Welding aluminum with a stick welder is challenging due to aluminum’s properties. Special techniques and electrodes are needed for success.
Aluminum’s high thermal conductivity and oxide layer make welding difficult. Stick welding, also known as Shielded Metal Arc Welding (SMAW), is generally used for steel and iron. Welding aluminum requires specific electrodes, often with a flux coating to protect against oxidation.
Proper preparation includes cleaning the aluminum surface thoroughly to remove the oxide layer. A high-amperage welder is essential to maintain the necessary heat. Preheating the aluminum can also improve results. Practice and patience are crucial for mastering the technique. Understanding these aspects helps achieve strong, reliable welds on aluminum using a stick welder.
Introduction To Aluminum Welding
Welding aluminum can be a rewarding skill. Aluminum is a versatile metal used in many applications. Its lightweight and strong properties make it a popular choice.
Using a stick welder for aluminum has unique challenges. It requires specific techniques and equipment. But with practice, anyone can master it.
Why Choose Aluminum
Aluminum is lightweight and corrosion-resistant. It is ideal for construction, automotive, and aerospace industries. Here are some key benefits:
- High Strength-to-Weight Ratio: Aluminum is strong but light.
- Corrosion Resistance: It doesn’t rust like steel.
- Recyclable: Aluminum is eco-friendly and reusable.
Challenges In Aluminum Welding
Welding aluminum with a stick welder has challenges. The material’s properties make it tricky. Below are some common issues:
- Oxidation: Aluminum forms an oxide layer quickly.
- Heat Control: Aluminum absorbs heat fast, causing warping.
- Porosity: Impurities can create pores in the weld.
To overcome these, use proper techniques and tools. Preheat the metal to reduce warping. Use a wire brush to clean the oxide layer.
Essential Tools And Equipment
Welding aluminum with a stick welder requires specific tools and equipment. These ensure a smooth and safe welding process. Using the right tools and safety gear is crucial.
Choosing The Right Stick Welder
Choosing the right stick welder is crucial for welding aluminum. Look for a welder that provides enough amperage. Aluminum welding needs higher heat. A welder with adjustable settings is ideal.
Consider the duty cycle of the welder. A higher duty cycle allows longer welding periods. Inverter welders are a good choice. They are lightweight and efficient.
Welding rods are also important. Use aluminum-specific rods. These provide better results and a cleaner weld.
Protective Gear And Safety
Safety is paramount in welding. Protective gear is essential. Wear a welding helmet with a proper shade. This protects your eyes from the bright arc.
Use welding gloves to protect your hands. They should be heat-resistant and provide a good grip. A welding jacket is also important. It protects your body from sparks and heat.
Ensure proper ventilation in your workspace. Aluminum welding produces fumes. Use a respirator if needed. Keep a fire extinguisher nearby. Safety first!
Tool/Equipment | Purpose |
---|---|
Stick Welder | Provides the necessary heat for welding aluminum. |
Welding Rods | Specific for aluminum, ensuring better welds. |
Welding Helmet | Protects eyes from arc light. |
Welding Gloves | Protects hands from heat and sparks. |
Welding Jacket | Protects the body from heat and sparks. |
Respirator | Filters out harmful fumes. |
Fire Extinguisher | Ensures safety in case of fire. |
Preparing Aluminum For Welding
Welding aluminum with a stick welder requires proper preparation. This ensures strong and clean welds. The preparation process includes cleaning and degreasing and preheating the aluminum. Both steps are crucial for successful welding.
Cleaning And Degreasing
Aluminum needs to be clean before welding. Dirt, oil, and grease can ruin welds. Start by using a wire brush. Make sure the brush is stainless steel. This avoids contamination.
Next, use a degreaser. A clean rag can apply the degreaser. Wipe the aluminum thoroughly. Be sure to remove all residue. Clean aluminum welds better and prevents defects.
