Looking to solder a copper pipe that has water in it? You’ve come to the right place. Soldering with water in the pipe can be a tricky task, but with the right techniques, it is definitely possible to achieve a leak-free joint. In this article, we will guide you through the step-by-step process of soldering copper pipe with water in it effectively.
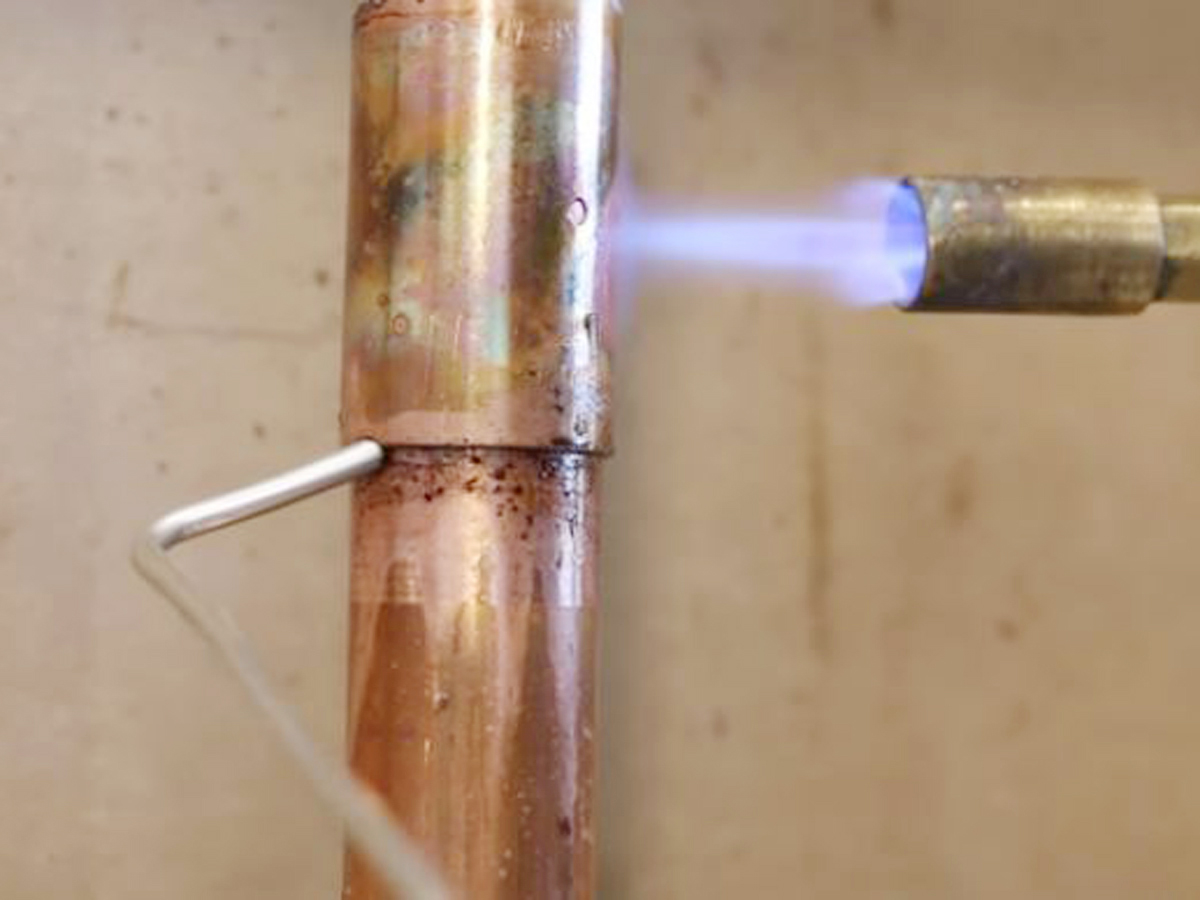
Photos by Got2Learn on YT
Safety Precautions When Soldering with Water in the Pipe
Before we dive into the soldering process, it’s crucial to prioritize safety. Here are some precautions you should take:
- Turn off the water supply: Begin by shutting off the main water supply to the pipe you will be working on. This will prevent water from flowing into the area while you are soldering, reducing the risk of accidents or damage.
