Welding high carbon steel is rarely a straightforward process. It requires skill, practice, and knowledge of what works best for you and your project. If you’re new to welding high carbon steel or need a refresher on the topic, this article is for you. Read on to learn everything you need to know about welding high carbon steel including its advantages and disadvantages, types of welds, tips for successful projects, equipment recommendations, and more.
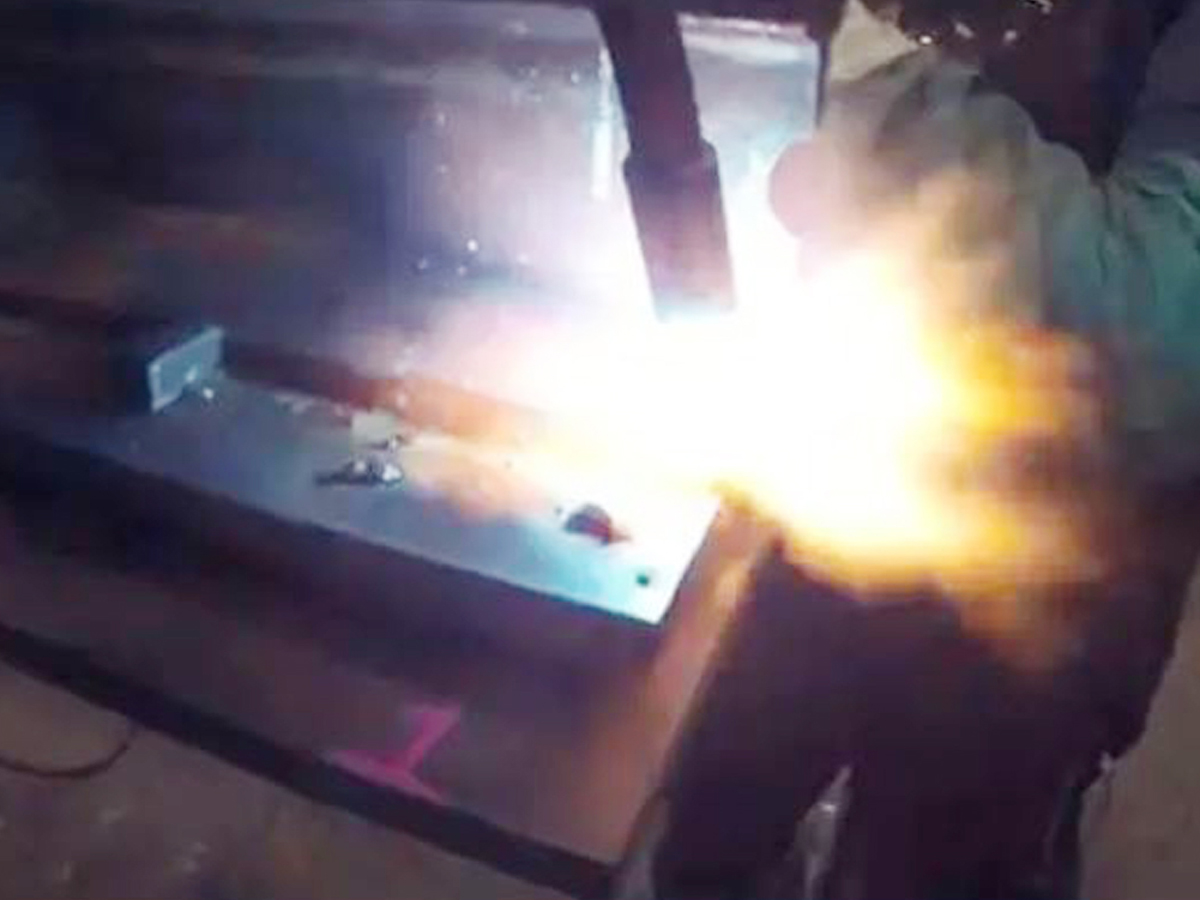
Photo by outdoorsoforegon3192
Definition of Welding
Welding means two different types of metal come together to form one continuous weld. One of the welded metals is called the weld metal, and the other is called the base metal. The weld metal is usually made of aluminum, steel, or another similar metal, and the base metal is often iron, carbon steel, or another high carbon alloy.
High-carbon steel is a type of alloy that contains more than 5% carbon. This type of steel is extremely versatile and has become a popular choice for welders because it can be welded with a wide range of welder settings and has many useful applications.
Differences Between Carbon Steel and High Carbon Steel
When welding carbon steel, you will also run into a few other common welding terms worth understanding. These include:
Welding/Welding Stick/Gas Stick – The welding equipment you will be using to weld. This could be a stick, gas stick, or other type of welder depending on your welding needs and preferences.
Flux Core – A piece of equipment that is used before the welding process to clean the weld area. Some welders will re-use the flux core, but others have a separate bottle that they keep for each project. Your preference will likely depend on your welding needs and preferences.
