In the world of plastic manufacturing, achieving a strong, durable weld is crucial for producing high-quality products. One technique that has emerged as a game-changer in this industry is ultrasonic plastic welding. This innovative process uses ultrasonic vibrations to melt and join plastic components together, creating a bond that is both reliable and aesthetically pleasing. In this blog, we will explore the key principles behind ultrasonic plastic welding and delve into its applications and advantages in various industries. Join us as we unlock the secrets of this revolutionary technology.
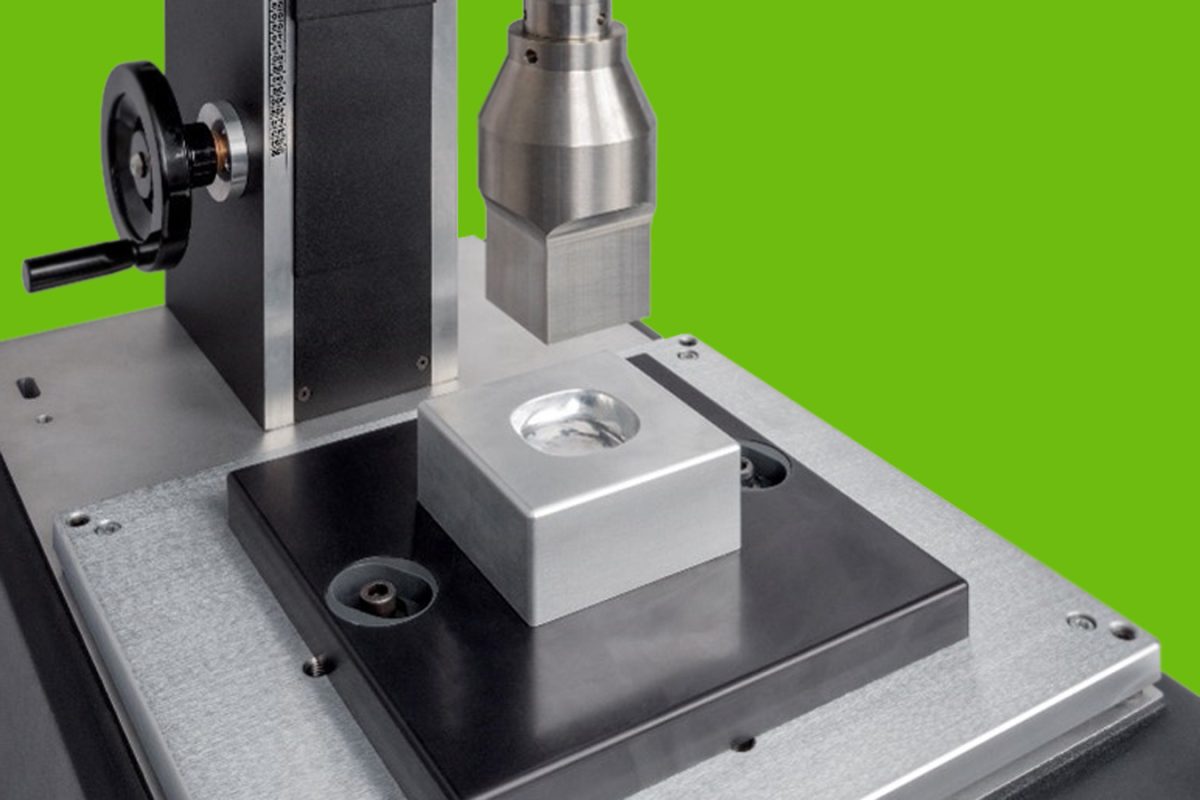
Image by thomasnet
The science behind ultrasonic plastic welding
Understanding the science behind ultrasonic plastic welding is essential for harnessing the full potential of this revolutionary technology.
At its core, ultrasonic plastic welding utilizes high-frequency mechanical vibrations to create friction and heat, which ultimately melt the plastic components together. These vibrations are generated by a transducer that converts electrical energy into mechanical oscillations. The vibrating horn then transmits these oscillations to the joint area, where the plastic parts are pressed together.
