Ensuring workplace safety is a top priority for any organization. It is crucial to establish and implement safe operating procedures to prevent accidents and protect employees. A safe operating procedure (SOP) is a step-by-step guide that outlines the necessary precautions and actions to be taken in order to safely complete a task or operate a piece of equipment. This blog post will provide a comprehensive step-by-step guide on how to develop and implement safe operating procedures in your workplace, helping you create a safer and more productive work environment.
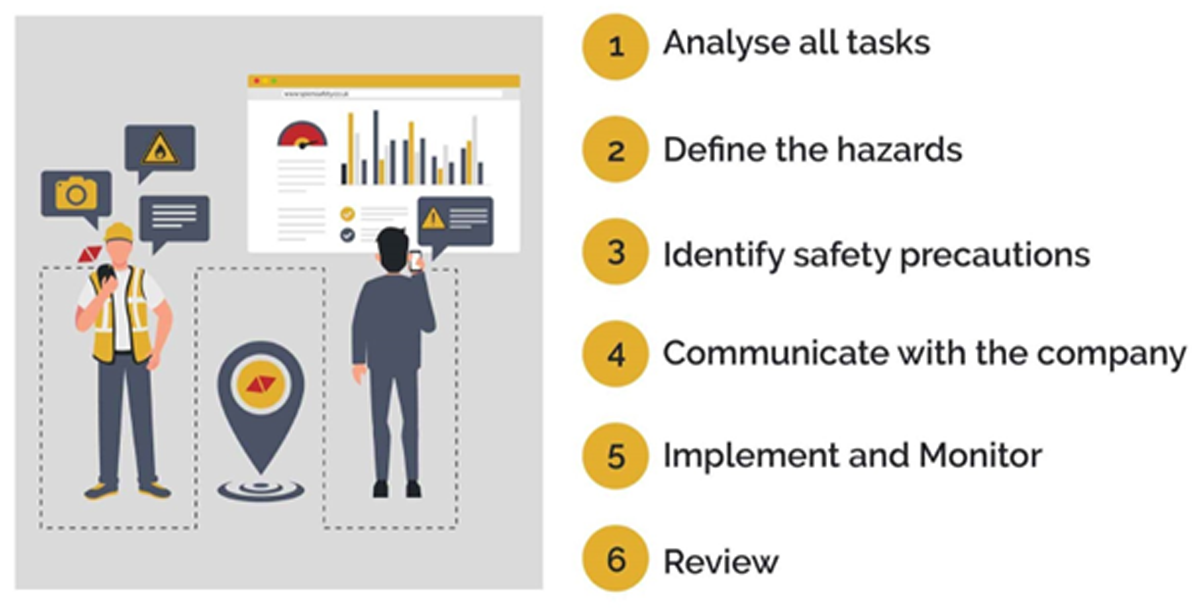
Photos by spierssafety.co.uk
Importance of safe operating procedures
To truly understand the value of safe operating procedures (SOPs), it’s essential to recognize the risks and consequences associated with neglecting them. Accidents and injuries in the workplace can result in financial losses, reputational damage, and most importantly, harm to employees. Implementing SOPs not only helps prevent accidents, but it also promotes consistency and efficiency in work processes.
By following a set of predefined steps, employees can reduce the likelihood of errors and improve their overall performance. SOPs also serve as a reference for new hires, ensuring that they are properly trained and equipped to carry out their responsibilities safely. In short, SOPs provide a structured approach to workplace safety, empowering organizations to create a culture that prioritizes the well-being of its employees.
Conducting a thorough risk assessment
Once you recognize the importance of safe operating procedures (SOPs), the next step in implementing them is conducting a thorough risk assessment. This crucial step involves identifying and evaluating potential hazards and risks that could arise within the workplace. To begin, gather a team of knowledgeable employees who can accurately assess the workplace environment and its associated risks. This team should include representatives from different departments or areas of expertise to ensure a comprehensive evaluation.
During the risk assessment, carefully examine all work processes, equipment, and materials used. Take note of any potential hazards, such as electrical or mechanical dangers, chemical exposure, ergonomic issues, or environmental factors. Prioritize the risks based on severity and likelihood of occurrence. Once the risks are identified, implement appropriate control measures to mitigate or eliminate them. This may involve implementing engineering controls, like installing safety guards or barriers, providing personal protective equipment (PPE), or establishing safe work practices.
Remember, a comprehensive risk assessment lays the foundation for developing effective SOPs that address the specific hazards present in your workplace. By conducting this assessment, you demonstrate your commitment to the safety and well-being of your employees.
Developing and documenting standard operating procedures
Developing and documenting standard operating procedures (SOPs) is the next crucial step in the process of implementing safe operating procedures. SOPs provide clear and detailed instructions on how tasks should be performed to ensure consistency, efficiency, and most importantly, safety in the workplace. Start by reviewing existing procedures and guidelines to identify any gaps or areas that need improvement. Involve employees who are directly involved in these tasks, as they have valuable insights and suggestions for enhancing safety measures.
When developing SOPs, ensure that they are concise, easy to understand, and include step-by-step instructions. Use visual aids, such as diagrams or flowcharts, to further enhance clarity. Clearly define responsibilities and specify any required training or certifications for these tasks.
Once the SOPs are developed, document them in a format that is easily accessible for all employees. This could be in the form of a printed manual, an online portal, or a digital document management system. Regularly review and update SOPs to reflect any changes in equipment, procedures, or regulations.
By developing and documenting SOPs, you provide a valuable resource that guides employees in performing tasks safely and consistently, reducing the risk of accidents and injuries.
