Are you looking to expand your welding skills and take on more challenging projects? Tig welding thin sheet metal may seem intimidating, but with the right techniques and equipment, you can achieve seamless results and take your welding to the next level.
In this comprehensive guide, we will explore the specific considerations for Tig welding thin sheet metal. From understanding the welding process and best practices to choosing the right techniques and equipment, we’ve got you covered. Whether you’re a beginner or an experienced welder, you’ll find valuable insights to help you master this specialized skill.
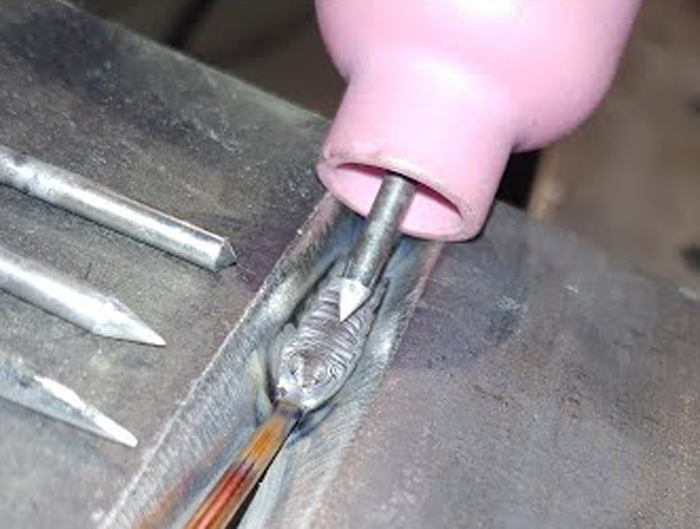
Photos: weldHAGOJIBI
Tig Welding Process for Thin Sheet Metal
If you are looking to master the art of Tig welding thin sheet metal, you need a solid understanding of the Tig welding process. Tig welding is a precise and controlled welding technique that uses a non-consumable tungsten electrode to heat and melt the metal, creating a strong and durable weld.
When working with thin materials or gauge metal, the welding process requires extra care and attention. Here are some essential considerations to keep in mind when Tig welding thin sheet metal:
- Equipment: Use a TIG welder with a low amperage range and a foot pedal for better control. A smaller torch or a gas lens kit can also help achieve better heat control and protect the tungsten electrode from contamination.
- Safety: Always wear the appropriate personal protective equipment, including gloves, a welding helmet, and a welding jacket.
- Tungsten electrode: Use a small diameter tungsten electrode with a pointed or truncated tip. This allows for better heat control and penetration.
- Filler wire: Choose a filler wire that matches the base metal thickness and composition for a strong and compatible weld.
When Tig welding thin sheet metal, it’s crucial to regulate the heat and maintain proper control over the welding process to prevent burn-through or distortion. The thinner the metal, the lower the amperage required. Here are some tips to help you achieve better control:
- Positioning: Keep the torch at a 10-15 degree angle and maintain a consistent distance from the workpiece.
- Pulsing: Use the pulse function on your TIG welder to alternate between high and low amperage. This helps control the heat input and prevent overheating or warping.
- Stitch welding: When welding long seams, consider using a stitch welding technique, which involves welding short sections of the seam before moving onto the next one. This helps prevent burn-through and minimizes distortion.
- Tacking: Use tacks to keep the workpiece in position before welding. This allows for better control and stability during the welding process.
By following these guidelines and practicing your welding skills, you can become proficient in Tig welding thin sheet metal. The next section will cover best practices for achieving high-quality welds on thin sheet metal.
Best Practices for Tig Welding Thin Sheet Metal
Tig welding thin sheet metal requires precision and attention to detail. Follow these best practices to ensure a successful welding process:
- Use the right equipment and tools for the job. Select a TIG welder with high-frequency start and minimum amperage control, and choose a tungsten electrode that matches the thickness and type of metal you’re welding. Use a gas lens to protect the weld area from oxygen and other contaminants, and choose the appropriate filler wire to match the base metal.
- Proper preparation is key. Thoroughly clean the metal surface before welding to remove any contaminants, such as rust, oil, or paint, that can weaken the weld. Use a wire brush or grinder to remove any stubborn residues, and use a degreasing solution to remove any oils or other substances.
- Position the metal carefully. Position the metal at a comfortable angle to reduce the risk of fatigue and ensure that the welding torch is in the correct position. Use a jig or fixture to hold the metal in place if necessary.
