Are you looking to master the art of Tig welding titanium? Look no further! In this article, we will dive into the world of Tig welding and discover the techniques, tips, and tricks you need to know to weld titanium like a pro. With its exceptional strength-to-weight ratio and corrosion resistance, titanium is a popular choice in industries such as aerospace, medical, and automotive. However, welding this fantastic metal comes with its own set of challenges. That’s where Tig welding comes in. Tig welding, also known as Gas Tungsten Arc Welding (GTAW), offers precise control, clean welds, and excellent weld quality when working with titanium.
We will explore the essential equipment and safety precautions you need to consider, as well as the process and best practices for achieving successful Tig welds on titanium. So, if you are ready to take your welding skills to the next level and unlock the potential of titanium.
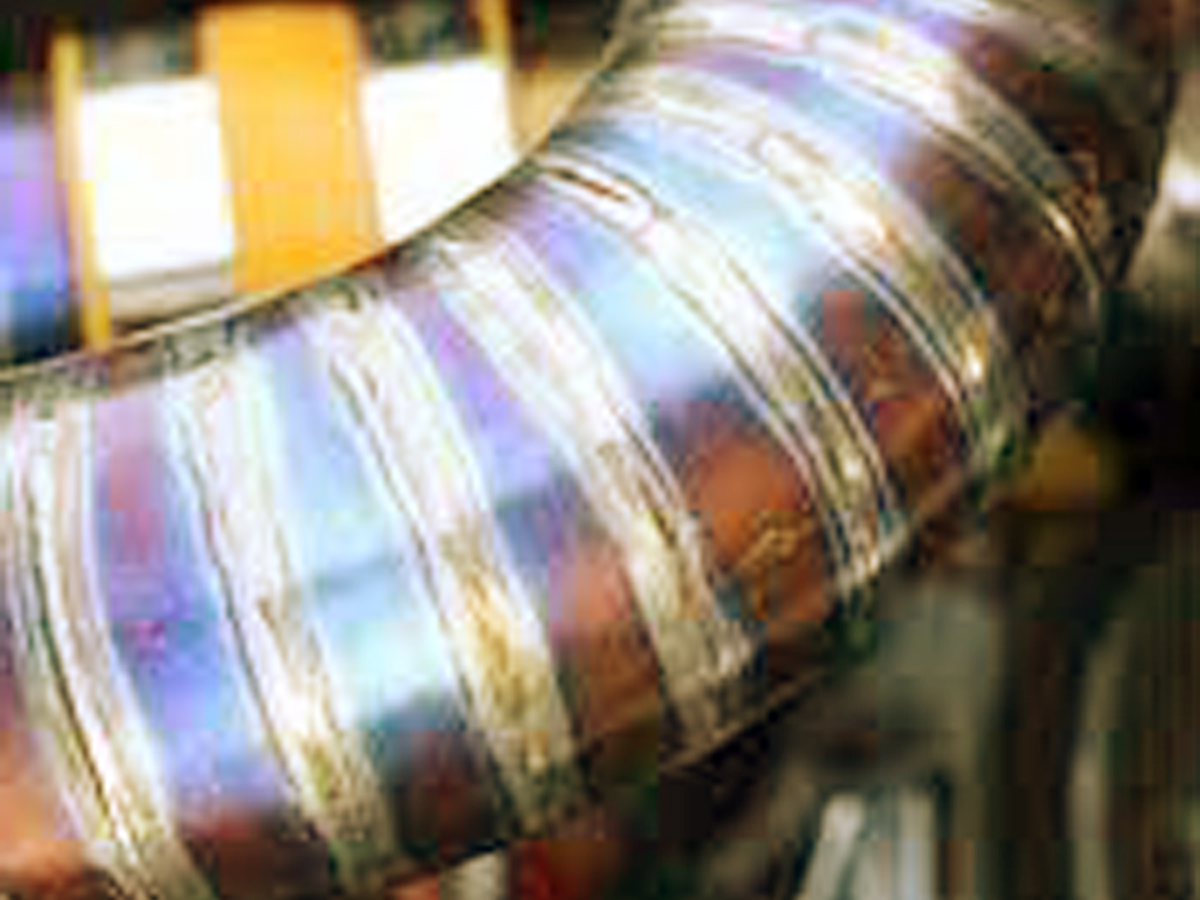
Characteristics of titanium as a welding material
Titanium possesses unique characteristics that make it both challenging and rewarding to weld. Understanding these characteristics is essential for achieving high-quality welds when tig welding titanium.
