Aluminum, renowned for its lightweight, durability, and corrosion resistance, has emerged as a pivotal material in modern manufacturing. Among the various methods of joining aluminum, spot welding stands out as a fundamental technique utilized across multiple industries, including automotive, aerospace, and construction. Unlike traditional fusion welding, spot welding involves the application of heat and pressure to create localized welds, making it a preferred choice for joining aluminum sheets and components.
This article aims to unravel the complexities of spot welding aluminum, shedding light on its benefits, challenges, and essential practices to achieve strong and reliable welds.
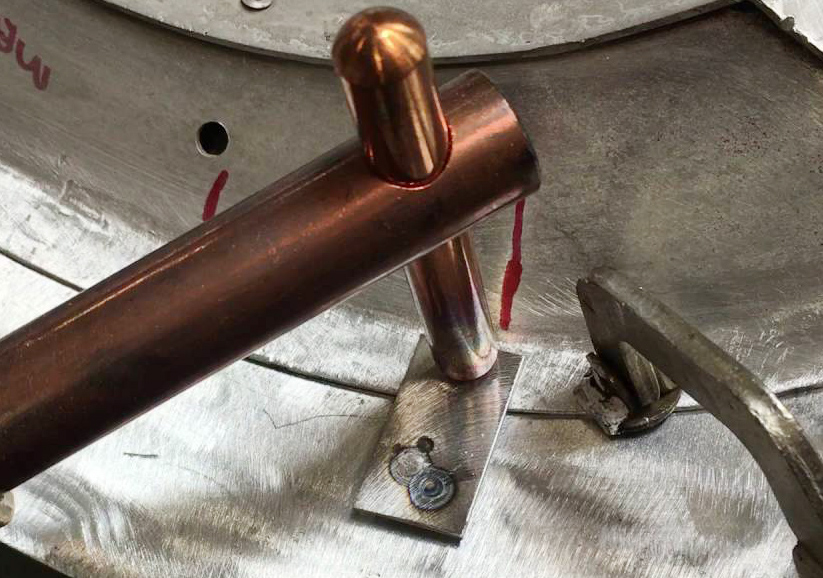
Image Source: usaweld
Spot welding plays a crucial role in aluminum fabrication, offering distinct advantages and posing unique challenges compared to welding other materials. The high thermal conductivity of aluminum necessitates precise control of the welding process to manage heat dissipation effectively and prevent distortion or burn-through.
The formation of brittle intermetallic compounds at the weld interface presents a challenge, requiring careful consideration of welding parameters and material preparation. Despite these challenges, the benefits of spot welding aluminum, such as rapid production cycles, minimal material distortion, and cost-effectiveness, make it an indispensable process in the manufacturing of aluminum structures and components.
Understanding the Spot Welding Aluminum
The ability of spot welding to produce consistent, high-strength joints in aluminum makes it an attractive choice for applications where structural integrity and performance are paramount. Understanding the intricacies of spot welding aluminum is essential for fabricators and engineers to harness the full potential of this joining method, ensuring the production of robust and reliable aluminum assemblies.
As we delve deeper into the spot welding process and its specific considerations for aluminum, a comprehensive understanding of its significance will empower industry professionals to optimize their welding practices and enhance the quality of their aluminum fabrications.
In the following sections, we will explore the spot welding process for aluminum in detail, examining the equipment, factors influencing weld quality, best practices, common applications, maintenance and safety measures, training and certification, as well as alternative methods for joining aluminum. Through this comprehensive exploration, readers will gain valuable insights into the art and science of welding aluminum, equipping them with the knowledge to elevate their welding endeavors to new heights.
Advantages of Spot Welding Aluminum
Spot welding aluminum offers a multitude of advantages, making it a preferred method for joining aluminum in various industrial sectors. The rapid welding cycles achievable with spot welding contribute to efficient production processes, enabling manufacturers to meet stringent timelines and maximize productivity.
The localized nature of spot welding minimizes heat-affected zones, reducing the risk of distortion and preserving the material’s structural integrity, particularly crucial in aluminum fabrication where heat sensitivity is a significant concern. The cost-effectiveness of spot welding, coupled with its ability to produce high-strength joints, enhances the economic viability of utilizing aluminum in manufacturing applications.
