Are you interested in diving into the intricate world of pipe welding? Understanding the diverse types of pipe welding is paramount for professionals in the industry and aspiring welders alike. From the versatility of TIG welding to the durability of MIG welding, there’s a multitude of methods tailored to specific requirements. In the realm of TIG welding, precision and control reign supreme. This method proves ideal for critical joints and thin materials, where the intricacy of the weld is of utmost importance. On the other hand, MIG welding boasts speed and efficiency, making it the go-to choice for large-scale projects and thicker materials.
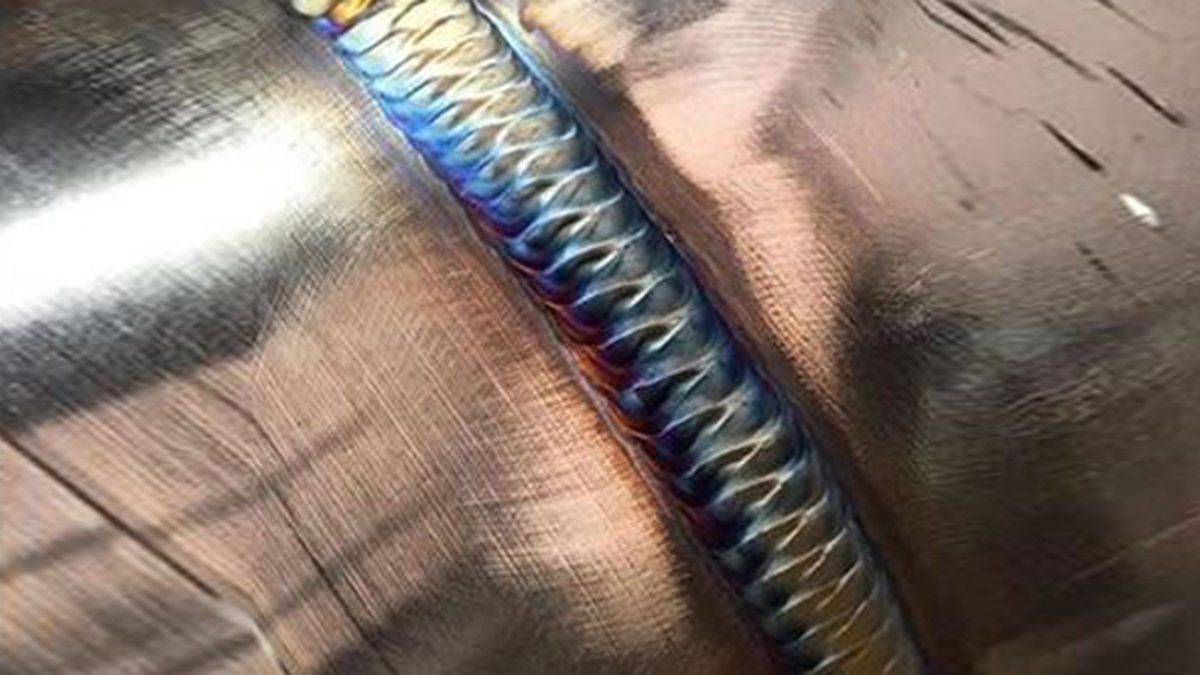
Image by arcweldingtipsandtricks
Whether you are a welding enthusiast or a professional seeking to expand your knowledge, delving into the unique characteristics of each welding type can elevate your expertise and proficiency. Join us as we unravel the diverse techniques, applications, and advantages of each pipe welding method, unravelling the artistry and science behind impeccable welds. Exploring the nuances of pipe welding techniques promises to enrich your understanding and enhance your welding prowess.
Different Types of Pipe Welding Processes
TIG Welding for Pipe Welding
TIG welding, or Tungsten Inert Gas welding, is a precise and versatile welding process commonly used in pipe welding. The technique utilizes a non-consumable tungsten electrode to produce the weld, along with a shielding gas to protect the weld area from atmospheric contamination. TIG welding offers exceptional control and produces high-quality welds, making it suitable for a wide range of materials, including stainless steel, carbon steel, and non-ferrous metals. Its ability to create clean, precise welds makes it ideal for applications where aesthetics and strength are crucial, such as in the food and beverage industry, pharmaceutical equipment, and aerospace components.
