Trying to weld aluminum to aluminum? You are not alone. Many DIY enthusiasts and professionals alike have wondered whether this combination is possible. In this article, we will dive deep into the world of aluminum welding to answer this burning question once and for all.
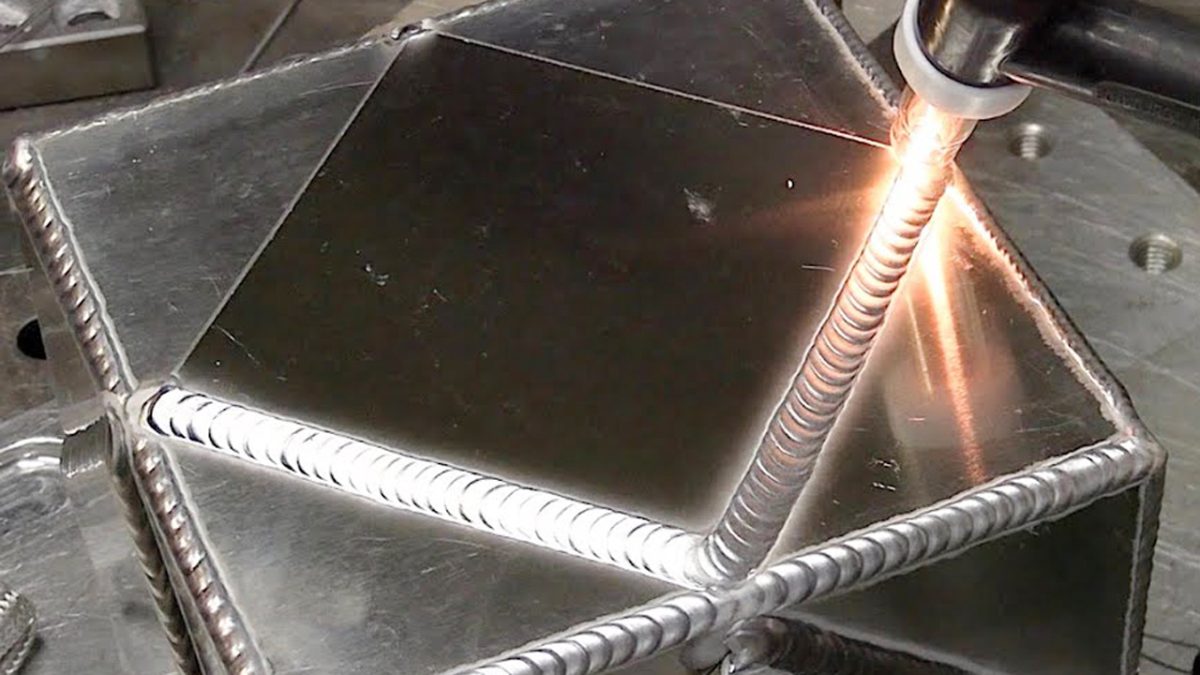
Image by weldingtipsandtricks
Understanding the Process of aluminum welding
Aluminum is a lightweight and highly versatile metal that’s widely used in various industries. Its excellent strength-to-weight ratio makes it an attractive choice for welding projects. However, welding aluminum to aluminum can be quite challenging due to its unique properties. Unlike other metals, aluminum has a lower melting point and high thermal conductivity, which can lead to several complications during the welding process.
When it comes to welding aluminum, it’s important to understand that aluminum oxide forms quickly when exposed to air. This oxide layer can hinder the formation of a strong weld. Therefore, proper cleaning and preparation of the aluminum surfaces are essential for successful welding.
The properties of aluminum that affect welding
Before we delve into the challenges of welding aluminum to aluminum, let’s take a look at some key properties of aluminum that directly impact the welding process. Understanding these properties will help you overcome the difficulties associated with aluminum welding.
Low melting point: Aluminum has a relatively low melting point compared to other metals, such as steel. This means that it requires careful control of heat to prevent the aluminum from melting too quickly and causing weak welds.
High thermal conductivity: Aluminum is an excellent conductor of heat, which means that heat dissipates quickly through the metal. This can make it challenging to maintain a stable welding temperature and can result in distortion or burn-through if not handled properly.
High thermal expansion: Aluminum expands significantly when heated, which can also contribute to distortion and warping during welding. Proper clamping and fixturing techniques are crucial to minimize these effects.