However, spot welding aluminum presents unique challenges that require careful consideration and precise control to achieve optimal results. The high thermal conductivity of aluminum necessitates specialized welding equipment capable of delivering precise heat input and electrode force to compensate for the rapid heat dissipation.
The formation of intermetallic compounds at the weld interface demands meticulous control of welding parameters, ensuring the prevention of brittle and weak welds. Understanding and mitigating these challenges are imperative for achieving consistent, high-quality spot welds in aluminum, underscoring the importance of expertise and precision in the welding process.
Despite the challenges, the advantages of spot welding aluminum far outweigh the complexities, making it a preferred for joining aluminum in diverse industrial applications. By comprehensively understanding the benefits and challenges associated with spot welding aluminum, industry professionals can optimize their welding practices and leverage the unique properties of aluminum to create robust and reliable assemblies.
In the subsequent sections, we will delve into the spot welding process for aluminum, elucidating the equipment, factors influencing weld quality, best practices, common applications, maintenance and safety measures, training and certification, as well as alternative methods for joining aluminum.
Spot Welding Aluminum Process and Equipment
The spot welding process for aluminum involves the application of heat and pressure at localized points to create secure welds between aluminum sheets or components. Specialized spot welding equipment designed for aluminum fabrication typically includes welding machines equipped with advanced control systems to regulate heat input, electrode force, and welding duration.
These machines are specifically tailored to address the challenges posed by the high thermal conductivity of aluminum, ensuring precise control and uniformity in the welding process. The electrodes used in spot welding aluminum are often manufactured from copper alloys, offering excellent thermal conductivity and wear resistance to withstand the demands of welding aluminum.
The spot welding process begins with the preparation of the aluminum surfaces to be joined, ensuring cleanliness and proper fit-up to facilitate optimal weld quality. Once the surfaces are prepared, the aluminum sheets or components are placed between the electrodes of the welding machine, and the welding parameters, including current, electrode force, and welding duration, are set according to the material thickness and desired weld characteristics.
Upon initiating the welding cycle, the electrodes deliver a precise amount of current and force to create localized fusion and establish a strong bond between the aluminum parts. The control systems in modern spot welding machines enable real-time monitoring and adjustment of welding parameters, ensuring consistent and reliable welds across production cycles.
Advancements in welding technology have led to the development of specialized welding processes such as pulse welding and resistance spot welding with adaptive control, further enhancing the capabilities and precision of welding aluminum. These innovative techniques enable fabricators to address the challenges associated with welding aluminum, including heat dissipation and intermetallic compound formation, resulting in improved weld quality and production efficiency. By leveraging specialized spot welding equipment and processes, manufacturers can harness the full potential of aluminum as a versatile and high-performance material in various industrial applications.
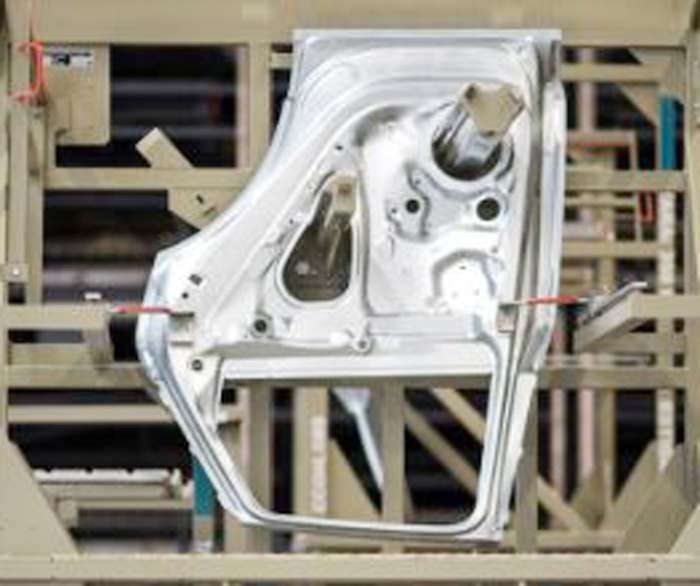
Image Source: Unsplashâ
Factors to Consider Before Spot Welding Aluminum
Before initiating the spot welding process for aluminum, several critical factors must be carefully considered to ensure the production of high-quality and reliable welds. The high thermal conductivity of aluminum necessitates precise control of welding parameters, including current, electrode force, and welding duration, to compensate for rapid heat dissipation and prevent material distortion or burn-through.