The frictional heat generated during the process causes the plastic to soften and form a molten state. As the vibrations continue, the molten material cools and solidifies, creating a strong and seamless bond between the components.
Advantages of ultrasonic plastic welding over other joining methods
Ultrasonic plastic welding offers several advantages over traditional joining methods, making it an attractive option for manufacturers in various industries. One major advantage is its ability to create strong and seamless bonds without the need for additional materials such as adhesives or fasteners. This not only reduces production costs but also eliminates the risk of chemical contamination or weak points in the joint.
Additionally, ultrasonic plastic welding is a non-contact process, meaning there is no direct physical contact between the welding equipment and the plastic components. This prevents any damage or distortion to delicate or sensitive parts, ensuring a high level of precision and accuracy during the welding process. Ultrasonic plastic welding is a fast and efficient method, with weld times often measured in milliseconds. This allows for high-volume production rates and increased productivity, making it ideal for industries with demanding production schedules.
In the upcoming section, we will explore specific examples of how ultrasonic plastic welding is being used in different industries, highlighting its wide-ranging applications and success stories. Stay tuned to discover the endless possibilities of this cutting-edge technology.
Selecting the right equipment for ultrasonic plastic welding
Selecting the right equipment for ultrasonic plastic welding is crucial to achieving optimal results. There are several factors to consider when choosing the appropriate equipment for a specific application.
Firstly, it is important to assess the power requirements of the welding process. Higher power levels are generally required for thicker or more complex plastic components, while lower power levels may be sufficient for thinner materials. Understanding the power requirements will help determine the suitable ultrasonic plastic welding machine for the job.
The welding tooling should be carefully selected to ensure proper alignment and contact with the plastic components. This includes choosing the correct horn design and shape, as well as the appropriate sonotrode size and material.
Another important factor to consider is the control system of the ultrasonic plastic welding equipment. Look for a system that offers precise control over welding parameters such as amplitude, pressure, and welding time. This will allow for customization and optimization of the welding process to meet specific requirements.
Lastly, it is essential to consider the overall reliability and durability of the equipment. Look for reputable manufacturers with a track record of producing high-quality and dependable ultrasonic plastic welding machines.
Preparing for a successful ultrasonic plastic welding process
In order to ensure a successful ultrasonic plastic welding process, proper preparation is key. Before beginning the welding process, it is important to properly clean and prepare the plastic components that will be joined together. Cleaning the surfaces of the plastic parts is crucial to remove any dirt, dust, or other contaminants that could affect the quality of the weld. This can be done using a variety of methods, such as wiping the surfaces with a clean cloth or using a specialized cleaning solution.
In addition to cleaning, it is also necessary to properly align the plastic components to be welded. This can be achieved by using fixtures or jigs that hold the parts in the correct position and orientation. Proper alignment is important to ensure that the weld is strong and free of any defects. It is essential to choose the appropriate welding parameters for the specific plastic materials being used. Factors such as welding time, pressure, and amplitude need to be carefully adjusted to achieve the desired weld strength and appearance.
Troubleshooting common challenges in ultrasonic plastic welding
While ultrasonic plastic welding is generally a reliable and effective joining method, there are some common challenges that can arise during the process. Understanding these challenges and knowing how to troubleshoot them can help ensure successful welds and minimize downtime.
One common issue that can occur is inadequate weld strength. This can be caused by factors such as insufficient pressure or amplitude, improper alignment of the plastic components, or improper welding time. To address this issue, it is important to carefully review and adjust the welding parameters to ensure they are appropriate for the specific materials and components being used.
Another challenge that may arise is the occurrence of flash, which is excess plastic material that is pushed out during the welding process. Flash can degrade the appearance and quality of the weld. To avoid this, it is crucial to properly position and align the plastic components, ensuring that they are tightly compressed during welding.
In some cases, delamination or separation of the plastic materials may occur. This can be caused by factors such as incompatible materials, inadequate pressure, or excessive welding time. To prevent delamination, it is important to select compatible materials and adjust the welding parameters accordingly.