Tools | Purpose |
---|---|
Wire Brush (Stainless Steel) | Remove surface dirt |
Degreaser | Remove oil and grease |
Clean Rag | Apply and wipe degreaser |
Preheating The Aluminum
Preheating aluminum helps in welding. It reduces thermal shock. Preheat the aluminum to around 300°F. Use a propane torch for this task.
Check the temperature with a thermometer. Even heating is essential. Do not overheat the metal. Preheating ensures better weld quality and reduces cracking.
- Preheat to 300°F
- Use a propane torch
- Check temperature with a thermometer
Proper preparation of aluminum is key to successful welding. Cleaning, degreasing, and preheating are vital steps. Follow these steps for strong and clean welds.
Selecting The Right Electrodes
Welding aluminum with a stick welder can be tricky. The key to success is selecting the right electrodes. This choice will affect the quality of your weld. Let’s explore the types of electrodes for aluminum and the factors to consider.
Types Of Electrodes For Aluminum
There are various types of electrodes suitable for aluminum welding. Each type has unique properties and benefits.
Electrode Type | Characteristics |
---|---|
4043 | Good for general-purpose welding. Offers good strength and corrosion resistance. |
5356 | Higher strength. Better for welding thicker aluminum. |
4047 | Low melting point. Ideal for brazing and soldering. |
Factors To Consider
Several factors influence the choice of electrodes for aluminum welding. Here are the key considerations:
- Base Material: Match the electrode to the aluminum alloy.
- Joint Design: Consider the joint type and thickness.
- Welding Position: Different electrodes work better in specific positions.
- Power Source: Ensure compatibility with AC or DC welding machines.
- Cost: Balance quality and budget.
Mastering Welding Techniques
Welding aluminum with a stick welder is an art that requires precision and practice. Mastering the techniques ensures high-quality welds. Here, we will delve into two critical aspects: striking the arc and maintaining a steady hand.
Striking The Arc
Striking the arc is the first step. It’s essential for a smooth weld. Follow these steps for success:
- Prepare the Surface: Ensure the aluminum is clean.
- Set the Welder: Adjust the welder to the correct settings.
- Hold the Electrode: Position the electrode at a 15-degree angle.
- Strike Like a Match: Move the electrode swiftly to create the arc.
The table below highlights the key settings for different aluminum thicknesses:
Aluminum Thickness | Amperage Setting |
---|---|
1/8 inch | 80-100 amps |
1/4 inch | 120-140 amps |
1/2 inch | 160-200 amps |
Maintaining A Steady Hand
A steady hand is crucial for welding aluminum. It helps prevent defects. Here are some tips to maintain control:
- Grip Properly: Hold the electrode firmly but not too tight.
- Support Your Arm: Rest your arm on a stable surface.
- Move Smoothly: Use a consistent, smooth motion.
- Watch the Puddle: Keep an eye on the weld puddle. Adjust as needed.
These techniques will help you improve your welding skills. Practice regularly to achieve better results.
