To solder an aluminum radiator, clean the area thoroughly and use a flux designed for aluminum. Then, heat the area and apply aluminum solder.
Soldering an aluminum radiator requires specific tools and techniques due to the metal’s unique properties. Aluminum’s high thermal conductivity and oxidation tendency make it challenging to work with using traditional soldering methods. Proper preparation, such as cleaning the surfaces and using an aluminum-specific flux, ensures a strong bond.
Heating the area evenly is crucial to avoid warping or damaging the radiator. Using the right type of solder, typically one designed for aluminum, helps achieve a durable repair. Mastering these steps can extend the life of your aluminum radiator, saving money and preventing future issues.
Introduction To Aluminum Radiator Soldering
Soldering an aluminum radiator can be a delicate task. It requires precision, proper tools, and a good understanding of the process. This guide will provide insights into the importance of proper repairs and common issues faced with aluminum radiators.
Importance Of Proper Repairs
Proper repairs are crucial for the longevity of your radiator. A well-soldered radiator prevents leaks and ensures efficient cooling. Poor repairs can lead to frequent breakdowns and costly replacements. Following the right steps in soldering can save time and money.
Common Issues With Aluminum Radiators
Aluminum radiators often face several common issues. Here are some of them:
- Leaks: Cracks or holes can cause coolant leakage.
- Corrosion: Exposure to elements can lead to corrosion over time.
- Clogs: Debris can block the radiator passages, reducing efficiency.
Identifying these issues early can help in timely repairs. This ensures your radiator functions smoothly.
Tools And Materials Needed
Soldering an aluminum radiator requires specific tools and materials. This guide covers the essential soldering tools, recommended solder types, and safety gear needed for a successful job.
Essential Soldering Tools
Having the right tools makes the job easier and safer. Here’s a list of must-have tools:
- Soldering Iron: Choose one with adjustable temperature control.
- Flux: Aluminum flux is crucial for a strong bond.
- Wire Brush: Clean the aluminum surface before soldering.
- Soldering Pad: Protect your work surface from heat.
- Heat Gun: Useful for preheating the radiator.
Recommended Solder Types
Using the right solder is key to a durable repair. Below are recommended solder types:
Solder Type | Description |
---|---|
Aluminum Solder: | Designed specifically for aluminum. Provides strong bonds. |
Lead-Free Solder: | Safer for health. Environmentally friendly. |
Rosin Core Solder: | Contains flux for better adhesion. Easy to use. |
Safety Gear
Safety should be your top priority. Always use the right safety gear:
- Safety Glasses: Protect your eyes from hot solder and debris.
- Heat-Resistant Gloves: Shield your hands from burns.
- Respirator Mask: Avoid inhaling harmful fumes.
- Protective Clothing: Wear long sleeves and pants to protect your skin.
Preparing The Radiator
Before starting the soldering process, preparing the radiator is crucial. This step ensures a strong bond and prevents future leaks. Follow these steps carefully for a successful soldering job.
Cleaning The Aluminum Surface
The first step is cleaning the aluminum surface. Dirt and grease can prevent the solder from sticking. Use a non-metallic brush and a degreaser. Scrub the surface gently. Rinse with clean water. Dry the surface with a clean cloth.
Inspecting For Damage
Next, start inspecting for damage. Look for cracks, holes, or weak spots. Use a flashlight for better visibility. Check both sides of the radiator. Mark any damaged areas with a marker.

Credit: types.blog
Techniques For Soldering Aluminum
Soldering an aluminum radiator can be tricky. Aluminum has unique properties. Proper techniques are essential for success. Let’s explore key methods to achieve a solid solder.
Flux Application
Flux is crucial for soldering aluminum. It cleans the surface and ensures a strong bond. Apply flux generously to the aluminum parts. Use a brush for even coverage.
- Clean the surface thoroughly before applying flux.
- Choose a flux suitable for aluminum.