One of the key characteristics of titanium is its high melting point. Titanium has a melting point of approximately 1,668 degrees Celsius (3,034 degrees Fahrenheit), which is significantly higher than most other metals. This high melting point requires welders to utilize specialized equipment and techniques to generate sufficient heat for the welding process.
Another characteristic of titanium is its high reactivity with oxygen and nitrogen. When exposed to these elements at high temperatures, titanium can form brittle compounds that weaken the weld and reduce its corrosion resistance. It is crucial to protect the weld zone from atmospheric contamination by utilizing effective gas shielding during the welding process.
Titanium also exhibits a unique thermal expansion coefficient. When heated, titanium expands and contracts at a different rate compared to the surrounding materials. This differential expansion can lead to distortion and stress in the welded structure if not properly managed. Therefore, careful consideration must be given to the design and welding techniques to minimize the risk of distortion and ensure the structural integrity of the weld.
Furthermore, titanium has a low thermal conductivity, which means it retains heat more effectively. While this characteristic contributes to the minimal heat input during tig welding, it also requires welders to carefully control the welding parameters to prevent overheating the material. Overheating can lead to grain growth, loss of mechanical properties, and reduced corrosion resistance.
It is also important to note that titanium has a relatively high coefficient of friction compared to other metals. This characteristic can result in increased tool wear during machining and welding processes. Using appropriate cutting tools and techniques can help mitigate these challenges and ensure the successful welding of titanium.
Overall, titanium’s unique characteristics, including its high melting point, reactivity to oxygen and nitrogen, thermal expansion coefficient, low thermal conductivity, and coefficient of friction, require welders to employ specialized techniques and precautions when tig welding titanium. Understanding these characteristics is crucial for achieving high-quality welds with excellent strength, durability, and corrosion resistance.
Advantages of TIG Welding Titanium
One of the key advantages of tig welding titanium is the ability to achieve precise control over the welding process. The technique utilizes a non-consumable tungsten electrode to create the arc, which is then shielded by an inert gas such as argon. This precise control allows welders to create clean and aesthetically pleasing welds with minimal spatter and distortion.
Another advantage of tig welding titanium is the minimal heat input. Titanium has a relatively low thermal conductivity compared to other metals, meaning it retains heat more effectively. This characteristic makes tig welding an ideal choice for titanium, as it reduces the risk of overheating the material and compromising its integrity. The low heat input also helps to minimize distortion, ensuring the welds maintain their strength and structural integrity.
Furthermore, tig welding provides excellent gas shielding, which is crucial when working with titanium. The inert gas, typically argon, creates a protective barrier around the weld pool, preventing oxidation and contamination. Titanium is particularly sensitive to contaminants, such as oxygen and nitrogen, which can weaken the weld and reduce its corrosion resistance. The gas shielding provided by tig welding ensures that the weld remains clean and free from impurities, resulting in high-quality welds with superior strength and corrosion resistance.
Overall, tig welding titanium offers numerous advantages, including precise control, minimal heat input, and excellent gas shielding. These factors contribute to the production of clean, strong, and aesthetically pleasing welds, making tig welding the preferred choice for working with titanium in various industries.
Preparing for Tig welding titanium
Before undertaking tig welding titanium, proper preparation is crucial to ensure successful and high-quality welds. The following preparations should be considered:
Material selection: Choose the appropriate grade of titanium for your specific application. Titanium alloys are classified based on their composition, such as commercially pure (CP) titanium or various grades of titanium alloys. Each grade has its unique properties and characteristics, so it is important to select the right grade that suits your welding requirements.
