When you welding steel vs aluminum, there are several tips you need to know before you get started. Welding this type of metal requires some different techniques than welding other materials. That said, learning how to successfully weld steel vs aluminum is easier than you think. Improving your results when welding these materials doesn’t have to be as challenging as most people might imagine. The information in this article will help you learn how to do just that. Keep reading if you want to learn more about which factors affect your results when welding steel vs aluminum, what types of welds work best for each material and more.
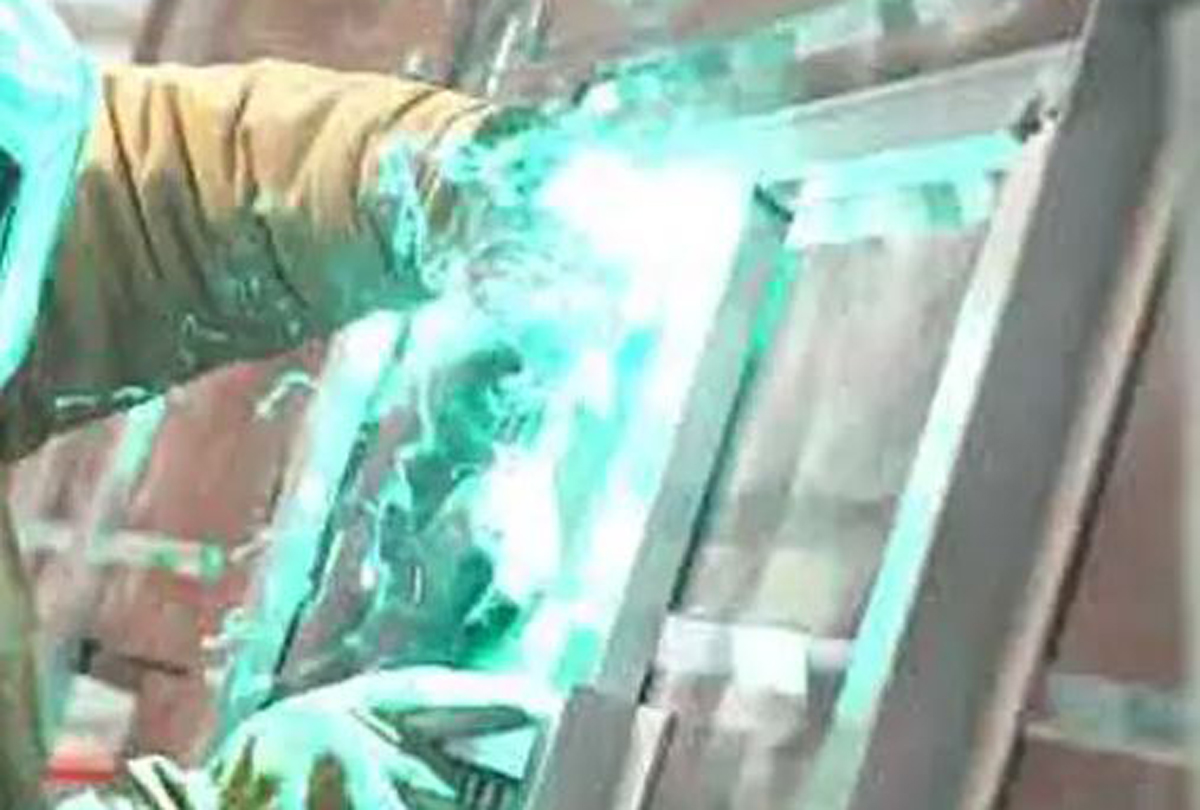
Image : looktrailers9709
Popularity of Welding Steel and Aluminum
Welding steel vs aluminum is a common question that comes up frequently. You might also be wondering why more people aren’t welding these materials rather than other types of metals. There are certainly benefits to welding both steel and aluminum. But, you should choose a material based on your welding needs. Aluminum is more commonly used than steel. Aluminum is a lighter weight material, so it might be easier to weld when certain weld joints are necessary. Despite these factors, welding steel vs aluminum is still an important skill.
