Welding thin sheet metal is a challenge for any welder, but it can be even more daunting as an entry-level amateur or as a seasoned professional. For novices and experts alike, the key to successful welding of thin sheet metal is practice and patience. Knowing which tips and techniques work best for you when you are working with thin sheet metal will help you get the most from your projects.
This article covers everything you need to know about welding thin sheet metal: from tips for beginners to advanced welding techniques that experienced professionals use under difficult circumstances. With these insights in mind, you all have a better understanding of how to best approach the challenges presented by this type of welding.
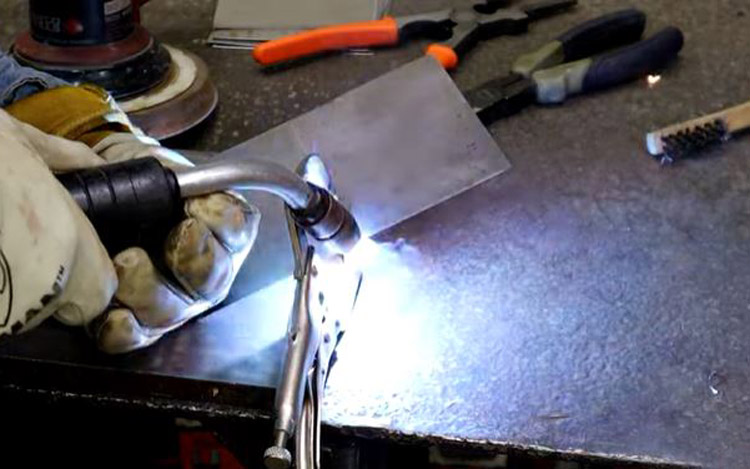
Choosing the Right Equipment
Choosing the right welder and equipment for welding thin sheet metal can be challenging. As you have probably figured out, welding thinner metal requires more precise control of the weld process. This can be incredibly challenging when you are starting to weld thinner metal, so it’s important to choose a welder and equipment that will allow you to succeed. For beginners, a mig welder is a great choice. It’s easy to use and will allow you to practice welding before investing in a more expensive and powerful arc welding machine.
A mig welder allows you to weld a wide range of metals, making it a great choice for welding thin sheet metal. If you are planning on welding steel often or you did like to invest in a more powerful welding machine, look for one with a power range of at least 8 amps. For a more affordable option, consider buying a 6-8 amp machine. If you are starting welding but have experience welding with a torch, a 4-6 amp machine is a good option.
How to Weld Sheet Metal Easily?
When welding metal sheet, the most important tip is to start with a clean, dust-free workspace. Cleaning off the area and placing a drop cloth beneath the work surface are essential to prevent spatter and slag from hitting your face, clothes, or eyes. Preparation is also key. When welding thin sheet metal, it’s especially important to keep your work area as clean as possible. Keep your workbench and other surfaces clean so you can safely weld and access all of the components you need to weld your project. Keep your workspace organized so you can quickly locate the tools, components, welding equipment, and welding rods you’ll need to complete your project.
Mig Welding Thin Sheet Metal
Mig welding is a popular and straightforward method of welding thin sheet metal. For mig welding, you don’t need much in the way of equipment. You will only need a mig welder and a proper technique for mig welding thin metal. If you are new to welding, start by welding with a low-amperage setting and a small wire feed.
Your mig welder should have a minimum of a 4-6 amp setting, with a range of 10-30 amps recommended for weld thin sheet metal. Start with a lower-amperage setting, and practice welding with a smaller wire feed until you’re comfortable welding without causing excessive damage to the material.
If you are welding with a low-amperage setting, you will need to be more careful when welding. Take your time, stay in control, and maintain a good distance between the weld joint and the material. This will prevent excessive damage to the material, which can be frustrating when you are trying to weld thin sheet metal.
Advanced Welder Tips and Tricks
Thin metal welding presents a high degree of difficulty for all welders. To get the best results from your welding, it’s important to understand what’s happening in your weld joint and how to correct any mistakes that may occur. Understanding the difference between joint type joints will help you identify what’s happening in the weld joint, which will help you correct any mistakes and make the weld joint right.
When welding thin metal with flux core or mig welding, you need to be extra aware of the material’s physical characteristics. When welding thin metal, it’s important to maintain a consistent distance between the weld joint and the material. Maintaining consistent distance will help prevent spatter, which can be frustrating and difficult to clean off.
Final Thoughts
welding thin metal presents a unique set of challenges. For experienced welders, these challenges can seem insurmountable. There are a few key tips and tricks you can use to get started welding thin metal and succeed. For beginners, a mig welder is a great choice. It’s easy to use and will allow you to practice welding before investing in a more expensive and powerful arc welding machine.
A mig welder allows you to weld a wide range of metals, making it a great choice for welding thin sheet metal. When welding thin metal, it’s especially important to keep your work area as clean as possible.
Keep your workbench and other surfaces clean so you can safely weld and access all of the components you need to weld your project. These tips can help you overcome the challenges associated with welding thin metal. When you are ready to start welding thin metal, follow these tips to get the most out of your projects.