing
Hardness testing is used to evaluate a material’s resistance to indentation or scratching. It provides insights into a material’s strength, wear resistance, and ability to withstand localized deformation.
There are several methods of hardness testing, including the Brinell, Rockwell, and Vickers tests. Each method involves applying a known force to a sample and measuring the depth or size of the resulting indentation. The hardness value is determined based on the size of the indentation and the applied force.
Hardness testing is used in various industries, including manufacturing, automotive, and tooling. It helps engineers select materials that are suitable for specific applications, such as determining the hardness of a metal alloy used in cutting tools or measuring the hardness of automotive parts to ensure they can withstand wear and tear.
Fatigue Testing
Fatigue testing is used to evaluate a material’s resistance to repeated loading and unloading cycles. It helps engineers understand how a material will perform under cyclic or fluctuating stresses, which is particularly important for applications where components are subjected to repetitive loading, such as aircraft wings or suspension systems.
During a fatigue test, a sample is subjected to a cyclic loading pattern, with the amplitude and frequency of the cycles controlled by the testing machine. The machine measures the number of cycles the material can withstand before failure occurs, providing valuable data about its fatigue strength and endurance limit.
Fatigue testing helps engineers determine the safe operating life of a material and identify potential failure points due to cyclic loading. This information is crucial for designing durable and reliable products that can withstand long-term usage without failure.
Compression Testing
Compression testing is used to evaluate a material’s ability to withstand compressive forces without deformation or failure. It is commonly used for materials such as concrete, ceramics, and composites.
During a compression test, a sample is placed in a testing machine, and a compressive force is applied until the sample deforms or fractures. The machine measures the applied force and the resulting deformation or strain. This data is used to calculate properties such as compressive strength and modulus of elasticity.
Compression testing is essential for determining the load-bearing capacity of materials used in construction and structural applications. For example, in the construction industry, compression testing is used to evaluate the strength of concrete used in building foundations and determine if it meets design specifications.
Shear Testing
Shear testing is used to evaluate a material’s ability to withstand forces that cause parallel layers to slide past each other. It is particularly important for materials used in applications where shearing forces are prevalent, such as in the manufacturing of cutting tools or fasteners.
During a shear test, a sample is subjected to a shearing force until it fractures. The machine measures the applied force and calculates properties such as the shear strength and shear modulus.
Shear testing helps engineers understand how a material will behave under shear stresses and determine its suitability for specific applications. For example, in the manufacturing industry, shear testing is used to evaluate the strength of adhesive bonds and determine if they can withstand the shear forces experienced during usage.
Final Thoughts
Destructive testing is an essential tool for ensuring the safety and reliability of products and structures. By intentionally subjecting materials or components to extreme conditions, engineers can identify potential failure points and evaluate their performance in real-world scenarios. Tensile testing, impact testing, hardness testing, fatigue testing, compression testing, and shear testing are just a few of the many types of destructive testing used in various industries.
Each technique provides unique insights into a material’s behavior under specific conditions, allowing engineers to make informed decisions about design improvements or material selection. Understanding the different types of destructive testing is crucial for engineers, manufacturers, and anyone involved in product development or quality control.
By utilizing these tests, industries can create safer and more reliable products that meet the highest standards of safety and performance.