Tig welding copper is a specialized skill that requires precision and expertise. Whether you are a seasoned professional or just starting out in the field of welding, mastering the art of Tig welding copper can open up new opportunities and enhance your career prospects. This comprehensive guide will provide you with all the information you need to successfully weld copper using the Tig welding technique. From understanding the properties of copper to selecting the right equipment and techniques, this guide covers it all. So, if you are looking to take your welding skills to the next level and become a master of Tig welding copper, keep reading!
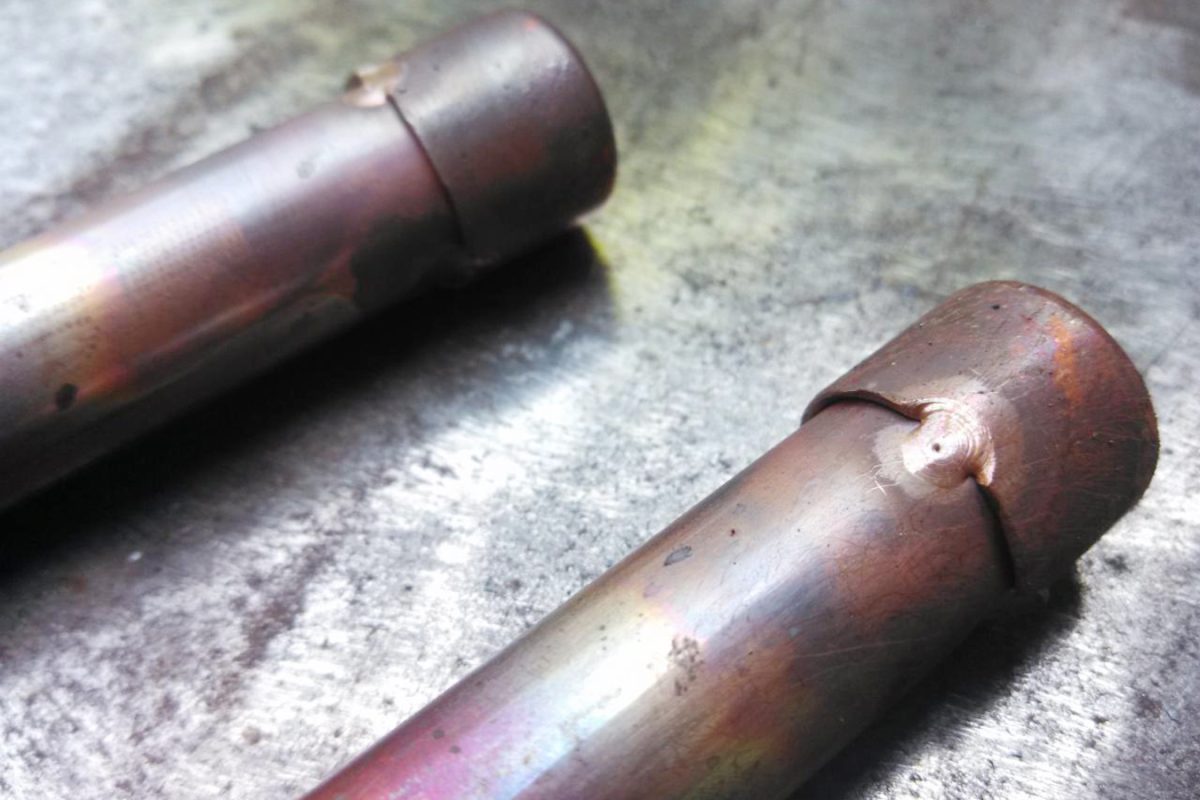
Image by everlastgenerators
Importance of Tig welding copper in the industry
Tig welding copper is an essential skill for professionals in various industries. Copper, known for its excellent conductivity and corrosion resistance, is widely used in electrical and plumbing applications, as well as in the aerospace and automotive industries. Mastering the art of Tig welding copper allows professionals to create strong and durable joints that can withstand extreme conditions.