Torch Stick – The welding torch that you will use to weld high carbon steel.
Materials for Welding High Carbon Steel
It’s important to note that regardless of the type of high-carbon steel you choose, the welded joint will enable the two pieces of metal to become one. So the two most important factors for welding any type of high carbon steel are the carbon content and the type of welding process you use. And depending on your welding needs, you may also need to consider other factors like the weld joint thickness, joint type, joint location, and joint geometry. All of these things play a role in the high quality welded joint you will be left with.
High carbon steels with a carbon content of over 5% may be welded with either gas or arc welding processes. Welded joints can be made using either butt or combination joints. And depending on your welding needs, you may also be able to choose between a wide range of joint types including channels, channels with fillets, seamless joints, and groove welds.
Essential Equipment for Welding High Carbon Steel
The first thing you will need to get started welding high carbon steel is a suitable welding equipment set. Depending on your welder type and requirements, you may need a gas stick, gas welder, stick welder, oxy-acetylene welder, or another type of equipment. Your welding set should include a welding torch, electrode, and either a carbide or ceramic rod electrode. A torch with a side handle is usually suitable, but a torch with a hand held or automatic torch is commonly recommended.
Regardless of your welder type, it’s also important to have a good pair of welding gloves on hand. Welding gloves are designed to protect your hands from the heat and flame of your torch, and also help to prevent burns from the electrode and reduce the mess you will be making during your project.
Why need to Weld High Carbon Steel
High carbon steels are a popular choice for welding because they are easy to weld, have a wide range of applications, and are affordable. High carbon steels with a carbon content of over 5% are the most common, but there are also other types of high carbon steel that are suitable for welding. High carbon steels can be welded using either gas or arc welding processes.
Weld joint types include butt, combination , and channels. And depending on your welding needs, you may also be able to choose between a wide range of joint types including channels with fillets, seamless joint, groove welds, and more.
How to Weld High Carbon Steel
Whether you’re welding high-carbon steel with a gas or an arc welder, you’ll start by prepping the base metal. This involves cleaning the surface and removing any scale, rust, or other impurities that could interfere with the welding process. Once the base metal is ready, you can get to work welding. This includes making sure the torch tip is properly adjusted, the electrode is correctly positioned, and the gas or gas mixture is at the correct level.
You can also make sure your glove-to-torch connections are tight and your gloves are properly fitted. Depending on your welder type and settings, you may also want to make sure your shielding is tight and your weld area is properly shielded. After you are done welding, you can clean the weld area, inspect it for defects, and shut off your equipment.
Tips for Successful Welding
Make sure the joint is properly cut and ground. This ensures the base metal is fully supported by the weld metal, and the welded joint is of high quality. Make sure your welding joints are clean. This includes making sure the weld joint is free of impurities, has a smooth finish, and is properly shielded. Make sure your torch tip is properly adjusted. This includes making sure the torch tip is properly adjusted, the joint heats up properly, and the torch tip is properly shielded.
Be mindful of the welding current and weld metal thickness. These should be at the correct levels for your welding type and project. Keep your welding glove on for the entire weld process. This includes shielding and cooling down between welding joints.
Advantages of Welding High Carbon Steel
High quality welded joints. Welded joints made from high-carbon steel can withstand a lot of stress, which makes them a popular choice for corrosion-free joints. Wide range of applications. High carbon steels can be welded using gas or arc welding processes, and can be welded using a wide range of joint types. Affordable. High-carbon steels are a relatively cheap metal, making them an affordable option for all types of projects.
Disadvantages of Welding High Carbon Steel
Not for everyone. High carbon steels have one major drawback they require more welding experience and skill to weld successfully. This means they are not recommended for beginners. High carbon steels require more work. High-carbon steels are also more difficult to weld because they require more welding practice and skill, so they may take longer to complete projects. Acidic environments. High carbon steels are also more susceptible to corrosion in acidic environments because of their high carbon content.
High carbon steels can corrode faster and be more expensive to repair in these environments. High-carbon steels are more difficult to weld. High carbon steels are more difficult to weld because they require more welding practice and skill, so they may take longer to complete projects.
Type of Welder You Need to Use
If you are new to weld high carbon steel, a gas stick is a good choice. Gas stick welders are easy to use and don’t require a license. If you are ready to take the next step and welding carbon steel, consider investing in a high quality stick welder. High-quality welders are designed for welding high carbon steel, so you will have an easier time working with these high-quality welders without experience.
Last word about Welding Carbon Steel
When welding carbon steel, the most important thing is to know the right way to do it. The right equipment, welding technique, and safety precautions will optimize the quality of the weld and help ensure a successful project. If you are still unsure about welding high carbon steels, take advantage of the welded joints that other welder have successfully made and use them as a starting point rather than starting from scratch.