- Control heat and speed. Use the right amperage settings and control the foot pedal to avoid overheating the metal. Move the torch slowly to prevent burn-through and ensure that the filler wire melts evenly into the base metal.
- Use the right welding technique. Different welding techniques, such as pulse welding, stitch welding, and tack welding, can be used depending on the project requirements. Experiment with different techniques to find the one that works best for you.
- Practice, practice, practice. Tig welding is a skill that requires practice and patience to master. Start with small projects and work your way up to more complex ones. Don’t be discouraged by mistakes; learn from them and keep improving.
“The key to successful tig welding of thin metal is proper heat control and filler wire feed. Proper positioning is also important to avoid fatigue and ensure a comfortable welding position.”
By following these best practices, you can achieve high-quality welds on thin sheet metal with minimal distortion or damage. Keep refining your skills and techniques, and you’ll soon be a master of tig welding thin sheet metal.
Choosing the Right Welding Techniques for Thin Sheet Metal
When it comes to Tig welding thin sheet metal, choosing the right welding technique is crucial for achieving precise and durable welds. Different welding techniques have their own applications, advantages, and disadvantages. In this section, we will explore some of the most common welding techniques used for thin sheet metal and their specific applications.
Pulse Welding
Pulse welding is a technique that alternates between low and high current pulses. It’s ideal for welding thin sheet metal as it reduces the overall heat input, minimizes distortion and prevents burn-through. This technique is perfect for critical applications in industries such as aerospace and automotive.
Stitch Welding
Stitch welding is a technique used to join two metal pieces intermittently with a series of small welds. It’s often used for lap joints in automotive and sheet metal fabrication. This technique is especially useful for thin sheet metal as it minimizes heat input, reduces warping, and controls distortion.
Tack Welding
Tack welding is a technique that uses small welds to temporarily hold two pieces of metal together. This technique is useful for aligning parts and preparing them for final welds. It’s commonly used in the automotive and shipbuilding industries.
Back Purging
Back purging is a technique that involves protecting the backside of the weld by flowing an inert gas such as argon gas through the back of the weld. This technique is ideal for ensuring clean and high-quality welds, especially for thin sheet metals such as stainless steel.
Ultimately, the right welding technique for thin sheet metal depends on the application, material, and specific requirements of the project. By understanding the different welding techniques available, welders can choose the most appropriate technique to achieve the desired results.
Equipment and Tools for Tig Welding Thin Sheet Metal
When it comes to Tig welding thin sheet metal, having the right equipment and tools is crucial to ensure accuracy, precision, and durability of the weld. The following are essential equipment and tools that you should consider:
Tungsten Electrode
The Tungsten Electrode is an essential part of the Tig welding process. It’s the electrode that creates the arc and conducts the current. When welding thin sheet metal, you should use a smaller diameter Tungsten electrode, typically 1/16″ or 3/32″. Choose a Tungsten electrode that matches the type of metal you are welding.
Gas and Filler Wire
The choice of gas and filler wire is also critical for achieving high-quality welds on thin sheet metal. For welding thin sheet metal, it’s recommended to use a gas mixture of Argon and Helium. The combination of these two gases provides good penetration and a stable arc. As for filler wire, choose a wire that matches the type of metal you are welding.
Welding Torch
The welding torch is the tool that holds the Tungsten electrode and creates the arc. When welding thin sheet metal, you should use a smaller, lighter welding torch that is easy to manipulate and control. Choose a welding torch with a flexible head that can be adjusted to different angles to access hard-to-reach areas.
Gas Lens Collet Body
A gas lens collet body is an essential tool when welding thin sheet metal. It helps to distribute the gas more evenly around the Tungsten electrode, providing better gas coverage and shielding. This results in cleaner, more precise welds. When selecting a gas lens collet body, choose one that matches the diameter of your Tungsten electrode.
Ground Clamp
You will need a good ground clamp to ground the workpiece and complete the electrical circuit. Choose a ground clamp that is large enough to fit securely on the workpiece, yet small enough to be easily positioned. A good ground connection is essential to ensure consistent and high-quality welds.