Understanding the relationship between these parameters and their impact on the welding process is essential for achieving optimal weld quality and consistency. The surface preparation of aluminum prior to welding plays a crucial role in ensuring proper fusion and minimizing the formation of intermetallic compounds, emphasizing the significance of cleanliness and material fit-up.
Additionally, the selection of suitable welding electrodes and their maintenance are pivotal factors influencing the success of spot welding aluminum. Copper alloys are commonly utilized for welding aluminum due to their excellent thermal conductivity and wear resistance, enabling consistent and durable electrode performance.
Regular maintenance and inspection of electrodes are essential to ensure their integrity and effectiveness in delivering precise heat input and electrode force during the welding process. The design and configuration of the weld joint, including the geometry and thickness of the aluminum components, impact the welding process and the resulting joint strength, necessitating meticulous planning and preparation to achieve the desired weld characteristics.
Considering these factors before welding aluminum is imperative for fabricators and engineers to mitigate challenges, optimize weld quality, and ensure the production of robust and reliable aluminum assemblies. By meticulously addressing the critical considerations and tailoring the welding process to the specific requirements of aluminum fabrication, industry professionals can elevate the performance and efficiency of their welding operations, unlocking the full potential of aluminum as a versatile and high-performance material.
In the subsequent sections, we will delve into the best practices for successful spot welding aluminum, common applications, maintenance and safety measures, training and certification, as well as alternative methods for joining aluminum in fabrication.
Best Practices for Successful Welding
Achieving successful spot welds in aluminum necessitates adherence to best practices that optimize weld quality, consistency, and production efficiency. The precise control of welding parameters, including current, electrode force, and welding duration, is paramount for managing heat dissipation and preventing material distortion or burn-through.
Establishing well-defined welding procedures tailored to the specific requirements of aluminum fabrication enables fabricators to consistently produce high-quality and reliable welds, ensuring structural integrity and performance. The selection and maintenance of suitable welding electrodes, typically manufactured from copper alloys, play a critical role in delivering precise heat input and electrode force during the spot welding process.
Furthermore, real-time monitoring and adjustment of welding parameters using advanced control systems in modern spot welding machines enable fabricators to optimize weld characteristics and address the challenges associated with welding aluminum. The integration of specialized welding processes, such as pulse welding and resistance spot welding with adaptive control, enhances the precision and efficiency of spot welding aluminum, resulting in improved weld quality and production consistency.
Additionally, thorough surface preparation of aluminum, including cleanliness and proper fit-up, ensures optimal fusion and minimizes the formation of intermetallic compounds, contributing to the production of durable and high-strength welds.
Regular training and certification programs for spot welding aluminum empower industry professionals to stay abreast of the latest advancements in welding technology, best practices, and safety measures, enhancing their expertise and proficiency in aluminum fabrication. By adopting best practices and leveraging advanced welding equipment and processes, manufacturers can optimize their spot welding operations, harnessing the unique properties of aluminum to create robust and reliable assemblies across diverse industrial applications.
Common Applications of Spot Welding in Aluminum Fabrication
Spot welding finds extensive applications in aluminum fabrication across various industries, owing to its ability to produce rapid, high-strength welds with minimal material distortion. In the automotive sector, spot welding is widely utilized for joining aluminum panels, structural components, and assemblies in the production of lightweight and fuel-efficient vehicles. The aerospace industry also relies on spot welding for aluminum fabrication, particularly in the assembly of aircraft structures and components, where the high strength-to-weight ratio of aluminum is advantageous.
Additionally, the construction industry incorporates spot welding in the fabrication of aluminum architectural components, structural elements, and assemblies, capitalizing on the material’s durability and corrosion resistance.
Spot welding plays a critical role in the manufacturing of consumer electronics, where aluminum enclosures and components require precise and efficient joining methods to ensure product durability and performance. The versatility of spot welding in aluminum fabrication extends to various consumer goods, industrial equipment, and electrical applications, where the lightweight and high-strength properties of aluminum are leveraged to deliver innovative and reliable products.