TIG welding is particularly well-suited for pipe welding due to its ability to provide precise control over the heat input and weld pool. This is especially advantageous when welding thin-walled pipes or intricate joints, where maintaining the structural integrity of the material is paramount. The process allows welders to produce welds with minimal spatter and distortion, resulting in clean, high-quality joints that meet stringent industry standards.
In pipe welding, TIG welding is often chosen for its ability to create welds with excellent penetration and fusion, ensuring the integrity and strength of the joint. Welders can manipulate the heat input and welding parameters to accommodate different pipe diameters, wall thicknesses, and materials, making TIG welding a versatile choice for a wide range of pipe welding applications.
Stick Welding for Pipe Welding
Stick welding, also known as Shielded Metal Arc Welding (SMAW), is a widely used welding process that is well-suited for pipe welding in various industrial and construction settings. The process involves the use of a consumable electrode coated in flux, which provides the necessary shielding gas and flux to protect the weld pool from atmospheric contamination. Stick welding is known for its versatility and ability to produce robust welds, making it a popular choice for welding pipes made of carbon steel, alloy steel, and other ferrous metals.
When it comes to pipe welding, stick welding offers several advantages, particularly in challenging or outdoor environments where other welding processes may be less practical. The portability and simplicity of stick welding equipment make it well-suited for on-site pipe welding, allowing welders to access and weld pipes in various positions and locations. This flexibility is especially valuable in construction, maintenance, and repair projects where pipes may be installed in confined spaces or at elevated heights.
Stick welding is also known for its ability to produce deep penetration welds, making it suitable for welding thick-walled pipes and components where strength and durability are essential. The process can effectively handle impurities and contaminants in the base metal, making it a reliable choice for welding pipes in less-than-ideal conditions. Additionally, stick welding equipment is generally more affordable and accessible compared to other welding processes, making it a practical choice for a wide range of pipe welding applications.
MIG Welding for Pipe Welding
MIG welding, or Gas Metal Arc Welding (GMAW), is a popular welding process known for its speed, efficiency, and ease of use. The process involves feeding a continuous solid wire electrode through a welding gun, along with a shielding gas, to create the weld. MIG welding is widely used in pipe welding for its ability to produce high-quality welds at a fast pace, making it suitable for manufacturing, fabrication, and construction projects that require efficient production and high productivity.
In the context of pipe welding, MIG welding offers several advantages, particularly in applications where speed and automation are paramount. The process excels in welding thicker pipes and components, where the deposition rate and efficiency of MIG welding can significantly reduce welding time and labor costs. Additionally, MIG welding can accommodate a wide range of base materials, including carbon steel, stainless steel, and aluminum, making it a versatile choice for various pipe welding applications.
MIG welding’s ability to create consistent and uniform welds makes it well-suited for mechanized and automated pipe welding processes, where precision and repeatability are essential. This is particularly advantageous in high-volume production environments, such as in the automotive, aerospace, and energy industries, where the reliability and efficiency of the welding process are critical. By leveraging MIG welding for pipe welding, manufacturers and fabricators can achieve high weld quality and productivity while meeting stringent industry standards.
Flux-Cored Arc Welding for Pipe Welding
Flux-cored arc welding (FCAW) is a semi-automatic or automatic welding process that utilizes a tubular electrode with a flux core to produce the weld. The process can be divided into two categories: gas-shielded flux-cored arc welding and self shielded flux cored arc welding, each offering distinct advantages for pipe welding applications. Flux-cored arc welding is known for its high deposition rates, deep penetration capabilities, and suitability for welding thick materials and components, making it a valuable choice for pipe welding in various industries.
When applied to pipe welding, flux-cored arc welding provides several benefits, particularly in scenarios where high welding speeds and efficiency are essential. The process’s ability to operate with higher electrical currents and deposition rates makes it well-suited for welding thicker pipes and components, allowing for rapid production and increased productivity. The deep penetration characteristics of flux-cored arc welding make it suitable for welding in challenging positions, such as vertical and overhead welding, where access and maneuverability may be limited.
Flux-cored arc welding also offers versatility in handling a wide range of base materials, including carbon steel, low-alloy steel, and stainless steel, making it adaptable to diverse pipe welding requirements. The process’s ability to perform well in outdoor and windy conditions, along with its minimal sensitivity to surface contaminants, further enhances its applicability in various pipe welding environments. By leveraging the advantages of flux-cored arc welding, welders and fabricators can achieve efficient and high-quality welds in pipe welding applications.
