Introducing the precision and artistry behind spot welding in automotive assembly! As the automotive industry continues to innovate, spot welding plays a crucial role in assembling vehicles with unparalleled strength and durability. Utilizing advanced technology and skilled craftsmanship, spot welding ensures that every vehicle is built to withstand the test of time.
In the world of automotive engineering, spot welding is more than just a process; it’s the fusion of science and skill. This article delves into the intricate process of spot welding cars, exploring the cutting-edge techniques that bring vehicles to life. From the seamless joining of metal sheets to the meticulous quality control procedures, every step reflects a commitment to excellence.
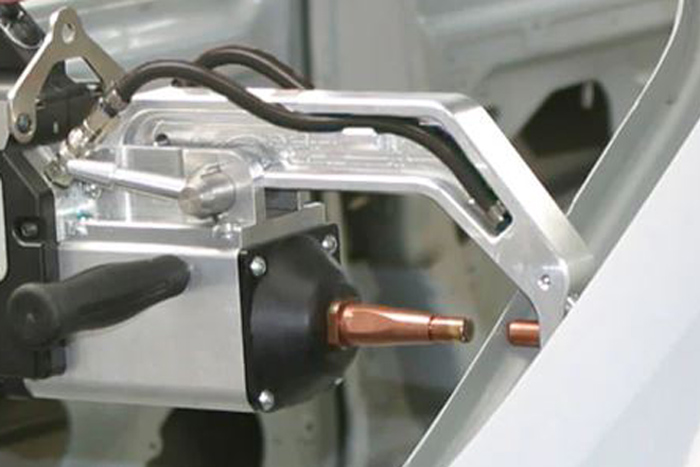
Image: basicwelding.co.uk
Spot Welding in Car Manufacturing
Spot welding is a process used to join overlapping metal sheets by applying pressure and heat to the weld area. In the automotive industry, this method is widely employed to assemble car body components, such as panels, frames, and structural parts. The precision and strength of spot welds are essential for ensuring the structural integrity and safety of vehicles. This process involves the use of specialized equipment and skilled operators to create high-quality, durable welds that meet stringent industry standards.
The fundamental principle of spot welding involves passing an electric current through the metal sheets to be joined, generating heat at the contact points. The heat softens the metal, allowing it to fuse together under pressure, forming a secure bond. This technique offers several advantages, including speed, efficiency, and the ability to create consistent and reliable welds. As automotive manufacturers strive for lightweight yet robust designs, spot welding has become indispensable for producing vehicles that excel in both performance and safety.
Spot welding is a highly controlled process that requires precise parameters for current, pressure, and duration to achieve optimal results. The weld nugget, the area where the metal sheets are fused, must meet specific size and strength criteria to ensure the integrity of the joint. Additionally, factors such as material thickness, surface condition, and electrode design play crucial roles in determining the quality of spot welds in car manufacturing.
Advantages of Spot Welding Car Manufacturing
Spot welding offers several distinct advantages that make it a preferred method for joining metal sheets in car manufacturing. One of the primary benefits is the speed and efficiency of the process, allowing for high-volume production with minimal cycle times. This rapid assembly capability is essential for meeting the demands of modern automotive production, where precision and productivity are paramount.
Another advantage of spot welding is its ability to create strong, reliable welds without the need for additional materials such as filler metal or fasteners. The welded joints exhibit excellent structural integrity, contributing to the overall durability and safety of vehicles. This method also produces clean and neat welds, minimizing the need for extensive post-welding finishing or cleanup, which streamlines the manufacturing process and reduces production costs.
In addition to its speed and strength, spot welding is well-suited for automating production lines, offering consistent and repeatable results. Automation ensures that welds are performed with precision and accuracy, contributing to the overall quality and uniformity of car body assembly. The heat-affected zone in spot welding is localized, minimizing distortion and preserving the material properties, which is crucial for maintaining the structural integrity of car components.
Types of Spot Welding Machines Used in Car Manufacturing
In car manufacturing, various types of spot welding machines are employed to meet the diverse needs of assembling different vehicle components. One of the most common machines is the rocker arm spot welder, which features a pivoting arm that lowers the electrodes onto the metal sheets to execute the weld. This type of machine is versatile and suitable for a wide range of welding applications, making it a staple in automotive production facilities.
Another prevalent machine is the press-type spot welder, which utilizes a hydraulic or pneumatic press to apply force and create the weld. This machine offers precise control over the welding parameters and is ideal for applications that require consistent pressure and uniform welds. The press-type spot welder is often used for high-precision welding of complex car body structures and assemblies.
