Spot welding is a widely used technique in industries that require joining metal parts together. It involves applying heat and pressure to a small area of the metal, creating a weld that fuses the two parts together. This process is commonly used in automotive manufacturing, electronics production, and various other industries where strong and efficient joining of metal parts is essential.
Spot welding works by passing an electrical current through the metal parts to be joined. The electrical current generates heat, causing the metal to melt and form a weld nugget. The pressure applied during the process ensures that the molten metal solidifies, creating a strong bond between the metal parts.
Spot welding is known for its speed and efficiency. It can create welds in a matter of seconds, making it an ideal choice for mass production environments. Additionally, spot welding produces minimal distortion and does not require any additional materials such as filler metals or fluxes, further enhancing its cost-effectiveness.
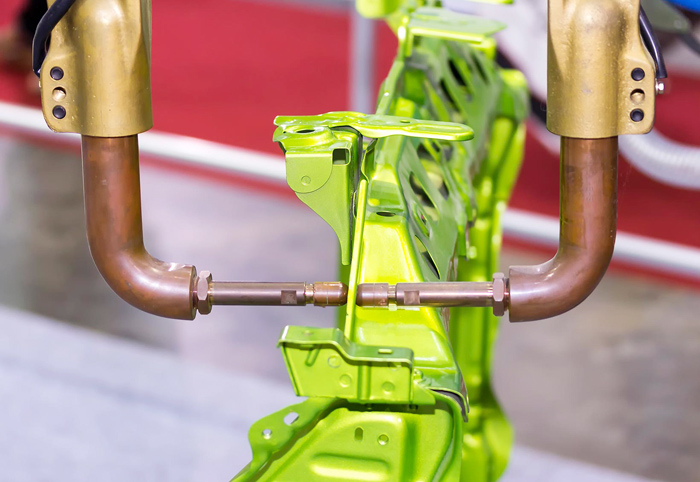
Photos by twi-global.com
How does spot welding work?
Spot welding operates on the principle of electrical resistance. When an electrical current is passed through two metal parts in contact with each other, the resistance of the metal creates heat. This heat causes the metal to reach its melting point, forming a weld nugget.
To perform spot welding, two copper alloy electrodes are used. These electrodes apply pressure to the metal parts, ensuring good contact and allowing the electrical current to pass through. The electrodes also act as a heat sink, preventing the metal from overheating and maintaining the desired temperature for the welding process.
Spot welding machines are equipped with a control system that regulates the electrical current, pressure, and welding time. This control system ensures consistent and reliable welds, meeting the required specifications for each application.
Advantages of spot welding
Spot welding offers several advantages that make it a preferred choice in many industries. Some of the key advantages include:
- Speed and efficiency: Spot welding is a fast process that can create welds in seconds. This makes it highly suitable for high-volume production environments where time is of the essence.
- Cost-effectiveness: Spot welding eliminates the need for additional materials such as filler metals or fluxes, reducing costs associated with welding. It also requires minimal post-welding operations, further enhancing cost-effectiveness.
- Strong and durable welds: Spot welding creates welds that are exceptionally strong and durable. The fusion of the metal parts ensures a reliable bond that can withstand high loads and stresses.
- Minimal distortion: Spot welding produces minimal distortion in the metal parts, making it suitable for applications where dimensional accuracy is crucial.
- Ease of automation: Spot welding is easily automated, allowing for efficient and consistent production. This automation capability contributes to increased productivity and reduced labor costs.
Disadvantages of spot welding
While spot welding offers numerous advantages, there are some limitations to consider. These disadvantages include:
- Limited joint configurations: Spot welding is best suited for joining metal parts in a lap joint configuration. It may not be suitable for complex joint configurations or joining dissimilar metals.
- Heat-affected zone: The heat generated during spot welding can create a heat-affected zone around the weld, which may affect the mechanical properties of the metal in that area.
- Equipment and setup costs: Spot welding requires specialized equipment and setup, which can be costly, especially for small-scale operations.
- Skill and training requirements: Operating spot welding machines requires skill and training to ensure proper setup, electrode alignment, and consistent weld quality.
Despite these disadvantages, spot welding remains a popular choice in industries where its benefits outweigh the limitations.
Resistance spot welding
Resistance spot welding is the most common type of spot welding, widely used in industries such as automotive manufacturing and appliance production. It utilizes electrical current and pressure to create strong welds between metal parts.