Submerged Arc Welding for Pipe Welding
Submerged arc welding (SAW) is a welding process that utilizes a granular flux and a continuous wire electrode to create the weld. The process involves submerging the arc and the welding area beneath a layer of granular flux, providing a protective environment that shields the weld from atmospheric contamination. Submerged arc welding is known for its high deposition rates, deep penetration capabilities, and suitability for welding thick materials, making it a preferred choice for pipe welding in industries such as shipbuilding, construction, and heavy equipment manufacturing.
In the context of pipe welding, submerged arc welding offers several advantages, particularly for welding large-diameter pipes and components that require high productivity and efficient weld quality. The process’s ability to operate with high welding currents and deposition rates allows for rapid and cost-effective production, making it suitable for high-volume pipe fabrication and manufacturing. Submerged arc welding can produce deep penetration welds with minimal spatter and fume generation, resulting in clean and high-quality welds that meet stringent industry standards.
Submerged arc welding’s suitability for mechanized and automated welding processes makes it well-suited for pipe welding applications where precision, consistency, and productivity are paramount. By leveraging the process’s ability to produce uniform and reliable welds, manufacturers and fabricators can achieve efficient and high-quality production of welded pipes, ensuring the integrity and performance of the welded components. Submerged arc welding’s versatility and efficiency make it a valuable asset in the realm of pipe welding, meeting the demands of various industrial applications.
Choosing the Right Welding Process for Specific Pipe Materials
Selecting the appropriate welding process for specific pipe materials is crucial for achieving high-quality and reliable welds. Different pipe materials, such as carbon steel, stainless steel, and non-ferrous alloys, require tailored welding approaches to ensure the integrity and performance of the welded joints.
By understanding the characteristics and considerations associated with each pipe material, welders can make informed decisions when selecting the most suitable welding process for their pipe welding applications.
Tips for Successful Pipe Welding
Achieving successful pipe welding requires attention to detail, precision, and adherence to best practices. Here are some valuable tips to enhance your pipe welding skills and ensure the quality and integrity of your welded joints:
Clean and Prepare the Weld Area: Properly cleaning and preparing the weld area is essential for achieving high-quality and defect-free welds. Remove any contaminants, rust, or scale from the surfaces to be welded, and ensure proper joint fit-up and alignment to facilitate smooth and uniform welding.
Select the Right Welding Process and Parameters: Choose the appropriate welding process and parameters based on the specific requirements of the pipe material, thickness, and joint configuration. Adjust the welding parameters, such as current, voltage, and travel speed, to achieve optimal weld penetration and fusion.
Maintain Consistent Arc Length and Travel Speed: Maintaining a consistent arc length and travel speed is crucial for producing uniform and sound welds. Control the distance between the electrode and the workpiece while ensuring steady and consistent travel speed to achieve consistent weld bead formation.
Implement Proper Welding Techniques: Employ proper welding techniques, such as weaving or stringer beads, to ensure thorough fusion and penetration throughout the weld joint. Utilize suitable welding positions and techniques to accommodate the specific requirements of the pipe welding application.
Conduct Thorough Visual and Non-Destructive Testing: After completing the welds, conduct thorough visual inspections and non-destructive testing, such as radiographic testing or ultrasonic testing, to assess the quality and integrity of the welded joints. Address any defects or discontinuities to ensure the reliability and performance of the welded pipes.
By implementing these tips and best practices, welders can elevate their pipe welding skills and produce high-quality, durable, and reliable welded joints that meet industry standards and specifications.
Final Thoughts
The world of pipe welding encompasses a diverse array of welding processes, each offering unique characteristics and advantages for specific applications. From the precision of TIG welding to the efficiency of MIG welding and the versatility of flux-cored arc welding, welders have a range of options to meet the demands of pipe welding in various industries. Understanding the intricacies of each welding process, along with the considerations for specific pipe materials, enables welders to make informed decisions and produce high-quality welded joints that meet stringent industry standards.
By honing their skills, leveraging the right welding processes, and adhering to best practices, welders can excel in the art and science of pipe welding, contributing to the fabrication, construction, and maintenance of vital infrastructure and industrial components. As the industry continues to evolve, embracing innovation and mastering the nuances of pipe welding processes will empower welders to meet the dynamic challenges and opportunities of the modern welding landscape. Join us in exploring the possibilities and achievements of pipe welding, where craftsmanship and expertise converge to create enduring and resilient welded structures.