Exploring the fascinating world of plastic welding unveils a versatile and efficient method for joining thermoplastics. Whether it’s for engineering, crafting, or repairs, the plastic welding method offers a reliable solution. With diverse techniques like hot gas welding, extrusion welding, or ultrasonic welding, the process addresses a wide array of applications. From automotive to manufacturing, the adaptability of plastic welding reinforces its significance in various industries.
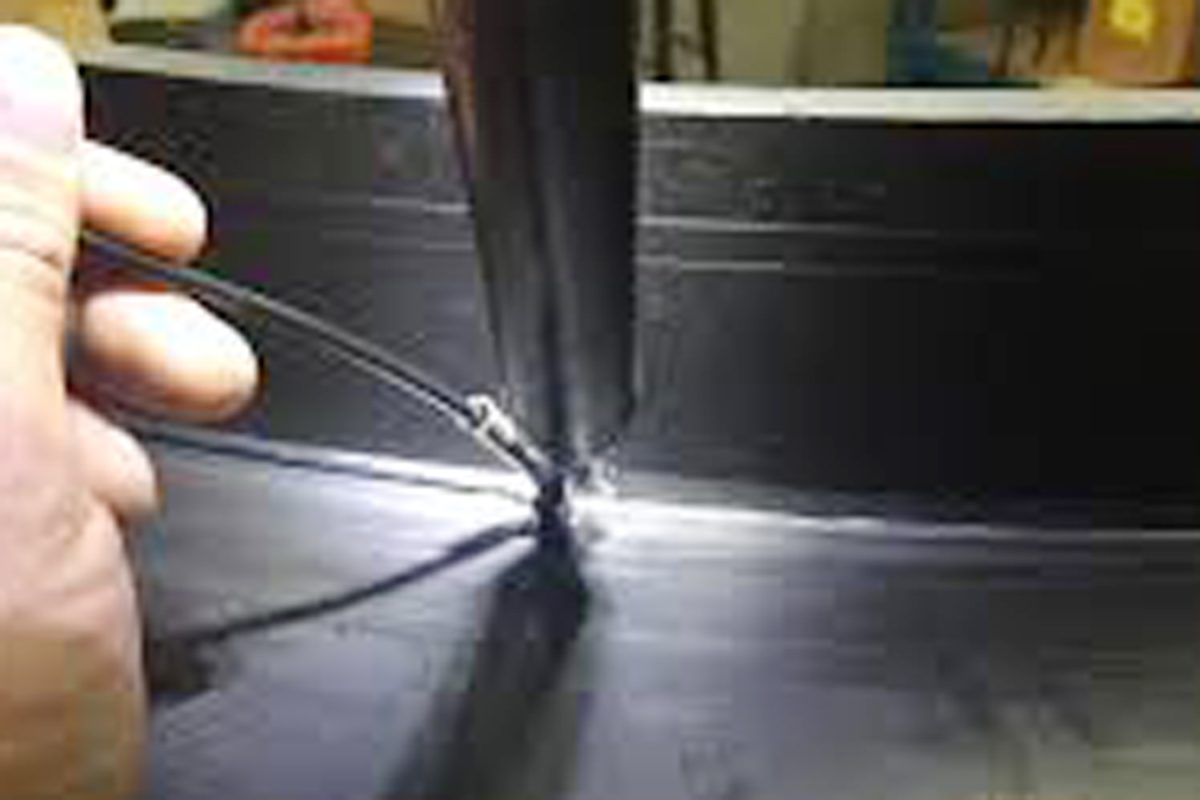
Understanding the intricacies of each welding technique and their suitability for different materials is essential for achieving robust and seamless welds. Join us as we delve into the nuances of plastic welding, uncovering its practical applications, advantages, and practical tips. Whether you’re a DIY enthusiast or a seasoned professional, mastering the art of plastic welding can open up a world of creative possibilities and problem-solving potential.
