Welding is a versatile skill that allows for the joining of metal components through the application of heat and pressure. To become a master welder, one must not only possess a strong understanding of the welding process but also be proficient in various welding positions. In this comprehensive guide, we will delve into the intricacies of 1g to 6g welding positions, exploring the techniques, challenges, and advantages associated with each.
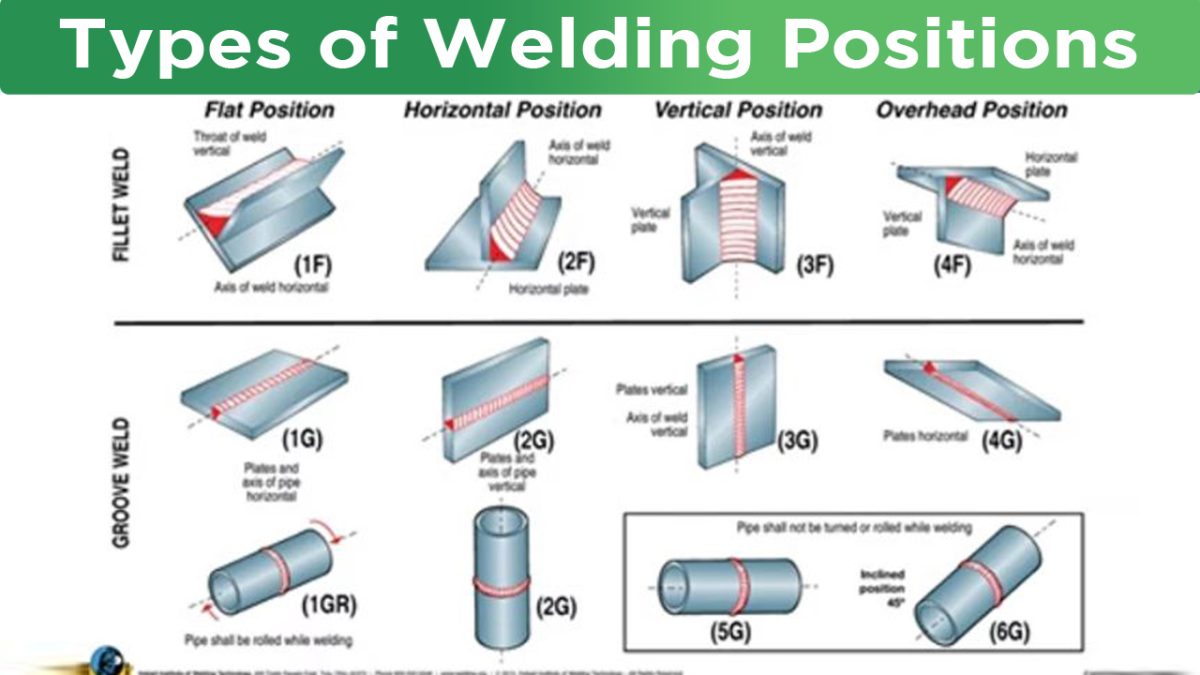
Image by welding.org
What is 1g welding position?
The 1g welding position, also known as the flat position, is the most straightforward and commonly used welding position. In this position, the welder works on a horizontal surface, with the weld bead forming in a flat plane. The 1g position is often considered the foundation of welding, as it allows beginners to develop their skills and gain confidence in their abilities.
Techniques and tips for welding in the 1g position
To excel in the 1g welding position, there are several techniques and tips that welders should keep in mind. Firstly, it is essential to ensure proper joint preparation, as clean and well-aligned edges facilitate a strong weld. Additionally, maintaining a consistent travel speed and electrode angle is crucial for achieving uniform weld penetration and bead appearance. Furthermore, implementing proper heat control and manipulation of the welding puddle helps prevent distortion and ensures optimal fusion.
Advantages and disadvantages of the 1g welding position
The 1g welding position offers several advantages, making it an excellent starting point for novice welders. Due to the flat orientation, the weld pool remains stable, allowing for easier control and manipulation. Moreover, the 1g position provides better accessibility and visibility, as the welder can directly observe the weld bead formation. However, one disadvantage of the 1g position is that it does not fully simulate real-world welding conditions, as most applications require welding in various positions.