Material cleaning: Thoroughly clean the titanium material before welding. Titanium is highly sensitive to contamination, so it is essential to remove any dirt, oils, or contaminants from the surface. Use a dedicated titanium cleaning agent or a mixture of acetone and a lint-free cloth to clean the surface. Ensure that the cleaning materials are free from chlorides, as they can adversely affect titanium’s corrosion resistance.
Joint preparation: Proper joint preparation is essential for achieving strong and durable welds. Ensure that the joint edges are clean, smooth, and free from any defects or imperfections. Depending on the joint configuration, you may need to perform edge preparation, such as beveling or chamfering, to achieve proper penetration and fusion during welding.
Fit-up and alignment: Ensure that the joint fit-up and alignment are precise and accurate. Proper fit-up helps maintain consistent heat distribution during welding, minimizing the risk of distortion and ensuring a strong weld. Use clamps or fixtures to secure the joint in the desired position and ensure it remains stable during welding.
Tungsten electrode selection: Select the appropriate tungsten electrode for tig welding titanium. Pure tungsten electrodes are commonly used, as they offer good arc stability and resistance to contamination. However, for improved performance and reduced contamination risk, you can also consider using thoriated or lanthanated tungsten electrodes.
Tungsten electrode preparation: Grind the tungsten electrode to a fine point and ensure it is free from any contamination. Use a dedicated grinder or a diamond wheel to achieve a clean and sharp point. The angle of the tungsten point should be approximately 20 to 30 degrees. Avoid touching the tungsten electrode to the workpiece, as this can contaminate the weld.
Gas shielding: Select the appropriate shielding gas for tig welding titanium. Inert gases, such as argon, are commonly used to provide excellent protection against atmospheric contamination. Ensure that the gas flow rate is adjusted according to the welding machine specifications and the size of the weld.
By properly preparing for tig welding titanium, you can ensure that the welding process goes smoothly and the resulting welds are of high quality. Taking the time to clean the material, prepare the joint, select the appropriate tungsten electrode, and set up the gas shielding will greatly contribute to the success of your welding project.
Safety Precautions for TIG Welding Titanium
As with any welding process, safety should be a top priority when Tig welding titanium. Titanium produces a bright and intense welding arc that emits harmful ultraviolet (UV) radiation. It is crucial to wear appropriate protective gear, including a welding helmet with a shade range suitable for titanium welding. Proper ventilation is essential to prevent the inhalation of fumes and gases generated during the welding process.
Titanium can produce hazardous fumes, such as titanium dioxide, which can have adverse health effects. Therefore, it is crucial to work in a well-ventilated area or use local exhaust ventilation to remove fumes from the welding zone. Taking these safety precautions will ensure your well-being and allow you to focus on achieving high-quality Tig welds on titanium.
Equipment and Materials Needed for TIG Welding Titanium
To Tig weld titanium, you will need specific equipment and materials to ensure successful and efficient welds. Firstly, you will require a Tig welding machine capable of producing a stable and controlled arc. Look for a machine with AC/DC capabilities, as titanium welding typically requires alternating current (AC) to clean the surface of the metal before welding. You will also need a welding torch with a gas lens and a suitable tungsten electrode. When welding titanium, it is recommended to use pure tungsten or a tungsten alloy containing a small percentage of zirconium. These electrodes offer excellent arc stability and minimize the risk of tungsten contamination.
You will need a shielding gas, such as argon, to protect the weld area from atmospheric contamination. Lastly, ensure you have the necessary hand tools, such as wire brushes and clamps, to prepare the metal and hold it in place during welding.
TIG Welding Techniques for Titanium
When Tig welding titanium, it is crucial to follow specific techniques to achieve optimal results. Firstly, ensure the titanium surface is clean and free from any contaminants, such as oil, grease, or oxides. Use a wire brush or a dedicated stainless steel brush to remove any surface impurities. It is also recommended to use a dedicated stainless steel wire brush for titanium to avoid cross-contamination.
