When it comes to high-speed and precision welding, laser welding is the method of choice for many industries. Unlike traditional welding methods, laser welding uses a focused laser beam to join two pieces of metal, making it an incredibly efficient and accurate technique.
In this section, we will take a closer look at the different types of laser welding methods, exploring the various techniques and processes used in this advanced welding technology. By understanding the different types of laser welding, you can make informed decisions about the best welding method for your specific needs.
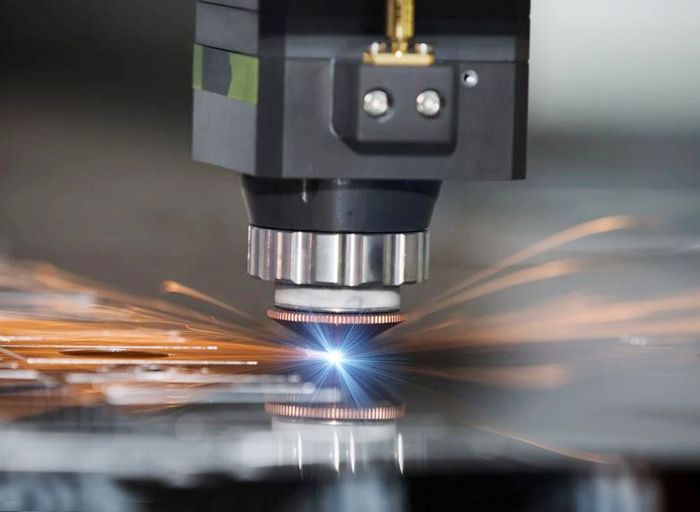
Photos: medicaldevice-network.com
Types of Laser Welding Techniques
Laser welding is a highly versatile technology that offers the ability to produce different types of welds with great precision and accuracy. In this section, we will explore the various types of laser welding techniques and the equipment used to achieve them.
Conduction Laser Welding
This type of welding uses a low-power laser beam to melt the base material and create a weld. It is commonly used for thin materials and requires minimal preparation. It can result in a shallow weld depth and may not be suitable for welding dissimilar metals.
Deep Penetration Laser Welding
As the name suggests, deep penetration welding involves using a high-powered laser beam to create a deeper weld penetration. This technique is ideal for welding thicker materials and can produce high-quality welds in a single pass. However, it requires precise control of the laser beam and is generally more complex and expensive than conduction welding.
Laser Hybrid Welding
This method combines a laser beam with another welding method, such as gas tungsten arc welding or plasma welding. The laser beam can improve the speed and precision of the welding process and can help to reduce defects. Hybrid welding is often used for welding thicker materials and for applications that require high-quality welds.
Laser Cladding
This technique involves using a laser beam to create a layer of material on the surface of a base material. It is commonly used for applications that require wear resistance, corrosion resistance, or the restoration of worn parts. Laser cladding can be used with a wide range of materials, including metals, ceramics, and polymers.
Type of Laser Welding | Advantages | Disadvantages |
---|---|---|
Conduction Laser Welding | Low-cost, minimal preparation required, suitable for thin materials. | Shallow weld depth, may not be suitable for welding dissimilar metals. |
Deep Penetration Laser Welding | Produces high-quality welds in a single pass, suitable for welding thicker materials. | Requires precise control of the laser beam, generally more complex and expensive than conduction welding. |
Laser Hybrid Welding | Improves speed and precision of welding process, can reduce defects, suitable for welding thicker materials. | More complex and expensive than other welding methods. |
Laser Cladding | Creates wear and corrosion-resistant surfaces, can restore worn parts, suitable for a wide range of materials. | May require post-processing, may not be suitable for some applications. |
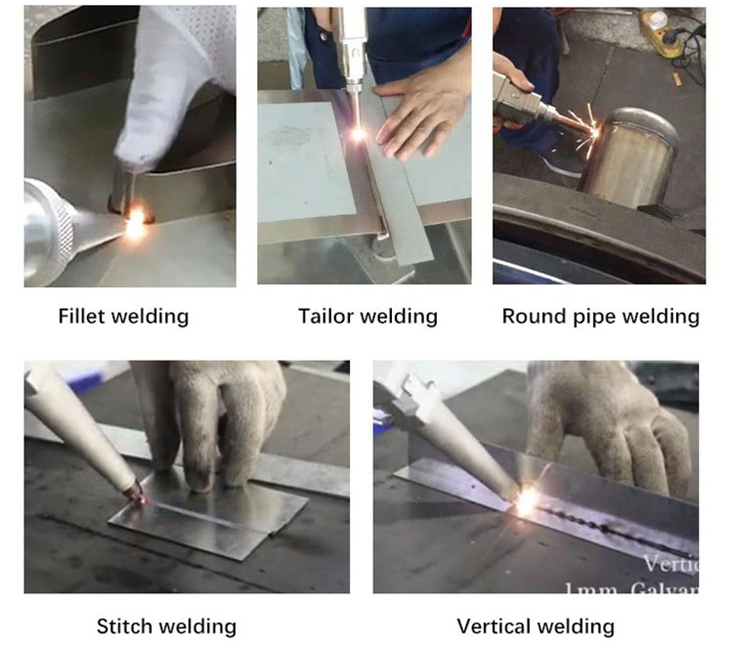
Photos: igolden-cnc.com
“Laser welding technology has revolutionized the welding industry, offering faster, more precise, and efficient welding solutions that can improve the quality and durability of products. “
- There are several different types of laser welding techniques, including conduction welding, deep penetration welding, laser hybrid welding, and laser cladding.
