Are you struggling with aluminum welding and looking for ways to improve your welding efficiency and quality? Look no further than push-pull guns. These specialized welding guns provide a consistent and controlled wire feed for aluminum welding, resulting in smoother and more precise welds. Push-pull guns are designed specifically for aluminum welding and offer a range of benefits, including reduced spatter, improved arc stability, and increased welding speed.
In this article, we will explore the benefits of using push pull guns for aluminum welding and provide some tips for maximizing their effectiveness. Whether you are a seasoned welder or just starting out, incorporating push-pull guns into your welding process can help take your skills to the next level. Let’s dive in and discover how you can improve your aluminum welding with push pull guns.
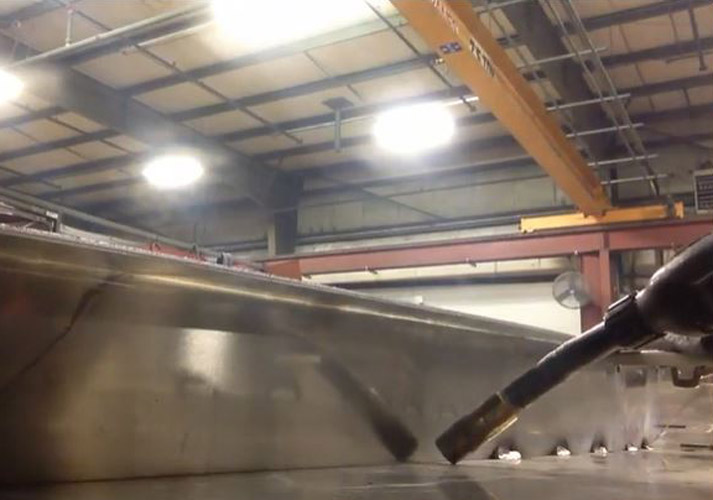
What are Push Pull Guns and How do They Work?
Push pull guns are a type of welding gun that provides a consistent and controlled wire feed for aluminum welding. They work by using a motorized mechanism to pull the wire through the gun, while a set of rollers push the wire out of the gun. This dual mechanism provides a more stable and consistent wire feed than traditional welding guns, which can help reduce spatter and improve weld quality.
Push pull guns are designed specifically for welding aluminum, which is a soft and malleable metal that requires a delicate touch. The motorized wire feed mechanism helps prevent the wire from jamming or buckling, which can cause problems with the welding process. Push pull guns are designed to work with softer, more flexible aluminum wire, which can be difficult to feed through traditional welding guns.
Benefits of Using Push Pull Guns for Aluminum Welding
There are several benefits to using push pull guns for aluminum welding. One of the main benefits is that they provide a more stable and consistent wire feed, which can help reduce spatter and improve weld quality. Additionally, push pull guns are designed specifically for welding aluminum, which means that they are optimized for the unique properties of the metal.
Another benefit of using push pull guns for aluminum welding is that they can increase welding speed. Because the wire is fed more consistently and smoothly, welders can work more quickly and efficiently. This can be especially helpful for larger welding projects, where speed is important.
Finally, push-pull guns can improve arc stability, which can help prevent problems like burn through or warping. The consistent wire feed helps maintain a stable arc, which can lead to smoother and more precise welds.
Types of Push Pull Guns for Welding Aluminum
There are several types of push pull guns for aluminum welding, each with its own set of features and benefits. One common type is the air-cooled push-pull gun, which is designed for low- to medium-amperage welding applications. These guns are typically lighter and more portable than their water-cooled counterparts, and they are ideal for welding in tight spaces or hard-to-reach areas.
Another type of push-pull gun is the water-cooled push-pull gun, which is designed for high-amperage welding applications. These guns use water to cool the gun and prevent overheating, which can be a concern with high-amperage welding. Water cooled push-pull guns are typically more durable and long-lasting than air-cooled guns, and they are better suited for heavy-duty welding applications.
Choosing the Right Push Pull Gun for Your Welding Project
When choosing a push pull gun for aluminum welding project, there are several factors to consider. One of the most important factors is the amperage of your welding machine. Push-pull guns are designed to work with specific amperage ranges, so it’s important to choose a gun that is compatible with your machine.
Another factor to consider is the length of the gun. Longer guns are better suited for welding in hard-to-reach areas or for larger welding projects, while shorter guns are more portable and easier to maneuver. You should consider the type of wire you will be using for your welding project. Push-pull guns are designed to work with softer, more flexible aluminum wire, so it’s important to choose a gun that is optimized for this type of wire.
Setting Up Push Pull Gun for Aluminum Welding
Once you have chosen the right push pull guns for aluminum welding application, it’s important to set it up properly for aluminum welding. This involves adjusting the tension on the wire feed rollers to ensure a consistent and controlled wire feed. To set up your push-pull gun, start by feeding the wire through the gun and adjusting the tension on the rollers until the wire feeds smoothly and consistently.
You may need to adjust the tension several times to find the right setting for your welding application. It’s also important to make sure that your welding machine is set up correctly for aluminum welding. This may involve adjusting the amperage, wire speed, and other settings to ensure a smooth and consistent weld.
Techniques for Using Pus Pull Guns
Once your push-pull gun is set up properly, it’s important to use the right techniques for aluminum welding. This involves maintaining a stable arc and using the right welding speed and technique.
One important technique for aluminum welding is to use a push technique, rather than a pull technique. This involves pushing the gun away from you, rather than pulling it toward you, which can help prevent burn-through and other welding problems.
Another important technique for aluminum welding is to maintain a consistent welding speed. This can help ensure a smooth and even weld, and can prevent problems like warping or burn-through.
Common Issues with Push Pull Guns and How to Fix Them
While push pull guns are designed to provide a consistent and controlled wire feed, there are some common issues that can arise during aluminum welding. One common issue is wire feeding problems, which can be caused by improper tension on the feed rollers or a dirty wire feed system. To fix wire feeding problems, start by checking the tension on the feed rollers and adjusting them as needed. You should also clean the wire feed system regularly to prevent dirt and debris from clogging the system.
Another common issue with push-pull guns is burn-back, which occurs when the wire melts and sticks to the contact tip. This can be caused by improper wire speed or arc length. To fix burn back problems, start by adjusting the wire speed and arc length to ensure a smooth and consistent weld. You may also need to replace the contact tip if it has become damaged or worn.
Maintenance and Care for Push Pull Guns
To ensure that your push pull gun continues to function properly, it’s important to take proper care of it. This involves cleaning the gun regularly and replacing any worn or damaged parts. To clean your push-pull gun, start by disconnecting it from the welding machine and removing the wire spool. Use a soft brush or cloth to remove any dirt or debris from the gun, and then use a wire brush to clean the contact tip. You should also inspect your push pull gun regularly for any signs of wear or damage. This may involve replacing the feed rollers, contact tip, or other parts as needed.
Conclusion and Final Thoughts
Push pull guns are a powerful tool for improving your aluminum welding efficiency and quality. They provide a consistent and controlled wire feed, which can help reduce spatter, improve arc stability, and increase welding speed. By choosing the right push pull gun for aluminum welding application and using the right techniques, you can take your aluminum welding skills to the next level.
Remember to set up your push pull gun properly for aluminum welding, and to maintain it regularly to ensure optimal performance. With the right tools and techniques, you can achieve smoother, more precise welds and take on even the most challenging aluminum welding projects with confidence.