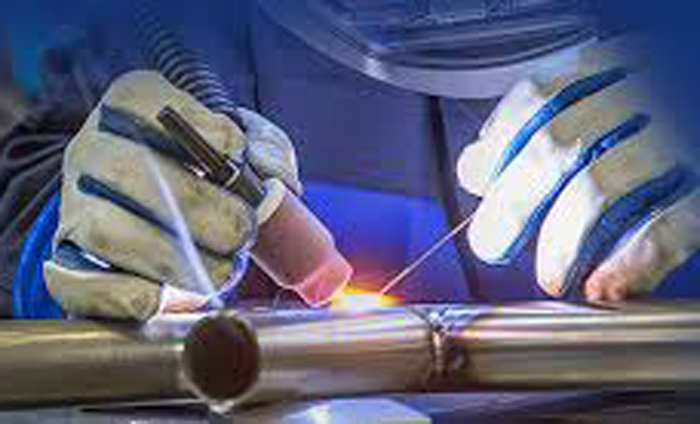
Photos: weldclass.com.au
Tig Welding Thin Sheet Metal Settings
Tungsten Inert Gas (TIG) welding is one of the most versatile welding techniques that can be used to weld thin sheet metal. However, the process can be challenging, especially for beginners who are not familiar with the setup process. Whether you’re a professional welder or a DIY enthusiast, setting up your TIG welding equipment for thin sheet metal welding can be an intimidating task. But worry not, in this blog post, we’ll provide a comprehensive guide to help you set up your TIG welding equipment for thin sheet metal welding.
Choose the Right TIG Welder
Choosing the right TIG welder for thin sheet metal welding depends on the thickness of the material you plan to weld. For welding sheet metal of up to ⅛ inches, a machine with a rating of 150 to 200 amps is recommended. For thinner sheet metal, a machine with a lower amperage rating will suffice. An AC/DC TIG welder is ideal for welding aluminum sheet metal while a DC-only TIG welder is suitable for mild steel sheet metal welding.
Choose the Right Tungsten Electrode
Selecting the right tungsten electrode is a crucial step in TIG welding thin sheet metal. Use 1/16 inch or smaller tungsten electrodes for sheet metal that is ⅛ inch or less. For sheet metal below 1/16 inch thickness, use 0.040 inch tungsten electrode. The tungsten electrode type will also depend on the material you’re welding. For aluminum sheet metal welding, a pure tungsten electrode is recommended. While for steel sheet metal welding, a tungsten electrode with a small amount of thorium or zirconium is ideal.
Set the Gas Flow Rate
The gas flow rate is vital for a successful TIG welding process. You need to select the right gas and flow rate to ensure adequate gas coverage over the weld zone. For sheet metal welding, a flow rate of 10 to 15 cubic feet per hour (CFH) is recommended. The gas also needs to be clean and dry to avoid contamination.
Prepare the Sheet Metal
Before welding, ensure that the sheet metal is clean and free of any contaminants such as rust, oil, or paint. Use a grinder or sandpaper to remove any rust present, and wipe the metal surface clean with a degreaser. The sheet metal should be clamped to a welding table or fixture to prevent any movement during the welding process.
Set the Welding Parameters
Setting the welding parameters is the final step in preparing for TIG welding thin sheet metal. The parameters will vary, depending on the type and thickness of metal you’re welding. For instance, thinner sheet metal requires lower amps and shorter arc lengths than thicker sheet metal. Adjust the amperage, arc length, and travel speed to the recommended specifications for your project.
Preparing Thin Sheet Metal for Tig Welding
Before you start Tig welding thin sheet metal, it’s crucial to prepare the metal properly. Adequate preparation will ensure that your welding project results in seamless and high-quality welds. In this section, we will cover some of the best practices for preparing thin sheet metal for Tig welding.
Cleaning and Removing Contaminants
The first step in preparing thin sheet metal for Tig welding is to clean and remove all contaminants on the surface. This will help to prevent weld defects and ensure proper adhesion. Solvents such as acetone or alcohol can be used to clean the surface of the metal. Ensure that all oil, grease, and other dirt are removed, as they can cause porosity in the welds.
Choosing the Right Joint Design
The joint design is another critical factor that affects the quality of the weld. For thin sheet metal, lap joints or butt joints without filler metal are often used. The joint should be tight to prevent gaps that can cause burn-through during welding.
Using Proper Clamping Techniques
Thin sheet metal can be easily warped or distorted during the welding process. To prevent this, it’s essential to use proper clamping techniques. Clamps with copper or aluminum jaws are ideal, as they won’t leave marks on the metal. Welding magnets can also be used to hold the metal in place.
Choosing the Right Tungsten Electrode
The type of Tungsten electrode you choose for your welding project can significantly impact the quality of the weld. For thin sheet metal, a pointed Tungsten electrode is typically the best choice.