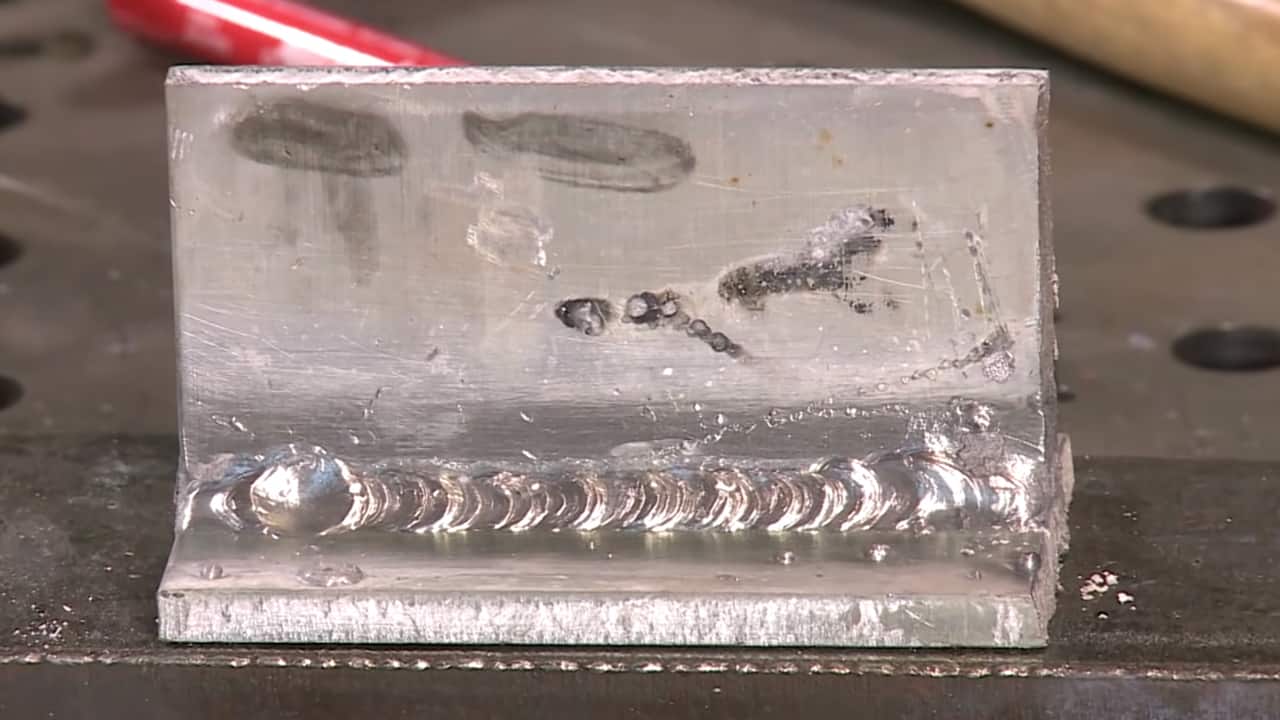
Credit: weldguru.com
Common Mistakes And Fixes
Welding aluminum with a stick welder can be tricky. Many beginners face common problems. Understanding and fixing these issues is crucial. This section will cover common mistakes and their solutions.
Avoiding Porosity
Porosity in welds weakens the structure. It occurs due to trapped gas bubbles. Follow these steps to avoid porosity:
- Clean the Aluminum: Remove all dirt and grease. Use a wire brush or grinder.
- Use Dry Electrodes: Moisture in electrodes causes porosity. Store them in a dry place.
- Proper Ventilation: Ensure good airflow to carry away fumes.
Keeping the surface clean and using dry electrodes helps. Proper ventilation also reduces porosity.
Preventing Cracks
Cracks in aluminum welds compromise strength. They often happen due to rapid cooling. Here are ways to prevent cracks:
- Preheat the Aluminum: Warm the metal to 300°F before welding.
- Slow Cooling: Allow the weld to cool gradually. Use a blanket or insulation.
- Proper Filler Rod: Choose a filler rod that matches the base metal.
Preheating and slow cooling are essential. Using the right filler rod also prevents cracks.
Post-welding Procedures
After welding aluminum with a stick welder, some steps ensure a strong, clean weld. These post-welding procedures help maintain the integrity and appearance of your weld. They include cleaning and inspecting the weld.
Cleaning The Weld
Cleaning the weld is crucial. Remove any slag and contaminants. Use a wire brush designed for aluminum. This helps in getting rid of any surface impurities.
For a more thorough clean, consider using a chemical cleaner. This ensures any oxides are removed. Always follow the manufacturer’s instructions for safe use.
Proper cleaning ensures a strong bond and enhances the weld’s appearance.
Inspecting For Defects
Inspecting the weld for defects is essential. Look for cracks, porosity, and other imperfections. These can weaken the weld.