Lastly, if the ultrasonic plastic welding process consistently produces inconsistent or weak welds, it may indicate a problem with the equipment itself. In such cases, it is recommended to consult a qualified technician or manufacturer to address the issue.
Best practices for maintaining the quality of ultrasonic plastic welding
Now that we have discussed some common challenges that can arise during the ultrasonic plastic welding process, let’s explore some best practices for maintaining the quality of your welds. By following these guidelines, you can maximize the effectiveness and efficiency of ultrasonic plastic welding in your manufacturing processes.
1. Material selection: It is crucial to choose compatible plastic materials that are suitable for ultrasonic plastic welding. Different materials have varying melting points, thermal properties, and molecular structures, which can affect the success of the weld. Consulting material datasheets or seeking advice from material suppliers can help you select the most appropriate materials for your application.
2. Equipment calibration and maintenance: Regularly calibrating and maintaining your ultrasonic plastic welding equipment is essential for consistent and reliable welds. This includes checking and adjusting parameters such as amplitude, pressure, and welding time. It is also important to keep the equipment clean and free from debris or contaminants that could interfere with the welding process.
3. Proper component alignment: Accurate alignment of the plastic components is critical for successful welds. Ensure that the components are securely held in place during welding to avoid any movement or shifting. Using fixtures or jigs can help achieve precise component alignment and improve the overall weld quality.
4. Optimal welding parameters: Adjusting the welding parameters to suit the specific materials and components being used is crucial. This includes setting the appropriate amplitude, pressure, welding time, and cooling time. Experimentation and testing may be required to find the optimal parameters for your application, taking into account factors such as material thickness and geometry.
5. Training and supervision: Provide proper training and supervision to operators involved in the ultrasonic plastic welding process. This will ensure that they have a thorough understanding of the equipment, welding techniques, and troubleshooting methods. Regularly reviewing and reinforcing best practices will help maintain the quality of the welds and minimize errors.
By implementing these best practices, you can enhance the quality and reliability of your ultrasonic plastic welding process. In the next section, we will delve into the specific future of ultrasonic plastic welding over other traditional joining methods. Don’t miss out on discovering why this technology is rapidly gaining popularity in various industries. Stay tuned!
Embracing the future of ultrasonic plastic welding technology
Now that we have discussed the best practices for maintaining the quality of your ultrasonic plastic welds, let’s take a look at why this technology is gaining popularity in various industries and the advantages it offers over traditional joining methods.
Ultrasonic plastic welding provides several unique advantages that make it a preferred choice for many manufacturers. Firstly, it offers fast and efficient welding, resulting in increased productivity and reduced production time. The process is also highly repeatable and consistent, ensuring uniform weld quality across each finished product.
Another significant advantage is the ability to weld complex and delicate parts without causing any damage or distortion. With ultrasonic plastic welding, the energy is focused at the joint interface, leaving the surrounding areas unaffected. This makes it an excellent choice for joining parts with intricate designs or thin walls.
Additionally, ultrasonic plastic welding is a non-contact process, meaning there is no need for adhesives, solvents, or additional consumables. This leads to cost savings in terms of materials and eliminates the risk of contamination from bonding agents. This technology offers excellent strength and hermetic seals, making it suitable for applications that require a strong and secure bond. The welds created through ultrasonic plastic welding are resistant to vibration, pressure, and moisture, ensuring product durability and reliability.
Conclusion and Harnessing the power of ultrasonic plastic welding for superior product manufacturing
Ultrasonic plastic welding is revolutionizing the manufacturing industry with its numerous advantages and versatility. From fast and efficient welding to the ability to join complex and delicate parts without damage, this technology offers a superior alternative to traditional joining methods. The non-contact nature of ultrasonic plastic welding eliminates the need for additional consumables, saving on material costs and reducing the risk of contamination. The resulting welds are strong, hermetic, and resistant to external factors such as vibration, pressure, and moisture. With these benefits in mind, it is no wonder that ultrasonic plastic welding has become a popular choice across various industries.