Welding is a fascinating skill that requires a lot of patience, technique, and practice to master. Tungsten Inert Gas (TIG) welding is a popular welding technique that is widely used in the welding industry. TIG welding is particularly useful when it comes to welding stainless steel pipes. Stainless steel pipes are commonly used in many industries, from pharmaceuticals to food processing. Welding these pipes can be a challenging task, especially for beginners.
In this article, we will cover some tips and techniques that will help you master the art of TIG welding stainless steel pipes. Whether you are a beginner or an experienced welder, these tips will help you improve your skills and produce high quality welds. So, let’s dive in and explore the world of TIG welding stainless steel pipes.
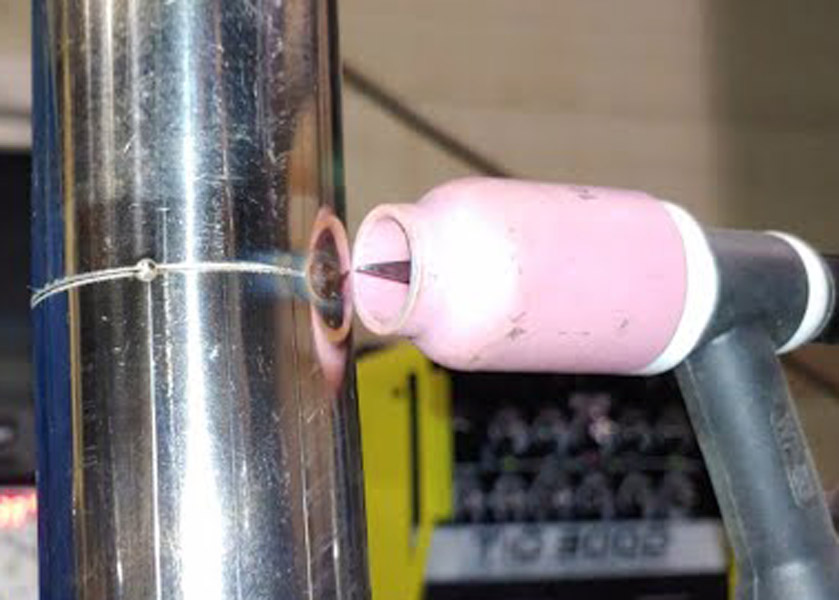
Photo by weldHAGOJIBI on YT
Understanding stainless steel pipes
Before we dive into the tips and techniques for TIG welding stainless steel , it’s important to understand the material you are working with. Stainless steel is a type of steel that contains at least 10.5% chromium, which gives the steel its unique properties. Stainless steel is highly resistant to corrosion, making it ideal for use in harsh environments. Stainless steel pipes are commonly used in industries project such as pharmaceuticals, food processing, and oil and gas companies.
There are different grades of stainless steel, and each grade has its own unique properties. The most commonly used grades of stainless steel for pipes are 304 and 316. Grade 304 stainless steel is a basic austenitic stainless steel that contains 18% chromium and 8% nickel. Grade 316 stainless steel is a higher-grade austenitic stainless steel that contains 16% chromium, 10% nickel, and 2% molybdenum.
Grade 316 stainless steel is more resistant to corrosion than grade 304, making it ideal for use in more corrosive environments. When welding stainless steel pipes, it’s important to know the grade of the stainless steel that you are working. Different grades of stainless steel require different welding techniques and procedures.
Differences between TIG welding and other welding techniques
TIG welding is a welding technique that uses a tungsten electrode to create an electric arc. The arc creates heat, which melts the base metal and filler metal to create a weld. TIG welding is different from other welding techniques because it uses a non consumable tungsten electrode, which means the electrode doesn’t melt during the welding process. TIG welding requires a shielding gas, typically argon, to protect the weld from contamination.
Other welding techniques, such as MIG welding and stick welding, use consumable electrodes that melt during the welding process. MIG welding uses a wire electrode that is fed through a welding gun and melted to create a weld. Stick welding uses a stick electrode that is coated in flux and melted to create a weld. Unlike TIG welding, MIG welding and stick welding do not require a separate shielding gas because the wire or stick electrode has a flux coating that protects the weld from contamination.
TIG welding is a precise welding technique that produces high quality welds. TIG welding is particularly useful when welding thin materials, such as stainless steel pipes.
Advantages of TIG welding stainless steel pipes
TIG welding has several advantages when it comes to welding stainless steel pipes. First, TIG welding produces high quality welds that are free from defects, such as porosity and undercutting. Second, TIG welding allows for precise control of the heat input, which is important when welding thin materials. Third, TIG welding produces a narrow, focused arc that allows for precise welding in tight spaces.
Another advantage of TIG welding stainless steel pipes is that it produces a clean, aesthetically pleasing weld. TIG welding produces a small, precise weld bead that blends in with the surrounding material. This is important when welding stainless steel pipes for industries such as food processing and pharmaceuticals, where a clean, hygienic weld is essential.
Preparation for TIG welding stainless steel
Before you begin TIG welding stainless steel pipes, there are several steps you need to take to prepare. First, you need to ensure that your work area is clean and free from any contaminants that could affect the quality of your weld. Second, you need to ensure that your welding equipment is in good working order and that you have all the necessary tools and materials.