Aluminum is often used in aircraft and is an important part of many industries. Steel is also used in many products. Steel is used in cars, structures, tools, ships, and many other types of products. Welding steel is a great way to join these products. Aluminum is used in different types of products like aircraft and sports equipment. Welding aluminum is also great for joining different types of products. Welding both types of metal is important for many industries.
Affects Your Welding Results
There are many factors that affect your welding results when welding steel vs aluminum. Factors such as the type of welding machine, your welding setup, the welding gas you use and more all influence your welding results. The type of joint you are welding will also affect your results. Butt welds don’t have any effect on the integrity of the joint, but penetrate less than fillet welds.
You should also consider the type of material you are welding. Some materials, like steel, are more forgiving than other materials, like aluminum. That means that you may have a better chance of getting a successful weld if you choose to weld steel.
Importance of Welding Steel vs. Aluminum
Welding steel vs aluminum is an important skill for several reasons. These include:
- It’s easier to get a license for welding aluminum than steel.
- You have more options when welding steel. For example, you can weld bare metal, stainless steel, and more.
- The end strength of the weld depends on the weld bead profile and filler metal.
- The weld area and weld penetration can also affect the integrity of the product.
Types of Welds for Steel and Aluminum
Depending on the type of welding you will be doing, there are several types of welds you can choose from. These types of welds allow you to adhere the two materials together more securely. – Shielded Metal Arc Welding (SMAW) – Gas Metal Arc Welding (GMAW) – Resistance Spot Welding (RWP) – Gas Tungsten Arc Welding (GTAW) – Flux Core Welding (FCW)
Shielded Metal Arc Welding (SMAW): SMAW is a type of welding that uses a shielded electrode to arc weld two pieces of metal together. Shielding protects the surrounding areas from the intense heat produced when welding, making SMAW one of the most common types of welding.
Gas Metal Arc Welding (GMAW): GMAW is a welding process that uses a gas to arc weld two pieces of metal together. This welding process produces a weld with a bright orange color that is ideal for making structural or mechanical joints.
Resistance Spot Welding (RWP): RWP uses a resistance spot welder machine to weld a small area together. This type of welding produces a strong, durable joint because it uses small weld beads that penetrate deeply into the material. Gas
Tungsten Arc Welding (GTAW): GTAW is a welding process that uses tungsten as the welding electrode. Because it’s not a cheap metal, welding with tungsten produces a more durable weld joint.
Flux Core Welding (FCW): FCW is a welding process that uses a flux core to arc weld two pieces of metal together. Flux core welding produces a weld joint that is more resistant to corrosion than other welding processes.
Tips for Successful Welding Steel vs Aluminum
– Keep your distance between the welding area and the work piece to a minimum.
– Don’t use a welding torch that’s too hot. You can burn the aluminum and make the weld weaker.
– Wear welding gloves to protect your hands from burns.
– Weld with thicker electrodes. Aluminum and steel have different characteristics that affect the weld strength. Using thicker electrodes helps you weld these different types of metals together.
– Weld with a shorter gas flow rate. Aluminum welding rods tend to produce a wider bead than steel welding rods.
– Weld with a higher filler metal content. Aluminum is less dense than steel. For this reason, you need to use more filler metal when welding steel vs aluminum.
– Weld with a lower voltage. Aluminum has a lower melting point than steel.
– Use a bead breaker when welding steel vs aluminum. A bead breaker is a side kick that keeps the weld bead from breaking.
Last word about Welding Steel vs Aluminum
When welding steel vs aluminum, it’s important to remember that the two metals have different characteristics. That means that choosing the right welding process is essential for successful. The key to welding both steel and aluminum successfully is to use the right welding processes for each type of metal. That way, you can get the best results when welding these materials. As you can see, there are many factors that affect your welding results. Learning how to weld steel vs aluminum properly is essential for successful welding.