Next, establish the correct welding parameters, such as the appropriate welding current, arc length, and travel speed. Titanium requires a higher welding current compared to other metals, so adjust the settings accordingly. Maintain a consistent arc length and travel speed to achieve a uniform weld bead and minimize the risk of overheating the metal.
Additionally, using a slight weaving motion can help distribute the heat evenly and prevent the formation of a narrow and brittle weld bead. Practice these techniques to achieve clean and aesthetically pleasing Tig welds titanium.
Step-by-step process for Tig welding titanium
Tig welding titanium requires a careful and meticulous approach to ensure the production of high-quality welds. The following step-by-step process outlines the key considerations and techniques for tig welding titanium:
Preparation: Begin by thoroughly cleaning the titanium surface to remove any dirt, oils, or contaminants that could compromise the weld quality. Use a dedicated titanium cleaning agent or a mixture of acetone and a lint-free cloth to clean the surface. Avoid using solvents that contain chlorides, as they can be detrimental to titanium’s corrosion resistance.
Selecting the tungsten electrode: Choose a tungsten electrode suitable for tig welding titanium. Pure tungsten electrodes are commonly used for welding titanium, as they offer good arc stability and resistance to contamination. However, for improved performance and reduced contamination risk, you can also consider using thoriated or lanthanated tungsten electrodes.
Setting up the welding machine: Adjust the welding machine settings according to the thickness of the titanium material. Consult the manufacturer’s recommendations for the appropriate amperage, gas flow rate, and tungsten extension for tig welding titanium. Ensure the machine is properly grounded to avoid electrical interference and maintain a stable welding arc.
Shielding gas selection: Select an inert gas, such as argon, for the gas shielding. Argon provides excellent protection against atmospheric contamination and ensures a clean weld pool. Adjust the gas flow rate according to the welding machine specifications and the size of the weld.
Preparing the tungsten electrode: Grind the tungsten electrode to a fine point and ensure it is free from any contamination. Use a dedicated grinder or a diamond wheel to achieve a clean and sharp point. The angle of the tungsten point should be approximately 20 to 30 degrees.
Establishing the arc: Position the tungsten electrode close to the titanium surface, maintaining a consistent and stable arc length. The ideal arc length is typically around 1.5 to 2 times the diameter of the tungsten electrode. Avoid touching the tungsten electrode to the workpiece, as this can contaminate the weld.
Welding technique: Utilize a steady and controlled welding technique when tig welding titanium. Move the torch in a consistent and uniform motion, ensuring even heat distribution along the weld joint. Maintain a consistent travel speed to prevent overheating or underheating the material.
Post-weld cleaning: After completing the weld, allow the titanium to cool naturally. Once cooled, clean the weld area using a dedicated titanium cleaning agent or a mixture of acetone and a lint-free cloth. Remove any discoloration or oxides that may have formed during the welding process.
By following these steps and techniques, you can achieve high-quality welds when tig welding titanium. It is important to practice and refine your technique to become proficient in tig welding titanium and produce welds with excellent strength, durability, and corrosion resistance.
Tips for successful welding titanium
Tig welding titanium requires precision, skill, and attention to detail to achieve successful and high-quality welds. The following tips will help you improve your tig welding technique and ensure successful welding of titanium:
Cleanliness is key: Titanium is highly sensitive to contamination, so it is crucial to maintain a clean work environment. Thoroughly clean the titanium material before welding to remove any dirt, oils, or contaminants. Use dedicated cleaning agents and lint-free cloths to ensure the surface is free from impurities that can compromise the weld quality.
Gas shielding importance: Pay close attention to the gas shielding during tig welding titanium. Inert gases, such as argon, provide excellent protection against atmospheric contamination. Ensure that the gas flow rate is adjusted correctly, and the shielding gas coverage is sufficient to protect the weld pool from oxidation and contamination.
Proper tungsten electrode selection: Choose the appropriate tungsten electrode for tig welding titanium. Pure tungsten electrodes are commonly used, as they offer good arc stability and resistance to contamination. However, thoriated or lanthanated tungsten electrodes can provide improved performance and reduced contamination risk. Experiment with different electrode types to find the one that suits your welding requirements.