In addition to these traditional spot welding machines, advanced robotic spot welding systems have gained prominence in modern car manufacturing. These automated systems integrate robots equipped with spot welding guns to perform intricate welding tasks with speed and accuracy. Robotics technology enables flexible programming and positioning, allowing for efficient welding of various car body components while adapting to evolving production requirements.
Factors to Consider for Effective Spot Welding in Car Manufacturing
Effective spot welding in car manufacturing relies on several critical factors that impact the quality and integrity of the welds. Material selection is paramount, as different types of metals and alloys exhibit varying weldability and thermal conductivity. Understanding the properties of the materials being joined is essential for optimizing the welding process and ensuring the durability of the weld joints.
The design and geometry of the car components influence the welding parameters, including the positioning of electrodes, current distribution, and weld nugget formation. Complex shapes and contours require meticulous planning to achieve consistent and reliable welds, necessitating advanced tooling and fixturing for optimal welding performance. The condition of the metal surfaces, such as cleanliness and flatness, directly impacts the quality of spot welds and must be carefully controlled during the manufacturing process.
Temperature control is another critical consideration for effective spot welding, as excessive heat can lead to metal distortion and weaken the welds. Proper cooling and monitoring of heat-affected zones are essential for preserving the structural integrity of the welded components. Moreover, maintaining precise control over welding parameters, such as current, pressure, and duration, is crucial for achieving uniform and robust welds across various car body materials and thicknesses.
Importance of Proper Training for Spot Welding Car Manufacturing
Skilled operators play a pivotal role in ensuring the success and quality of spot welding car manufacturing. Proper training and certification programs are essential for equipping welders with the knowledge and proficiency needed to perform spot welding techniques effectively. Training encompasses a comprehensive understanding of welding principles, equipment operation, safety protocols, and quality assurance measures to uphold industry standards.
Additionally, ongoing professional development and proficiency testing are crucial for welders to stay abreast of technological advancements and best practices in spot welding. With continuous training, operators can enhance their skills in welding different materials, adapting to new welding technologies, and troubleshooting welding challenges to maintain the highest standards of weld quality in car manufacturing.
The emphasis on safety training cannot be overstated, as spot welding involves working with high electrical currents, heat, and potentially hazardous materials. Welders must be well-versed in safety protocols, protective equipment usage, and emergency procedures to mitigate risks and create a secure working environment. By prioritizing proper training, car manufacturers can ensure that spot welding operations are performed by competent and certified professionals, contributing to the overall reliability and safety of the vehicles produced.
Common Challenges in Spot Welding Car Parts
While spot welding offers numerous benefits, it also presents certain challenges that impact the welding process and the quality of the weld joints in car parts. One common challenge is achieving consistent weld penetration and nugget formation, especially in assemblies with varying material thicknesses or surface coatings. Controlling the weld parameters to accommodate these differences is crucial for producing uniform and robust spot welds across the entire assembly.
Another challenge arises from the presence of contaminants or surface coatings on the metal sheets, which can interfere with the welding process and compromise the integrity of the welds. Proper surface preparation and cleaning techniques are necessary to remove contaminants and ensure optimal weld quality. Addressing potential material inconsistencies, such as variations in hardness or alloy composition, is essential for overcoming welding challenges and maintaining the structural integrity of the welded car parts.
Maintaining electrode integrity and performance is also a critical aspect of spot welding, as electrode wear and deformation can affect the quality of welds over time. Regular inspection and maintenance of electrodes are essential for preserving their effectiveness and ensuring consistent welding performance. Addressing issues related to electrode alignment, pressure distribution, and electrical conductivity is crucial for mitigating potential welding defects and enhancing the overall reliability of spot welds in car parts.
Best Practices for Spot Welding Car Parts
Implementing best practices is essential for achieving optimal results of spot welding car manufacturing. Proper process control and documentation are fundamental for ensuring that welding parameters, such as current, pressure, and duration, are meticulously monitored and maintained within specified tolerances. This level of control enables consistent and reliable weld quality, contributing to the overall structural integrity and performance of car components.
Employing advanced welding monitoring and inspection technologies can enhance the quality assurance process, providing real-time feedback on weld integrity and detecting potential defects or irregularities. Non-destructive testing methods, such as ultrasonic inspection and visual examination, are valuable tools for verifying the quality of spot welds and identifying any imperfections that may compromise the structural soundness of car parts.