- Apply flux evenly using a small brush.
Heat Management
Managing heat is vital in soldering aluminum. Aluminum dissipates heat quickly. Use a high-power soldering iron or torch. Apply heat evenly to avoid warping.
- Preheat the aluminum surface.
- Use a soldering iron with at least 60 watts.
- Maintain a consistent temperature.
Soldering Procedure
The actual soldering process involves several steps. Ensure the parts are aligned properly. Use a soldering iron to melt the solder. Let the solder flow into the joint.
Step | Action |
---|---|
1 | Align the parts correctly. |
2 | Apply heat to the joint. |
3 | Feed the solder into the joint. |
4 | Allow the joint to cool naturally. |
Common Mistakes To Avoid
Soldering an aluminum radiator can be tricky. Avoid common mistakes to ensure a successful job. Below are some key errors to watch out for.
Overheating The Metal
Overheating the aluminum can cause severe damage. Aluminum melts at a lower temperature than other metals.
Use a controlled heat source. Monitor the temperature closely. This prevents the metal from overheating.
Temperature (°C) | Effect on Aluminum |
---|---|
Above 660 | Melting Point |
Below 660 | Safe Zone |
Using The Wrong Solder
Not all solder types work with aluminum. Using the wrong solder will result in weak joints. Always use solder designed for aluminum.
Check the packaging. Look for solder labeled for aluminum use. This ensures a strong bond.
Ignoring Safety Protocols
Soldering can be dangerous. Ignoring safety protocols increases risk. Always wear safety gear.
- Wear protective gloves
- Use safety goggles
- Work in a well-ventilated area
Ensure a safe environment. Follow all safety guidelines. This minimizes accidents.
Testing The Repair
After soldering an aluminum radiator, testing the repair is crucial. This ensures the integrity and efficiency of the radiator. Performing a thorough test helps identify any potential leaks or weaknesses in the bond. Below are some methods and tips to guarantee a successful repair.
Leak Testing Methods
Several methods exist to test for leaks in a soldered aluminum radiator. Here are the most effective ones:
- Pressure Test: Fill the radiator with water. Apply pressure using a hand pump. Check for any water escaping.
- Soap and Water Test: Mix soapy water in a spray bottle. Spray the solution on the repaired area. Look for bubbles indicating leaks.
- Vacuum Test: Create a vacuum in the radiator. Listen for hissing sounds. This indicates air escaping through leaks.
Ensuring A Strong Bond
To ensure the soldered bond is strong, follow these steps:
- Visual Inspection: Look closely at the soldered area. Ensure the solder has flowed smoothly and covers the joint completely.
- Heat Test: Heat the radiator to operational temperature. Observe any changes or leaks.
- Flex Test: Gently flex the repaired area. Ensure the bond holds firm under slight pressure.
By using these methods, you can confidently verify the effectiveness of your repair. A properly tested radiator ensures longevity and optimal performance.
Maintenance Tips
Maintaining an aluminum radiator ensures its longevity and optimal performance. Regular care prevents overheating and costly repairs. Below are essential maintenance tips to keep your radiator in top shape.
Regular Inspection
Conduct regular inspections to spot potential issues early. Check for visible leaks, corrosion, or damage. Inspect the radiator’s fins for any blockage or bent sections.
Use a flashlight to see areas clearly. Ensure the radiator cap is functioning correctly. A faulty cap can cause pressure issues.
Inspection Task | Frequency |
---|---|
Visual Check | Monthly |
Pressure Test | Every 6 Months |
Coolant Level Check | Weekly |
Preventive Measures
Implement preventive measures to avoid radiator issues. Always use the correct coolant mix. The wrong mixture can cause corrosion.
Keep the coolant level within recommended limits. Low coolant can lead to overheating.
- Flush the radiator every two years.
- Replace coolant as per manufacturer guidelines.
- Ensure the cooling system is free from air pockets.
