Welding without shielding gas may seem like a tempting shortcut, but it can have severe consequences for your welding project. Shielding gas plays a crucial role in the welding process by protecting the weld pool from harmful outside elements such as nitrogen and oxygen in the air. Without it, the weld quality can be compromised, leading to defects and safety risks.
In this section, we will explore the various risks and consequences associated with welding without shielding gas. By understanding the effects of not using shielding gas in welding, you can make informed decisions and take appropriate measures to ensure a successful welding operation.
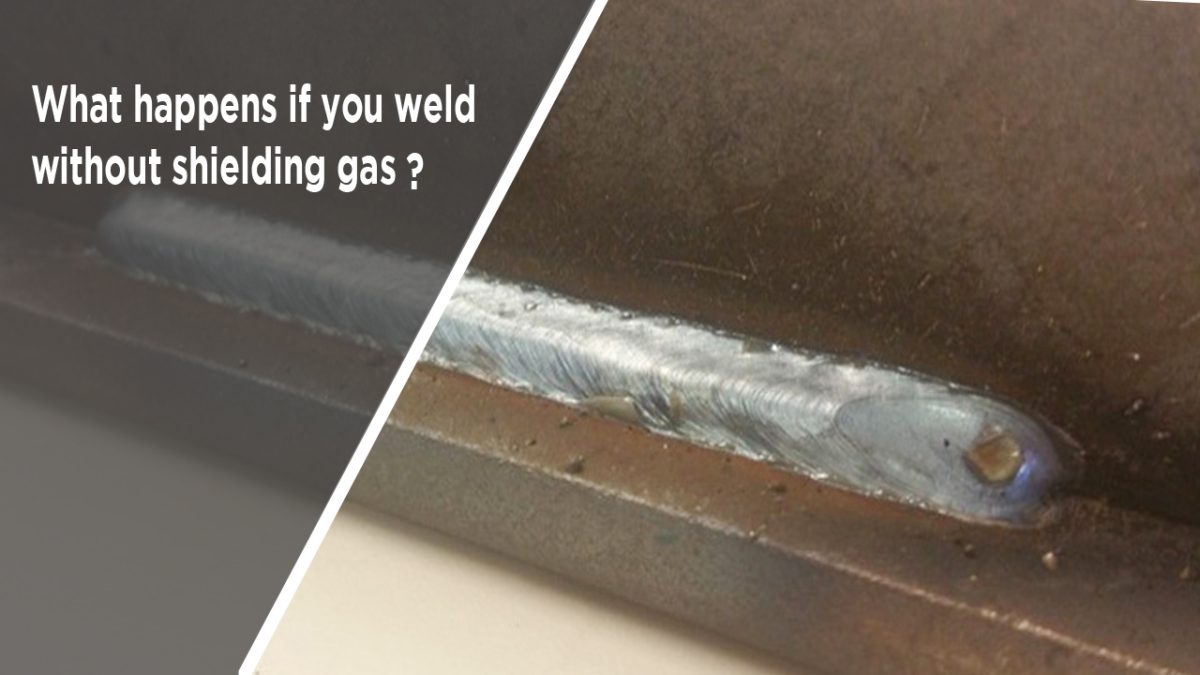
Image by millerwelds
Understanding the Role of Shielding Gas in Welding
Shielding gas is a crucial element in welding that serves to protect the weld area from atmospheric gases such as oxygen and nitrogen. It creates an environment that is free of contamination, ensuring that the welding process is stable and the weld itself is of good quality.
When welding without shielding gas, the welding process becomes vulnerable to various problems, including excessive oxidation, porosity, and lack of penetration. The lack of shielding gas can lead to imperfect welds that are prone to cracking, which can compromise the structural integrity of the weld.
Shielding gas plays another important role in welding, which is to prevent the weld area from overheating. The gas creates an insulated environment that helps regulate the temperature of the welding process, avoiding overheating that could lead to warping and distortion of the welded materials.
The role of shielding gas in welding is to protect the weld area from contamination, improve weld quality, and regulate the welding temperature. Neglecting to use shielding gas can cause various problems, such as oxidized, porosity, and lack of penetration, resulting in potential welding defects, safety issues, and compromised performance. Therefore, it is crucial to use shielding gas properly to achieve optimal weld results.
Impacts on weld quality
Welding without shielding gas is a risky business. If you are not careful, your weld quality can suffer greatly. Porosity is a major issue that can occur when working without the gas. When gas is not present, air gets in and causes bubbles to form in the weld, resulting in a porous metal that is prone to cracking, corrosion, and other defects.
