In the world of manufacturing, efficiency and precision are paramount. Robotic spot welding has revolutionized the way metal components are joined together, offering a faster and more accurate alternative to traditional welding methods. This cutting-edge technology utilizes robots equipped with advanced sensors and programming to perform spot welding tasks with unparalleled speed and precision.
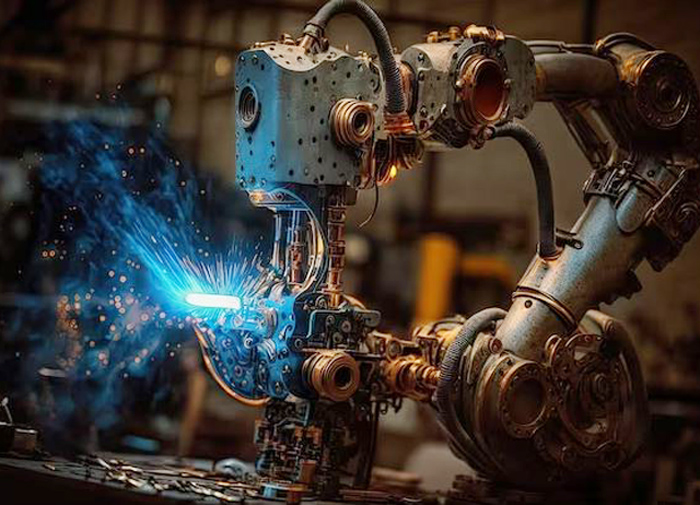
Advantages of Robotic Spot Welding over Traditional Welding Methods
Robotic spot welding offers several advantages over traditional welding methods. Firstly, the precise control offered by robots ensures consistent and high-quality welds, reducing the occurrence of defects and minimizing rework. With traditional welding, human error and fatigue can lead to inconsistencies in the quality of the welds, resulting in the need for costly repairs and potential safety hazards.
Robots can work tirelessly without fatigue, increasing productivity and reducing labor costs. Unlike human welders who require breaks and rest periods, robots can operate 24/7, maximizing production output. This allows manufacturers to meet tight deadlines and handle large volumes of work efficiently, ultimately improving overall business performance.
The flexibility of robotic spot welding allows for easy adaptation to different product configurations and production volumes. Robots can be programmed to adjust welding parameters based on the specific requirements of each product, eliminating the need for manual adjustments and reducing setup times. This versatility makes robotic spot welding suitable for a wide range of industries, from automotive to aerospace, where there is a need for efficient and precise welding processes.
Robotic Spot Welding Process Explained
The robotic spot welding process involves several key steps. It begins with the preparation of the metal components to be welded, ensuring that they are clean and properly positioned. Next, the robotic arm equipped with welding tools and sensors is programmed to follow a pre-determined welding path. The sensors detect the exact position and orientation of the components, allowing the robot to adjust its movements accordingly.
Once the welding path is set, the robot initiates the welding process by applying an electrical current to the spot where the components meet. This current generates heat, causing the metal to melt and fuse together, forming a strong and durable weld. The robot carefully controls the welding parameters, such as current intensity and duration, to ensure optimal weld quality and integrity.
Throughout the welding process, the robot continuously monitors the welding parameters and the quality of the weld. Advanced sensors detect any deviations or anomalies, allowing the robot to make real-time adjustments to maintain consistent weld quality. This ensures that each weld meets the required standards and specifications, reducing the need for post-weld inspections and rework.
Robotic Spot Welding Equipment
Robotic spot welding systems consist of several key components and equipment that work together to achieve efficient and precise welding. The robotic arm, equipped with welding tools, is the core component of the system. It is responsible for carrying out the welding tasks with precision and accuracy.
The welding tools attached to the robotic arm vary depending on the specific requirements of the welding process. Common tools include spot welding guns, electrode holders, and wire feeders. These tools deliver the necessary heat and pressure to create the welds.
To ensure accurate positioning and movement, robotic welding systems rely on advanced sensors and vision systems. These sensors provide real-time feedback on the position, orientation, and quality of the welds, allowing the robot to make adjustments as needed. Vision systems use cameras and image processing algorithms to detect and track the components being welded, ensuring precise alignment and consistent weld quality.
The control system is another crucial component of robotic spot welding systems. It consists of software and hardware that enable the programming and operation of the robot. The control system allows manufacturers to define welding paths, set welding parameters, and monitor the entire welding process. It also provides the flexibility to adjust welding parameters based on specific product requirements.