Install a coolant filter to remove debris. This prevents clogging and improves efficiency. Regularly clean the exterior of the radiator. Dust and dirt can reduce its cooling capacity.
- Clean with a soft brush.
- Avoid using high-pressure water jets.
- Check hose connections for tightness.
Following these maintenance tips can extend the life of your aluminum radiator. It ensures your vehicle runs smoothly and efficiently.
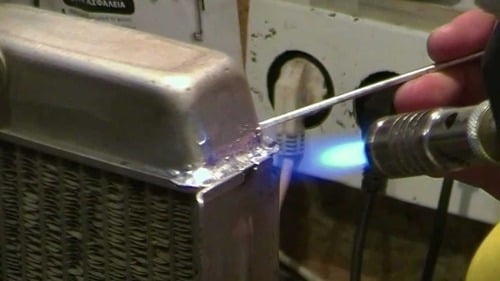
Credit: mayeralloys.com
Expert Advice And Best Practices
Soldering an aluminum radiator requires skill and precision. Let’s dive into expert advice and best practices. These insights will help you achieve a strong, reliable solder joint.
Professional Insights
Professionals recommend using high-quality flux designed for aluminum. The right flux ensures proper cleaning and bonding. Always clean the area thoroughly before soldering. Any dirt or grease can weaken the joint.
Use a propane or MAPP gas torch for heating. These torches provide the necessary heat without damaging the radiator. Maintain a steady hand and apply heat evenly. This prevents warping or burning the aluminum.
Advanced Techniques
Consider using a heat sink. This absorbs excess heat and protects surrounding areas. Apply the heat sink near the soldering area for best results.
Practice the tinning technique. This involves coating the soldering iron tip with solder. It helps in better heat transfer and smoother solder flow.
Here is a table summarizing the best practices:
Best Practice | Description |
---|---|
Use high-quality flux | Ensures proper cleaning and bonding |
Clean thoroughly | Removes dirt and grease |
Use a propane or MAPP gas torch | Provides necessary heat without damage |
Maintain a steady hand | Ensures even heat application |
Use a heat sink | Absorbs excess heat |
Practice tinning technique | Coats soldering iron tip for better heat transfer |
Follow these tips for successful soldering. Happy soldering!
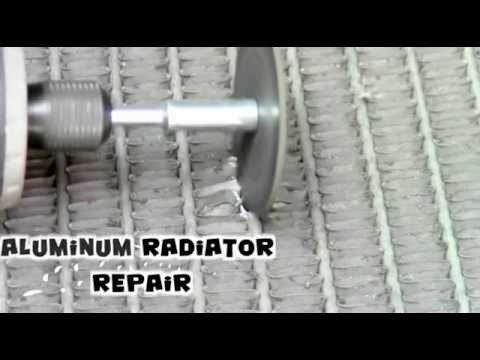
Credit: www.muggyweld.com
Frequently Asked Questions
How Do I Prepare An Aluminum Radiator For Soldering?
First, clean the area using a wire brush and degreaser. Ensure it’s free from dirt and oil. Then, gently sand the surface for better adhesion.
What Type Of Solder Works Best On Aluminum Radiators?
Use a flux-cored aluminum solder. It’s specially designed for aluminum and offers strong, lasting bonds. Ensure it’s suitable for high temperatures.
Can I Use A Regular Soldering Iron?
No, a regular soldering iron won’t work. Use a propane torch or a high-temperature soldering iron. These provide the necessary heat to melt aluminum solder.
Is It Necessary To Use Flux When Soldering Aluminum?
Yes, flux is crucial. It removes the oxide layer and ensures proper bonding. Choose a flux designed for aluminum.
Conclusion
Mastering the art of soldering an aluminum radiator ensures efficiency and durability. By following these steps, you can achieve professional results. Always prioritize safety and practice patience. With the right tools and techniques, your radiator will be as good as new.
Happy soldering and enjoy the benefits of a well-maintained radiator!