Welding thin sheet metal with flux core requires careful control to prevent burn-through. Use a low amperage setting and maintain a steady hand.
Welding thin sheet metal can be tricky due to its susceptibility to warping and burn-through. Flux core welding offers a convenient solution, especially for outdoor conditions and windy environments. It doesn’t require an external shielding gas, making it simpler and more portable.
Proper technique and equipment settings are crucial to achieve strong, clean welds. A low amperage setting helps manage heat input, while a steady hand ensures consistent weld quality. Always practice on scrap pieces to fine-tune your approach before working on the final project. This method proves effective for various thin metal applications, ensuring durability and precision.
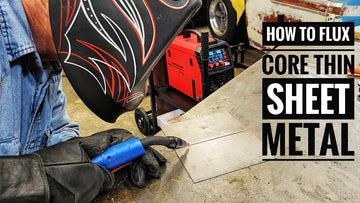
Credit: www.arccaptain.com
Introduction To Welding Thin Sheet Metal
Welding thin sheet metal is a delicate task. It requires precision and skill. Using flux core can make this easier. This method is popular in many industries. It offers several benefits.
Why Choose Flux Core?
Flux core welding is perfect for thin sheet metal. It is user-friendly and effective. Here are the main reasons:
- Less equipment needed
- Works well in outdoor conditions
- Provides strong, clean welds
- Suitable for various metals
Common Applications
Flux core welding is used in many fields. Here are some common applications:
Industry | Application |
---|---|
Automotive | Repairing car bodies |
Construction | Building metal frameworks |
Manufacturing | Creating metal products |
Essential Tools And Equipment
Welding thin sheet metal with flux core requires specific tools. Having the right equipment ensures a clean and strong weld. Below are the essential tools you need.
Welding Machine
A flux core welding machine is crucial. It should have adjustable settings. This helps you control the heat and speed. Ensure the machine is suitable for thin metals. Look for machines with a low amp range.
A machine with variable voltage settings is best. This feature helps prevent burn-through. A lightweight, portable machine is also useful.
Protective Gear
Welding is dangerous without proper protection. You need protective gear to stay safe. Here is a list of essential items:
- Welding helmet: Protects your eyes and face from sparks.
- Welding gloves: Keep your hands safe from heat.
- Welding jacket: Shields your body from sparks.
- Welding boots: Protect your feet from falling hot metal.
Make sure your gear is fire-resistant. Comfortable gear will make your work easier.
Preparing The Work Area
Welding thin sheet metal with flux core requires a well-prepared work area. Ensuring safety and efficiency is crucial. Let’s explore the essential steps for a perfect setup.
Safety Precautions
Safety is always the priority. Follow these steps to protect yourself:
- Wear a welding helmet and gloves to protect your eyes and hands.
- Use a flame-resistant jacket to prevent burns from sparks.
- Ensure proper ventilation to avoid inhaling harmful fumes.
- Keep a fire extinguisher nearby in case of emergencies.
- Clear the area of any flammable materials before starting.
Work Surface Setup
A stable work surface is essential for precise welding. Follow these tips:
- Choose a flat, sturdy table that can support your materials.
- Use welding clamps to secure the sheet metal in place.
- Ensure the work surface is clean and free of debris.
- Position your welding machine within easy reach for adjustments.
Here is a summary of the key points for an ideal setup:
Task | Details |
---|---|
Safety Gear | Helmet, gloves, jacket, fire extinguisher |
Ventilation | Proper air flow to avoid fumes |
Work Surface | Flat, sturdy, and clean |
Secure Materials | Use welding clamps |
Following these guidelines ensures a safer and more efficient welding process. Prepare your work area properly and weld with confidence.
Credit: www.mig-welding.co.uk
Selecting The Right Flux Core Wire
Choosing the right flux core wire is crucial for welding thin sheet metal. Selecting the wrong wire can lead to poor weld quality and increased spatter. This section will guide you on how to select the appropriate flux core wire for your project.
Wire Diameter
The diameter of the flux core wire plays a significant role in welding thin sheet metal. For thin materials, you should use a smaller diameter wire. Smaller diameters minimize heat input and help avoid burn-through.
Material Thickness | Recommended Wire Diameter |
---|---|
Less than 1/8 inch | 0.030 inches |
1/8 inch to 1/4 inch | 0.035 inches |
Material Compatibility
Ensure the flux core wire is compatible with the metal you are welding. Different wires are designed for different metals. For example, use an E71T-11 wire for mild steel. This wire type is versatile and provides good penetration.
For stainless steel, a 316L flux core wire is ideal. It offers excellent corrosion resistance and weld appearance. Always check the manufacturer’s recommendations for wire compatibility.
- Mild Steel – E71T-11
- Stainless Steel – 316L
- Galvanized Steel – E71T-GS
Using the right wire ensures strong, clean welds and reduces the risk of defects.
Setting Up The Welding Machine
Setting up your welding machine correctly is crucial for welding thin sheet metal with flux core. Proper setup ensures smooth operation and high-quality welds. Key settings include voltage and wire feed speed.
Adjusting Voltage
Voltage controls the heat of the weld. For thin sheet metal, lower voltage is ideal. High voltage can burn through the metal. Start by setting the voltage as per the machine’s manual.
- Check the manual for recommended voltage.
- Set the voltage to a low setting.
- Test on scrap metal to fine-tune.