During resistance spot welding, two copper alloy electrodes apply pressure to the metal parts, ensuring good contact. An electrical current is then passed through the metal parts, generating heat. The heat causes the metal to melt and form a weld nugget. The pressure applied ensures that the molten metal solidifies, creating a strong bond between the metal parts.
Resistance spot welding offers several advantages, including high productivity, cost-effectiveness, and strong welds. It is particularly suitable for joining thin metal sheets and is commonly used in automotive body assembly, electrical component manufacturing, and other applications where speed and efficiency are crucial.
Projection spot welding
Projection spot welding is a variant of resistance spot welding that is particularly useful when precise weld locations are required. In projection spot welding, the welding occurs at specific points called projections that are designed into the metal parts.
Projections are small raised areas on the metal parts that concentrate the electrical current and heat during the welding process. The projections serve as localized heat sources, ensuring that the welds are formed at the desired locations. This technique allows for precise control over the welding process and results in strong and visually appealing welds.
Projection spot welding is commonly used in industries where aesthetics are important, such as automotive manufacturing and consumer electronics production. By utilizing projections, manufacturers can create visually pleasing welds that enhance the overall appearance of the finished product.
Seam spot welding
Seam spot welding is a variation of spot welding that is used to join two overlapping metal sheets along a continuous seam. Unlike resistance spot welding, which creates individual weld nuggets, seam spot welding produces a continuous weld along the length of the seam.
Seam spot welding is commonly used in the automotive industry for joining sheet metal components, such as the body panels of cars. It offers several advantages, including increased strength, improved leak resistance, and enhanced aesthetics.
During seam spot welding, two rotating copper alloy wheels are used as the electrodes. The wheels apply pressure to the overlapping metal sheets and rotate along the seam, creating a continuous weld. This technique ensures consistent weld quality and allows for high-speed production.
Flash butt spot welding
Flash butt spot welding is a type of spot welding that is primarily used for joining thick metal parts. It utilizes electrical resistance to generate heat and create a seamless weld.
During flash butt spot welding, the metal parts to be joined are clamped between two copper alloy electrodes. An electrical current is passed through the metal parts, generating heat by resistance. The heat causes the metal to soften and eventually melt. The clamping force applied ensures that the molten metal is forced together, forming a seamless weld.
Flash butt spot welding is commonly used in industries such as shipbuilding, construction, and heavy machinery manufacturing. It is particularly suitable for joining thick metal plates and bars, where other welding methods may not be as effective. The resulting welds are strong, durable, and capable of withstanding high loads and harsh environments.
Spot welding vs other welding methods
Spot welding offers unique advantages that differentiate it from other welding methods. Some of the key differences include:
- Speed and efficiency: Spot welding is significantly faster than many other welding methods. It can create welds in seconds, making it highly suitable for mass production environments.
- Cost-effectiveness: Spot welding eliminates the need for additional materials such as filler metals or fluxes, reducing costs associated with welding. It also requires minimal post-welding operations, further enhancing cost-effectiveness.
- Minimal distortion: Spot welding produces minimal distortion in the metal parts, making it suitable for applications where dimensional accuracy is crucial.
- Joint configurations: Spot welding is best suited for lap joint configurations, whereas other welding methods may offer more flexibility for complex joint configurations or joining dissimilar metals.
- Power consumption: Spot welding typically requires lower power consumption compared to other welding methods, contributing to its cost-effectiveness.
The choice of welding method depends on various factors, including the specific application, material properties, joint configuration, and production requirements. By understanding the strengths and limitations of spot welding and other welding methods, manufacturers can make informed decisions about the most suitable technique for their needs.
Conclusion
Spot welding is a versatile and widely used technique that offers numerous benefits in various industries. Understanding the different types of spot welding, such as resistance spot welding, projection spot welding, seam spot welding, and flash butt spot welding, provides valuable insights into their unique applications and advantages.
From the speed and efficiency of resistance spot welding to the precise weld locations achieved through projection spot welding, each type of spot welding offers distinct advantages. Seam spot welding provides continuous welds along the length of the seam, while flash butt spot welding excels in joining thick metal parts.
By considering the specific requirements of each application, manufacturers can optimize their spot welding processes and achieve strong, durable, and visually appealing welds. Whether you’re involved in automotive manufacturing, electronics production, or any industry that requires joining metal parts together, understanding the different types of spot welding can help you make informed decisions and ensure the success of your projects.