To prepare for TIG welding stainless steel pipes, you will need the following tools and materials:
- TIG welding machine
- Tungsten electrode
- Argon shielding gas
- Filler rod (if needed)
- Welding helmet
- Welding gloves
- Welding jacket or apron
- Wire brush
- Grinding wheel
Once you have all the necessary tools and materials, you can begin preparing the stainless steel pipes for welding. The first step is to clean the pipes thoroughly to remove any dirt, grease, or other contaminants. You can clean the pipes using a wire brush or a grinding wheel.
Next, you need to ensure that the pipes are properly aligned and held securely in place. This can be done using clamps or magnets.
Tips for setting up your TIG welder
Setting up your TIG welding equipment correctly is essential for producing high quality welds. Here are some tips for setting up your TIG welding equipment:
Choose the correct tungsten electrode: The tungsten electrode you choose will depend on the thickness of the stainless steel pipe you are welding. A general rule of thumb is to use a tungsten electrode that is one size smaller than the thickness of the material you are welding.
Choose the correct filler rod: If you need to use a filler rod, choose a rod that is the same grade as the stainless steel you are welding.
Set the correct amperage: The amperage you use will depend on the thickness of the stainless steel pipe you are welding. A general rule of thumb is to use 1 amp of welding current for every 0.001 inch of material thickness.
Set the correct shielding gas flow rate: The shielding gas flow rate you use will depend on the diameter of the tungsten electrode you are using. A general rule of thumb is to use a flow rate of 15-20 cubic feet per hour (CFH) for a 1/16 inch tungsten electrode, and 20-25 CFH for a 3/32 inch tungsten electrode.
Keep your tungsten electrode sharp: A sharp tungsten electrode will produce a more precise arc, which will result in a better quality weld. You can sharpen your tungsten electrode using a dedicated tungsten grinder or a grinding wheel.
Techniques for TIG welding stainless steel pipes
TIG welding stainless steel pipes requires a specific set of techniques to produce high quality welds. Here are some techniques to keep in mind:
Maintain a consistent arc length: The distance between the tungsten electrode and the workpiece should be consistent throughout the welding process. A consistent arc length will produce a more precise weld.
Use a weaving motion: When welding stainless steel, it’s important to use a weaving motion to distribute the heat evenly. Start on one side of the pipe and weave back and forth across the joint.
Watch your travel speed: Travel speed refers to the speed at which you move the TIG torch along the joint. A slower travel speed will produce a wider weld bead, while a faster travel speed will produce a narrower weld bead.
Use the correct filler rod technique: If you need to use a filler rod, use a technique called “stacking dimes.” This involves dipping the filler rod into the weld pool and quickly pulling it out to create a series of small “dime” shapes along the weld bead.
Common mistakes to avoid when TIG welding stainless steel pipes
TIG welding stainless steel pipes can be challenging, especially for beginners. Here are some common mistakes to avoid:
Using too much heat: Using too much heat can cause the stainless steel to warp or distort, which can affect the quality of the weld.
Not cleaning the workpiece thoroughly: Failing to clean the workpiece thoroughly can result in a contaminated weld that is prone to defects.
Not using the correct tungsten electrode: Using the wrong tungsten electrode can result in a poor-quality weld.
Not using the correct filler rod: Using the wrong filler rod can result in a weld that is prone to cracking or corrosion.
Not maintaining a consistent arc length: Failing to maintain a consistent arc length can result in a weld that is uneven or has a poor appearance.
Troubleshooting TIG welding issues
Even with the best techniques and equipment, TIG welding stainless steel pipes can sometimes result in issues. Here are some common issues and how to troubleshoot them:
Porosity: Porosity refers to small holes or voids in the weld. Porosity can be caused by a contaminated workpiece or a shielding gas flow rate that is too low. To fix porosity, clean the workpiece thoroughly and increase the shielding gas flow rate.
Undercutting: Undercutting refers to a groove that is melted into the base metal at the joint. Undercutting can be caused by using too much heat or a travel speed that is too slow. To fix undercutting, reduce the heat input and increase the travel speed.
Cracking: Cracking can occur if the weld is too hot or if the wrong filler rod is used. To prevent cracking, use the correct filler rod and reduce the heat input.
Distortion: Distortion refers to the warping or bending of the workpiece during welding. Distortion can be caused by using too much heat. To prevent distortion, use the correct heat input and clamp the workpiece securely in place.
Best practices for TIG welding stainless steel
To produce high quality welds when tig welding stainless steel pipes, it’s important to follow some best practices:
- Clean the workpiece thoroughly before welding.
- Use the correct tungsten electrode and filler rod for the grade of stainless steel you are welding.
- Maintain a consistent arc length and travel speed.
- Use a weaving motion to distribute the heat evenly.
- Keep your tungsten electrode sharp.
- Use a shielding gas flow rate of 15-25 CFH.
- Use the stacking dimes technique when using a filler rod.
Following these best practices will help you produce high quality welds when welding stainless steel pipes.
Conclusion and next steps for mastering TIG welding skills
TIG welding stainless steel can be a challenging task, but with the right techniques and equipment, you can produce high quality welds that meet industry standards. Understanding the material you are working with, choosing the correct equipment, and following best practices will help you improve your TIG welding skills and produce high quality welds.
If you are interested in mastering TIG welding skills, consider taking a welding course or practicing on scrap materials. With practice and patience, you can become a skilled TIG welder and produce high quality welds that meet the demands of the welding industry.