Welding without filler metal is a challenging task that requires a number of steps and processes to achieve. But once you have mastered the procedure, it becomes one of the most efficient ways to join two metals together. With the advancement in technology, there are several new types of welding processes were introduced in recent years, including direct metal-to-metal welding and self-shielding arc welding.
These processes eliminate the need for using filler metal or shielding gas by increasing the efficiency and speed of welds without affecting the joint quality. This article discusses everything about welding without filler metal, from its advantages over traditional methods to key considerations when working with this process.
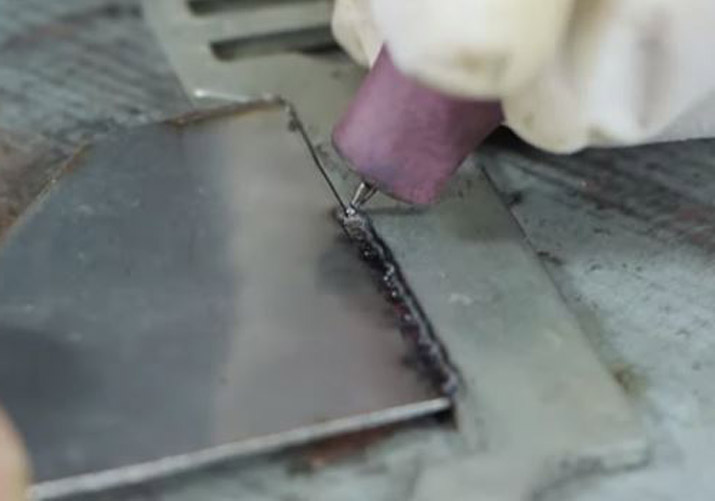
What is Welding Without Filler Metal?
Weld metal without filler is a welding process that joins metals without the use of metal-based filler metal. Instead, a different type of material, such as metal powder, metal powder solution, or binder, is used to fill the weld joint. The advantage of welding without filler metal is that it doesn’t require any additional welding equipment.
The welding process itself creates a weld joint, which can then be filled with a binder or powder. The advantages of welding without filler over traditional welding processes are low or zero cost per weld, low joint contamination, and low energy consumption.
Types of Welding Processes
Shielded Metal-Shielded Metal (SMS)
This welding process is the opposite of direct metal-to-metal welding, where a shielding gas is used to protect the weld joint from the atmosphere. On the other hand, in this process, a metal shield is used to protect the weld joint against the atmosphere.
Shielded Metal-Constant-Current Arc
This welding process is similar to direct metal-to-metal welding, except it uses a constant-current arc. In this process, the arc is shielded by a metal shield and a shielding gas, while
Considerations when working without filler metal
The welding process for without filler metal requires a different procedure and welding equipment compared with welding without filler. As a result, the key considerations when working with welding without filler metal include the joint material, welding joint size, welding joint position, welding joint type and quality, and welding pressure and current. One of the key factors to consider when welding without filler is the joint material you are going to use.
The joint material must have the right mechanical, thermal, and hydraulic properties or characteristics to withstand the stress of welding. It’s also important to assess the welding joint size and shape to ensure the joint size is big enough for the weld joint to properly fill.
The welding joint shape can be either parallel or perpendicular to the joint axis. If the joint shape is perpendicular, the joint angle should be between 35 and 90 degrees to ensure the weld joint has enough volume to properly fill. The welding joint position can also affect the weld joint, especially when using weld without filler metal. Joint positioning can affect the weld joint shape and size, as it can affect the weld joint axis. The position of the joint can be horizontal, vertical, offset, or canted. The position of the joint can also affect the weld joint shape and size.
Required equipment for welding
The required equipment for weld without filler metal includes a welding machine with a welding power source, a welding torch, a shielding gas, an air supply, a regulator, a flowmeter, and an air filter. Welding machine settings should be adjusted to full pierce while the weld joint is forming. Your welding parameters should be adjusted based on the joint shape, joint size, and weld joint position to achieve the best weld joint quality. It’s also important to adjust your torch settings to obtain the right weld puddle or weld pool size and shape.