What is 2g welding position?
The 2g welding position, also known as the horizontal position, involves welding on a vertical surface. In this position, the weld bead moves horizontally and forms a fillet weld. Welding in the 2g position presents unique challenges and requires additional skills compared to the 1g position.
Mastering the 2g welding position – techniques and challenges
To become proficient in the 2g welding position, welders need to adapt their techniques and overcome specific challenges. One crucial technique is maintaining the correct electrode angle to ensure proper penetration and fusion. Controlling the travel speed is essential to achieve a consistent weld bead profile. Challenges in the 2g welding position include the tendency for gravity to pull the molten metal downwards, which can lead to inadequate fusion if not adequately managed.
Comparing the 2g and 1g welding positions
While the 2g and 1g welding positions share similarities, they also have distinct differences. One key difference is the direction of the weld bead movement. In the 1g position, the weld bead moves in a horizontal direction, while in the 2g position, it moves vertically. The 2g welding position requires the welder to adjust their technique to account for gravity’s effect on the molten metal.
What is 3g welding position?
The 3g welding position, also known as the vertical position, involves welding on a vertical surface with the weld bead moving in an upward direction. Welding in the 3g position requires advanced skills and is often considered a significant milestone in a welder’s journey.
Tips and tricks for welding in the 3g position
To excel in the 3g welding position, welders should consider implementing specific tips and tricks. One crucial tip is to maintain proper torch angle and manipulation to ensure proper fusion and penetration. Using the correct welding technique, such as a weaving motion, can help distribute heat evenly and prevent the formation of defects.
What is 4g welding position?
The 4g welding position, also known as the overhead position, requires welding on a horizontal surface with the weld bead moving in a downward direction. Welding in the 4g position presents unique challenges and requires special techniques to overcome them.
Challenges and techniques for welding in the 4g position
Welding in the 4g position requires welders to overcome challenges such as gravity’s effect on the molten metal and limited visibility due to the welding position. Techniques that can help welders navigate these challenges include maintaining a consistent travel speed, using proper torch manipulation, and frequently pausing to inspect the weld bead.
Comparing the 4g and 3g welding positions
The 4g and 3g welding positions share similarities, as both involve welding on vertical surfaces. However, the key difference lies in the direction of the weld bead movement. In the 3g position, the weld bead moves upward, while in the 4g position, it moves downward. The 4g position presents additional challenges due to the overhead orientation.
What is 5g welding position?
The 5g welding position, also known as the horizontal-vertical position, combines elements of both the horizontal and vertical positions. In this position, the weld bead moves in both horizontal and vertical directions, creating a challenging welding scenario.
Techniques and considerations of 5g position
To become proficient in the 5g welding position, welders must master specific techniques and considerations. One crucial technique is maintaining a consistent and controlled torch angle throughout the weld. Additionally, implementing proper joint fit-up and preparation is essential to ensure optimal fusion and penetration. Welders should also consider the orientation of the weld joint and adjust their travel speed and manipulation accordingly.
What is 6g welding position?
The 6g welding position, also known as the pipe position, involves welding on a pipe that is positioned at a 45-degree angle. Welding in the 6g position is considered the most challenging due to the combination of complex joint geometry and the need for multi-directional weld bead movement.
Tips and tricks for welding in the 6g position
To tackle the challenges associated with the 6g welding position, welders should employ specific tips and tricks. One essential tip is to practice proper body positioning and stability, as this helps maintain control and precision during the welding process. Additionally, using a combination of welding techniques, such as a weaving motion and a push-pull technique, can help distribute heat evenly and achieve uniform fusion.
Comparing the 6g and 5g welding positions
While the 6g and 5g welding positions share similarities, the 6g position presents additional challenges due to the pipe’s angled orientation. Welding in the 6g position requires welders to adapt their techniques and consider the joint geometry to achieve a strong and durable weld.
Conclusion and Becoming a master welder in all positions
Welding requires proficiency in various welding positions, from the foundational 1g position to the complex 6g position. By understanding the techniques, challenges, and considerations associated with each position, welders can expand their skill set and become versatile craftsmen. With practice, determination, and a commitment to continuous learning, aspiring welders can embark on a journey towards becoming a master welder in all positions.