Training employees on safe operating procedures
Training employees on safe operating procedures is essential for ensuring workplace safety. Once the SOPs have been developed and documented, it is crucial to provide comprehensive training to all employees involved in the tasks outlined in the procedures. Start by conducting initial training sessions to introduce the SOPs and explain the importance of following them. Emphasize the potential risks and consequences of not adhering to the procedures, and highlight the benefits of compliance.
Consider different learning styles and provide training materials in various formats, such as presentations, videos, or hands-on demonstrations. This will help ensure that employees have a clear understanding of the procedures and know how to implement them correctly. Depending on the complexity of the tasks, consider providing additional hands-on training or refresher courses to reinforce the knowledge and skills required. This could involve simulating real-life scenarios or providing opportunities for employees to practice using the procedures.
Regularly evaluate the effectiveness of the training program and gather feedback from employees to identify any areas for improvement. Update the training materials and approach as necessary to address any gaps or challenges. Remember, training is an ongoing process. New employees should receive comprehensive training as part of their onboarding process, while existing employees should undergo regular refresher training to keep their knowledge up to date.
By investing time and resources into training employees on safe operating procedures, you are equipping them with the knowledge and skills required to maintain a safe working environment. This will ultimately lead to a reduction in accidents and injuries, enhancing overall workplace safety.
Monitoring and evaluating the effectiveness of procedures
Once training has been conducted and employees are familiar with the safe operating procedures (SOPs), it is essential to monitor and evaluate their effectiveness. Regular monitoring helps ensure that employees are following the procedures correctly and identifies any areas for improvement. Implement a system for monitoring the implementation of SOPs, such as regular check-ins or audits. These can be conducted by supervisors, safety officers, or designated team members. During these inspections, observe employees as they perform their tasks to ensure they are following the established procedures.
In addition to monitoring, gathering feedback from employees is crucial. Encourage them to provide input on the effectiveness of the procedures and any challenges they may face during implementation. This feedback can be collected through surveys, suggestion boxes, or one-on-one discussions. Based on the monitoring and feedback received, make necessary adjustments to the SOPs. Continuously updating and improving procedures ensures that they remain relevant to the evolving needs of the work environment.
By monitoring and evaluating the effectiveness of procedures, you can identify any gaps or weaknesses in the training program and make necessary improvements. This ongoing assessment is critical for maintaining a safe working environment and preventing accidents or injuries.
Regularly reviewing and updating procedures
Regularly reviewing and updating the implemented safe operating procedures (SOPs) is essential to maintain a safe working environment. As workplace practices and technologies evolve, it is important to ensure that procedures remain relevant and effective. Conduct periodic reviews of the SOPs to identify any areas that need improvement or modification. This can be done by gathering feedback from employees, safety officers, and supervisors. Encourage open communication and provide opportunities for employees to share their insights and suggestions.
Once feedback has been gathered, take the necessary steps to update the procedures accordingly. This may involve revising the existing procedures, incorporating new safety measures, or providing additional training to address any identified gaps.
By regularly reviewing and updating the SOPs, you are demonstrating your commitment to continuous improvement and the safety of your workforce. This proactive approach will help prevent accidents, protect employees, and contribute to a productive and positive work environment.
Ensuring compliance with legal and regulatory requirements
In addition to regularly reviewing and updating safe operating procedures (SOPs), it is crucial to ensure compliance with legal and regulatory requirements. This step helps protect both your employees and your organization from potential legal consequences. Stay informed about the latest health and safety regulations specific to your industry. Regularly verify that your SOPs align with these regulations to prevent any violations. Consult with legal experts or industry professionals if needed, to ensure your procedures are in line with the necessary compliance standards.
Make sure your employees are aware of the legal and regulatory requirements that apply to their roles. Provide regular training sessions to keep them informed and up to date with any changes in the law. Encourage open communication and address any concerns or questions they may have regarding compliance.
The benefits of implementing safe operating procedures
Implementing safe operating procedures (SOPs) in the workplace provides numerous benefits to both employees and organizations. Firstly, SOPs ensure consistency in the way tasks are performed, reducing the likelihood of errors or accidents. This, in turn, improves operational efficiency and productivity.
Secondly, SOPs promote a culture of safety within the organization. When employees know that their well-being and safety are prioritized, they feel valued and motivated to work. This leads to increased job satisfaction, lower turnover rates, and a positive work environment.
Moreover, implementing SOPs can help organizations achieve compliance with legal and regulatory requirements. This not only protects the organization from potential legal consequences but also maintains a positive reputation among stakeholders.
Lastly, having well-documented SOPs enables organizations to effectively onboard new employees and provide consistent training. This ensures that all employees are equipped with the knowledge and skills necessary to perform their tasks safely and effectively.
In summary, implementing SOPs in the workplace has a wide range of benefits, including improved safety, increased productivity, and legal compliance. By prioritizing this aspect of workplace safety, organizations can create a culture of safety and ensure the well-being of their employees.
Conclusion and the commitment to workplace safety
In conclusion, implementing safe operating procedures (SOPs) is crucial for maintaining and promoting workplace safety. By prioritizing safety through the use of SOPs, organizations can ensure the well-being of their employees, improve operational efficiency, and achieve compliance with legal and regulatory requirements. To fully commit to workplace safety, organizations must take a proactive approach.
This involves regularly reviewing and updating SOPs to reflect any changes in equipment, processes, or regulations. It also requires providing comprehensive training to employees on the proper use of SOPs and ensuring their understanding and compliance. Furthermore, organizations should encourage a culture of safety by promoting open communication, encouraging employees to report safety concerns or near-misses, and recognizing and rewarding safe behaviors.
By making safety a priority and continuously striving to improve workplace safety measures, organizations can create a safer and healthier work environment for their employees. Remember, workplace safety is not just a box to check off; it is an ongoing commitment to protecting the well-being of all those involved.