When it comes to MiG welding, choosing the right shielding gas is crucial for achieving optimal welding results. The right gas can improve the quality of your weld, reduce defects, and enhance overall welding performance. In this article, we will explore the various options for shielding gas and help you determine the best one for your specific needs.
Whether you are a beginner or an experienced welder, understanding the importance of selecting the best shielding gas for MiG welding is essential for successful and efficient welding projects. We will provide practical tips and considerations to help you make an informed decision. So, let’s dive in and explore the world of Mig welding shielding gas.
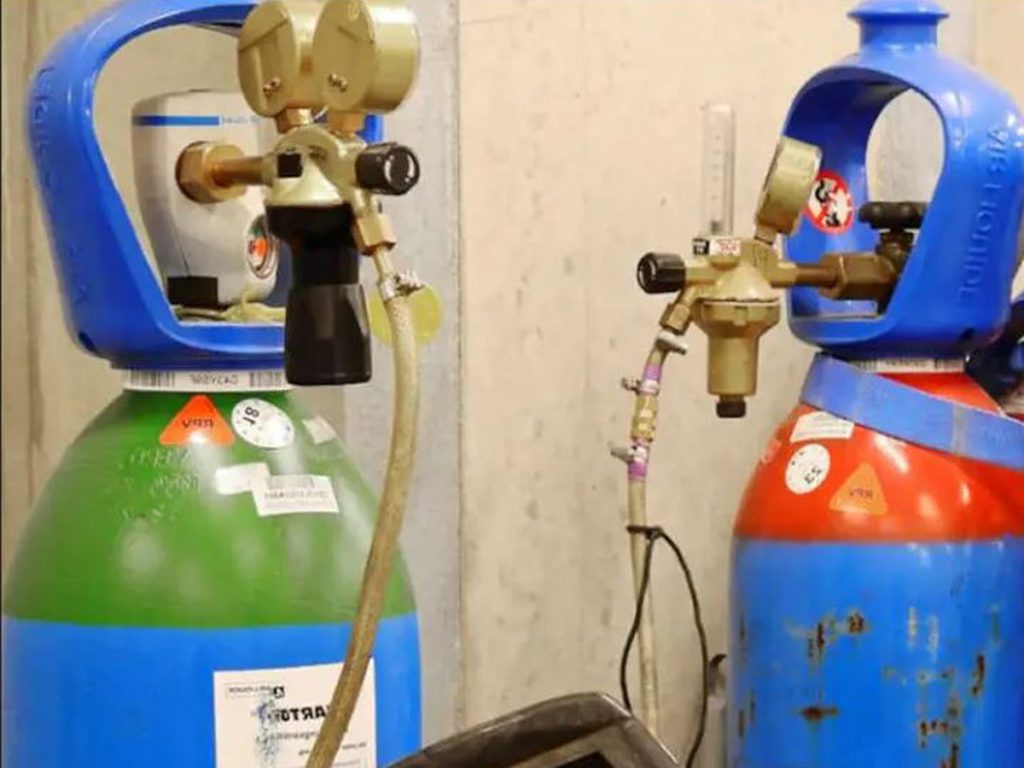
Photos by americanindustrialsupl
About MiG Welding and Shielding Gas
Before we can determine the best shielding gas for MiG welding, it is essential to understand the process itself. MiG welding, also known as Gas Metal Arc Welding (GMAW), uses an electric arc to join metals. A wire electrode is fed through a MiG gun, which also releases the shielding gas to protect the weld from atmospheric contamination.
Choosing the right shielding gas is crucial for achieving optimal welding results. The gas options available for MiG welding vary in their chemical composition, properties, and applications. When selecting a shielding gas, factors such as the type of metal being welded, thickness, welding position, and desired outcome must be considered.
One of the most critical considerations when choosing a shielding gas for MiG welding is its ability to protect the weld from various atmospheric gases, such as oxygen and nitrogen, which can cause defects in weld quality. Additionally, the shielding gas can also affect the welding speed, penetration, and heat input.