Use a magnifying glass for a detailed inspection. Ensure there are no visible flaws. For critical applications, consider non-destructive testing methods like X-ray or ultrasonic testing.
Address any defects immediately. Grind out the defect and re-weld the area if necessary.
Advanced Tips From Experts
Welding aluminum with a stick welder can be challenging. Experts have shared advanced tips to improve your skills. These tips focus on improving weld quality and increasing efficiency.
Improving Weld Quality
Achieving high-quality aluminum welds requires precision and technique. Here are some expert tips:
- Clean the surface: Always clean aluminum before welding. Use a wire brush or chemical cleaner.
- Preheat the metal: Preheating reduces cracking. Aim for a temperature of 300°F.
- Use the right electrode: Choose an electrode designed for aluminum, such as E4043.
- Maintain proper arc length: Keep a short arc length to prevent contamination.
These steps ensure a strong, clean weld. Consistency is key. Practice these techniques regularly.
Increasing Efficiency
Efficiency in welding saves time and resources. Experts recommend the following:
- Optimize your settings: Adjust amperage and voltage for best performance.
- Use a backing strip: A copper backing strip helps control heat and prevent burn-through.
- Plan your welds: Organize your welding sequence to minimize repositioning.
- Invest in quality gear: High-quality welding machines and protective gear improve efficiency.
Implementing these tips will enhance your welding process. Efficiency leads to better results and higher productivity.
Tip | Description |
---|---|
Clean the surface | Removes contaminants that can weaken the weld. |
Preheat the metal | Reduces the risk of cracking. |
Use the right electrode | Ensures compatibility with aluminum. |
Maintain proper arc length | Prevents contamination and improves weld quality. |
Optimize your settings | Ensures the best performance from your welder. |
Use a backing strip | Helps control heat and prevents burn-through. |
Plan your welds | Minimizes time spent repositioning. |
Invest in quality gear | Improves safety and efficiency. |
Safety Precautions
Welding aluminum with a stick welder is a precise task. Ensuring safety is paramount to avoid accidents. Below are crucial safety measures to keep in mind.
Handling Aluminum Safely
Before starting, inspect the workspace. Ensure it is clean and dry. Remove any flammable materials.
- Wear protective gear. This includes gloves, helmet, and a fire-resistant jacket.
- Check your equipment. Ensure all tools are in good working condition.
- Secure the aluminum piece. Use clamps to hold it in place.
Safety Gear | Purpose |
---|---|
Helmet | Protects eyes and face from sparks |
Gloves | Protects hands from heat and metal splinters |
Fire-resistant jacket | Prevents burns from sparks |
Dealing With Fumes
Welding aluminum produces fumes that can be harmful. Proper ventilation is essential.
- Work in a well-ventilated area. Open windows and use exhaust fans.
- Wear a respirator. This helps filter out harmful particles.
- Install fume extractors. These devices remove fumes from the air.
Regular breaks are important. Step away from the workspace to breathe fresh air.