Oxidation: As mentioned earlier, aluminum rapidly forms an oxide layer when exposed to air. This oxide layer must be removed before welding to ensure proper fusion between the aluminum surfaces.
Common challenges of welding aluminum to aluminum
Welding aluminum to aluminum presents several challenges that require careful consideration and specialized techniques. Some of the main challenges include:
Aluminum oxide layer: The oxide layer that quickly forms on aluminum surfaces must be removed prior to welding. This can be done using various methods, such as mechanical cleaning, chemical cleaning, or using specialized aluminum cleaning solutions.
Heat control: As mentioned earlier, aluminum has a low melting point and high thermal conductivity. This means that heat control is crucial during the welding process. Too much heat can cause the aluminum to melt too quickly, leading to weak welds, while insufficient heat can result in incomplete fusion.
Distortion and warping: Due to its high thermal expansion, aluminum is prone to distortion and warping during the welding process. Proper clamping and fixturing techniques, as well as careful heat management, are essential to minimize these effects.
Fusion and penetration: Achieving proper fusion and penetration between the aluminum surfaces can be challenging due to the oxide layer and the metal’s low heat resistance. Specialized welding techniques and filler materials are often required to ensure strong and durable welds.
Techniques for welding aluminum to aluminum
Now that we understand the challenges associated with welding aluminum to aluminum, let’s explore some of the techniques that can be used to overcome these challenges and achieve successful welds.
TIG (Tungsten Inert Gas) welding
TIG welding is a popular choice for welding aluminum due to its precise heat control and ability to produce high-quality welds. In TIG welding, a non-consumable tungsten electrode is used to create an arc that melts the aluminum surfaces. A separate filler rod is then added to the weld pool to achieve proper fusion.
TIG welding allows for excellent control over the welding parameters, such as heat input and travel speed, which is crucial for welding aluminum. It also produces clean, aesthetically pleasing welds with minimal spatter.
MIG (Metal Inert Gas) welding
MIG welding is another common method used for aluminum welding. In MIG welding, a consumable wire electrode is fed through a welding gun, along with a shielding gas, typically argon or a mixture of argon and helium. The electric arc melts the wire and the aluminum surfaces, creating a weld pool. The shielding gas protects the weld pool from oxidation.
MIG welding is known for its speed and ease of use. It is often preferred for larger projects or when high productivity is required. However, it may not provide the same level of control and precision as TIG welding.
Preparing the aluminum surfaces for welding
Proper preparation of the aluminum surfaces is crucial for successful welding. Here are some steps to follow when preparing aluminum for welding:
- Cleaning: Remove any dirt, oil, grease, or other contaminants from the aluminum surfaces using a suitable cleaning method. Mechanical cleaning, such as sanding or wire brushing, can be effective for removing surface impurities. Chemical cleaning solutions specifically designed for aluminum can also be used.
- Removing the oxide layer: As mentioned earlier, the aluminum oxide layer must be removed prior to welding. This can be done using a stainless steel brush, a dedicated aluminum cleaning solution, or by using specialized aluminum cleaning equipment, such as a wire wheel.
- Fit-up and alignment: Ensure that the aluminum pieces to be welded are properly aligned and tightly fit together. Proper fit-up helps to achieve good fusion and penetration during the welding process.
- Clamping and fixturing: Use clamps or fixtures to hold the aluminum pieces in place during welding. This helps to prevent distortion and warping.
- Tack welding: Before fully welding the aluminum pieces, tack weld them at strategic points to hold them together. This ensures proper alignment and stability during the welding process.
Choosing the right welding method for aluminum to aluminum
When it comes to welding aluminum to aluminum, both TIG and MIG welding methods can be suitable options, depending on the specific requirements of your project. Here are some factors to consider when choosing the right welding method:
Precision and control: If you require precise control over the welding parameters and high-quality welds, TIG welding is the recommended choice. TIG welding allows for better control over heat input, travel speed, and filler material deposition.
Speed and productivity: If speed and productivity are the main factors, MIG welding may be more suitable. MIG welding is generally faster and easier to learn than TIG welding, making it a preferred choice for large-scale projects.
Material thickness: TIG welding is often preferred for thinner aluminum sheets or components, as it allows for better control over the heat input and minimizes the risk of burn-through. MIG welding can be suitable for thicker aluminum materials.
Skill level: Consider your skill level and experience with welding. TIG welding requires more skill and practice to master, while MIG welding is generally more forgiving and easier to learn.
