Welding is a complex and skillful process that requires precision and expertise. However, even the most experienced welders can encounter an issue called burn through. Burn through can lead to weakened welds, structural damage, and even accidents, making it crucial to understand its causes and prevention.
In this article, we will delve into the common causes of welding burn through and explore effective prevention strategies. From excessive heat input to improper technique, we will analyze the factors that contribute to burn through and provide practical solutions to avoid it.
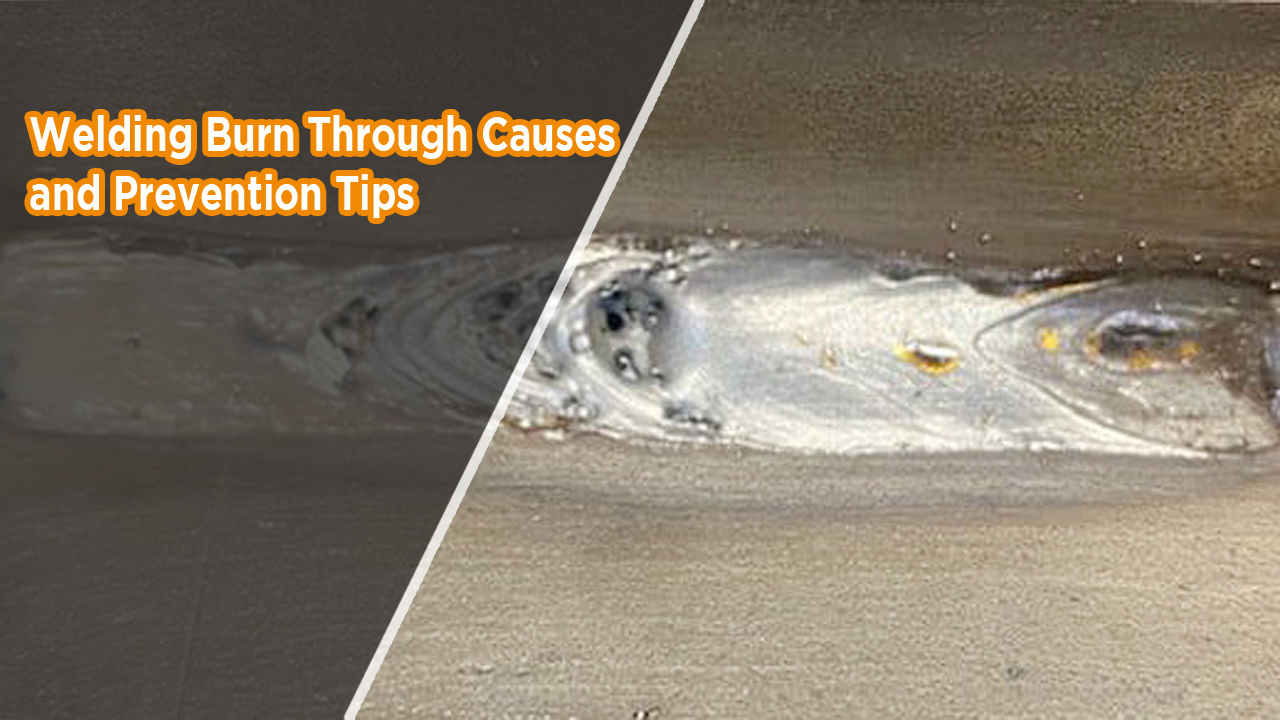
Image by hobartbrothers
Whether you’re a seasoned welder looking to enhance your skills or a beginner seeking to avoid costly mistakes, this article will offer valuable insights. By understanding the root causes of welding burn through and implementing preventative measures, you can ensure the integrity of your welds and create strong and durable structures.
What is welding burn through?
Welding burn through refers to the complete penetration of the base material during the welding process, resulting in a hole or excessive melting. It occurs when the heat input is too high or when the welding technique is incorrect. Burn through can weaken the weld, compromise the structural integrity of the workpiece, and may lead to leaks or other failures.
Common causes of welding burn through
Excessive heat input: One of the primary causes of burn through is excessive heat input during the welding process. This occurs when the heat generated by the welding arc is too high for the base material, causing it to melt and penetrate completely. It is crucial to strike a balance between heat input and the material’s heat resistance to prevent burn through.
Improper technique: Using improper welding techniques can also lead to burn through. This includes using incorrect travel speed, improper electrode angle, or inconsistent arc length. These errors can result in excessive heat concentration in a specific area, leading to burn through.
Insufficient joint preparation: Inadequate joint preparation can contribute to burn through. When the edges of the joint are not properly cleaned, beveled, or aligned, it can lead to uneven heat distribution during welding. This uneven distribution can cause localized overheating and subsequent burn through.
Now that we understand the causes of welding burn through, let’s examine the impact it can have on the welding process and the importance of prevention.
