Welding mild steel to cast iron can be a challenge part for many welders. However, with a little bit of research and practice, it can be easier than you think. This article will explain the challenges that you may face and how you can overcome them. One of the most common types of welding used in industry today is called tube welding. It’s generally used for joining two pieces of metal together when they are both inside a pipe. For example, if you had an oil pipeline that needed to be securely fastened together, it would be sealed inside another pipe.
The first thing that you need to know when working with this type of welding is that there are different types of steel and cast iron. Keep reading to learn more about these challenges and tips to help you succeed.
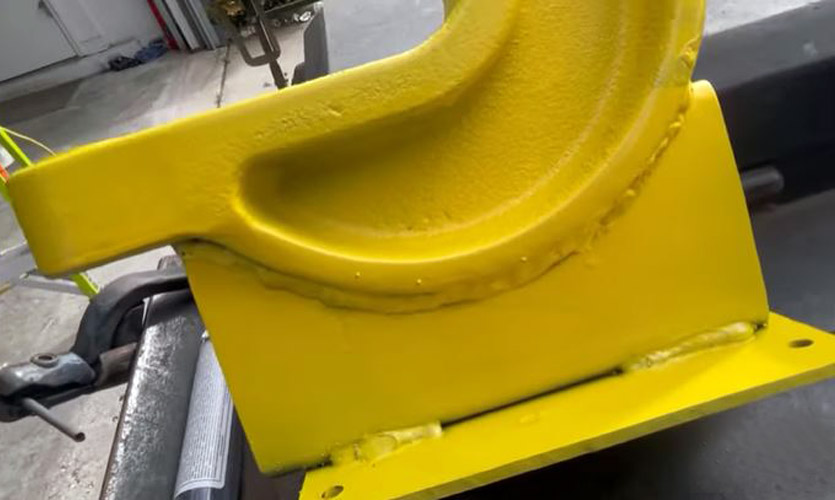
Photo by MeltinMetalAnthony on YT
Difference between welded steel and cast iron
In this type of welding, the base material is usually welded steel that has been specially treated to be compatible with cast iron. This is the most common type of welding used to join cast iron to mild steel and other types of steel. It’s important to remember the difference between welded steel and cast iron. Cast iron is a type of iron that’s been used for hundreds of years.
It’s also known as ductile iron because it’s relatively malleable and ductile, which means it can be formed into a wide range of objects. Welded steel is a type of steel that’s been specially treated to be welded to cast iron.
What are the Challenges for Welding Mild Steel to Cast Iron?
Joint Penetration: The most common challenge that you will face when welding mild steel to cast iron is joint penetration. This is when one weld enters another piece of metal and it doesn’t go all the way through to the other side. This can happen to both the joints inside the pipe or joint surfaces that are touching each other. If you are having trouble with joint penetration, try welding with a higher gas voltage and a smaller electrode diameter. You can also try welding at a higher pressure. It’s also important to remember that the joint penetration depth is different for different types of steel.
Welding Gas Composition: When considering how to weld steel to cast iron, you first need to understand about the two types of welding gases that can be used to weld mild steel to cast iron: tungsten-free (TF) and tungsten-containing (WC). The main difference between these welding gases is the amount of tungsten they contain. The Welding gas composition is also different between mild steel and cast iron, which is why you need to choose the correct welding gas for your welding application. It’s important to find out as soon as possible which welding gas you should use for this type of welding.
Filler Metal Temperature: Another challenge that you may face is the correct welding filler metal temperature for welding cast iron to mild steel. Welding filler metal is the material that’s used to fill in the welds and prevent corrosion. Welding filler metal for mild steel to cast iron welding has to be slightly hotter than the base material. The correct welding filler metal temperature for mild steel to cast iron welding is around 1000°F.
Arc Frequency: The last welding challenge that you will face while welding mild steel to cast iron is the correct welding arc frequency. The welding arc frequency is the speed at which the welding electric current flows between the welding electrode and the welding metal. The welding arc frequency has to be set accordingly to the type of metal that you are welding.
Welding Equipment for MIG and Tig Welding
Vacuum pump: This gas welding machine is used to create a low-pressure environment inside of the weld joint. This is the ideal environment for mild steel to cast iron welding, because it keeps the filler metal cool and prevents it from being attacked by oxygen.
Gas bottle: Some welding gases for mild steel to cast iron welding are to be stored in a gas bottle. You can also use a gas bottle if you’re using a MIG welder.
Welding gun: For MIG welding, you will need a welding gun that uses a small wire electrode. The welding gun has different voltage settings to create different weld sizes.