Understanding the diverse applications of spot welding in aluminum fabrication underscores its significance as a versatile and indispensable joining method, contributing to the advancement of manufacturing processes and the utilization of aluminum across multifaceted industries.
The widespread adoption of spot welding in aluminum fabrication reflects its efficacy in producing strong and durable welds, making it an integral process in the assembly of aluminum structures and components. By recognizing the common applications and benefits of spot welding in diverse industries, fabricators and engineers can capitalize on its capabilities to optimize their manufacturing processes and deliver high-quality aluminum assemblies tailored to specific industry requirements.
Importance of Proper Maintenance and Safety Measures
Ensuring the proper maintenance and adherence to safety measures in welding aluminum is essential for optimizing weld quality, prolonging equipment lifespan, and safeguarding the well-being of personnel. Regular inspection and maintenance of spot welding equipment, including welding machines and electrodes, are imperative to uphold their performance and precision in delivering localized heat and pressure during the welding process.
The maintenance of welding electrodes, typically manufactured from copper alloys, is pivotal to ensure consistent and durable electrode performance, contributing to the production of high-quality and reliable spot welds in aluminum.
Adherence to safety protocols and regulations in spot welding operations is paramount to mitigate potential hazards and protect personnel from occupational risks. Proper ventilation and fume extraction systems are essential to manage the release of fumes and gases generated during the spot welding process, safeguarding the health and well-being of welding operators.
The implementation of personal protective equipment (PPE), including welding helmets, gloves, and protective clothing, is crucial to minimize the exposure of personnel to welding hazards and ensure a safe working environment. Emphasizing the importance of proper maintenance and safety measures in spot welding aluminum underscores the commitment to upholding the highest standards of quality, efficiency, and personnel well-being in welding operations.
By prioritizing the maintenance of equipment and the implementation of safety measures, manufacturers can optimize their spot welding operations, ensuring the production of robust and reliable aluminum assemblies while safeguarding the health and safety of their personnel. The integration of comprehensive maintenance and safety protocols in spot welding aluminum reflects a proactive approach to enhancing operational efficiency, quality assurance, and personnel well-being, fostering a conducive and sustainable work environment.
Training and Certification for Spot Welding Aluminum
Continuous training and certification programs for spot welding aluminum are instrumental in equipping industry professionals with the latest advancements, best practices, and safety measures, enhancing their expertise and proficiency in aluminum fabrication. Specialized training programs tailored to spot welding aluminum encompass theoretical knowledge, practical skills, and hands-on experience with advanced welding equipment and processes, enabling participants to stay abreast of industry trends and technological advancements.
Moreover, certification programs validate the proficiency and competency of welding professionals, providing industry-wide recognition of their expertise and adherence to the highest standards of quality and safety in spot welding aluminum.
The integration of training and certification programs for spot welding aluminum underscores the commitment to continuous improvement, professional development, and the advancement of welding practices across diverse industrial sectors. By investing in the training and certification of welding professionals, manufacturers demonstrate their dedication to upholding the highest standards of quality, efficiency, and safety in spot welding operations, fostering a culture of excellence and innovation.
The participation in training and certification programs for spot welding aluminum not only enhances the expertise and proficiency of industry professionals but also contributes to the advancement of welding practices, quality assurance, and safety standards in aluminum fabrication. By embracing continuous learning and professional development, welding professionals can elevate the performance and efficiency of spot welding operations, unlocking the full potential of aluminum as a versatile and high-performance material across multifaceted industries.
Conclusions and Alternative Methods for Joining Aluminum in Fabrication
In addition to spot welding, several alternative methods for joining aluminum are employed in fabrication processes, each offering unique advantages and considerations tailored to specific applications and material requirements. One prominent alternative to spot welding is adhesive bonding, which utilizes specialized adhesives to create strong and durable bonds between aluminum components, particularly suitable for applications requiring seamless aesthetics and uniform distribution of stress.
Additionally, mechanical fastening techniques such as riveting and clinching provide effective means of joining aluminum, offering versatility and ease of disassembly, advantageous in applications requiring modularity and reparability.