Control heat input: Titanium has a relatively low thermal conductivity, so it retains heat more effectively. Control the heat input during welding to prevent overheating and potential damage to the material. Maintain a consistent travel speed and adjust the welding parameters, such as amperage and gas flow rate, to ensure optimal heat control.
Avoid overheating: Overheating titanium can lead to grain growth, loss of mechanical properties, and reduced corrosion resistance. To avoid overheating, use the pulse welding technique, which allows for periods of cooling between welds. This technique helps to dissipate excess heat and maintain the integrity of the titanium structure.
Minimize distortion: Titanium’s unique thermal expansion coefficient can cause distortion and stress in the welded structure. To minimize distortion, use proper joint fit-up and alignment techniques. Secure the joint with clamps or fixtures to maintain stability during welding. Additionally, use appropriate welding techniques, such as back-stepping or stitch welding, to distribute heat evenly and reduce the risk of distortion.
Practice and refine: Tig welding titanium requires practice and refinement of your welding technique. Experiment with different welding parameters, tungsten electrode types, and gas flow rates to find the optimal combination for your specific application. Practice on scrap pieces of titanium to gain confidence and improve your welding skills before working on critical projects.
By implementing these tips and continuously refining your tig welding technique, you can achieve successful and high-quality welds when working with titanium. Remember to prioritize cleanliness, pay attention to gas shielding, select the appropriate tungsten electrode, control heat input, avoid overheating, minimize distortion, and practice regularly to become proficient in tig welding titanium.
Common challenges and Troubleshooting
Tig welding titanium can pose certain challenges due to the unique characteristics of the material. Understanding these challenges and knowing how to troubleshoot them is crucial for achieving successful and high-quality welds. The following are some common challenges in tig welding titanium and their corresponding troubleshooting techniques:
Contamination: Titanium is highly sensitive to contamination, particularly from oxygen and nitrogen. Contamination can weaken the weld and reduce the corrosion resistance of titanium. To minimize contamination, ensure that the welding environment is clean, free from dirt, oils, and other contaminants. Use dedicated titanium cleaning agents and lint-free cloths to clean the material before welding. Additionally, pay close attention to the gas shielding, ensuring a sufficient flow rate and coverage to protect the weld pool from atmospheric gases.
Heat input: Titanium has a low thermal conductivity, meaning it retains heat more effectively. Excessive heat input can lead to overheating, grain growth, and reduced mechanical properties. To control the heat input, adjust the welding parameters such as amperage, travel speed, and pulse settings. Use pulse welding techniques to allow for periods of cooling between welds. This technique helps dissipate excess heat and maintain the integrity of the titanium structure.
Distortion: Titanium’s unique thermal expansion coefficient can cause distortion and stress in the welded structure. To minimize distortion, ensure proper joint fit-up and alignment. Use clamps or fixtures to secure the joint and maintain stability during welding. Employ appropriate welding techniques, such as back-stepping or stitch welding, to distribute heat evenly and reduce the risk
Examples of Applications and Industries That Use TIG Welding Titanium
Tig welding titanium finds its applications in a wide range of industries. In the aerospace industry, titanium is extensively used for aircraft components, including engine parts, landing gear, and structural elements. The medical industry also relies on titanium for implants, such as joint replacements and dental fixtures, due to its biocompatibility and corrosion resistance. The automotive industry utilizes titanium in exhaust systems, suspension components, and lightweight body panels to enhance performance and fuel efficiency. These examples highlight the versatility and importance of Tig welding titanium in various industries.
Conclusion and Final Thoughts
Tig welding titanium offers a precise and clean welding method for joining this remarkable metal. By understanding the properties and characteristics of titanium, following proper safety precautions, and employing the right techniques and best practices, you can achieve exceptional Tig welds on titanium. Whether you are working in the aerospace, medical, or automotive industry, mastering the art of Tig welding titanium will unlock a world of possibilities.
So, equip yourself with the necessary knowledge and skills, and embrace the challenges and rewards of Tig welding titanium. With practice and dedication, you can become a true master of this extraordinary welding process.