One of the key reasons why Tig welding copper is important in the professional industry is its ability to ensure high-quality and reliable connections. The precise control and low heat input of the Tig welding process result in clean and aesthetically pleasing welds, making it ideal for applications where appearance is crucial. Tig welding copper offers increased efficiency and cost-effectiveness. By using the appropriate techniques and equipment, professionals can minimize material waste and reduce the need for expensive rework.
The unique properties of copper for successful welding
Understanding the unique properties of copper is crucial for successful Tig welding. Copper is known for its high thermal and electrical conductivity, as well as its excellent corrosion resistance. These properties make copper a popular choice in various industries. When welding copper, it is important to consider its high thermal conductivity. Copper conducts heat rapidly, which can result in heat dissipation and difficulties in achieving proper fusion. To overcome this, professionals must adjust their welding techniques to compensate for the rapid heat transfer.
Additionally, copper has a higher melting point compared to other metals commonly welded. This requires precise control of the welding parameters, such as heat input and welding speed, to prevent overheating and ensure proper fusion. Copper oxide forms quickly on the surface of copper, which can make welding challenging. Thorough cleaning and proper shielding gas selection are essential to prevent oxidation and ensure clean welds.
Tools and equipment for Tig welding copper
To successfully Tig weld copper, professionals must have the right tools and equipment at their disposal. Here are the essential items needed for a seamless copper welding experience:
a. Tig Welder: Invest in a high-quality Tig welder that offers precise control over the welding parameters such as heat input, amperage, and pulse settings. Look for a welder with adjustable settings specifically designed for welding copper.
b. Tungsten Electrodes: Choose thoriated or ceriated tungsten electrodes to achieve optimal results while welding copper. These electrodes offer excellent arc stability and performance, ensuring clean and consistent welds.
c. Torch: Opt for a Tig torch with the flexibility to accommodate different sizes of copper electrodes. The torch should also have a comfortable grip and precise control for an accurate and steady welding process.
d. Filler Rods: Select copper filler rods that match the composition of the base metal, ensuring a stronger and more durable weld. Copper filler rods typically come in various diameters to suit different welding applications.
e. Gas and Flow Meter: Use a shielding gas, such as argon, to prevent oxidation and ensure a clean weld. Invest in a reliable flow meter to accurately regulate the gas flow during welding, maintaining a consistent and proper shield around the welding area.
f. PPE (Personal Protective Equipment): Safety should always be a priority. Wear heat-resistant gloves, a welding helmet with a proper lens shade, long-sleeved clothing, and leather boots to protect yourself from potential hazards and injuries.
By having the right tools and equipment, professionals can tackle any Tig welding project involving copper with confidence. These essential items will enable precise control, clean welds, and ultimately help in mastering the art of Tig welding copper effectively.
Step-by-step guide of Tig welding copper
Now that you have the essential tools and equipment for Tig welding copper, let’s delve into a step-by-step guide to help you master this art. Follow these instructions to ensure a seamless welding experience and achieve impeccable results:
Step 1: Prepare the copper surface
Before you start welding, it is crucial to clean the copper surface thoroughly. Remove any dirt, debris, or oxidation using a wire brush or sandpaper. Ensure the surface is smooth and free from contaminants that may affect the welding process.
Step 2: Set up your Tig welder
Refer to the manufacturer’s instructions to set up your Tig welder correctly. Adjust the welding parameters, such as heat input and amperage, based on the thickness and type of copper you are working with. Take note of the recommended settings for welding copper and make the necessary adjustments.
Step 3: Insert and sharpen the tungsten electrode
Insert a tungsten electrode (thoriated or ceriated) into your Tig torch. Use a dedicated tungsten sharpener or grinder to sharpen the electrode to a fine point. Ensure the electrode is securely tightened in the torch holder.
Step 4: Choose the appropriate filler rod
Select a copper filler rod that matches the composition of the base metal. This will provide compatibility and ensure a stronger weld. Use the appropriate rod diameter for the welding application, and have multiple rod sizes on hand for different thicknesses of the copper material.