Another risk of welding without shielding gas is a lack of penetration. Shielding gas helps to create the right conditions for the weld pool to flow and penetrate deeply into the metal, forming a strong and durable bond. Without the presence of the gas, the weld may not be able to penetrate deeply enough into the base metal, resulting in weakened and unstable welds.
Welding without shielding gas can also cause defects in the welds, such as warping, cracking and slag inclusions. Presence of oxygen and moisture can cause these defects, which compromise the integrity of the weld. Removing these defects can be time-consuming and expensive, so it’s best to avoid them from the get-go.
Overall, welding without gas drastically increases the risks of poor quality welds, which can have serious consequences in the long term.
Safety Concerns
Welding without shielding gas poses numerous safety risks, both to the welder and those in close proximity to the welding area. Without shielding gas, welding produces harmful fumes and sparks that can cause serious injuries, such as burns, eye damage, and respiratory system damage.
When welding without shielding gas, the resulting welds may be weaker than expected and may break more easily, posing a danger to people and equipment nearby. In addition, welding without shielding gas increases the potential for fire hazards, which can lead to property damage and serious injury.
It is crucial for welders to use proper safety equipment, such as helmets, gloves, and respiratory masks, to protect themselves while welding. In addition, using shielding gas is essential to mitigate the safety risks associated with welding and maintain a safe work environment.
Alternatives to Shielding Gas
While shielding gas is the standard method used in most welding applications, there are instances where it may not be feasible or practical to use it. Welders can explore the alternative techniques and materials to use in these specific scenarios. Some of the common alternatives to shielding gas include:
Flux-cored welding: This method uses a tubular wire that is filled with flux, a material that releases a protective gas when heated. This technique is ideal for outdoor welding tasks that may not provide adequate protection for shielding gas.
Stick welding: Also known as shielded metal arc welding (SMAW), this technique uses an electrode covered in a flux coating that produces a gas shield when heated. This method is ideal for working with thicker materials or for projects that require high quality welds.
Tungsten inert gas (TIG) welding: This technique uses a non-consumable tungsten electrode to create an arc, while a separate filler material is added to the weld pool. This technique is suitable for welding thin materials and producing clean, precise welds.
Cost Implications
While alternatives to shielding gas can be effective, they may come at a higher cost. In some cases, the process can be more complicated and time-consuming than using shielding gas, which can drive up the overall cost of the project.
Method | Advantages | Disadvantages |
---|---|---|
Flux-cored welding | a. Suitable for outdoor welding b. No need for external shielding gas c. Versatile | a. Reduced weld quality b. Requires post-weld cleaning c. More expensive |
Stick welding | – Ideal for thicker materials b. Can be used in outdoor conditions c. Affordable | – Requires post-weld cleaning b. Limited to certain materials c. Limited to flat or horizontal positions |
TIG Welding | a. Produces high-quality welds b. Can be used with thin materials c. Versatile | a. Requires more skill to operate b. Can be more costly c. Lower productivity than other methods |
Ultimately, the choice of welding technique will depend on the specific application, materials, and desired results. By being aware of the alternative methods available, welders can select the best approach and produce high-quality, safe welds.
Common Misconceptions About Welding Without Shielding Gas
Welding without shielding gas is a practice that is often surrounded by myths and misunderstandings. Let’s debunk some of the most common misconceptions about welding without shielding gas.
Myth 1: Welding without shielding gas is always cheaper
Many people assume that welding without shielding gas will save them money. However, this is not always the case. While the initial cost of shielding gas may be higher, investing in proper equipment and training can lead to overall cost savings in the long term.
Myth 2: Welding without shielding gas is just as effective
Some believe that welding without shielding gas yields results that are just as effective as welding with shielding gas. However, welding without shielding gas can lead to weaker and less durable welds, which can ultimately compromise the integrity of the structure being welded.
Myth 3: You don’t need to be as careful when welding without shielding gas
Welding without shielding gas requires just as much caution and care as welding with shielding gas. In fact, it may require even more attention to detail to compensate for the lack of protection that shielding gas provides.
Myth 4: All types of welding can be done without shielding gas
Not all types of welding can be done without shielding gas. The effectiveness of welding without shielding gas depends on the specific welding process and materials being used. Some welding processes, such as MIG welding, require shielding gas to achieve proper results.
Myth 5: You don’t need to worry about ventilation when welding without shielding gas
Welding without shielding gas can produce harmful fumes and gases that can pose a danger to the welder and those nearby. Proper ventilation and safety precautions are necessary to protect against these hazards.
It’s important to separate fact from fiction when it comes to welding without shielding gas. Misunderstandings about this practice can lead to poor welding results and safety hazards.