Equipment and materials needed for aluminum welding
To weld aluminum to aluminum, you’ll need the following equipment and materials:
Welding machine: For TIG welding, you’ll need a TIG welding machine with AC (Alternating Current) capability. For MIG welding, a MIG welding machine with appropriate settings for aluminum welding is required.
Welding torch/gun: A TIG welding torch or MIG welding gun is needed for the actual welding process. Make sure the torch or gun is compatible with aluminum welding and can handle the required amperage.
Tungsten electrode: If you are using TIG welding, you will need tungsten electrodes with suitable alloy composition for aluminum welding. Thoriated or lanthanated tungsten electrodes are commonly used for aluminum welding.
Filler material: Depending on the welding method, you will need suitable filler materials for aluminum welding. Aluminum filler rods or wires are available in various alloys and diameters. Choose the appropriate filler material based on the specific application and requirements.
Shielding gas: For MIG welding, you’ll need a shielding gas, typically argon or a mixture of argon and helium, to protect the weld pool from oxidation.
Personal protective equipment (PPE): Always prioritize safety when welding. Wear appropriate PPE, including welding gloves, a welding helmet with a suitable shade, a welding jacket or apron, and safety glasses.
Safety precautions for aluminum welding
Welding aluminum requires following specific safety precautions to protect yourself and ensure a safe working environment. Here are some safety tips to keep in mind:
Ventilation: Ensure proper ventilation in the welding area to remove welding fumes and gases. Aluminum welding fumes can be harmful, so it’s important to work in a well-ventilated space or use exhaust fans or fume extractors.
Fire prevention: Aluminum dust and chips can be highly flammable. Keep the work area clean and free of flammable materials. Have a fire extinguisher nearby and be prepared to extinguish any potential fires.
Eye and skin protection: Wear appropriate PPE, including a welding helmet with a suitable shade, safety glasses, welding gloves, and a welding jacket or apron. Aluminum welding can produce intense ultraviolet (UV) radiation, so protect your eyes and skin from UV exposure.
Electrical safety: Ensure that the welding equipment is properly grounded and that all electrical connections are secure. Avoid touching the electrode or the workpiece while the welding machine is energized.
Training and certification: If you’re new to welding or aluminum welding specifically, consider taking a welding course or seeking guidance from an experienced welder. Proper training and certification can help ensure safe and successful aluminum welding.
Common mistakes to avoid when welding aluminum to aluminum
To achieve successful aluminum-to-aluminum welds, it’s important to avoid common mistakes that can compromise the quality and strength of the welds. Here are some common mistakes to watch out for:
Insufficient cleaning: Failing to properly clean the aluminum surfaces before welding can result in poor fusion and weak welds. Always remove any dirt, oil, grease, or oxide layer from the aluminum surfaces.
Incorrect heat control: Aluminum requires precise heat control during the welding process. Too much heat can cause the aluminum to melt too quickly, leading to weak welds, while insufficient heat can result in incomplete fusion. Maintain proper heat input and travel speed for optimal results.
Inadequate filler material selection: Choosing the wrong filler material or using an incorrect filler material can result in poor weld quality. Select the appropriate filler material based on the aluminum alloy and application.
Improper fit-up and alignment: Poor fit-up and alignment can lead to weak fusion and improper penetration. Ensure that the aluminum pieces are properly aligned and tightly fit together before welding.
Lack of proper shielding gas: In MIG welding, using an incorrect or insufficient shielding gas can result in oxidation of the weld pool and poor weld quality. Always use the appropriate shielding gas, typically argon or a mixture of argon and helium, to protect the weld pool.
Conclusion and final thoughts on welding aluminum to aluminum
Welding aluminum to aluminum is indeed possible with the right techniques, equipment, and materials. Aluminum’s unique properties, such as its low melting point and high thermal conductivity, present challenges that require careful consideration and specialized welding methods.
By understanding the properties of aluminum, the challenges of welding aluminum to aluminum, and the various welding techniques available, you can achieve strong and durable welds on aluminum surfaces. Proper cleaning and preparation of the aluminum surfaces, as well as careful heat control and filler material selection, are key to successful aluminum welding.
Whether you choose TIG welding for its precision and control or MIG welding for its speed and productivity, remember to prioritize safety and follow proper welding practices. With practice and experience, you can master the art of welding aluminum to aluminum and tackle a wide range of welding projects with confidence. Happy welding!