Controlling Wire Feed Speed
Wire feed speed determines the rate at which the wire is fed into the weld. For thin sheet metal, a slower feed speed is better. Too fast can cause poor penetration and spatter.
- Refer to the machine’s guide for initial settings.
- Set a slow feed speed to start.
- Adjust by testing on scrap pieces.
Always use a consistent speed. Inconsistent speed leads to weak welds and defects.
Metal Thickness | Voltage | Wire Feed Speed |
---|---|---|
0.6mm – 0.8mm | 14-16V | 2.5-3.5 m/min |
0.8mm – 1.0mm | 16-18V | 3.5-4.5 m/min |
Correct voltage and wire feed speed settings prevent issues like burn-through and spatter. Always refer to the machine’s manual and perform tests to ensure optimal settings.
Proper Welding Techniques
Welding thin sheet metal with flux core can be tricky. Proper techniques help achieve strong, clean welds. These methods ensure minimal damage and best results.
Maintaining Steady Hand
A steady hand is crucial. It helps create smooth, consistent welds. Follow these tips:
- Practice holding the welding gun firmly.
- Use both hands for better control.
- Move slowly and consistently along the weld path.
Position yourself comfortably. It reduces strain and improves accuracy. Use a support if needed. Rest your arm or hand on a steady surface. This helps maintain control over the welding gun.
Managing Heat Input
Thin sheet metal is prone to warping. Managing heat input is essential. Follow these steps:
- Set the correct voltage and wire feed speed.
- Use short welds, also known as “stitch welding”.
- Allow the metal to cool between welds.
Monitor the weld pool closely. A small, controlled pool prevents burn-through. Keep the welding gun at the right angle. This helps direct heat away from the metal.
Refer to the table below for optimal settings based on metal thickness:
Metal Thickness (inches) | Voltage (V) | Wire Feed Speed (inches per minute) |
---|---|---|
0.024 | 16-18 | 200-250 |
0.030 | 18-20 | 250-300 |
0.035 | 20-22 | 300-350 |
Adjust settings as needed. Test on scrap metal first. This ensures proper setup and avoids damage to the actual workpiece.
Troubleshooting Common Issues
Welding thin sheet metal with flux core can be tricky. Many welders face common problems during the process. Understanding these issues helps achieve better welds.
Burn Through
Burn through is a common issue in welding thin sheet metal. It occurs when the metal gets too hot and melts away. This leaves a hole in the material.
To prevent burn through, try these tips:
- Lower the amperage settings on your welder.
- Use a faster travel speed to reduce heat build-up.
- Employ a backing bar to absorb excess heat.
- Use a smaller diameter wire for less heat input.
Porosity
Porosity refers to the presence of tiny holes in the weld. These holes weaken the weld and can lead to failure.
Causes of porosity include:
- Contaminated base metal or filler wire.
- Improper gas coverage, leading to air pockets.
- Excessive moisture on the metal surface.
To fix porosity, consider these steps:
- Clean the metal surface thoroughly before welding.
- Ensure proper gas flow to shield the weld area.
- Store filler wire in a dry place to prevent moisture absorption.
Addressing these common issues can significantly improve your welding results. Practice these tips and watch your skills grow.
Post-welding Considerations
After welding thin sheet metal with flux core, it’s crucial to focus on post-welding considerations. These steps ensure the weld’s strength and appearance. Proper inspection and cleaning lead to a successful project.
Inspecting The Weld
First, inspect the weld carefully. Look for any imperfections or defects. Common issues include:
- Cracks
- Porosity
- Incomplete fusion
Use a magnifying glass for detailed inspection. Check the entire weld length. Ensure the weld is consistent and free of gaps.
For a thorough inspection, consider using non-destructive testing (NDT) methods. These methods include:
- Dye penetrant testing
- Ultrasonic testing
These methods help identify hidden flaws. An accurate inspection guarantees a strong and safe weld.
Cleaning And Finishing
After inspection, clean the weld area. Flux core welding leaves residue. Remove this residue to prevent corrosion.
Follow these steps for cleaning:
- Brush off loose slag with a wire brush.
- Use a grinder to smooth the weld.
- Wipe the area with a clean cloth.
For a polished finish, use a sanding disc. Sand the weld gently. Ensure the weld blends with the surrounding metal.
Apply a protective coating to the cleaned weld. This coating prevents rust and enhances appearance.
Post-welding considerations are essential for a high-quality project. Inspect and clean the weld properly for the best results.

Credit: www.youtube.com
Frequently Asked Questions
Can You Weld Thin Sheet Metal With Flux Core?
Yes, you can weld thin sheet metal with flux core. It’s challenging, but with proper settings and technique, you can achieve good results.
What Settings For Flux Core Welding Thin Metal?
Use low voltage and wire speed settings. This helps prevent burning through the thin metal. Practice is essential.
How To Avoid Burn-through In Thin Metal Welding?
To avoid burn-through, use a lower voltage setting. Move quickly and maintain a steady hand during welding.
What Type Of Flux Core Wire For Thin Metal?
Use a 0. 030-inch flux core wire. It’s suitable for welding thin sheet metals and provides better control.
Conclusion
Mastering flux core welding for thin sheet metal requires practice and precision. Remember to adjust settings for optimal results. Patience and careful technique are key to achieving clean welds. With dedication, you can enhance your welding skills and create strong, reliable joints.
Keep experimenting and refining your approach for continued improvement.