- Each technique has its own advantages and disadvantages, and the choice of technique will depend on the specific requirements of the application.
- Laser welding technology offers numerous benefits over traditional welding methods, including higher precision, faster processing times, and reduced distortion.
Applications and Merits of Laser Welding
Laser welding technology offers numerous advantages over traditional welding methods. Some of the benefits of laser welding include:
- High precision and accuracy, making it ideal for small or intricate parts.
- Minimal distortion of the material and no need for filler material in most cases.
- Reduced heat input, reducing the risk of warping and damage to the material being welded.
- High welding speeds, resulting in increased productivity and lower costs.
- Cleaner welds, with minimal debris and fumes.
Given its many advantages, laser welding technology has wide-ranging applications, including:
Industry | Applications |
---|---|
Automotive | Body-in-white (BIW), powertrain, and suspension systems. |
Medical | Surgical instruments, implants, and medical devices. |
Aerospace | Fuselage, turbine blades, and heat exchangers. |
Electronics | Microelectronics, PCB, and sensor manufacturing. |
Jewelry | Precision welding for jewelry making and repair. |
With such a wide range of applications, laser welding technology has become a preferred welding method across many industries. Its precise and efficient nature has made it an invaluable tool for manufacturing and fabrication processes.
Understanding Laser Welding Processes
When it comes to laser welding, the right equipment is essential for achieving optimal results. Laser welding machines are available in a range of sizes and configurations, each with unique capabilities and features. Here, we’ll take a closer look at the key factors to consider when choosing the right laser welding machine for your specific needs.
Types of Laser Welding Machines
There are two primary types of laser welding machines: pulsed and continuous wave (CW). Pulsed laser welding machines create high-intensity laser pulses that last just a fraction of a second, producing precise and localized welds. CW laser welding machines, on the other hand, emit a continuous laser beam that can be used for a variety of welding applications, including deep penetration and high-speed welding.
The type of laser welding machine you choose will depend on the specific applications and materials you’re working with. For example, pulsed laser welding machines are ideal for welding small, delicate parts, while CW laser welding machines are better suited for larger, thicker materials that require high-speed welding.
Factors to Consider
When selecting a laser welding machine, there are several key factors to consider:
- Power output: The power output of a laser welding machine determines its welding speed and capabilities. Higher power output machines are better suited for thick and dense materials, while lower power output machines are better suited for thinner materials.
- Beam quality: A laser beam’s quality determines its focusability and precise positioning capabilities. Higher beam quality machines are better suited for complex welding projects that require precision and accuracy.
- Welding speed: The welding speed of a laser welding machine is determined by its pulse frequency and power output. Faster welding speeds are ideal for high-production applications.
- Cost: Laser welding machines can be expensive, so it’s important to choose a machine that matches your budget and specific welding needs.
Advantages of Laser Welding Machines
Laser welding machines offer several advantages over traditional welding methods:
- Precision: Laser welding machines produce precise and accurate welds, even on complex surfaces and materials.
- Speed: Laser welding machines can produce high-quality welds at a faster speed than traditional welding methods.
- Cleanliness: Laser welding machines produce clean, spatter-free welds with minimal post-welding cleanup required.
- Versatility: Laser welding machines can be used for a wide range of welding applications, including dissimilar materials and non-metallic materials.
By understanding the different types of laser welding machines and factors to consider, you can choose the right machine for your specific welding needs and achieve optimal results.
Conclusion
Overall, laser welding technology offers a range of benefits and advantages over other welding processes. By using high-powered lasers, laser welding processes can produce strong and precise welds in a variety of materials and applications. Additionally, laser welding machines are highly efficient and can complete welding tasks quickly, which can save time and money.
When choosing the right laser welding method for your application, it’s essential to consider factors like the thickness and type of materials being welded, the required precision, and the welding environment. By understanding these key considerations, you can choose the right laser welding process and equipment to achieve the desired results.
As laser welding technology continues to evolve, we can expect to see even more advancements and improvements to this highly effective welding process. From automotive and aerospace to medical device manufacturing and beyond, laser welding is poised to become an increasingly important part of many industries.
FAQ
What are the different types of laser welding methods?
Laser welding methods include continuous wave (CW) welding, pulsed laser welding, and keyhole welding.
What are the advantages of laser welding?
Laser welding offers precise control, minimal heat input, high welding speeds, and the ability to weld hard-to-reach areas.
What are some common applications of laser welding?
Laser welding is commonly used in industries such as automotive, aerospace, electronics, and medical devices for applications like joining components, sealing, and cutting.
How do laser welding machines work?
Laser welding machines use a high-intensity laser beam to melt and fuse materials together. The laser beam is focused on the joint area, creating a strong and precise weld.