There are three primary gas options for MiG welding:
- Carbon dioxide (CO2)
- Argon (Ar)
- Helium (He)
The most commonly used gas for MiG welding is a mixture of CO2 and argon, known as C25. This mixture provides good weld penetration and a reasonable amount of spatter while remaining cost-effective. A pure argon gas is used mainly for welding aluminum and other non-ferrous metals. On the other hand, helium, with its high thermal conductivity, is often used for welding thick sections of stainless steel and other alloys.
Choosing the right shielding gas for MiG welding requires a thorough understanding of the welding process and the materials involved. Consult with welding experts or suppliers to determine the optimal gas for your specific project needs.
Exploring Different Shielding Gas Options for MiG Welding
When it comes to MiG welding, choosing the right shielding gas is crucial for producing high-quality welds. Different gases have different properties that impact the welding process, so it’s important to understand the options available and their potential applications.
Here are some of the top shielding gas options for MiG welding:
Gas Type | Advantages | Potential Applications |
---|---|---|
Argon | Provides good penetration Produces clean welds Works well on thinner metals | Aluminum, Stainless steel, Copper |
Carbon dioxide | Produces strong weldless expensive than other gases Works well on thicker metals | Mild steel, Cast iron |
Helium | Provides good heat input Improves weld penetration Works well on thicker metals | Stainless steel, Copper, Titanium, |
While these are some of the optimal shielding gases for MiG welding, choosing the right one for your specific project depends on various factors such as the type of metal being welded and the welding position. It’s recommended to consult with industry experts to determine the best shielding gas for your welding needs.
Benefits of Using the Right Shielding Gas for MiG Welding
Choosing the appropriate shielding gas for MiG welding can have a significant impact on the quality and efficiency of the welding process. Here are some benefits of using the right shielding gas:
- Improved weld quality: The right shielding gas ensures that the welding process is protected from atmospheric contamination, resulting in stronger and cleaner welds.
- Reduced defects: Shielding gas helps prevent common welding defects such as porosity, which occurs when air pockets are trapped in the weld. This results in a more uniform and consistent weld.
- Enhanced welding performance: The use of the correct shielding gas can improve the speed and efficiency of the MiG welding process, resulting in increased productivity and profitability.
Using the optimal shielding gas for your specific welding needs can also lead to cost savings and a safer work environment.
It is important to note that different shielding gases have varying benefits, and selecting the best option requires careful consideration of the application and desired outcome. Consulting with welding professionals and testing different gases is recommended to ensure the best results.
Recommended Shielding Gas for MiG Welding
When it comes to selecting the right shielding gas for MiG welding, there are several options to consider. Based on our research and expertise, we have compiled a list of recommended gases to help you make an informed decision.
Gas Type | Advantages | Potential Applications |
---|---|---|
Argon | Produces a stable arc, reduces spatter, enhances weld quality | Aluminum, stainless steel, carbon steel, titanium |
Carbon Dioxide | Cost-effective, deep penetration, good for thick metal | Steel, low-alloy steel, cast iron |
Helium | Produces hotter arc, good for thicker metal, enhances penetration | Stainless steel, titanium, aluminum |
Mixed Gas (Argon/Carbon Dioxide) | Cost-effective, improves weld quality and appearance | Carbon steel, low-alloy steel, stainless steel |
It is important to choose the right shielding gas for your specific welding application. When selecting a gas, consider factors such as the type of metal being welded, the thickness of the metal, and the welding position.
- For aluminum welding, argon is the optimal choice.
- For carbon steel, a mixed gas of argon and carbon dioxide can provide improved weld quality.
- For stainless steel and titanium, helium is a great option for enhanced penetration and arc stability.
- For cost-effective and deep penetration in thick metal, carbon dioxide is a suitable choice.
Remember, each shielding gas has its own set of advantages and potential applications. Be sure to consult with experts and conduct thorough research before making a final decision.
