Welding is one of the most widely used repair methods. Repairing structures and equipment after natural disasters, accidents, or other damage is just one of the many uses for welding. Spot welding with mig is a great way to repair damaged metal components. Not only can it be done in much less time than other methods of making repairs, but it’s also less expensive than some other options as well. When repairing with welding you have less variables to deal with and are therefore likely to get a better result the second time around. This article will explain everything you need to know about spot welding with MIG and TIG.
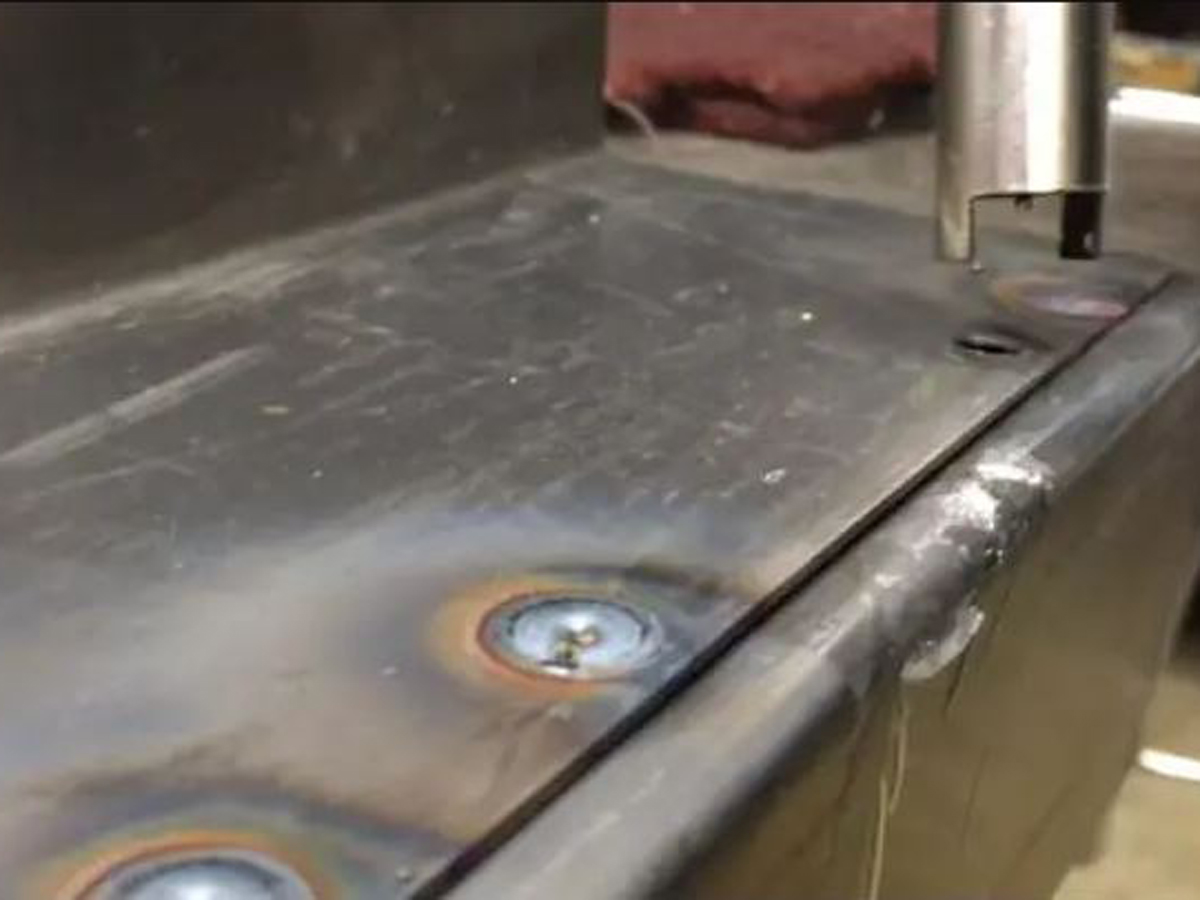
Photo by ZILAwelds
About Spot Welding
Spot welding is a process that joins two pieces of metal together by applying a small amount of welding rod between the surfaces and joining them together. The welding rod is heated, and then directed between the surfaces of the two pieces of metal you are trying to join. Once the welding rod comes into contact with the surface of one of the pieces, it transfers heat to the other piece, melting the metal and creating a strong, reliable joint.