Impact of welding burn through on the welding process
Welding burn through can have severe consequences on the overall welding process and the quality of the weld. When burn through occurs, the structural integrity of the workpiece is compromised, making it susceptible to failures and leaks. Burn through also weakens the weld, reducing its strength and durability.
Furthermore, repairing burn through can be time-consuming and costly. It often requires removing the damaged section, re-preparing the joint, and re-welding the area. This not only adds to the project’s timeline but also increases material and labor costs.
To avoid these issues, it is essential to employ effective prevention strategies. Let’s explore some welding techniques that can help prevent burn through.
Welding techniques to prevent burn through
Controlled heat input: Proper control of heat input is crucial in preventing burn through. Adjusting the welding parameters, such as current, voltage, and travel speed, can help achieve the ideal heat input for the specific material being welded. Maintaining a consistent heat input throughout the weld helps prevent excessive melting and burn through.
Proper technique: Using the correct welding technique is vital in avoiding burn through. This includes maintaining the appropriate electrode angle, keeping a consistent arc length, and ensuring proper travel speed. Following the recommended techniques for the specific welding process and material helps distribute heat evenly, minimizing the risk of burn through.
Avoiding excessive weaving: Excessive weaving or zigzag motion during welding can increase heat concentration in a particular area, leading to burn through. Using a steady and controlled weaving technique, or even avoiding weaving altogether, can help prevent burn through and create a more uniform weld.
Now that we’ve covered welding techniques, let’s discuss the importance of choosing the right welding parameters to prevent burn through.
Choosing the right welding parameters to avoid burn through
Selecting the appropriate welding parameters is crucial in preventing burn through. These parameters include current, voltage, travel speed, and electrode size. Each parameter plays a significant role in controlling the heat input during welding.
For example, reducing the current and voltage can help reduce the heat input, minimizing the risk of burn through. Similarly, adjusting the travel speed can control the amount of heat applied to the workpiece, preventing excessive penetration.
It is essential to refer to the welding procedure specifications (WPS) provided by the manufacturer or consult industry standards to determine the optimal welding parameters for specific materials and joint configurations.
Importance of proper joint preparation in preventing burn through
Proper joint preparation is a critical step in preventing burn through during welding. It ensures that the edges of the joint are clean, beveled, and aligned correctly, allowing for even heat distribution.
Cleaning the joint surfaces removes any contaminants, such as rust, oil, or paint, that could interfere with the welding process. Beveling the edges creates a wider weld area, reducing the risk of excessive heat concentration. Aligning the joint properly ensures that the heat is evenly distributed across the entire joint, minimizing the likelihood of burn through.
Investing time and effort in joint preparation can significantly contribute to preventing burn through and improving the quality of the weld.
Using back purging to prevent burn through in pipe welding
In pipe welding, burn through can be a common issue due to the confined space and the potential for inadequate shielding gas coverage. Back purging is a technique used to prevent burn through and ensure the integrity of the weld in pipe welding.
Back purging involves supplying an inert gas, such as argon, into the pipe’s interior to displace oxygen and other contaminants. This creates a controlled and oxygen-free environment, reducing the risk of burn through and improving the overall quality of the weld.
By implementing back purging techniques, welders can prevent burn through and create strong and durable pipe welds.
Welding materials and their susceptibility to burn through
Different materials have varying susceptibility to burn through during the welding process. For example, materials with higher thermal conductivity, such as aluminum, are more prone to burn through compared to steel or stainless steel.
Understanding the material being welded and its specific characteristics is crucial in preventing burn through. It allows welders to adjust their welding techniques, parameters, and joint preparation methods accordingly to minimize the risk of burn through.
Importance of monitoring heat input to prevent burn through
Monitoring heat input during the welding process is essential in preventing burn through. Heat input refers to the amount of energy transferred to the workpiece per unit length of weld. Excessive heat input can lead to burn through, while insufficient heat input may result in incomplete penetration and weak welds.
Using heat input monitoring devices, such as pyrometers or infrared thermometers, can help ensure that the heat input remains within the desired range. By closely monitoring the heat input, welders can make real-time adjustments to prevent burn through and maintain the quality of the weld.
Ensuring quality welds by preventing burn through
Welding burn through can have detrimental effects on the integrity and strength of welds. Understanding the causes of burn through and implementing effective prevention strategies is essential for welders to create strong and durable structures.
By controlling heat input, using proper welding techniques, preparing joints correctly, and selecting the appropriate welding parameters, welders can significantly reduce the risk of burn through. Monitoring heat input and considering the material’s susceptibility to burn through further enhances the weld quality.
As a welder, it is crucial to continuously strive for excellence by improving your skills and knowledge. By mastering the art of avoiding burn through in welding, you can ensure the integrity of your welds and contribute to the creation of safe and reliable structures.