Common Types of Plastic Welding Methods
Hot Gas Welding
Hot gas welding, also known as heat sealing, employs a stream of heated gas to soften the plastic surfaces, allowing them to fuse together. This method is particularly effective for welding thermoplastics such as PVC, polypropylene, and polyethylene. The process begins by heating the welding rod and the joint edges, followed by the application of pressure to fuse the molten surfaces. Hot gas welding is widely used in fabricating chemical tanks, pipes, and other industrial components where a strong, leak-proof seal is crucial.
Extrusion Welding
Extrusion welding involves the use of a heated plastic extruder to melt and fuse thermoplastic materials. This technique is commonly utilized in large-scale projects, such as constructing plastic tanks, pipelines, and geomembranes. By extruding molten plastic into the joint, a continuous, homogeneous weld is achieved. The versatility and efficiency of extrusion welding make it an ideal choice for joining thermoplastics of varying thicknesses and compositions.
High-Frequency Welding
High-frequency welding, also referred to as radio-frequency welding, utilizes an electromagnetic field to generate heat within the plastic materials, resulting in a strong molecular bond. This method is favored for creating airtight and watertight seals, making it suitable for applications in the medical, automotive, and inflatable products industries. High-frequency welding is particularly effective for welding PVC, PET, and other vinyl-based materials, offering precise control over the welding process and ensuring consistent, high-quality welds.
Ultrasonic Welding
Ultrasonic welding harnesses high-frequency ultrasonic vibrations to create frictional heat between the plastic components, leading to molecular bonding. This rapid and efficient process is widely employed in industries such as electronics, automotive, and medical devices. Ultrasonic welding is renowned for its ability to produce clean, precise joints without the need for additional materials or adhesives, making it an environmentally friendly and cost-effective welding technique.
Spin Welding
Spin welding is a frictional welding process that involves rotating one component against a stationary component, generating frictional heat that results in a secure weld. This method is commonly used for joining thermoplastics with circular or cylindrical geometries, such as fittings, caps, and valves. Spin welding offers fast cycle times and uniform welds, making it a preferred choice for applications requiring consistent, high-strength connections.
Advantages of Plastic Welding
Plastic welding offers numerous advantages over traditional joining methods such as adhesives or mechanical fasteners. By directly melting and fusing the plastic materials, welding creates seamless and robust bonds that are often stronger than the surrounding material. This results in joints that are resistant to impacts, chemicals, and environmental factors, making them ideal for demanding applications.
Plastic welding eliminates the need for additional consumables like adhesives or screws, reducing material costs and simplifying the assembly process. The precise control over the welding parameters allows for consistent and uniform joints, ensuring high-quality results across production batches. Furthermore, the ability to weld dissimilar plastics together expands the design possibilities, enabling the creation of complex and multi-material structures.
Applications of Plastic Welding
The versatility of plastic welding extends its applications across a wide range of industries and disciplines. In the automotive sector, plastic welding is commonly utilized for repairing bumpers, interior panels, and fuel tanks, offering a cost-effective alternative to part replacement. In the manufacturing realm, plastic welding finds extensive use in fabricating tanks, pipes, and enclosures, where the seamless joints and chemical resistance of welded assemblies are essential. The construction industry leverages plastic welding for installing and repairing geomembranes, ensuring watertight seals in various environmental containment applications.
Moreover, the versatility of plastic welding is evident in the realm of art and design, where it enables the creation of intricate sculptures and functional art pieces from thermoplastic materials. Understanding these diverse applications underscores the significance of mastering plastic welding techniques for professionals and hobbyists alike.
Factors to Consider When Choosing Plastic Welding Method
When selecting a plastic welding technique, several factors must be considered to ensure optimal results. The type of plastic material, joint design, welding environment, and desired strength and aesthetics all play crucial roles in determining the most suitable welding method. Factors such as production volume, cost considerations, and regulatory standards should be taken into account when evaluating the feasibility of a specific welding technique for a given application.