Controlling Heat Input
One of the most challenging aspects of Tig welding thin sheet metal is controlling the heat input. Too much heat can cause warping and burn-through, while too little heat can result in insufficient penetration. To achieve the right balance, it’s recommended to use low amperage and high travel speed.
By following these best practices for preparing thin sheet metal for Tig welding, you will be able to achieve high-quality welds with minimal distortion or damage.
Overcoming Common Challenges in Tig Welding Thin Sheet Metal
While Tig welding thin sheet metal can produce seamless results, it can also present unique challenges that require specific troubleshooting techniques. As you gain experience and confidence in your welding skills, you may encounter some of the following issues:
Burn-Through
Burn-through occurs when the heat generated by the weld puddle penetrates the sheet metal too deeply, causing a hole to form. To prevent burn-through, try using a lower amperage setting or reducing the travel speed. You can also try welding in small sections, allowing each area to cool before moving on to the next.
Warping
Warping can occur when the heat generated by the weld causes the sheet metal to expand and contract unevenly. To prevent warping, try alternating your welding direction or using a tack weld technique to secure the metal in place before making the final weld. You can also try clamping the metal to prevent movement during welding.
Porosity
Porosity occurs when gas becomes trapped in the weld puddle, resulting in small holes or voids. To prevent porosity, ensure your gas flow and coverage are adequate, and your weld surface is free of rust, oil, or other contaminants. You can also try increasing your amperage or adjusting your welding angle to reduce the amount of gas trapped in the weld puddle.
Tip: Always refer to the manufacturer’s instructions for your welding equipment and materials for specific troubleshooting techniques and recommendations.
By understanding these common challenges and practicing the appropriate solutions, you can overcome these obstacles and achieve high-quality welds on thin sheet metal. Remember to stay patient and take your time to ensure precision and accuracy in your welding techniques.
Overcome common challenges
To overcome common challenges, such as preventing burn-through and dealing with warpage, use practical solutions and troubleshooting techniques. Remember, mastering the art of Tig welding thin sheet metal takes practice, so keep at it and continue to refine your skills.
So, whether you’re a beginner or an experienced welder, use the knowledge and techniques outlined in this guide to elevate your skills and achieve seamless results in sheet metal welding. Start Tig welding thin sheet metal today!
Choose the right welding technique
When choosing the right welding technique, consider the application and scenario, and explore various methods such as pulse welding, stitch welding, and tack welding.
Be sure to select the right equipment and tools for Tig welding thin sheet metal, including Tungsten electrodes, gas, and filler wire. Proper preparation is also key, from cleaning and removing contaminants to choosing the right joint design.
Final Thoughts
Tig welding thin sheet metal is a specialized skill that requires knowledge of the welding process, best practices, techniques, and equipment. With the right approach, you can achieve exceptional results on thin sheet metal projects and overcome common challenges that may arise.
Remember to start by understanding the Tig welding process for thin sheet metal, including the equipment required and safety precautions to take. From there, practice best practices for Tig welding, including proper preparation, positioning, heat, and speed control.
FAQ
What is Tig welding?
Tig welding, also known as Tungsten Inert Gas welding, is a welding process that uses a non-consumable tungsten electrode to create the weld. The weld area is protected from atmospheric contamination by an inert shielding gas, typically argon.
Can Tig welding be used on thin sheet metal?
Yes, Tig welding can be used on thin sheet metal. However, it requires careful control of heat and skillful technique to prevent distortion or burn-through.
What are some tips for Tig welding thin sheet metal?
Some tips for Tig welding thin sheet metal include using a lower amperage, keeping a short arc length, moving quickly to prevent excessive heat buildup, and using a smaller filler rod for better control.
What are the different welding techniques for thin sheet metal?
Some common welding techniques for thin sheet metal include pulse welding, stitch welding, and tack welding. These techniques offer different advantages depending on the specific project requirements.
What equipment and tools are needed for Tig welding thin sheet metal?
The equipment and tools needed for Tig welding thin sheet metal include a Tig welding machine, a suitable Tungsten electrode, shielding gas (typically argon), filler wire, a welding helmet, gloves, and safety gear.
How should I prepare thin sheet metal before Tig welding?
Before Tig welding thin sheet metal, it’s important to clean the surface, remove any contaminants, and ensure a proper joint design. This will help promote better weld quality and reduce the risk of defects.
What are some common challenges in Tig welding thin sheet metal?
Some common challenges in Tig welding thin sheet metal include burn-through, warpage, and difficulty in controlling heat. These challenges can be overcome by adjusting welding parameters and using proper techniques.