- Protect nearby objects: Cover any nearby objects or surfaces that could be damaged by heat or solder splatters. Use a heat-resistant material such as a fire-resistant cloth or a heat shield.
- Wear protective gear: It’s essential to protect yourself from potential harm. Wear heat-resistant gloves, safety glasses, and clothing that covers your arms and legs. This will minimize the risk of burns or injuries.
Now that we have covered the safety precautions, let’s move on to the tools and materials you will need for soldering with water in the pipe.
Tools and Materials Needed for Soldering with Water in the Pipe
To successfully solder a copper pipe with water in it, you will need the following tools and materials:
Soldering iron: A soldering iron is an essential tool for soldering copper pipes. Choose a high-quality soldering iron with adjustable temperature settings to ensure precise control.
Flux: Flux is a chemical compound that helps clean the copper pipe and facilitate the soldering process. Opt for a flux specifically designed for copper pipes.
Solder: Solder is the metal alloy that creates the bond between the copper pipes. Choose a solder with a melting point suitable for your project, typically a lead-free solder.
Pipe cutter: A pipe cutter will allow you to cut the copper pipe to the desired length. Look for a cutter that is suitable for the pipe diameter you’re working with.
Emery cloth or sandpaper: Use emery cloth or sandpaper to clean the pipe before soldering. This will remove any corrosion or debris, ensuring a clean surface for soldering.
Heat-resistant cloth: A heat-resistant cloth will protect nearby surfaces from heat or solder splatters during the soldering process.
Now that you have gathered all the necessary tools and materials, let’s move on to the step-by-step guide on soldering copper pipes with water in them.
Step-by-Step Guide to Soldering Copper Pipes with Water In Them
Prepare the work area: Begin by ensuring the work area is dry and well-ventilated. Remove any nearby flammable objects and cover nearby surfaces with a heat-resistant cloth to protect them from heat or solder splatters.
Drain the water temporarily: To solder a copper pipe with water in it, you’ll need to temporarily drain the water. Locate the nearest valve to the section you’ll be working on and shut it off. Open the faucets connected to the pipe to release any remaining water. Use a bucket or towels to catch any drips.
Clean the pipe: Use emery cloth or sandpaper to clean the outside of the pipe and the inside of the fitting. This will remove any corrosion or debris, ensuring a clean surface for soldering. Wipe away any dust or residue.
Apply flux: Apply a thin and even layer of flux to the cleaned areas of the pipe and fitting. Flux helps clean the surfaces and ensures a strong bond between the solder and copper.
Assemble the joint: Insert the pipe into the fitting, ensuring a tight and secure fit. Make sure the pipe is fully inserted, leaving no gaps. Wipe away any excess flux.
Heat the joint: Use a soldering iron with the appropriate temperature setting to heat the joint evenly. Move the soldering iron around the joint, applying heat to both the pipe and the fitting. This will help the solder melt and flow smoothly.
Apply solder: Once the joint is heated, touch the solder wire to the joint. The heat will melt the solder, allowing it to flow into the joint. Continue applying solder until the joint is completely filled. Be careful not to apply too much solder, as it can lead to leaks or weak joints.
Inspect the joint: Allow the joint to cool for a few seconds, then visually inspect it. The solder should have flowed evenly and filled the joint completely. It should appear smooth and shiny. If there are any gaps or imperfections, reheat the joint and add more solder as needed.
Clean the joint: After soldering, use a damp cloth to clean any flux residue from the joint. Flux residue can corrode the joint over time if not properly cleaned.
Now you have successfully soldered a copper pipe with water in it. However, there are some common mistakes you should be aware of to avoid any issues.