Collaboration between engineering, quality control, and production teams is essential for optimizing spot welding processes and addressing any welding-related challenges that may arise during car manufacturing. By fostering a multidisciplinary approach, manufacturers can leverage collective expertise to refine welding techniques, troubleshoot issues, and implement continuous improvement initiatives that elevate the overall quality and efficiency of spot welding operations.
Embracing technological advancements, such as adaptive welding systems and intelligent welding control software, can empower car manufacturers to achieve greater precision, flexibility, and efficiency in spot welding. These innovations enable adaptive control of welding parameters based on real-time conditions, ensuring that welds are tailored to specific car components while accommodating variations in materials and production requirements.
Innovations in Spot Welding Technology for Car Manufacturing
The evolution of spot welding technology in car manufacturing has seen remarkable advancements that have revolutionized the welding process and expanded the capabilities of automotive assembly. One notable innovation is the integration of advanced robotic systems equipped with vision-guided welding tools, enabling precise and agile welding of complex car body structures. Robotic spot welding systems offer unparalleled flexibility and adaptability, accommodating diverse assembly geometries and enhancing production efficiency.
The implementation of intelligent welding control systems has transformed spot welding into a data-driven process, leveraging real-time monitoring and feedback to optimize welding parameters and ensure consistent weld quality. These systems utilize advanced sensors and algorithms to adjust welding conditions dynamically, adapting to variations in material properties and environmental factors to produce reliable and high-quality spot welds.
The advent of high-strength and lightweight materials in car manufacturing has spurred the development of advanced welding techniques tailored to these materials. Laser welding and resistance spot welding of aluminum and other lightweight alloys have emerged as key technologies for achieving strong and durable welds while meeting the demands for lightweight vehicle designs. These innovations have broadened the scope of spot welding applications, enabling car manufacturers to explore new material combinations and design possibilities.
Incorporating simulation and modeling tools into spot welding processes has facilitated virtual optimization of welding parameters and electrode designs, leading to enhanced weld quality and production efficiency. By simulating welding scenarios and analyzing the impact of various parameters, car manufacturers can refine their spot welding techniques and minimize the need for extensive trial-and-error experimentation, accelerating the development of robust welding processes.
Maintenance and Safety Guidelines for Spot Welding Car Manufacturing
Maintaining spot welding equipment and ensuring a safe working environment are essential priorities in car manufacturing to uphold the quality and integrity of spot welds while safeguarding the well-being of operators. Regular maintenance of spot welding machines, including electrode inspection, calibration, and wear monitoring, is crucial for sustaining optimal welding performance and preventing equipment malfunctions that could compromise weld quality.
Implementing comprehensive safety protocols, including machine guarding, personal protective equipment, and hazard awareness training, is imperative for minimizing the risks associated with spot welding car operations. Ensuring proper ventilation and fume extraction systems further mitigates potential health hazards stemming from the release of fumes and gases during the welding process. By adhering to stringent safety standards, car manufacturers can create a secure and conducive environment for spot welding activities.
Additionally, establishing preventive maintenance schedules for spot welding equipment, such as regular cleaning, lubrication, and component inspections, is essential for prolonging the lifespan of the machines and minimizing downtime due to unexpected failures. Robust maintenance practices contribute to the reliability and consistency of spot welding operations, supporting uninterrupted production and the delivery of high-quality car components.
Training operators on safe handling and maintenance of spot welding equipment is paramount for fostering a culture of safety and responsibility in car manufacturing facilities. Providing clear guidelines and procedures for addressing potential hazards, emergency situations, and equipment malfunctions empowers operators to perform their welding duties with confidence and competence, contributing to a secure and efficient working environment.
Final Thoughts
Spot welding stands at the forefront of automotive manufacturing, embodying the marriage of precision engineering and skilled craftsmanship. As car manufacturers continue to push the boundaries of innovation, spot welding remains an indispensable process for creating vehicles that exemplify strength, durability, and safety. From the seamless fusion of metal sheets to the integration of cutting-edge technologies, spot welding epitomizes the art and science of car assembly.
By understanding the intricacies of spot welding car manufacturing, embracing technological advancements, and prioritizing training and safety, automotive industry professionals can elevate the quality and efficiency of spot welding operations. The relentless pursuit of excellence in spot welding paves the way for vehicles that not only meet the rigorous demands of today’s automotive landscape but also embody the enduring legacy of precision engineering and uncompromising quality.
As the automotive industry continues to evolve, spot welding remains steadfast as a cornerstone of car manufacturing, shaping the vehicles that inspire and empower us on the road ahead.