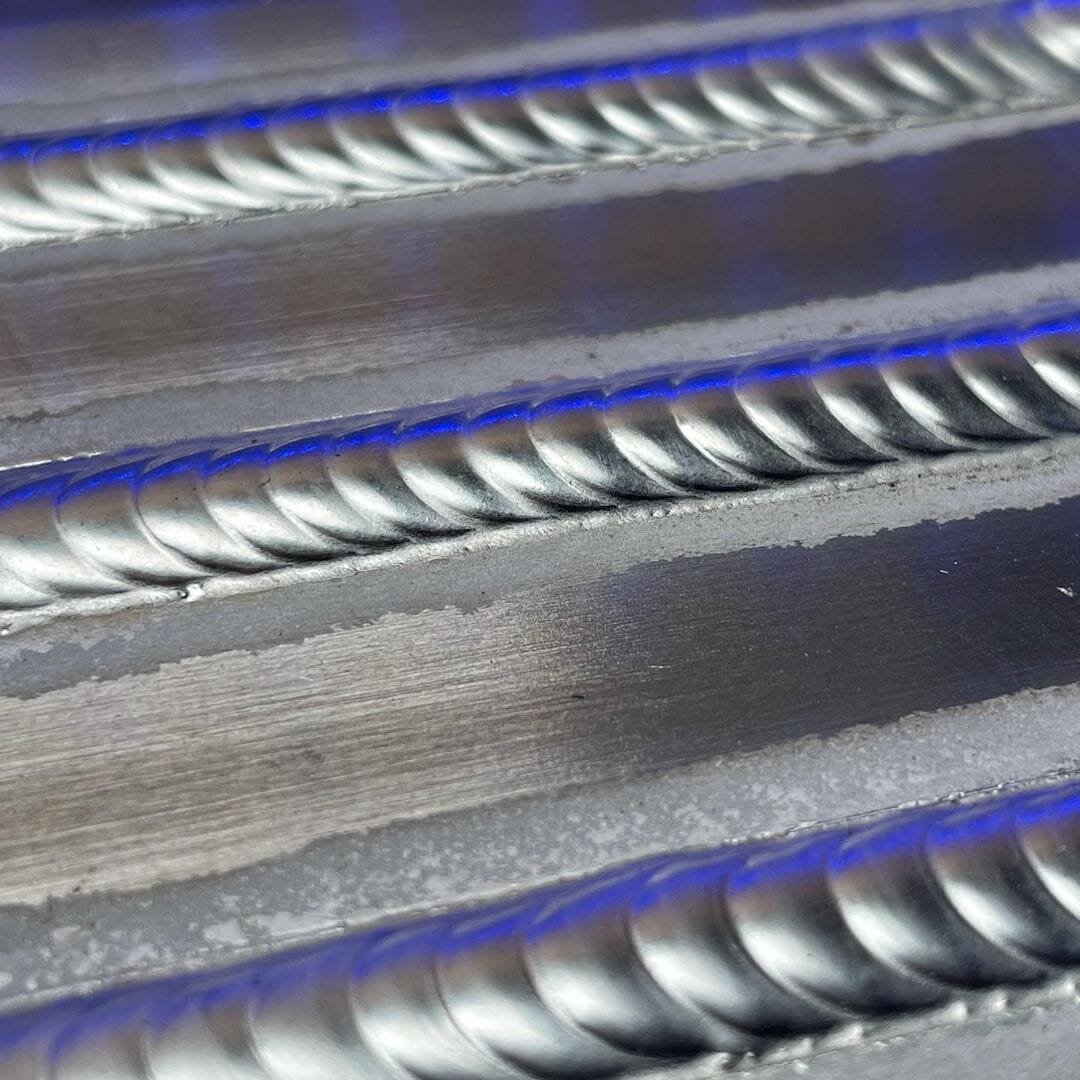
Credit: yeswelder.com
Conclusion And Next Steps
Welding aluminum with a stick welder is a valuable skill. Understanding the process and the equipment is crucial. This section will summarize key points and provide additional resources for further learning.
Recap Of Key Points
Let’s quickly review the most important points:
- Proper Preparation: Clean the aluminum surface thoroughly.
- Electrode Selection: Use a suitable electrode for aluminum.
- Correct Settings: Adjust your welder to the right settings.
- Technique: Maintain the right angle and speed during welding.
- Safety: Always wear protective gear while welding.
Further Learning Resources
Explore these resources to deepen your understanding:
Resource | Type | Link |
---|---|---|
Welding Forums | Community | WeldingWeb |
Online Courses | Course | Udemy |
Instructional Videos | Video | YouTube |
Books | Book | Amazon |
These resources will help you gain more confidence in welding aluminum with a stick welder. Continue practicing and learning to master this skill.