Step 5: Position and secure the copper pieces
Position and clamp the copper pieces together in the desired welding configuration. Ensure they are firmly secured to prevent movement during the welding process.
Step 6: Begin welding
With the torch in one hand and the filler rod in the other, ignite the arc by lightly tapping the tungsten electrode against the copper surface. Maintain a steady and consistent torch angle, typically around 70 to 80 degrees, and control the speed of your torch movement.
Step 7: Add filler material
As the weld progresses, continuously add filler rod to the joint. Melt the filler rod into the weld puddle while maintaining the desired torch angle and travel speed. This will ensure a clean and uniform weld.
Step 8: Inspect and clean the weld
After completing the weld, inspect it for any defects or flaws. Use a wire brush or a suitable cleaning tool to remove any slag or excess filler material. This will help in achieving a clean and visually appealing weld.
By following these step-by-step instructions, you will be well on your way of Tig welding copper. Practice, patience, and attention to detail are key to honing your skills and achieving exceptional results.
Common challenges and troubleshooting techniques
While Tig welding copper can be a rewarding process, it’s not without its challenges. As a professional welder, you may encounter certain issues that can hinder the quality of your welds. However, knowing how to identify and troubleshoot these challenges will help you overcome them with ease. Here are some common challenges you may face when welding copper and the corresponding troubleshooting techniques:
1. Overheating: Copper has relatively high thermal conductivity, which makes it prone to overheating. If you’re experiencing overheating issues, try reducing your welding current or increasing the travel speed to avoid excessive heat buildup.
2. Fusion issues: Achieving proper fusion between the base metal and filler material is crucial for a strong weld. If you’re not getting sufficient fusion, you may need to increase the heat input or adjust the torch angle to ensure adequate penetration and fusion.
3. Porosity: Copper is susceptible to porosity, which can weaken the weld. To minimize porosity, ensure the copper surfaces are properly cleaned and free from contaminants before welding. Additionally, using high-purity shielding gas, such as argon, and maintaining a consistent arc length can help reduce porosity.
4. Tungsten contamination: Contaminated tungsten can affect the quality of your weld and lead to defects. To avoid tungsten contamination, make sure to use a clean and properly sharpened tungsten electrode. Also, be cautious of accidentally touching the tungsten to the molten copper, which can cause contamination.
By being aware of these common challenges and applying the appropriate troubleshooting techniques, you can overcome obstacles and achieve high-quality welds when working with copper. Remember that practice and experience are vital in becoming a skilled Tig welder, so don’t be discouraged by initial difficulties. Stay focused, keep adapting your techniques, and you’ll soon master the art of Tig welding copper like a pro.
Safety precautions and best practices for professionals
As a professional welder, safety should always be your top priority. When it comes to Tig welding copper, there are specific safety precautions and best practices that you should follow to ensure your well-being and the quality of your work.
First and foremost, it’s crucial to wear the appropriate personal protective equipment (PPE) during the welding process. This includes a welding helmet with a properly shaded lens, gloves that are heat resistant and offer good dexterity, flame-resistant clothing, and safety glasses to protect your eyes from flying sparks and debris.
Copper welding can produce harmful fumes and gases, so it’s important to work in a well-ventilated area or use local exhaust ventilation to remove these contaminants from the air. Additionally, wearing a respiratory mask or a powered air-purifying respirator (PAPR) is recommended to protect yourself from inhaling harmful particles.
Furthermore, be mindful of the risks of electric shock when working with electricity. Inspect all cables and connections regularly to ensure they are in good condition and consider using a ground fault circuit interrupter (GFCI) to minimize the risk of electric shock.
Lastly, maintaining a clean and organized work area is essential for safety. Remove any flammable materials from the vicinity of your welding station and keep a fire extinguisher nearby in case of emergencies.
Conclusion
The article highlights the importance of TIG welding copper and the common challenges that arise during the process. It emphasizes the significance of TIG welding in various industries, particularly when working with copper materials. The article also provides valuable troubleshooting techniques to overcome these challenges effectively.
Overall, TIG welding copper requires precision and expertise, but with the right techniques, it can be accomplished successfully.