Tips for Choosing the Right Shielding Gas
Choosing the right shielding gas for MiG welding is a critical step towards achieving successful welds. Here are some tips to help you make an informed decision:
- Consider the type of metal being welded: Different metals require different shielding gases. For example, stainless steel typically requires a gas blend that includes helium, while carbon steel can be welded with a 100% carbon dioxide gas.
- Assess your environment: Outdoor welding may require a different shielding gas than indoor welding. Wind and drafts can cause issues with gases that are lighter than air, like argon, while heavier gases like carbon dioxide can displace air in an enclosed space, causing suffocation.
- Evaluate the desired outcome: If the goal is to achieve a high-quality finish, then a gas blend with argon may be the best choice. However, if the priority is to minimize costs, then 100% carbon dioxide may be a more economical option.
- Consult with experts: Reach out to reputable welding supply stores and welding professionals who have experience with MiG welding. They can provide guidance on which shielding gases are best suited for your specific needs and goals.
- Test multiple options: It is important to test different shielding gas options before committing to a specific one. This can help you get a better understanding of how each gas performs and find the optimal choice for your welding needs.
By following these tips, you can make an informed decision when choosing the right shielding gas for your MiG welding projects. Remember to prioritize safety and consult with experts for professional advice.
Conclusion
Choosing the right shielding gas is crucial for achieving the perfect weld in MiG welding. It is important to evaluate the different shielding gas options and their applications to select the optimal solution for your specific welding requirements. By taking into account factors such as the type of metal being welded, the welding position, and the desired outcome, you can make an informed decision. Remember to prioritize safety and consult with experts for professional advice.
With this knowledge, you can confidently select the best shielding gas for your MiG welding projects. Taking the time to understand your options and considering your specific needs will lead to successful and efficient welding projects.
FAQs
What is the best shielding gas for MiG welding?
The best shielding gas for MiG welding depends on various factors such as the type of metal being welded, the welding position, and the desired outcome. Common shielding gas options include argon, carbon dioxide, and a mixture of both. It is recommended to consult with welding experts or refer to the manufacturer’s guidelines to determine the most suitable shielding gas for your specific project.
Why is choosing the right shielding gas important in MiG welding?
Choosing the right shielding gas is important in MiG welding because it plays a crucial role in protecting the weld pool from atmospheric contamination. The shielding gas creates a protective environment around the weld, preventing the formation of defects and ensuring high-quality welds. Using the wrong shielding gas can lead to poor weld integrity and compromised joint strength.
What are the benefits of using specific shielding gas for MiG welding?
Using specific shielding gas for MiG welding offers several benefits. It can improve weld quality, reduce the formation of porosity and spatter, enhance arc stability, and promote better penetration. Additionally, certain shielding gases can provide improved weld appearance and reduce post-weld cleaning requirements. Choosing the right shielding gas for your specific welding needs can significantly enhance overall welding performance.
Which shielding gas is recommended for MiG welding?
The recommended shielding gas for MiG welding depends on the type of metal being welded. For welding stainless steel, argon or a mixture of argon and carbon dioxide is commonly used. Carbon dioxide is often used for welding carbon and low-alloy steels. However, it is important to refer to welding guidelines and consult with experts to determine the optimal shielding gas for your specific project.
What should I consider when choosing the right shielding gas for MiG welding?
When choosing the right shielding gas for MiG welding, consider factors such as cost, availability, desired weld appearance, weld penetration requirements, and specific welding conditions. Different shielding gases have varying properties and performance characteristics, so it is important to assess your welding needs and consult with professionals to make an informed decision.
Can I use a shielding gas mixture for MiG welding?
Yes, using a shielding gas mixture is common in MiG welding. These mixtures are often tailored to specific welding applications and provide a combination of benefits from different gases. The ratio and composition of the shielding gas mixture will depend on the type of metal being welded and the desired welding parameters. Consult with welding experts or refer to welding guidelines for the recommended shielding gas mixtures for your specific project.