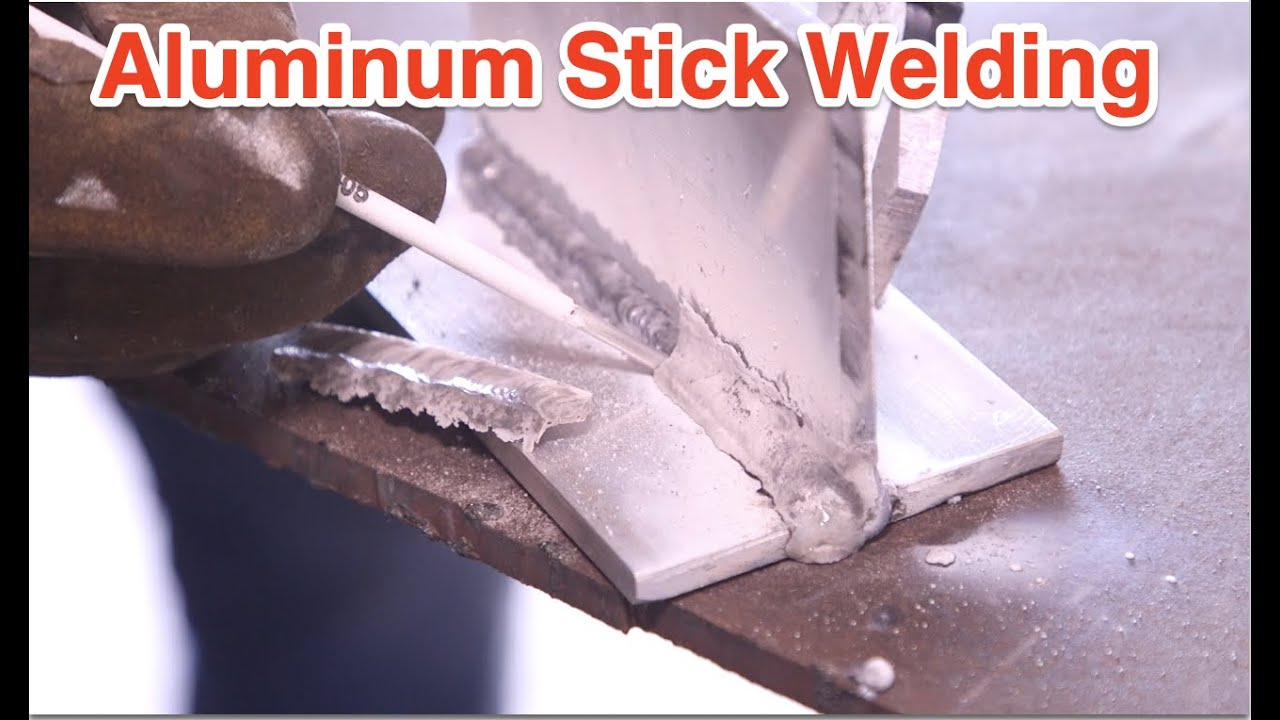
Credit: www.youtube.com
Frequently Asked Questions
Can You Weld Aluminum With A Stick Welder?
Yes, you can weld aluminum with a stick welder. However, it requires special electrodes and techniques. Ensure your welder supports AC output.
What Type Of Electrode Is Used For Aluminum?
For aluminum, use a special electrode known as E4043 or E5356. These electrodes are designed for welding aluminum and provide better results.
Do I Need Ac Or Dc For Welding Aluminum?
AC is preferred for welding aluminum. AC helps break the oxide layer on aluminum, making the welding process smoother.
Is Preheating Aluminum Necessary Before Welding?
Yes, preheating aluminum is often necessary. Preheat to around 300°F to 400°F. This helps prevent cracking and improves weld quality.
Conclusion
Mastering aluminum welding with a stick welder takes practice and patience. Utilize proper techniques for better results. Remember to prioritize safety and choose the right equipment. With dedication, you can achieve strong, durable welds. Keep experimenting and refining your skills.
Happy welding!