Flux core is one of the newer welding processes you can use to join thin sheet metal. It’s also one of the more complex and welding thin sheet metal with flux core is a great way to produce complex, detailed shapes quickly and efficiently. In this article, you will learn about flux core welding and get tips for successfully using. The last thing you need is to ruin a perfectly good piece of thin sheet, only because you didn’t know what you were doing. So read on and learn everything you need to know about flux core welding with thin sheet metal.
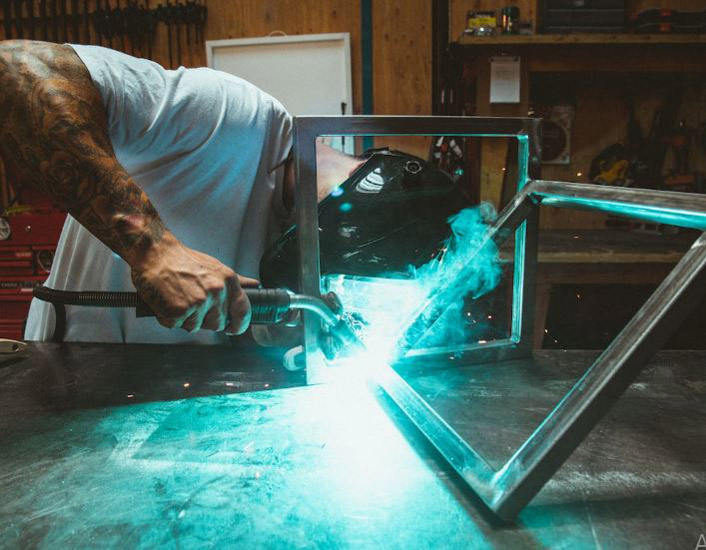
Definition of Flux Core Welding
Flux core welding is an advanced welding technique that uses a special shielding gas to join metallic materials. Unlike gas metal arc welding (GMAW), flux core requires a shielding gas and the ability to arc weld without the need for an electrode. The flux core welding process utilizes a fluxing agent to create a fluxed environment between the weld metal and the workpiece, allowing the weld metal to arc without the presence of Oxygen. Since the weld metal and workpiece are in a fluxed environment, a coating is formed on the weld metal which acts as a shield against the Oxygen, preventing it from combining with the weld metal.
Flux core welding is a bit more difficult to learn than gas metal arc welding, but the end result is that you can weld extremely complex and detailed shapes, which is helpful if you need to weld thin metal in a very specific shape. Like with most other welding processes, the quality of the weld is determined by a number of factors including but not limited to the skill of the welder, the skill of the operator, what gauge of metal the operator is using, the type of equipment they are using, and the environment in which they are welding.
Using Flux Core Welding for Thin Sheet Metal
If you have ever attempted to weld thin metal, you are probably aware that welding this kind of metal is extremely difficult. Weld metal that is less than 6mm will have a tendency to buckle and sag over time, and it can be extremely difficult to get a good bead on the metal. Weld metal that is too thick will cause you issues as well. To avoid these issues, you will want to weld thin sheet metal with flux core. Welding thin sheet metal with flux core is a great way to produce complex, detailed shapes quickly and efficiently. In this article, you will learn about flux core welding and get tips for successfully using.
Differences between flux core and conventional welding
There are a few key differences between welding with flux core and conventional welding. The shielding gas that is used in flux core is significantly different from the shielding gases used in GMAW. The shielding gases used in flux core are much less Oxygen-rich, and the fluxed environment that flux core creates makes it an extremely effective welding method for joining sheet metal. The shielding gas in flux core welding is also different, and it creates an inert shield that keeps the Oxygen from combining with the weld metal. A second major difference between flux core and conventional welding is the process of welding.
In flux core welding, the weld metal is not an arc and it is not heated to a high enough temperature to produce a good bead. Instead, a shielding gas is used in flux core, and the weld metal is quenched, which is to say it is cooled. However, flux core welding is an advanced welding method that requires a high level of skill to get it right.
Things You Need to Know When Welding
Welding with flux core requires a high level of skill – welding with flux core is an advanced welding process – flux core is difficult to learn – you will need to practice a lot to become proficient – you will need a flux core shield to weld with flux core – flux core is best for complex, detailed shapes. – If you are welding thin metal, flux core is hands down the best method. – You need to use high quality welding rods.
Why is Welding With a Shield So Difficult?
You may be surprised to learn that welding thin sheet metal with a flux core shield is harder than welding thick metal. The reason why welding with a flux core shield is so difficult is that it makes welding with flux core more difficult than welding with an electrode. When you weld with an electrode, you have a fairly predictable arc that you can focus on. Welding with a flux core shield is different, it is an arc that you don’t even see. Welding with a flux core shield requires focus, precision and a high level of skill. When you weld with a shield, you are welding in an invisible arc.
The shielding gas creates an inert shield that prevents the Oxygen from combining with the weld metal. However, shielding gases also contain Argon, Nitrogen and Helium, which makes it difficult to shield your weld and keep the shield clean. Welding with a shield is very difficult to learn, you will need to practice a lot to get it right.
How to Do Welding Thin Sheet Metal with Flux Core?
Below are some steps to help you successfully weld with flux core. The first thing you need to do is to pick a shielding gas. A shielding gas is necessary for welding with flux core, but there are many options to choose from. Choose a shielding gas that is low in Oxygen and rich in other gases such as Argon, Helium, Krypton or Nitrogen. Make sure the shielding gas you pick has a low percentage of Argon in it, as Argon is what makes the fluxed shielding gas. And as always, pick a shielding gas that is certified for flux core welding.
Next, you need to pick a welding rod that is right for your application. Pick a welding rod that is right for your application and is certified for flux core welding. Choose a gauge of metal that is right for your application. Pick a higher quality welding rod to help with the Shielding gas. Pick a rod that is certified for flux core welding. Pick a rod that is higher quality. Pick a lower quality rod for thicker metals, or a higher quality rod for thinner metals. Choose a rod that is certified for flux core welding.
Third, pick a shielding gas shield. Pick a flux core shield that is certified for flux core welding. Pick a shielding gas shield that is certified for flux core welding. Choose a shielding gas shield that is certified for flux core welding. Pick a shielding gas shield that is certified for flux core welding. Fourth, you need to adjust the speed of the welder and make the correct adjustments to the current. Pick the correct speed for your application.
Safety and Precautions for Welding Thin Sheet Wetal with flux core
When welding with flux core, remember that shielding gas is extremely hazardous. Always wear welding gloves, safety glasses, a dust mask, and a breathing filter as recommended by the welding certification program you are using. To help prevent overexposure to the shielding gas, always weld in a well-ventilated area and wear a welding helmet. Make sure you are shielding your weld and keep the shield clean by wiping it with a rag dipped in water after welding. Always use a spool gun if possible, and always ground your shield if it is magnetic.
Tips for Successful Welding
There are a few tips you will want to keep in mind when welding thin sheet metal with flux core, and they are as follows. First, make sure that your fluxed shield is kept clean and free from dust and other particles. Second, make sure your shielding gas is not leaking from your shield and that it is kept in a clean container. Third, do not use oils, grease or other liquids when welding with a fluxed shield. Fourth, do not use a torch hotter than the recommended temperature on your certification program. Fifth, never weld with a flux core shield and a conventional