Factors to Consider When Implementing in Manufacturing Setting
Implementing robotic spot welding in a manufacturing setting requires careful consideration of several factors. Firstly, manufacturers need to assess the suitability of their products for robotic welding. Products that have consistent geometries and require high-volume production are ideal candidates for this technology. On the other hand, products with complex geometries or low production volumes may require additional customization and programming, which can increase implementation costs.
Another important factor to consider is the layout and integration of the robotic spot welding system within the existing manufacturing environment. Manufacturers need to ensure that the system can be seamlessly integrated into their production lines, optimizing workflow and minimizing disruptions. This may involve modifying the layout of the production floor or reconfiguring other equipment to accommodate the robotic system.
Training and expertise are also crucial when implementing robotic spot welding. Manufacturers need to ensure that their operators are properly trained to program, operate, and maintain the robotic system. This includes understanding the welding parameters, interpreting sensor feedback, and troubleshooting any issues that may arise. Proper training will not only ensure the efficient operation of the system but also enhance the safety of the operators.
Common Challenges and Solutions in Robotic Welding
While robotic welding offers numerous advantages, there are also common challenges that manufacturers may encounter. One challenge is the need for precise positioning and alignment of the components to be welded. Any misalignment can result in poor weld quality or even failure. To overcome this challenge, manufacturers can invest in advanced vision systems and sensors that provide accurate feedback on component position and alignment. This allows the robot to make real-time adjustments and ensure precise weld placement.
Another challenge is the variability of the welding process due to factors such as material thickness, joint design, and welding parameters. Manufacturers need to carefully calibrate the welding parameters to account for these variables and ensure consistent weld quality. This may involve conducting extensive testing and optimization to identify the optimal welding parameters for each specific application.
Maintaining and troubleshooting the robotic welding system is also a challenge that manufacturers may face. To address this, manufacturers should establish a regular maintenance schedule and provide operators with the necessary training and resources to handle common issues. Additionally, working closely with the system supplier or integrator can provide access to expert support and guidance in case of more complex problems.
Examples of Industries That Benefit from Robotic Welding
Robotic spot welding is widely utilized in various industries that require efficient and precise welding processes. One industry that greatly benefits from this technology is the automotive industry. With the increasing demand for electric vehicles and lightweight materials, robotic welding plays a crucial role in joining different components, such as body panels and chassis, with high accuracy and consistency. The automotive industry also benefits from the speed and productivity of robotic spot welding, enabling efficient production lines and meeting tight production schedules.
The aerospace industry is another industry that benefits from robotic welding. The lightweight materials used in aerospace manufacturing, such as aluminum and titanium alloys, require precise and high-quality welds to ensure structural integrity and safety. Robotic spot welding offers the necessary precision and control to meet the stringent quality requirements of the aerospace industry. The ability of robots to work in hazardous environments, such as welding aircraft components in confined spaces, enhances safety and reduces the risk of accidents.
Other industries that benefit from robotic spot welding include the electronics industry, where it is used for the assembly of circuit boards and other electronic components, and the construction industry, where it is utilized in the fabrication of steel structures and components.
Future Trends and Developments in Robotic Spot Welding Technology
The field of robotic spot welding continues to evolve, with ongoing advancements and innovations that promise to further enhance efficiency and precision. One emerging trend is the integration of artificial intelligence (AI) and machine learning algorithms into robotic spot welding systems. AI algorithms can analyze large amounts of data collected during the welding process, enabling predictive maintenance and optimization of welding parameters. Machine learning algorithms can also improve the accuracy and speed of robotic programming, reducing setup times and improving overall productivity.
Another trend is the development of collaborative robotic systems, also known as cobots. These systems allow humans and robots to work side by side, leveraging the strengths of each. Cobots are designed to be safe and easy to program, allowing operators to quickly switch between manual and robotic welding tasks. This flexibility increases the versatility of robotic spot welding systems, making them suitable for small-batch production and customization.
Advancements in sensor technology are also driving improvements in robotic spot welding. Advanced sensors can provide real-time feedback on welding parameters, such as temperature and weld penetration, allowing for precise control and quality monitoring. Additionally, vision systems are becoming more sophisticated, enabling robots to accurately detect and track components in complex welding environments.
Conclusion
By embracing robotic spot welding, manufacturers can enhance their competitiveness in the market. With its ability to deliver consistent quality, increased productivity, and cost savings, this technology is undoubtedly a game-changer in the manufacturing industry. Robotic welding offers numerous advantages over traditional welding methods, including precise control, increased productivity, and flexibility.
However, implementing robotic spot welding requires careful consideration of factors such as product suitability, layout integration, and operator training. Despite the challenges, the benefits of robotic spot welding make it a worthwhile investment for manufacturers in various industries. Stay ahead of the competition and explore the possibilities of robotic spot welding for your business today.