Best practices for optimal welding with shielding gas
When it comes to welding with shielding gas, adopting best practices can make all the difference in weld quality and safety. Here are some tips and techniques to help you achieve optimal results:
Cleanliness is key: Before starting the welding process, make sure the workpiece is clean and free from any rust, oil, or debris. This will help ensure a strong weld and prevent contamination of the welding pool.
Adjust gas flow: Proper gas flow is necessary for protecting the welding pool and achieving a quality weld. Adjust the flow rate according to the type of gas and the welding application, keeping in mind that too much gas can create turbulence and too little can lead to insufficient protection.
Choose the right gas: Selecting the right gas for the welding application is crucial for achieving optimal results. Consult with experts and manufacturers to determine the best gas for your specific needs.
Monitor welding speed: To avoid overheating and other potential problems, monitor welding speed and adjust it accordingly. Additionally, ensure that the welding machine settings align with the welding speed to achieve proper penetration and fusion.
Protective gear: Always wear proper protective gear, including gloves, helmet, and clothing, when performing welding operations. This will help prevent injuries and keep you safe from harmful gases and particles.
By following these best practices, you can ensure optimal welding results and maintain a safe work environment. Remember to always prioritize safety and quality in any welding project.
Conclusion
Welding without shielding gas is not recommended as it can result in poor weld quality and pose safety risks. Understanding the role of shielding gas in welding and following best practices is essential for achieving optimal results and maintaining safety. While alternative techniques and materials can be used in certain situations, it’s important to evaluate their effectiveness and suitability for the task at hand. By debunking misconceptions and adhering to proper procedures, welders can ensure successful welding operations.
FAQ
What happens if you weld without shielding gas?
Welding without shielding gas can have severe consequences. Shielding gas is crucial for protecting the molten weld pool from atmospheric contamination. Without shielding gas, the weld may suffer from increased porosity, lack of penetration, and potential defects such as cracks. Additionally, welding without gas can result in reduced weld quality, making it less structurally sound and compromising its strength. It is important to always use shielding gas during welding to ensure optimal results.
What is the role of shielding gas in welding?
Shielding gas serves a protective function in welding. It creates a barrier between the molten weld pool and the surrounding atmosphere, preventing oxygen and other contaminants from contaminating the weld. This protective environment ensures that the weld is clean and free from defects. Shielding gas also helps to stabilize the arc and improve the overall weld quality.
How does welding without shielding gas affect weld quality?
Welding without shielding gas can negatively impact weld quality in several ways. Without proper protection, the weld may be more prone to porosity, which can weaken the joint and compromise its integrity. Lack of penetration is also a common issue when welding without gas, resulting in poor fusion and a weaker bond. Additionally, the absence of shielding gas can lead to defects such as cracks and inconsistencies in the weld bead. It is essential to use shielding gas to achieve high-quality welds.
What are the safety concerns associated with welding without shielding gas?
Welding without shielding gas poses significant safety risks. Shielding gas not only protects the weld, but it also helps create a safe working environment. Without it, harmful fumes and gases from the welding process can escape and expose the welder and others nearby to toxic substances. Additionally, the risk of fire and explosion increases when welding without gas, as oxygen and other reactive gases can be present in the atmosphere. To ensure the safety of the welder and those in the vicinity, it is crucial to use the appropriate shielding gas.
Are there alternatives to using shielding gas for welding?
While shielding gas is the preferred method for most welding processes, there are alternative techniques and materials available for certain applications. Some alternatives include the use of flux-cored wires, which contain flux that releases gases to protect the weld. Another option is using self-shielded flux-cored wires, which have a flux coating that generates its own shielding gas when heated. These alternatives can be useful in situations where it is not feasible or practical to use traditional shielding gas.
What are some common misconceptions about welding without shielding gas?
There are a few common misconceptions surrounding welding without shielding gas. One misconception is that welding without gas saves time and money. However, the potential consequences of poor weld quality and safety risks far outweigh any perceived benefits. Another misconception is that shielding gas is not necessary for certain types of welding, such as stick welding. While it is true that some processes may not always require shielding gas, it is essential to understand the specific requirements for each welding application to ensure the best results.
What are the best practices for welding with shielding gas?
To achieve optimal results when using shielding gas, it is important to follow best practices. This includes selecting the appropriate type of shielding gas for the specific welding process and materials being used. It is also crucial to maintain the correct flow rate of shielding gas, as too much or too little can affect the weld quality. Proper preparation of the welding surface, including cleaning and removing any contaminants, is essential. Additionally, ensuring the welder and others in the vicinity are using adequate personal protective equipment (PPE) is critical to maintaining safety during the welding process.