Mig shield: A mig shield protects the welding operator from the spatter that’s created when welding mild steel to cast iron.
Welding Process for Steel to Cast Iron
Here’s a helpful step-by-step guide of how to weld steel to cast iron:
Prepare the Welding Joint: Make sure that the welding joint is clean and free of all debris. This will help prevent the weld joint from getting clogged up with slag or oxides.
Clean Weld Joint: After the welding joint has been cleaned, it should be cooled down to around 600°F. If you’re using a MIG welder, the welding joint should be slightly warmer.
Bed Preparation: In this step, the welding joint must be heated to around 1100°F. The welding joint should be kept heated for about five minutes after which it should be cooled down to below 600°F. This is the correct and ideal beam-width for mild steel to cast iron welding.
MIG Arc: In this welding step, the welding joint should be kept at a constant current of between 30 and 50 amps. The correct current should cover the entire weld joint area.
Tig Arc: The welding joint should be kept at the same current as the MIG arc. The welding joint should be heated to around 1300°F.
Tungsten Inert Gas (TIG) Welders
TIG welders are often the first choice for welders who are new to welding mild steel to cast iron. A tungsten inert gas (TIG) welder produces a pure arc light that’s free of the dangers and hazards of an arc welding. A tungsten inert gas weld uses tungsten as an electrode to produce a pure arc. It’s completely inert, which means that it doesn’t produce any gas. TIG welding is mostly used for metals that have a relatively high melting point.
A tungsten inert gas weld is considered as a clean weld because there is no gas present in it. But it’s not considered as a strong weld as it’s only capable of holding about 3/4 of an ounce. A pure arc weld can only be used for joining mild steel to cast iron because it has a low resistance and does not form a good joint with cast iron.
Plasma Arc Welders
If you want to weld steel to cast iron without the problems associated with welding mild steel to cast iron, then you should try plasma arc welding. Plasma welding is a type of welding that uses a gas such as tungsten or inert gas. The arc is generated by an electrical current between the electrodes and a solid source of gas. The arc is a self-sustaining process that produces a hot, ionized gas that’s used to vaporize the weld joint and molten pool as it’s being welded.
Plasma welding has a high oxygen content, which means that it creates a large amount of gas when it’s being welded. Plasma arc welding is fast, produces a high amount of gas, and is considered to be one of the best welding methods for steel to cast iron.
What Welding Process Should You Use?
The main thing to remember when you’re working with mild steel to cast iron is that the weld joint penetration should be at least 0.04 in. Another important factor is that the welding filler metal must be kept at a temperature of 900°F. These are the best practices that you should remember when welding steel to cast iron. If you want to weld steel to cast iron but don’t want to deal with the challenges that come with it, then you should try Tig welder. Tig welders produce a high current that’s capable of penetrating through a joint. This weld technique is ideal for welding steel to cast iron because it creates a strong joint that holds up against corrosion.
Tips to Make Welding Mild Steel to Cast Iron Easier
Welding mild steel to cast iron can be a challenging task due to the differences in their composition and melting points. Here are some tips to help you make a successful weld:
- Preheat the cast iron before welding to reduce the risk of cracking. Heat the cast iron to about 500-600°F using a torch or furnace.
- Use a nickel-based electrode or filler material for welding. Nickel can handle the thermal expansion and contraction that occurs during welding.
- Clean the surfaces of both metals thoroughly before welding. Use a wire brush or grinder to remove rust, dirt, and other contaminants.
- Use a low amperage setting to avoid overheating the cast iron. Work in short intervals to allow the cast iron to cool down.
- Use a peening hammer to relieve stress in the weld and prevent cracking.
- After welding, allow the metal to cool slowly to avoid thermal shock. A slow cool-down will also help to reduce the risk of cracking.
Welding mild steel to cast iron requires skill and experience. If you are unsure about your abilities, it is best to seek the help of a professional welder.
Challenging part of welding mild steel to cast iron
Welding mild steel to cast iron can be a challenging part due to the differences in their composition. However, with proper preparation and technique, a successful weld can be achieved. Preheating the cast iron, using a nickel-based electrode or filler material, cleaning the surfaces, using a low amperage setting, and allowing for a slow cool-down are all essential steps in making a strong and durable weld. I
t is important to note that welding requires skill and experience, and if you are unsure about your abilities, it is best to seek the help of a professional welder. With the right tools and knowledge, welding cast iron to mild steel can be a rewarding and fulfilling task.