By carefully weighing these factors and consulting with experienced welding professionals, the most appropriate plastic welding method can be chosen to achieve the desired performance and durability.
Safety Precautions for Plastic Welding
As with any industrial process, plastic welding requires adherence to strict safety protocols to mitigate potential hazards. Proper ventilation is essential when working with heated plastics to prevent the inhalation of fumes and airborne particles. Using personal protective equipment such as respirators, safety glasses, and heat-resistant gloves shields welders from exposure to hazardous fumes and molten plastic.
Additionally, maintaining a clean and organized work area minimizes the risk of accidents and ensures efficient workflow during welding operations. Adequate training and familiarity with the specific welding equipment and techniques are paramount to executing plastic welding tasks safely and effectively. By prioritizing safety measures, welders can create a secure working environment while achieving top-quality welds.
Equipment and Materials for Plastic Welding
Executing successful plastic welding operations necessitates the use of specialized equipment and materials tailored to each welding method. Hot gas welding requires a heat gun or hot air welder capable of delivering precise and controlled heat to the plastic surfaces. Extrusion welding mandates an extrusion welding gun and compatible welding rods that match the base material for seamless fusion. Ultrasonic welding systems comprise a welding press equipped with ultrasonic transducers that convert electrical energy into high-frequency vibrations for molecular bonding.
Understanding the nuances of each equipment type and selecting high-quality materials ensures the reliability and integrity of plastic welds. Maintaining the equipment in optimal condition through regular maintenance and calibration prolongs their service life and enhances welding performance.
Common Mistakes in Plastic Welding
Despite the precision and intricacies of plastic welding, common mistakes can compromise the integrity and strength of welded joints. Inadequate surface preparation, such as insufficient cleaning or roughing, hinders the adhesion and fusion of plastic surfaces, leading to weak welds. Overheating the plastic during welding can cause material degradation, resulting in discoloration, warping, or reduced mechanical properties in the welded area. Inconsistent pressure application during welding may lead to uneven weld beads or incomplete fusion, compromising the overall strength of the joint.
Additionally, using incompatible welding rods or neglecting proper welding technique can introduce defects and imperfections in the weld, diminishing its performance. By recognizing and addressing these common pitfalls, welders can elevate the quality and reliability of their plastic welding endeavors.
Professional Plastic Welding Services
For complex or specialized plastic welding requirements, enlisting the expertise of professional welding services offers a dependable solution. Professional welders possess extensive experience and knowledge in a wide range of plastic welding methods, ensuring the precise execution of welding tasks with exceptional quality. Whether it’s for industrial applications, custom fabrication, or prototyping, professional plastic welding services cater to diverse needs with precision and reliability.
Furthermore, professional welders are equipped with advanced welding equipment and tools, enabling them to tackle intricate projects and challenging materials with confidence and expertise. Collaborating with professional plastic welding services not only guarantees superior weld quality but also streamlines the production process, saving time and resources for businesses and individuals alike.
Final Thoughts
The diverse array of plastic welding techniques offers unparalleled versatility and efficiency in joining thermoplastic materials. From the precision of ultrasonic welding to the robustness of hot gas welding, each method presents unique strengths and applications, catering to a wide range of industrial and manufacturing needs. By understanding the advantages and intricacies of hot gas welding, extrusion welding, high-frequency welding, ultrasonic welding, and spin welding, professionals and enthusiasts alike can make informed decisions when selecting the most suitable welding technique for their specific projects.
With the right knowledge and expertise, the seamless fusion of plastics through welding opens the door to innovative solutions and boundless possibilities in today’s dynamic industrial landscape. By incorporating these insights into your welding endeavors, you can elevate the quality and durability of your plastic assemblies, ensuring that they meet the stringent demands of modern applications. Embrace the art and science of plastic welding, and discover the transformative potential it holds for your projects and innovations.