The right torch settings can help control the weld joint shape, as well as the weld joint size and shape. To ensure the best weld joint quality, you should also adjust the shielding gas and air settings to provide the right amount of shielding gas and oxygen. The right amount of shielding gas and oxygen can help control the weld joint shape, as well as the weld joint size and shape.
How to weld without filler metal?
There are two methods for welding without filler metal. In both cases, the joint shape needs to be deep enough for the weld joint to properly fill.
Method 1
Gas-Drawn Arc To produce a gas-drawn arc in this method, the joint shape is first prepared with a slag removal tool, such as a slag removal tool. As the joint shape nears completion, the joint is brought inside the torch shielding gas and arc area to produce a gas-drawn arc. The torch shielding gas should be at a high enough concentration to block the flux and prevent the weld joint from being exposed to the atmosphere. After the arc is established, the welding joint is drawn into the joint.
Method 2
MIG Arc-Spatter Shielding and shielding gas are not used in this method. Instead, the joint is drawn inside the MIG torch spatter shield, which prevents the weld joint from exposure to the atmosphere. After the arc is established, the joint is spattered to produce a weld joint.
Method 3
Constant-Current Arc-Spatter Shielding gas and arc are not used in this method. Instead, the joint is brought inside the welding torch spatter shield, which prevents the weld joint from exposure to the atmosphere. After the arc is established, the joint is spattered to produce a weld joint.
Advantages of Welding Without Filler Metal
Here are some advantage of working without filler metal:
Low or zero cost per weld
Traditional welding processes generally require the use of filler metal, which can add up to a significant cost. Welding without filler metal, however, has no additional cost because the process itself creates a weld joint.
Low or zero energy consumption
Welding without filler has a low energy consumption compared with traditional welding processes, which can help reduce the impact on the environment.
Low or zero joint contamination
Welding without filler metal has a low risk of joint contamination compared with traditional welding processes, which can help reduce the impact on the environment.
Faster welding speed
Welding without filler has a quicker welding speed compared with traditional welding processes, which can help increase productivity.
Reduced joint distortion
Welding without filler metal has a reduced risk of joint distortion compared with traditional welding processes, which can help increase productivity.
Disadvantages of Welding Without Filler Metal
Here are some disadvantage of welding without filler :
Joint contamination
As traditional welding processes use filler metal, the joint becomes contaminated after welding. Welding without filler, does not produce a weld joint, so in this case, the joint remains uncontaminated after welding.
Equipment maintenance
Although the welding machine is not used in welding without filler metal, it still needs to be maintained to ensure it works properly.
Weld joint size and shape
Weld without filler metal has a lower weld joint size and shape compared with traditional welding, which can affect the weld joint quality and weld joint strength.
Weld joint stability
Welds produced in welding without filler metal have a higher tendency to become unstable compared with those produced in traditional welding.
Safety precautions while working Without Filler Metal
The welding process itself can generate hazardous chemicals and gases, including weld spatter, hydrogen, oxygen, and carbon dioxide. You should wear suitable welding safety equipment when welding without filler metal to prevent exposure to these hazardous materials. The weld temperature and joint pressure should be monitored to ensure the weld joint is being heated to the required temperature and joint pressure. The correct weld joint position should also be maintained to ensure the weld joint is held firmly against the base material. You should also wear appropriate safety footwear when walking around the welding position to prevent serious injury from falling or slipping.
The bottom line
It’s important to choose the right time, place, and type of weld joint for welding without filler metal. Whether you are working in a pass through or shielded area, it’s important to choose the right time and location for the weld joint. To start with, it’s important to determine the type of weld joint you are going to use. The type of weld joint you choose can help determine the strength and quality of your weld joint. The three most common types of weld joints are butt joints, fillet, and lap joints. The type of weld joint you choose should be based on the material being welded together.
When welding without filler metal, it’s important to ensure that the joint shape is deep enough for joint to properly fill. Deep joint shapes increase the weld joint strength and improve the weld joint quality. Unlike conventional weld joints, the weld joint is not always symmetrical about the joint axis. Therefore, it’s important to make sure the weld joint is symmetrical about the joint axis.