Common Mistakes to Avoid When Soldering with Water in the Pipe
- Insufficient cleaning: Failing to properly clean the pipe and fitting before soldering can result in a weak joint. Take the time to thoroughly clean the surfaces to ensure a strong bond.
- Overheating the joint: Applying too much heat to the joint can cause the solder to flow improperly or even burn off. Use a soldering iron with adjustable temperature settings and carefully control the heat.
- Using too much solder: Applying excessive amounts of solder can lead to leaks or weak joints. Use only enough solder to fill the joint completely without excess.
- Not allowing the joint to cool: Rushing the soldering process by not allowing the joint to cool properly can result in a weak joint. Give the joint enough time to cool before handling or testing it.
Now that you are aware of the common mistakes to avoid, here are some additional tips for successful soldering with water in the pipe.
Tips for Successful Soldering with Water in the Pipe
Practice on scrap pieces: If you’re new to soldering or unsure of your skills, practice on scrap pieces of copper pipe before working on an actual project. This will help you gain confidence and improve your technique.
Use a heat-resistant barrier: Consider using a heat-resistant barrier, such as a wet cloth or heat shield, to protect nearby surfaces that could be damaged by heat or solder splatters.
Work quickly: When soldering with water in the pipe, work as quickly as possible to minimize the time the joint is exposed to heat. This reduces the risk of damage to the surrounding area or the pipe itself.
Inspect for leaks: After soldering, inspect the joint for any signs of leaks. Turn on the water supply and check for any water seepage. If you notice any leaks, reheat the joint and add more solder as needed.
Now, let’s explore alternative methods for repairing copper pipes with water in them.
Alternative Methods for Repairing Copper Pipes with Water In Them
While soldering is the most common method for repairing copper pipes with water in them, there are alternative approaches you can consider:
Compression fittings: Compression fittings provide a quick and easy way to repair copper pipes without the need for soldering. These fittings consist of a compression ring and a nut that tightens around the pipe, creating a watertight seal.
Push-fit connectors: Push-fit connectors, also known as push-to-connect or quick-connect fittings, can be used to repair copper pipes without soldering. These connectors feature a push-fit design that securely connects the pipe without the need for tools or solder.
Epoxy putty: Epoxy putty can be used to create a temporary or emergency repair on a copper pipe with water in it. This putty hardens and forms a seal around the damaged area, temporarily stopping leaks until a proper repair can be made.
While these alternative methods can be effective, soldering is generally considered the most reliable and long-lasting solution for repairing copper pipes.
Frequently Asked Questions About Soldering with Water in the Pipe
Can I solder copper pipes with water in them without draining the water?
It is strongly recommended to drain the water temporarily before soldering. Soldering with water in the pipe can make the process more difficult and increase the risk of leaks or weak joints. By draining the water, you can ensure a dry and clean work area.
Can I solder copper pipes with hot water in them?
It is not advisable to solder copper pipes with hot water in them. The heat from the soldering process can cause the water to boil, potentially leading to steam and pressure buildup. This can result in leaks, bursts, or even injury. Always drain the water and wait for the pipes to cool before soldering.
What type of solder should I use for copper pipes with water in them?
It is recommended to use a lead-free solder specifically designed for copper pipes. Lead-free solder is safer for drinking water applications and meets plumbing code requirements.
How do I know if my soldered joint is leak-free?
After soldering, visually inspect the joint for any signs of leaks. Turn on the water supply and check for any water seepage. If you notice any leaks, reheat the joint and add more solder as needed.
Conclusion
Soldering copper pipes with water in them requires careful preparation, the right tools and materials, and precise technique. By following the step-by-step guide, taking necessary safety precautions, and avoiding common mistakes, you can achieve a leak-free joint. Remember to always drain the water temporarily before soldering and inspect the joint for leaks after the process. If you are unsure or inexperienced, it’s always a good idea to seek professional help.
With the knowledge and skills gained from this article, you are now equipped to take on the challenge of soldering copper pipes with water in them like a pro.