Low carbon steel is one of the most commonly used steels for construction applications. The downside to using it so often is that it’s not as easy to weld as higher carbon content steels. That being said, welding low carbon steel can be done and there are a few factors you need to keep in mind if you want to do it successfully. In this article, we will discuss some aspects of welding low carbon steel which you should keep in mind before attempting to weld these materials.
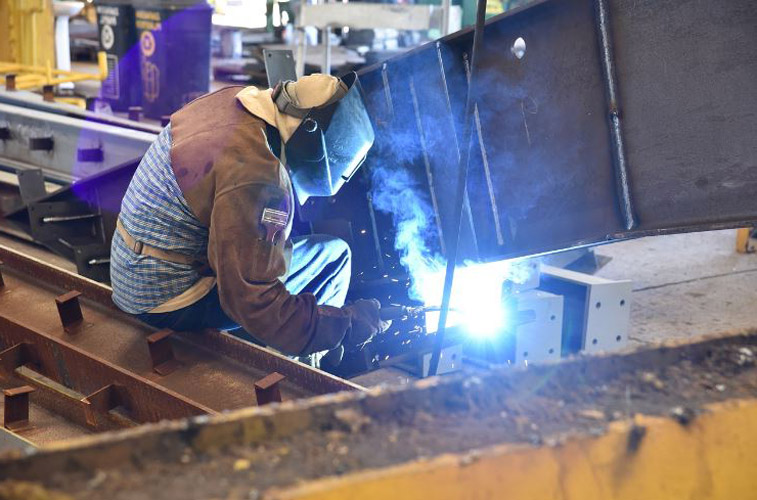
Photo by alcangel144, pixabay
What is low carbon steel?
Low carbon steels are classified as a type of carbon steel. These types of steels are often used in construction and engineering applications because they don’t require high levels of heat or cooling for welding to take place. Like their high carbon content cousins, low carbon steels are susceptible to oxidation and corrosion if not maintained.
Low carbon steels are made up of the following chemical makeup: Iron – 0.24% carbon – 0.09% Manganese – 0.050% Chromium – 0.035% Sulfur – 0.020% Oxygen – 0.008% Metallic Iron is produced in a low carbon state by reducing the iron to basic iron with carbon. The remaining impurities are removed. Next, carbon is added to increase the carbon content to a level that the steel can be used to produce a desired product
Why need to weld low carbon steel?
Weld low carbon steels also offers a couple of other advantages over higher carbon steels:
Lower Costs – A low carbon content steel like 3003 is usually much cheaper than using high carbon content steels like 1018. This is because a higher carbon content requires more expensive manufacturing processes and that increases costs. Low carbon steels are often produced using older, cheaper processes that have been used for decades. As a result, they are much cheaper than high carbon steels in comparison.
Low Carbon Contamination Risk – Since low carbon steels don’t require as high a carbon content level for production, there is a higher chance that the material will be produced using less controlled processes. This increases the risk of exposure to carbon contamination, especially if the steel is being produced in a less controlled environment. This makes it important to weld low carbon steel inside a controlled climate.
Difference between Low Carbon Steel and High Carbon Steel
Chemical makeup of low carbon steel – Iron – 0.24% carbon – 0.09% Manganese – 0.050% Chromium – 0.035% Sulfur – 0.020% Oxygen – 0.008% Chemical makeup of High carbon steel – Iron – 0.92% carbon – 0.10% Manganese – 0.035% Sulfur – 0.030% Oxygen – 0.005% Wrought carbon steel is produced by heating iron and carbon, mixing them and then hammering them with water to produce ingots. Therefore, the carbon in wrought steel is less than 0.2%
Welding process of low carbon steel
Low carbon steels are often used in construction and engineering applications because they don’t require high levels of heat or cooling for welding to take place. Welding low carbon steel also offers a couple of other advantages over higher carbon steels:
Welding Low Carbon Steel – Low carbon steels are weldable but they need to be heated and cooled at a lower temperature to prevent them from rusting. To perform a successful weld, the correct electrodes must be used, the correct shielding gas and the correct arc must be used. More importantly, the operator must have the correct knowledge and skills to perform a successful weld with low carbon steels.
Low carbon steels are weldable but they need to be heated and cooled at a lower temperature to prevent them from rusting. To perform a successful weld, the correct electrodes must be used, the correct shielding gas and the correct arc must be used. More importantly, the operator must have the correct knowledge and skills to perform a successful weld with low carbon steels.
Shielding is required to protect the operator from the possible hazards associated with the welding process. Gas shielding provides a layer of gas between the electrode and the weld pool to prevent the arc from being transmitted to the operator’s face Shielding gas helps to prevent arc shock to the operator and reduces welding slag generation Low carbon steels require less current and more arc voltage than high carbon steels.
Troubleshooting of Weld Low Carbon Steel
Low carbon steels are often used in construction and engineering applications because they don’t require high levels of heat or cooling for welding to take place. Welding low carbon steels also offers a couple of advantages over higher carbon steels: Shielding gas is required to prevent the arc from being transmitted to the operator’s face Arc voltage must be adjusted for low carbon steels Low carbon steels require less current and more arc voltage than high carbon steels Shielding gas may need to be adjusted during welding.
Safety while welding low carbon steel
Low carbon steels are often used in construction and engineering applications because they don’t require high levels of heat or cooling for welding to take place. The safety while welding low carbon steel is important to consider. Welding is an inherently dangerous activity. Proper planning, training, and work practices can help minimize risks, but there is no way to ensure complete safety. The best anyone can do is practice safe practices, stay alert, and don’t be afraid to get help if you need it.
Last word about welding low carbon steel
Shielding gas must be adjusted during welding carbon steels require less welding penetration than high carbon steels. The things to consider while welding low carbon steel are low carbon content, welding time, and welding equipment. Low carbon steel is a type of carbon steel which has a lower carbon content than high carbon steels.