Advantage of Spot Weld
There are several advantages to spot welding that make it both a fast and cost-effective way to repair metal components and machinery.
Simple and Easy Setup – Unlike other welding methods, spot welding doesn’t require special equipment like a welder, torch, or shielded environment. You can do it in your garage or even in your workbench.
Quick Fix – In addition to being quick, spot welding is also fairly forgiving. Spot welds are easy to Patch up so that you can continue using the item if the weld isn’t perfect.
Versatility – Another great thing about spot welding is how versatile it is. You can use it to repair or replace any type of metal, including steel, iron, aluminum, copper, and more.
When Should You Use Spot Weld
Spot welding is a great way to join two pieces of metal, but it shouldn’t be used all the time. You can weld almost any time you have the opportunity, but you should avoid welding when the temperature is too high or too low, the humidity is too high or too low, or there is a great deal of dust in the air. Doing so will greatly increase the chances of an unsuccessful weld. In most cases, you should also avoid welding when it’s windy. While wind does have its advantages, it can also knock over your weld, ruining the job. This can happen even when the welding itself is done properly.
How to Spot Weld with Mig
Mig welding is a type of gas welding that uses a high voltage coil to create a powerful arc. The arc melts the metal and forms a weld at the tip of the electrode. The mig welding torch is powered by an electric arc and uses high volatile gas as a consumable to transfer heat to the workpiece. Mig welding is relatively easy to get started with and doesn’t require any special equipment or tools. It’s also extremely versatile and can be used on a wide variety of materials. These are the steps to mig welding with MIG:
- Attach the MIG welding torch to the welding power source. This could be a battery, wall outlet, or gas supply.
- Connect the torch to the workpiece with a welding cable.
- Hold the torch in the correct position over the workpiece and place the torch tip against the workpiece.
- Turn on the torch and wait for it to heat up.
- Once the torch is hot, start the welding process by depressing the trigger on the torch. The welding cable will be latched onto the torch and will begin to draw current from the torch. Air in the torch will be pushed out through the nozzle and create a plasma arc. Where the plasma arc meets the metal, a chemical reaction begins and heat is transferred through the metal. The metal then begins to melt and produce a weld between the two pieces.
TIG vs. MIG for Spot Welding
There are some clear differences between the two when welding with TIG and MIG.
- TIG can be used on almost any material, while MIG is only used on metals.
- MIG is more versatile, while TIG is limited to only two electrode types.
- TIG is more expensive, while MIG is usually more affordable.
Tips for Successful Spot Welding With MIG
There are some tips for spot welding with mig:
– Welders should use a protective shield to reduce the risk of damage from the arc. A shield can also help keep the welder and workpiece safer from damage.
– When welding, the welding torch operator should ensure the workpiece is held securely.
– Welders should use the correct shielding and power settings to minimize the chance of an unsuccessful weld and damage to the equipment.
– Welders should weld in a well ventilated area.
– Welders should wear proper safety gear such as gloves, safety glasses, and a protective helmet.
– Spot welding is a great option for quick repairs and limited budgets, but when it comes to long-term projects or large structural repairs, you should consider using a more robust method of welding like MIG.
Way to repair metal surfaces
The final verdict is that spot welding with MIG is an effective and fast way to repair metal surfaces. It’s quick and easy to do, and it also doesn’t require any special equipment like a welder or torch. However, spot welding with MIG isn’t designed for long term use and shouldn’t be used in place of MIG welding. It’s also not a good choice for repairing large structural components or for welding metals like steel. That being said, it’s still a great way to quickly and easily repair broken parts and damaged structures.