Spot welding is a most popular technique in the welding industry, especially used for stainless steel. It involves the use of electrical resistance to fuse metal sheets together. Achieving a flawless bond can be quite challenging, especially for beginners. As a skilled assistant in the field of welding, I have had the privilege of helping numerous clients master the art of spot welding for stainless steel. In this content, I will share some practical tips and tricks to help you achieve a perfect spot weld every time.
From selecting the right equipment to preparing your workpiece and setting the right parameters, these tips are guaranteed to take your spot welding game to the next level. So, whether you are a novice welder or a seasoned pro, read on to discover how you can master spot welding for stainless steel like a pro.
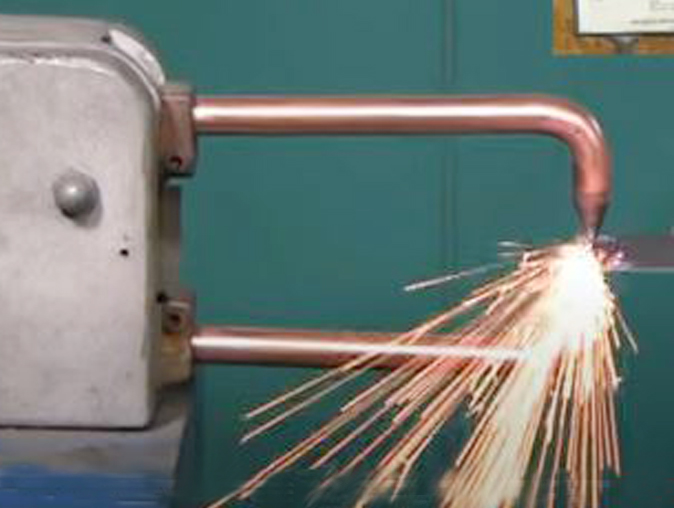
Benefits of Spot Welding for Stainless Steel
Spot welding is an excellent way to join stainless steel sheets due to its many benefits. For starters, it is a quick and efficient process that can produce a high quality bond in a matter of seconds. This is because spot welding uses a concentrated heat source to melt the metal sheets, creating a strong and durable bond. Spot welding is a cost effective method since it requires minimal material and energy input. It is also a cleaner process, producing minimal fumes and debris, making it a safer option for both the welder and the surrounding environment.
Another benefit of spot welding is that it can be used to weld various thicknesses of stainless steel sheets. This makes it a versatile process that can be used in various industries, including the automotive, aerospace, and construction sectors. Spot welding also provides high repeatability, ensuring consistent and precise welds, making it ideal for mass production.
Process of Spot Welding
To master spot welding for stainless steel, it is essential to understand the process involved. Spot welding uses a focused electrical current to create heat, which melts the metal sheets and creates a bond. The process involves three main stages, namely clamp, weld, and hold. In the clamp stage, the metal sheets are held together in position using the welding electrodes. In the weld stage, a high electrical current is passed through the electrodes, creating heat that melts the sheets. In the hold stage, the electrodes hold the metal in place until they cool, forming a solid bond.
To produce a flawless spot weld, the metal sheets must be clean and free from any contaminants such as oil, dirt, or rust. Any impurities on the metal can cause the weld to be weak and brittle, leading to possible failure. The metal must be in good condition, with no cracks, deformations or warping. Any defects on the metal sheets can cause the weld to be uneven, leading to a weak bond.
Choosing the Right Equipment for Welding
Choosing the right spot welding equipment is crucial to achieving a perfect spot weld on stainless steel. The equipment you choose should be suitable for the thickness and type of stainless steel sheets you plan to weld. For instance, thicker sheets may require a higher amperage spot welder to produce a strong bond. The electrodes should be the correct size for the metals, ensuring that they hold the metal sheets firmly in place.
When selecting a spot welding machine, consider its features and capabilities. Look for a machine that has adjustable welding parameters, such as the welding time, current, and pressure. This will allow you to fine-tune the welding process to suit your specific welding needs. Look for a machine that is easy to use and maintain, with a user friendly interface and clear instructions.
Setting up Your Equipment for Welding
Once you have chosen the right spot welding equipment, you need to set it up correctly to produce a flawless spot weld on stainless steel. First, ensure that the electrodes are clean and free from any debris or rust that may affect the welding process. Next, adjust the welding parameters, including the welding time, current, and pressure, to suit the thickness and type of stainless steel sheets you plan to weld. It is also essential to position the electrodes correctly on the stainless steel sheets.
Spot Welding Safety Precautions for Stainless Steel
Spot welding can be a hazardous process, especially when dealing with stainless steel sheets. As such, it is essential to take the necessary safety precautions to protect yourself and those around you. First and foremost, always wear appropriate personal protective equipment (PPE), including eye protection, gloves, and a welding helmet.
Ensure that your spot welding equipment is in good working condition and free from any defects that may cause accidents. Always work in a well ventilated area to prevent exposure to harmful fumes and gases. Finally, keep a fire extinguisher nearby in case of any emergencies.
Tips for Achieving a Flawless Spot Welding for Stainless Steel
Achieving a perfect spot welding for stainless steel requires skill and practice. Here are some tips to help you achieve a flawless bond every time:
Use the correct welding parameters
The welding time, current, and pressure should be adjusted to suit the thickness and type of stainless steel sheets you plan to weld. This will ensure that you produce a strong and durable bond.
Prepare your workpiece properly
The stainless steel sheets should be clean and free from any contaminants such as oil, dirt, or rust. Any impurities on the metal sheets (spot welding sheet metal) can cause the weld to be weak and brittle, leading to possible failure.
Position the electrodes correctly
The position of the electrodes determines the size and shape of the weld, so it is crucial to position them precisely. Ensure that the electrodes are in good condition, with no cracks or deformations, as this can affect the quality of the weld.
Use the correct electrode size and shape
The electrodes should be the correct size and shape for the metal sheets, ensuring that they hold the metal firmly in place during the welding.
Practice, practice, practice
Spot welding requires skill and practice to master. Try practicing on scrap steel sheets before attempting to weld your actual workpiece.
Troubleshooting of Spot Welding for Stainless Steel
Even with the best preparation and equipment, spot welding can sometimes go wrong. Here are some troubleshooting tips to help you identify and fix common spot welding problems:
Weak or brittle welds
.Weak or brittle welds can be caused by using the wrong welding parameters, failing to prepare your workpiece properly, or incorrect electrode positioning. Check and adjust the welding parameters, ensure that the stainless steel sheets are clean and free from any contaminants, and position the electrodes correctly.
Welds that are too small or too large
Welds that are too small or too large can be caused by incorrect electrode positioning or using the wrong electrode size and shape. Position the electrodes correctly and use the correct electrode size and shape.
Uneven welds
Uneven welds can be caused by using the wrong welding parameters or incorrect electrode positioning. Check and adjust the welding parameters and position the electrodes correctly.
Final Thughts
Spot welding for stainless steel is a versatile and efficient method of joining metal sheets. To achieve a flawless spot weld, it is crucial to choose the right equipment, prepare your workpiece properly, and set the correct welding parameters. Additionally, take the necessary safety precautions to protect yourself and those around you. With practice and patience, you can master spot welding for stainless steel and produce high-quality welds every time.